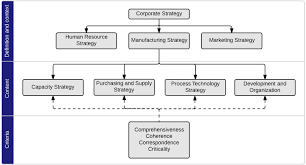
Logistics coordinators ensure that goods arrive on time and in a cost-effective manner. You'll be responsible for ensuring that goods get delivered to the customer in a timely fashion. Learn more about logistics in this article. We will also discuss the roles of customer service specialists, inventory analysts, and supply chain managers. Here are some of the most important jobs you will find in logistics.
Logistics coordinator
Monster has thousands upon thousands of job openings for logistic coordinators. This type of job requires a lot of hands-on training. Candidates who have little or no industry experience will be expected to complete the apprenticeship or internship. If you have prior experience in the logistics industry, you might be interested to apply for a job with Logistics Coordinator.
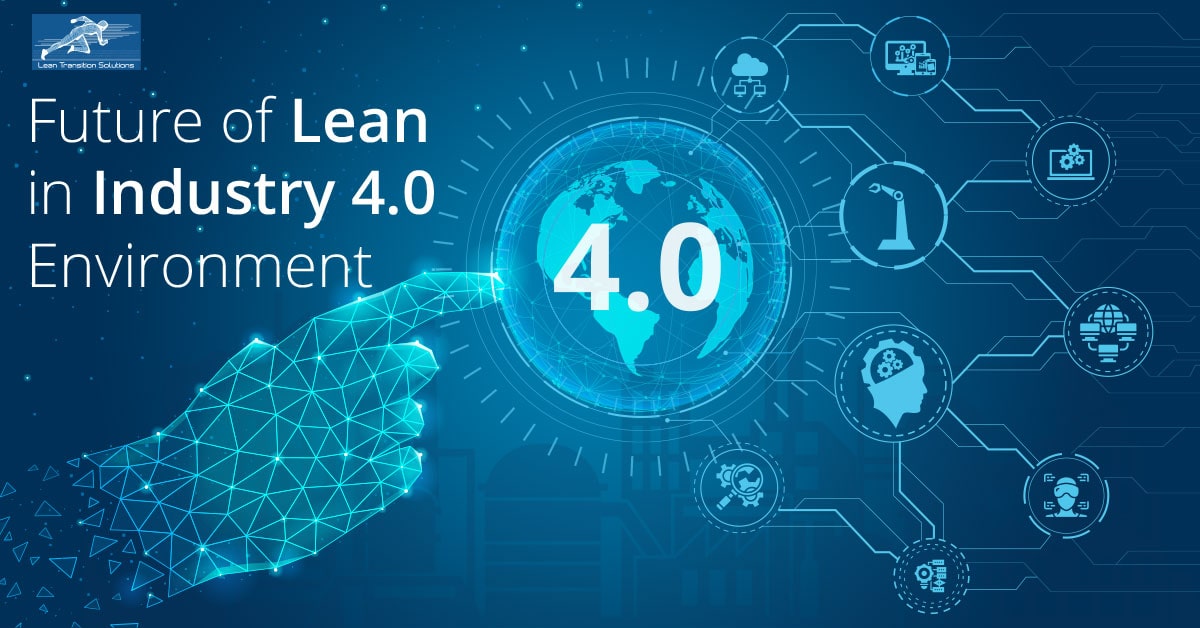
Customer service specialist
The customer service specialist manages and delivers customer service. They interact with customers on a daily basis, coordinate inland transportation, resolve customer complaints, and help them to resolve any issues. In addition to managing customer relationships, they also coordinate appointments, document special service needs, and schedule transportation and warehousing processes. As a customer services specialist, you will also coordinate the documentation and ensure that all necessary documents are properly documented to ensure timely delivery and budget compliance.
Analyst for inventory
An inventory analyst is responsible for maintaining service levels and improving overall inventory productivity. They are responsible for the fulfillment of all orders for TSC Feed programs and the management of the daily activities associated with inventory replenishment. They manage the inventory levels of their product categories and support assortment and merchandise plan. They analyze trends and data, and plan article-site replenishment in stores. They might also assist with promotion and marketing activities. They are responsible for analyzing sales data, and developing new strategies to increase business efficiency.
Supply chain manager
A supply chain manager oversees the movement of materials and goods from suppliers to manufacturers, customers, and more. A bachelor's degree is usually required for this role. Employers prefer candidates with master's degrees. You can apply for the job of supply chain manager in many ways. Learn more about this career. If you're thinking of going into supply chain management, consider getting an associate's degree in business administration first.
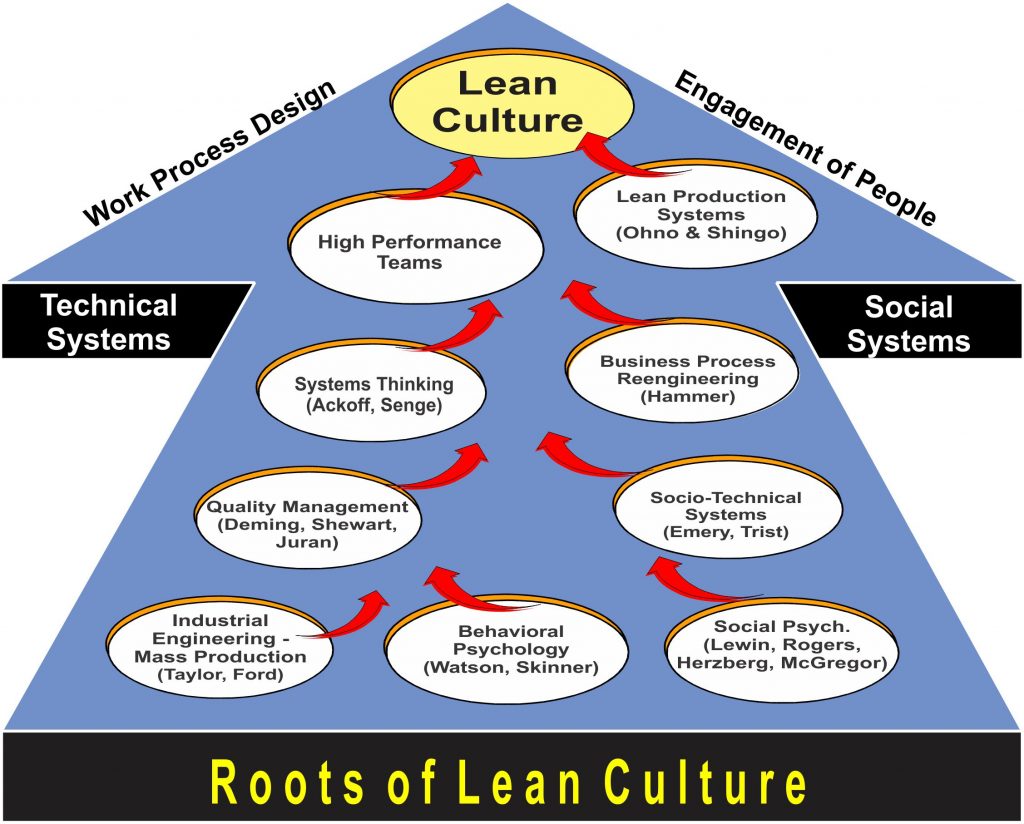
Freight agent
When creating your job description, include a section about your freight agent and cargo responsibilities. So that potential candidates can see what they have to do every day, the job description should include a list of key responsibilities. Use strong action verbs to grab the attention of qualified candidates. Your job description should include a detailed list indicating the qualifications you will need to fill this role.
FAQ
Why should you automate your warehouse?
Modern warehouses are increasingly dependent on automation. E-commerce has brought increased demand for more efficient and quicker delivery times.
Warehouses must be able to quickly adapt to changing demands. To do so, they must invest heavily in technology. Automation of warehouses offers many benefits. Here are some reasons why it's worth investing in automation:
-
Increases throughput/productivity
-
Reduces errors
-
Improves accuracy
-
Safety enhancements
-
Eliminates bottlenecks
-
This allows companies to scale easily
-
Makes workers more efficient
-
It gives visibility to everything that happens inside the warehouse
-
Enhances customer experience
-
Improves employee satisfaction
-
Reduces downtime and improves uptime
-
You can be sure that high-quality products will arrive on time
-
Human error can be eliminated
-
This helps to ensure compliance with regulations
How can we improve manufacturing efficiency?
First, determine which factors have the greatest impact on production time. Then we need to find ways to improve these factors. You can start by identifying the most important factors that impact production time. Once you identify them, look for solutions.
Do we need to know about Manufacturing Processes before learning about Logistics?
No. No. Understanding the manufacturing process will allow you to better understand logistics.
What does the term manufacturing industries mean?
Manufacturing Industries are companies that manufacture products. The people who buy these products are called consumers. This is accomplished by using a variety of processes, including production, distribution and retailing. They manufacture goods from raw materials using machines and other equipment. This includes all types and varieties of manufactured goods, such as food items, clothings, building supplies, furnitures, toys, electronics tools, machinery vehicles, pharmaceuticals medical devices, chemicals, among others.
Statistics
- In 2021, an estimated 12.1 million Americans work in the manufacturing sector.6 (investopedia.com)
- Job #1 is delivering the ordered product according to specifications: color, size, brand, and quantity. (netsuite.com)
- (2:04) MTO is a production technique wherein products are customized according to customer specifications, and production only starts after an order is received. (oracle.com)
- In the United States, for example, manufacturing makes up 15% of the economic output. (twi-global.com)
- You can multiply the result by 100 to get the total percent of monthly overhead. (investopedia.com)
External Links
How To
How to Use the Just-In-Time Method in Production
Just-intime (JIT), which is a method to minimize costs and maximize efficiency in business process, is one way. It's a way to ensure that you get the right resources at just the right time. This means that you only pay for what you actually use. Frederick Taylor first coined this term while working in the early 1900s as a foreman. Taylor observed that overtime was paid to workers if they were late in working. He realized that workers should have enough time to complete their jobs before they begin work. This would help increase productivity.
JIT teaches you to plan ahead and prepare everything so you don’t waste time. Look at your entire project, from start to end. Make sure you have enough resources in place to deal with any unexpected problems. If you anticipate that there might be problems, you'll have enough people and equipment to fix them. This way, you won't end up paying extra money for things that weren't really necessary.
There are many types of JIT methods.
-
Demand-driven JIT: You order the parts and materials you need for your project every other day. This will allow to track how much material has been used up. This will allow you to calculate how long it will take to make more.
-
Inventory-based: You stock materials in advance to make your projects easier. This allows you to predict how much you can expect to sell.
-
Project-driven: This method allows you to set aside enough funds for your project. Once you have an idea of how much material you will need, you can purchase the necessary materials.
-
Resource-based: This is the most common form of JIT. Here, you allocate certain resources based on demand. If you have many orders, you will assign more people to manage them. You'll have fewer orders if you have fewer.
-
Cost-based: This approach is very similar to resource-based. However, you don't just care about the number of people you have; you also need to consider how much each person will cost.
-
Price-based pricing: This is similar in concept to cost-based but instead you look at how much each worker costs, it looks at the overall company's price.
-
Material-based: This is very similar to cost-based but instead of looking at total costs of the company you are concerned with how many raw materials you use on an average.
-
Time-based: Another variation of resource-based JIT. Instead of worrying about how much each worker costs, you can focus on how long the project takes.
-
Quality-based JIT is another variant of resource-based JIT. Instead of looking at the labor costs and time it takes to make a product, think about its quality.
-
Value-based JIT is the newest form of JIT. You don't worry about whether the products work or if they meet customer expectations. Instead, your focus is on the value you bring to the market.
-
Stock-based. This method is inventory-based and focuses only on the actual production at any given point. It's used when you want to maximize production while minimizing inventory.
-
Just-in time (JIT), planning: This is a combination JIT/supply chain management. It's the process of scheduling delivery of components immediately after they are ordered. It's important because it reduces lead times and increases throughput.