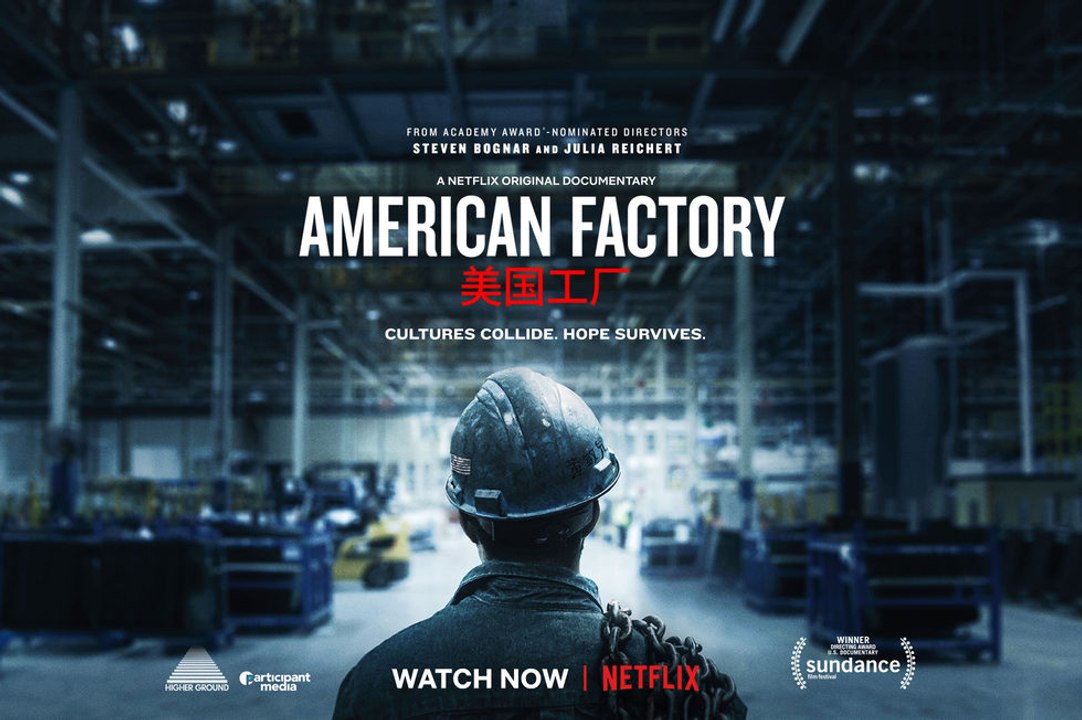
The field of manufacturing engineering is often referred to as production engineering. This type of engineering shares many common ideas and concepts with other engineering fields. This area of engineering is a great way to find your niche and be a part of the company's success. These engineers can ensure that products and services meet high quality standards.
Job duties
A production engineer is responsible for managing and analysing all aspects of the production process, including design and implementation. This position requires attention to detail, and commitment to safety in the workplace. Production engineers also ensure that their company maintains high quality standards and environmental safety, and they evaluate existing production activities to identify ways to improve them.
Production engineers help companies produce products efficiently and cost-effectively. Their work may include analyzing current production processes, as well as focusing their attention on one aspect of the production process. They can also adjust plant software or train production workers.
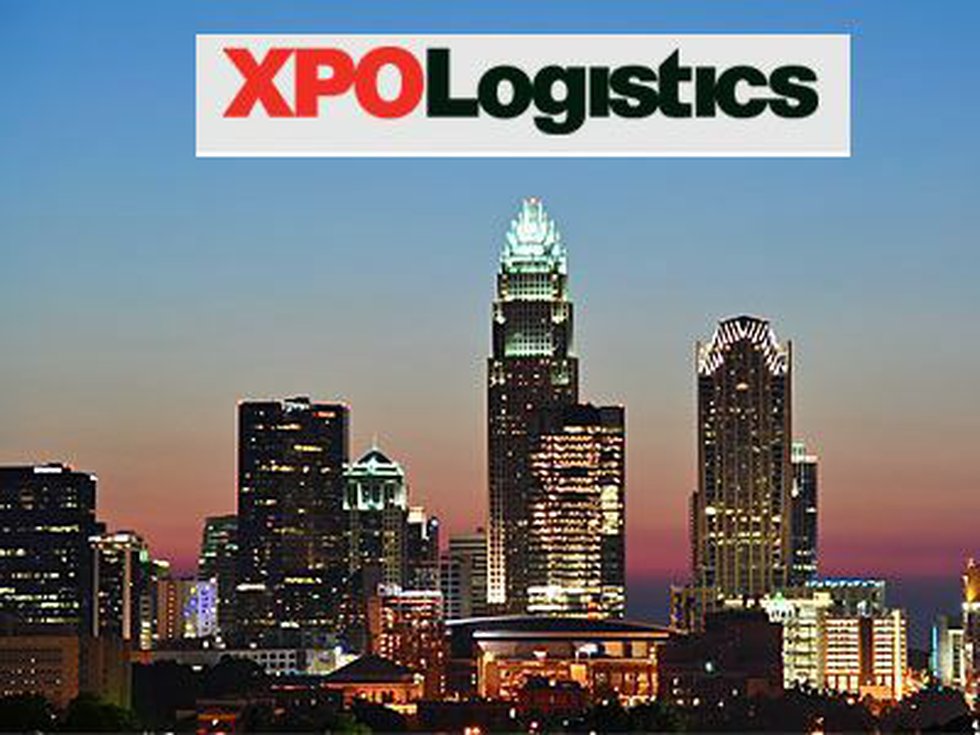
This job requires excellent communication skills. Engineers need to be able communicate complex engineering concepts in a simple and understandable way. Engineering often involves complicated calculations and mathematics. An engineer in production may use equations to calculate the cost of a finished product or solve problems on the manufacturing line.
Education Required
First, earn a bachelor’s degree in industrial or manufacturing engineering to get a job as a production engineer. Employers may prefer to have a master's degree especially for positions in research-oriented manufacturing. It's also helpful to possess proficiency in one or more specialized areas.
Industrial engineers bring creativity and analysis to improve the efficiency in production processes. They are interested in reducing waste and developing new ways to make use of equipment and workers. They must also have good communication skills, as they must be able to explain complex processes to non-technical audiences. Good communication skills also involve being able to listen carefully and fully understand the views and opinions of others.
During the degree program, manufacturing engineers receive hands-on training. They will also be taught safety regulations and procedures. A Professional Engineer license issued by the National Society of Professional Engineers is required. This license is vital as it informs clients and employers that you have the required credentials. You should also renew your license in accordance with state requirements.
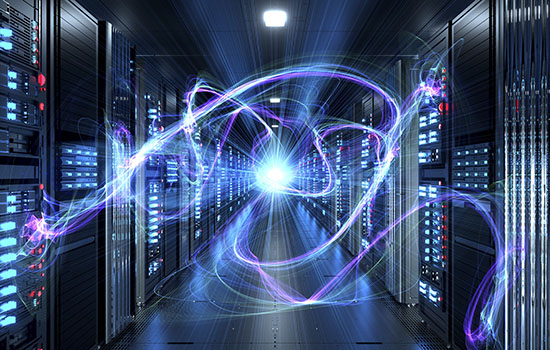
Salary
The salary for a production engineer can vary depending on where they work and what company they are working for. Production engineers usually work in an office environment. However they may occasionally travel to production sites to inspect machinery, improve processes and perform other tasks. Some production engineers work independently, while others work in larger companies. Production engineers are expected to not only earn a decent salary, but to also complete their work quickly.
Production engineers are part of a team that works with other professionals in order to ensure safety and quality. They also work closely alongside designers to ensure efficient production processes. In some cases they will also be responsible to maintain safety standards on the factory floor as well as train workers on safe procedures. Although this job description is not exhaustive, it provides an overview of the duties and responsibilities for a production engineer.
The salary of a production engineer depends on his or her level of experience. Entry-level production engineers earn approximately Rs2.5 lakhs annually. Mid-level engineers could earn Rs3.8 Lakhs. In the meantime, production engineers with experience can expect to earn up to Rs6.1 million annually.
FAQ
What are manufacturing and logistic?
Manufacturing is the production of goods using raw materials. Logistics encompasses the management of all aspects associated with supply chain activities such as procurement, production planning, distribution and inventory control. It also includes customer service. Manufacturing and logistics are often considered together as a broader term that encompasses both the process of creating products and delivering them to customers.
What is the difference in Production Planning and Scheduling, you ask?
Production Planning (PP), also known as forecasting and identifying production capacities, is the process that determines what product needs to be produced at any particular time. This can be done by forecasting demand and identifying production capabilities.
Scheduling involves the assignment of dates and times to tasks in order to complete them within the timeframe.
What is the importance of logistics in manufacturing?
Logistics are essential to any business. They are essential to any business's success.
Logistics plays a significant role in reducing cost and increasing efficiency.
Statistics
- You can multiply the result by 100 to get the total percent of monthly overhead. (investopedia.com)
- In the United States, for example, manufacturing makes up 15% of the economic output. (twi-global.com)
- [54][55] These are the top 50 countries by the total value of manufacturing output in US dollars for its noted year according to World Bank.[56] (en.wikipedia.org)
- Job #1 is delivering the ordered product according to specifications: color, size, brand, and quantity. (netsuite.com)
- Many factories witnessed a 30% increase in output due to the shift to electric motors. (en.wikipedia.org)
External Links
How To
How to Use Six Sigma in Manufacturing
Six Sigma is defined as "the application of statistical process control (SPC) techniques to achieve continuous improvement." Motorola's Quality Improvement Department in Tokyo, Japan developed Six Sigma in 1986. Six Sigma's core idea is to improve the quality of processes by standardizing and eliminating defects. In recent years, many companies have adopted this method because they believe there is no such thing as perfect products or services. Six Sigma's main objective is to reduce variations from the production average. This means that you can take a sample from your product and then compare its performance to the average to find out how often the process differs from the norm. If it is too large, it means that there are problems.
Understanding the dynamics of variability within your business is the first step in Six Sigma. Once you have a good understanding of the basics, you can identify potential sources of variation. This will allow you to decide if these variations are random and systematic. Random variations are caused by human errors. Systematic variations can be caused by outside factors. If you make widgets and some of them end up on the assembly line, then those are considered random variations. You might notice that your widgets always fall apart at the same place every time you put them together.
Once you identify the problem areas, it is time to create solutions. This could mean changing your approach or redesigning the entire process. After implementing the new changes, you should test them again to see if they worked. If they didn't work, then you'll need to go back to the drawing board and come up with another plan.