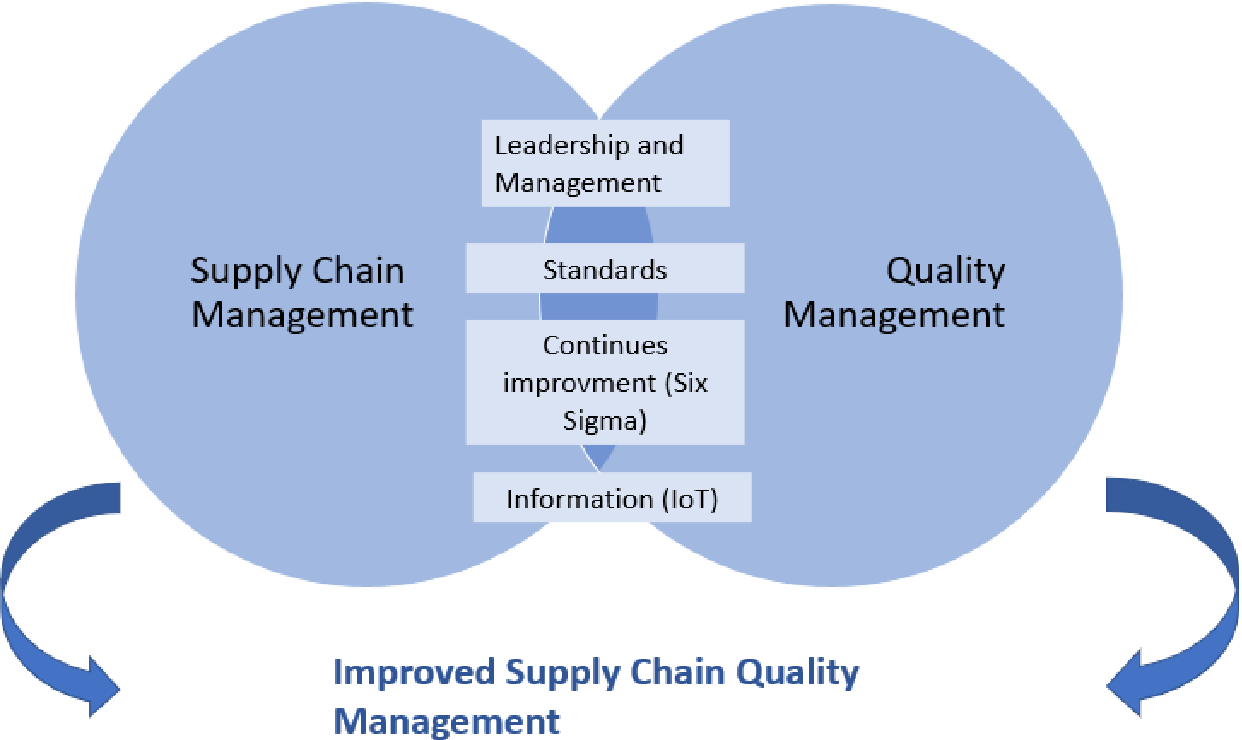
Medical equipment manufacturers create products that are used in hospitals, by hospital staff, doctors, researchers, and lab technicians. These companies produce a wide range of medical equipment, including wheelchairs, oxygen tanks and ventilators. The medical industry is expected to reach $135 billion in 2024.
Transport Equipment
Transport of some medical equipment is done by truck and airplane. These medical equipments can be transported anywhere in the United States or even internationally. The manufacturers of this equipment must also have a reliable transportation system.
Manufacturing:
Injection molding and micromachining are some of the popular processes in the manufacture of medical devices. These processes require specialized machines, high-quality material and sterile environments.
You Need the Right Certification
FDA will regulate many of the products produced in this industry. A medical device maker must be ISO 13485 accredited to ensure compliance. This non-government organisation inspects and certifies manufacturing companies based on their quality and consistency.
Usability:
One of the most important factors when designing a device is its user-friendliness. It should be simple to use and operate for both the users and the manufacturers. This can include many factors, such as the size and form of the product and its ease in handling and moving.
The design of the product:
When designing a medical device, it is important to consider all of the components that will make up the final product. This includes its shape, its materials and any special features. Also, it's important that you make sure the item is safe to use.
The Best Medical Devices:
Some of the most successful medical equipments have been designed to be easy to use and able to perform their intended function. This will help to increase their longevity and success in the market.
Also, it is important that the medical device be made of materials that are easy to disinfect and clean. This can help to reduce the risk of cross contamination and infection.
In addition to these considerations, medical devices should be designed to fit specific medical applications. This is true in particular for devices attached to the body, or any other equipment/tools.
It is also well-known for its large variety of products, which can be tailored to meet a wide range of medical preferences and needs. It offers wheelchairs and equipment that can be adjusted according to the height of the patient.
Merit Medical is a world-renowned medical equipment manufacturer. It strives for innovative products that can change the lives of patients and healthcare professionals around the globe. Merit Medical's commitment to high-quality products, innovation, and customer service has made it a leading supplier of proprietary disposable medical devices.
FAQ
What skills are required to be a production manager?
A production planner must be organized, flexible, and able multitask to succeed. Effective communication with clients and colleagues is essential.
What is production planning?
Production Planning includes planning for all aspects related to production. This document ensures that everything is prepared and available when you are ready for shooting. This document should also include information on how to get the best result on set. It should include information about shooting locations, casting lists, crew details, equipment requirements, and shooting schedules.
The first step is to decide what you want. You may already know where you want the film to be shot, or perhaps you have specific locations and sets you wish to use. Once you have identified your locations and scenes, you can start working out which elements you require for each scene. If you decide you need a car and don't know what model to choose, this could be an example. This is where you can look up car models online and narrow down your options by choosing from different makes and models.
Once you have found the right car, you can start thinking about extras. What about additional seating? Or maybe you just need someone to push the car around. Maybe you'd like to change the interior from black to a white color. These questions can help you decide the right look for your car. You can also think about the type of shots you want to get. Are you going to be shooting close-ups? Or wide angles? Maybe you want to show your engine or the steering wheel. This will allow you to determine the type of car you want.
Once you have all the information, you are ready to create a plan. The schedule will show you when to begin shooting and when to stop. You will need to know when you have to be there, what time you have to leave and when your return home. So everyone is clear about what they need to do. You can also make sure to book extra staff in advance if you have to hire them. You should not hire anyone who doesn't show up because of your inaction.
When creating your schedule, you will also need to consider the number of days you need to film. Some projects can be completed in a matter of days or weeks. Others may take several days. While creating your schedule, it is important to remember whether you will require more than one shot per day. Multiple shots at the same location can increase costs and make it more difficult to complete. If you are unsure if you need multiple takes, it is better to err on the side of caution and shoot fewer takes rather than risk wasting money.
Budgeting is another crucial aspect of production plan. A realistic budget will help you work within your means. You can always lower the budget if you encounter unexpected problems. It is important to not overestimate how much you will spend. You'll end up with less money after paying for other things if the cost is underestimated.
Planning production is a tedious process. Once you have a good understanding of how everything works together, planning future projects becomes easy.
What are the 7 Rs of logistics?
The acronym 7Rs of Logistics refers to the seven core principles of logistics management. It was developed by the International Association of Business Logisticians (IABL) and published in 2004 as part of its "Seven Principles of Logistics Management" series.
The following letters make up the acronym:
-
Responsible - to ensure that all actions are within the legal requirements and are not detrimental to others.
-
Reliable: Have faith in your ability or the ability to honor any promises made.
-
It is reasonable to use resources efficiently and not waste them.
-
Realistic - Consider all aspects of operations, including environmental impact and cost effectiveness.
-
Respectful: Treat others with fairness and equity
-
Responsive - Look for ways to save time and increase productivity.
-
Recognizable - Provide value-added services to customers
What is the responsibility of a production planner?
Production planners ensure that all project aspects are completed on time, within budget and within the scope. A production planner ensures that the service and product meet the client's expectations.
What is meant by manufacturing industries?
Manufacturing Industries refers to businesses that manufacture products. These products are sold to consumers. To accomplish this goal, these companies employ a range of processes including distribution, sales, management, and production. They create goods from raw materials, using machines and various other equipment. This includes all types if manufactured goods.
How can we improve manufacturing efficiency?
The first step is to determine the key factors that impact production time. We then need to figure out how to improve these variables. If you aren't sure where to begin, think about the factors that have the greatest impact on production time. Once you've identified them all, find solutions to each one.
What does warehouse refer to?
Warehouses and storage facilities are where goods are kept before being sold. You can have it indoors or outdoors. In some cases it could be both indoors and outdoors.
Statistics
- According to a Statista study, U.S. businesses spent $1.63 trillion on logistics in 2019, moving goods from origin to end user through various supply chain network segments. (netsuite.com)
- Many factories witnessed a 30% increase in output due to the shift to electric motors. (en.wikipedia.org)
- According to the United Nations Industrial Development Organization (UNIDO), China is the top manufacturer worldwide by 2019 output, producing 28.7% of the total global manufacturing output, followed by the United States, Japan, Germany, and India.[52][53] (en.wikipedia.org)
- In 2021, an estimated 12.1 million Americans work in the manufacturing sector.6 (investopedia.com)
- You can multiply the result by 100 to get the total percent of monthly overhead. (investopedia.com)
External Links
How To
How to Use Six Sigma in Manufacturing
Six Sigma can be described as "the use of statistical process control (SPC), techniques to achieve continuous improvement." Motorola's Quality Improvement Department created Six Sigma at their Tokyo plant, Japan in 1986. Six Sigma's core idea is to improve the quality of processes by standardizing and eliminating defects. Since there are no perfect products, or services, this approach has been adopted by many companies over the years. Six Sigma's primary goal is to reduce variation from the average value of production. This means that if you take a sample of your product, then measure its performance against the average, you can find out what percentage of the time the process deviates from the norm. If this deviation is too big, you know something needs fixing.
Understanding how your business' variability is a key step towards Six Sigma implementation is the first. Once you understand this, you can then identify the causes of variation. These variations can also be classified as random or systematic. Random variations are caused when people make mistakes. While systematic variations are caused outside of the process, they can occur. For example, if you're making widgets, and some of them fall off the assembly line, those would be considered random variations. It would be considered a systematic problem if every widget that you build falls apart at the same location each time.
After identifying the problem areas, you will need to devise solutions. This could mean changing your approach or redesigning the entire process. Once you have implemented the changes, it is important to test them again to ensure they work. If they don't work you need to rework them and come up a better plan.