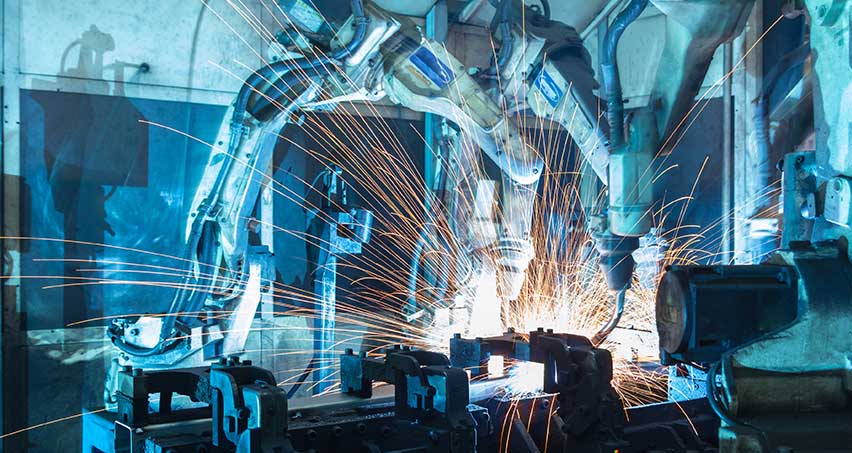
Visual management involves the transmission of information via visual signals. As information can be instantly identified, this process increases efficiency and clarity. There are many kinds of visual controls, including process control charts (FIFO lane), Lean daily management boards and process control tables. Below are some of the more common examples. Learn more about visual control and Lean manufacturing. Learn more. This is a great way for your company to adopt lean manufacturing.
Lean manufacturing
Andon is a Japanese word meaning status-display visualization. This method can be used to visual manage lean manufacturing. This technique allows supervisors and workers alike to see work-in progress, process flow, or any other pertinent information. Visual management allows easy labeling of workspaces as well as materials, parts, final goods, and waste. It allows for the identification of inefficiencies and simplifies processes. Listed below are some of the benefits of visual management in lean manufacturing.
Visible tools for visual management are a crucial component of the Lean methodology. Clear visual signals help supervisors and operators identify waste, improve process flow, and avoid errors. Safety concerns can be reduced by using clear visual signals. Forklift drivers can stay in the right areas by looking at floor markings and other visual indicators. Workers can be more productive by using visual management in lean production. In addition to reducing waste, visual management also minimizes safety risks.
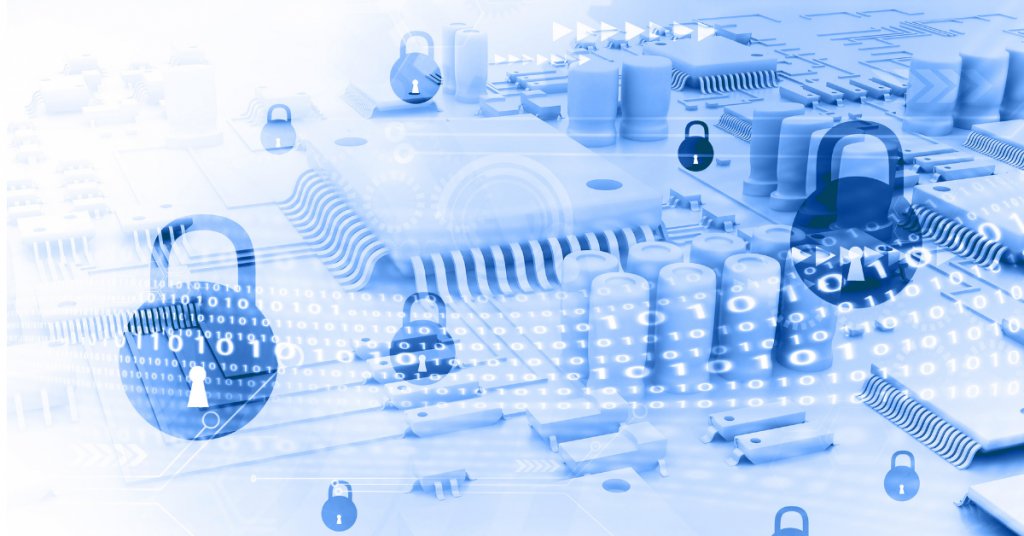
Process control charts
Process control charts can be a useful tool to visualize performance metrics and set a baseline for future enhancements. They also help improve output. They help management, operators, and other stakeholders get on the same page by identifying common causes of variation and setting the correct path for improvement. Because they show unusual patterns, these charts are very helpful in processes that are outof control. These process control charts are useful for visual management. They are easy to create, and can be used as visual indicators to see the status of any process.
Control charts are used to track the performance of processes over time. These charts display the sequence of samples and measurements that allow managers to determine whether or not the process is stable. These charts can also be used for analytic purposes to identify and propose solutions. An operator can compare the process’s performance with the baseline by using the centerline in the control chart. The control limits are typically three standard deviations above and below the centerline.
FIFO lane
FIFO lanes increase system throughput. Consider a fast food restaurant or assembly line. You have likely experienced the frustration of standing in a long line to get something. The FiFo lane is a visual management tool that helps you control the flow of work. It establishes priority in queues and allows for visual management. You can define these lanes by placing painted lines on the floor, markings on roller conveyors, and clearly marked shelf spaces. The first job that arrives from Process A would be placed in the first FIFO lane position. The next job would be taken into the next available position.
Time registration is one way to improve FIFO lane visual control. Employees can record the date and time when carts are loaded into a FIFO lane. Some employees use digital clocks for counting the products as soon as they are placed in the FIFO lane. To write times on carts, you can also use whiteboard stickers. These whiteboard stickers can be used to indicate the order of each step.
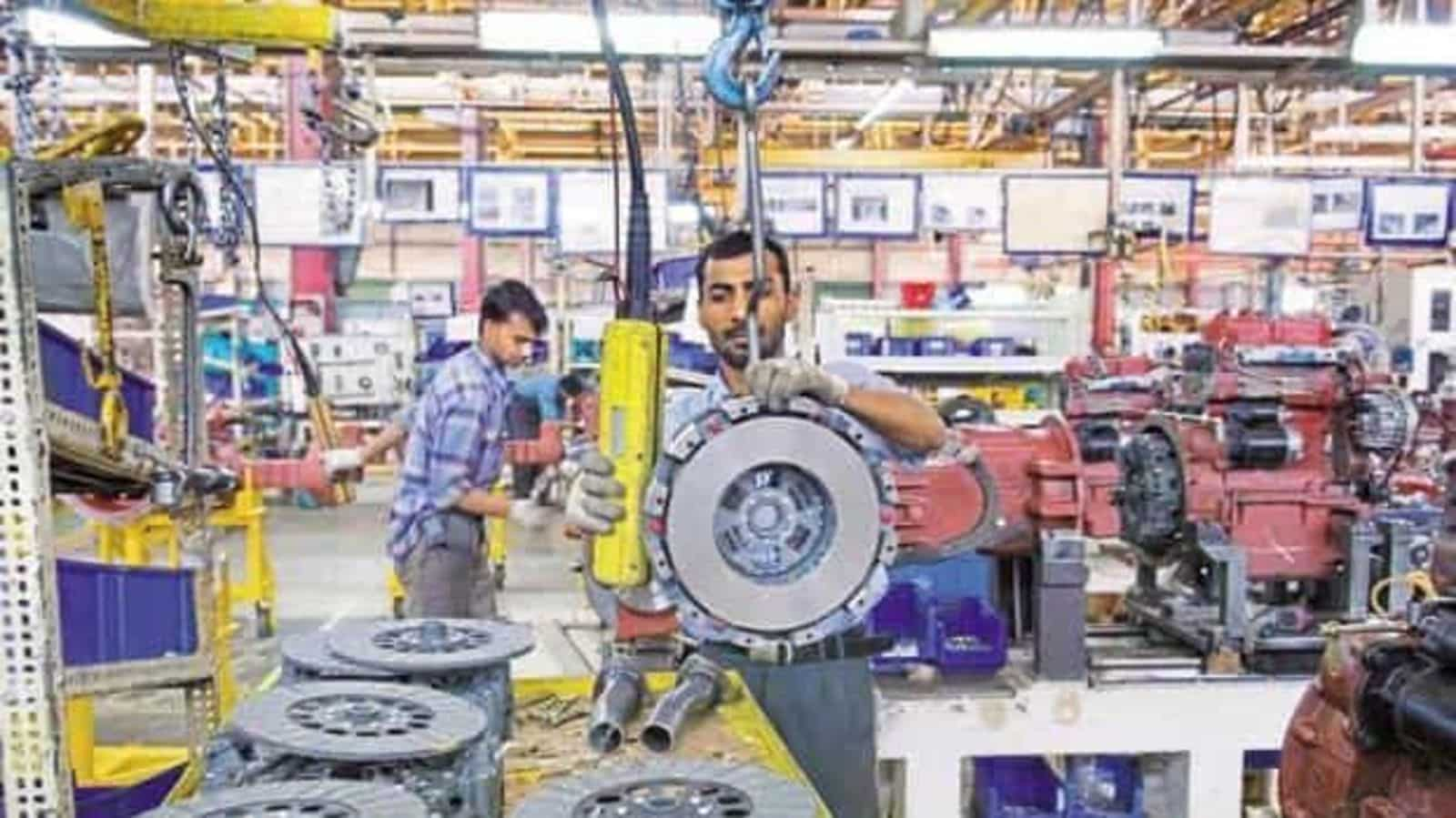
Lean daily management board
The Lean Daily Management Board was created by a multidisciplinary team based on five predetermined metrics: patient outcomes, documentation adherence, employee engagement, and productivity. Each day, the team met to review each area's progress. To verify every daily activity, the team used a checklist. They also used a problem solving tool to respond to any fallouts. Initial data collected January 2014 revealed a medication scan rate 75% and a rate of fall of 1.32/1000 days. These initial data did not include patient care or continuing education.
Instead of simply looking at a company's performance over time, daily managing makes it visible. Managers can then respond to problems as soon as they happen. Poor performers stretch out work to avoid being asked to do more. Poor performers must be able to clearly see the stretching work and account for the additional time and effort required to complete the work. While daily management isn't meant to be punitive, it does highlight any processes that may be inefficient or ineffective. People issues should be considered for those who are unable to point out a failure in a process.
FAQ
How can overproduction in manufacturing be reduced?
In order to reduce excess production, you need to develop better inventory management methods. This would reduce the time needed to manage inventory. This could help us free up our time for other productive tasks.
This can be done by using a Kanban system. A Kanban board can be used to monitor work progress. Kanban systems allow work items to move through different states until they reach their final destination. Each state has a different priority level.
When work is completed, it can be transferred to the next stage. A task that is still in the initial stages of a process will be considered complete until it moves on to the next stage.
This helps to keep work moving forward while ensuring that no work is left behind. With a Kanban board, managers can see exactly how much work is being done at any given moment. This allows them the ability to adjust their workflow using real-time data.
Lean manufacturing is another option to control inventory levels. Lean manufacturing works to eliminate waste throughout every stage of the production chain. Anything that does nothing to add value to a product is waste. There are several types of waste that you might encounter:
-
Overproduction
-
Inventory
-
Packaging that is not necessary
-
Exceed materials
By implementing these ideas, manufacturers can improve efficiency and cut costs.
What skills is required for a production planner?
Production planners must be flexible, organized, and able handle multiple tasks. Also, you must be able and willing to communicate with clients and coworkers.
What does "warehouse" mean?
Warehouses and storage facilities are where goods are kept before being sold. You can have it indoors or outdoors. It could be one or both.
What types of jobs can you find in logistics
There are many kinds of jobs available within logistics. Some of them are:
-
Warehouse workers: They load and unload trucks, pallets, and other cargo.
-
Transport drivers - These are people who drive trucks and trailers to transport goods or perform pick-ups.
-
Freight handlers: They sort and package freight in warehouses.
-
Inventory managers – They manage the inventory in warehouses.
-
Sales representatives - They sell products.
-
Logistics coordinators - They plan and organize logistics operations.
-
Purchasing agents – They buy goods or services necessary to run a company.
-
Customer service representatives - They answer calls and emails from customers.
-
Shippers clerks - They process shipping order and issue bills.
-
Order fillers - They fill orders based on what is ordered and shipped.
-
Quality control inspectors (QCI) - They inspect all incoming and departing products for potential defects.
-
Others - There is a variety of other jobs in logistics. These include transportation supervisors and cargo specialists.
Statistics
- Job #1 is delivering the ordered product according to specifications: color, size, brand, and quantity. (netsuite.com)
- It's estimated that 10.8% of the U.S. GDP in 2020 was contributed to manufacturing. (investopedia.com)
- Many factories witnessed a 30% increase in output due to the shift to electric motors. (en.wikipedia.org)
- (2:04) MTO is a production technique wherein products are customized according to customer specifications, and production only starts after an order is received. (oracle.com)
- You can multiply the result by 100 to get the total percent of monthly overhead. (investopedia.com)
External Links
How To
How to Use Six Sigma in Manufacturing
Six Sigma is defined as "the application of statistical process control (SPC) techniques to achieve continuous improvement." Motorola's Quality Improvement Department created Six Sigma at their Tokyo plant, Japan in 1986. The basic idea behind Six Sigma is to improve quality by improving processes through standardization and eliminating defects. Since there are no perfect products, or services, this approach has been adopted by many companies over the years. Six Sigma aims to reduce variation in the production's mean value. This means that you can take a sample from your product and then compare its performance to the average to find out how often the process differs from the norm. If you notice a large deviation, then it is time to fix it.
Understanding the dynamics of variability within your business is the first step in Six Sigma. Once you understand that, it is time to identify the sources of variation. It is important to identify whether the variations are random or systemic. Random variations are caused when people make mistakes. While systematic variations are caused outside of the process, they can occur. These are, for instance, random variations that occur when widgets are made and some fall off the production line. It would be considered a systematic problem if every widget that you build falls apart at the same location each time.
Once you've identified where the problems lie, you'll want to design solutions to eliminate those problems. The solution could involve changing how you do things, or redesigning your entire process. Test them again once you've implemented the changes. If they don't work you need to rework them and come up a better plan.