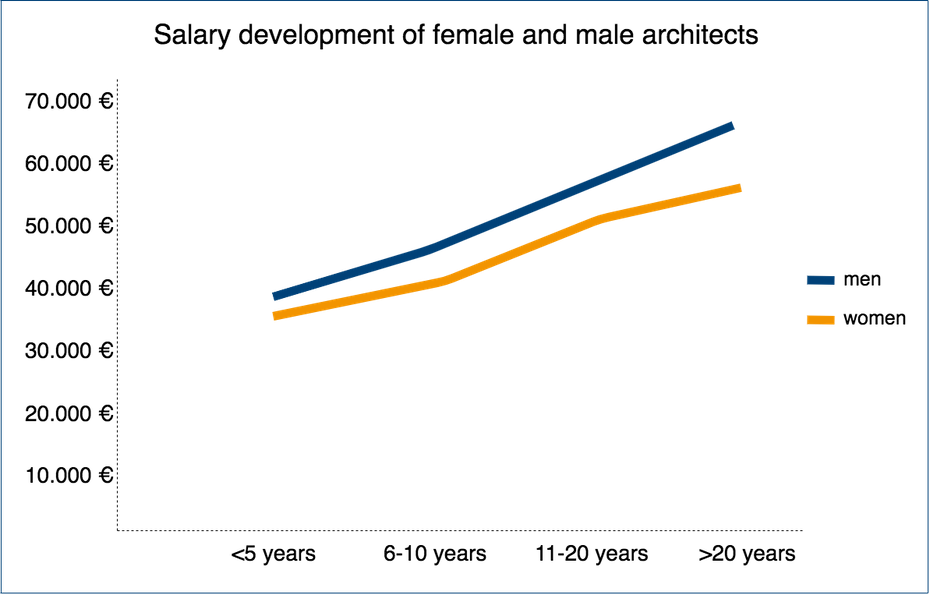
Maritime Engineers are qualified to manage and operate all components of a ship or boat. They are responsible for designing and building everything, from the ship's deck to the machinery within. They assist in solving maritime problems, and they also develop solutions. They work closely together with experts in related areas, such as oil rigs or offshore structures.
The salaries of marine engineers are attractive. Their salary varies according to their experience and education. Their salaries range from $17.061 to $458.998. It depends on their experience, qualifications and what type of boat or ship they work on. It also depends on what shipping company they work with.
Marine Engineers not only work at sea but also manage research projects. They create a computer model of a boat or ship, calculate stability and weight, then present their ideas to clients. They keep detailed records of the ship's machinery. These professionals also use diagnostic machinery to test the ship's functionality. They provide documentation and troubleshooting guidance.
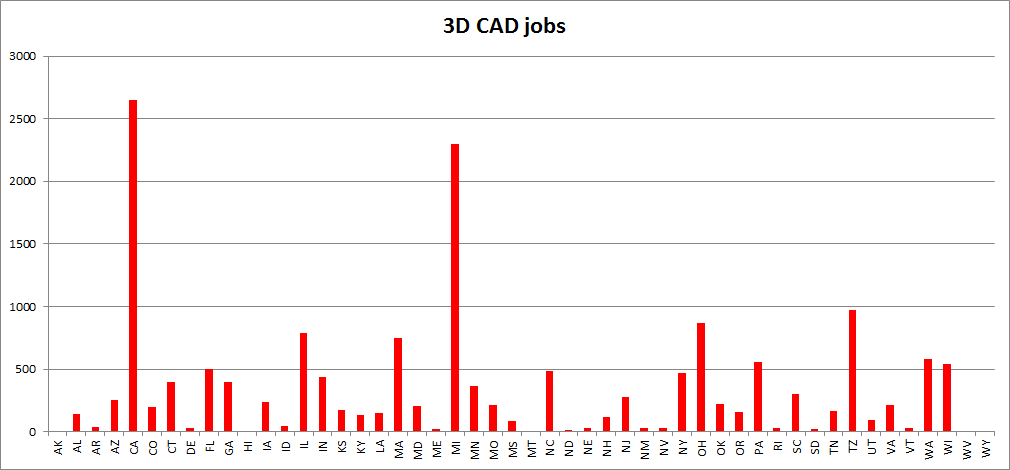
They should also be able collaborate with others. They must be familiar with their equipment and communicate well. They can operate engines, pumps and heaters as well as deck machines. They must also perform daily inspections, report on the situation, and test all equipment.
These professionals also conduct research and design marine technology. These professionals also have access computer software and can use their knowledge to solve various maritime problems. Marine engineers are usually employed in government agencies or private companies. They must pass a written as well as a physical exam in order to be granted a job. To be promoted, they must also pass an exam. They will also be paid vacation pay and bonuses.
The salary of a Marine Engineer also varies according to the type of ship he or she works on. The highest salaries are on cruise vessels, gas/oil vessels, and general cargo ships. The government sector has the lowest salary.
Marine Engineers are also trained to make 3D models of a ship or boat. They also have to inspect the ship daily, create reports, check for flaws and keep track of its machinery. They often work together with contractors and engineers to solve problems. They must ensure that everything runs according to the ship’s maintenance program.
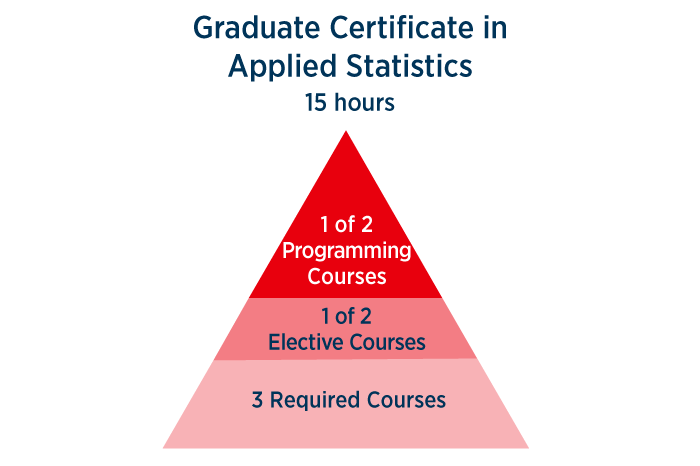
Marine Engineers not only have a responsibility, but they also work to solve various ecological issues. They collaborate closely with oceanographers, marine biologists and other experts in solving these problems. They have access computer software, various equipment, and other resources that can help them design solutions. They need to be able work under different conditions and communicate well.
The salary of a marine engineer depends on their education, experience, and what type of ship or boat they work on. The US salary ranges from $17,061 up to $458,998 for a Marine Engineering Engineer.
FAQ
What does it take for a logistics enterprise to succeed?
A successful logistics business requires a lot more than just knowledge. For clients and suppliers to be successful, you need to have excellent communication skills. You should be able analyse data and draw inferences. You need to be able work under pressure and manage stressful situations. You need to be innovative and creative to come up with new ways to increase efficiency. Strong leadership qualities are essential to motivate your team and help them achieve their organizational goals.
It is also important to be efficient and well organized in order meet deadlines.
How can manufacturing avoid production bottlenecks
The key to avoiding bottlenecks in production is to keep all processes running smoothly throughout the entire production cycle, from the time you receive an order until the time when the product ships.
This includes planning for capacity requirements as well as quality control measures.
This can be done by using continuous improvement techniques, such as Six Sigma.
Six Sigma Management System is a method to increase quality and reduce waste throughout your organization.
It focuses on eliminating variation and creating consistency in your work.
What is the role of a logistics manager
Logistics managers make sure all goods are delivered on schedule and without damage. This is achieved by using their knowledge and experience with the products of the company. He/she must also ensure sufficient stock to meet the demand.
What is production planning?
Production Planning is the creation of a plan to cover all aspects, such as scheduling, budgeting. Location, crew, equipment, props and other details. This document aims to ensure that everything is planned and ready when you are ready to shoot. This document should include information about how to achieve the best results on-set. This includes shooting schedules, locations, cast lists, crew details, and equipment requirements.
The first step is to decide what you want. You may have already chosen the location you want, or there are locations or sets you prefer. Once you have identified the scenes and locations, you can start to determine which elements are required for each scene. One example is if you are unsure of the exact model you want but decide that you require a car. In this case, you could start looking up cars online to find out what models are available and then narrow your choices by choosing between different makes and models.
After you've found the perfect car, it's time to start thinking about adding extras. Do you have people who need to be seated in the front seat? Or maybe you just need someone to push the car around. Maybe you'd like to change the interior from black to a white color. These questions will help to determine the style and feel of your car. Another thing you can do is think about what type of shots are desired. Will you be filming close-ups or wide angles? Maybe you want to show your engine or the steering wheel. These things will help you to identify the car that you are looking for.
Once you have made all the necessary decisions, you can start to create a schedule. A schedule will tell you when you need to start shooting and when you need to finish. A schedule for each day will detail when you should arrive at the location and when you need leave. So everyone is clear about what they need to do. You can also make sure to book extra staff in advance if you have to hire them. You should not hire anyone who doesn't show up because of your inaction.
Also, consider how many days you will be filming your schedule. Some projects can be completed in a matter of days or weeks. Others may take several days. When creating your schedule, be aware of whether you need more shots per day. Multiple shots at the same location can increase costs and make it more difficult to complete. It's better to be safe than sorry and shoot less takes if you're not certain whether you need more takes.
Budget setting is another important aspect in production planning. It is important to set a realistic budget so you can work within your budget. If you have to reduce your budget due to unexpected circumstances, you can always lower it later. You shouldn't underestimate the amount you'll spend. You will end up spending less money if you underestimate the cost of something.
Production planning is a complicated process. But once you understand how everything works together, it becomes much easier to plan future project.
Is automation important for manufacturing?
Automating is not just important for manufacturers, but also for service providers. They can provide services more quickly and efficiently thanks to automation. It helps them to lower costs by reducing human errors, and improving productivity.
How can manufacturing overproduction be reduced?
In order to reduce excess production, you need to develop better inventory management methods. This would reduce the time needed to manage inventory. We could use these resources to do other productive tasks.
You can do this by adopting a Kanban method. A Kanban board, a visual display to show the progress of work, is called a Kanban board. In a Kanban system, work items move through a sequence of states until they reach their final destination. Each state has a different priority level.
For instance, when work moves from one stage to another, the current task is complete enough to be moved to the next stage. However, if a task is still at the beginning stages, it will remain so until it reaches the end of the process.
This helps to keep work moving forward while ensuring that no work is left behind. A Kanban board allows managers to monitor how much work is being completed at any given moment. This data allows them adjust their workflow based upon real-time data.
Lean manufacturing is another option to control inventory levels. Lean manufacturing is about eliminating waste from all stages of the production process. Anything that doesn't add value to the product is considered waste. Some common types of waste include:
-
Overproduction
-
Inventory
-
Packaging not required
-
Exceed materials
Manufacturers can increase efficiency and decrease costs by implementing these ideas.
What are the 7 Rs of logistics.
The acronym 7Rs of Logistics refers to the seven core principles of logistics management. It was published in 2004 by the International Association of Business Logisticians as part of their "Seven Principles of Logistics Management" series.
The acronym consists of the following letters:
-
Responsible - ensure that all actions taken are within legal requirements and are not harmful to others.
-
Reliable – have faith in your ability and capability to keep promises.
-
It is reasonable to use resources efficiently and not waste them.
-
Realistic - Take into consideration all aspects of operations including cost-effectiveness, environmental impact, and other factors.
-
Respectful - show respect and treat others fairly and fairly
-
You are resourceful and look for ways to save money while increasing productivity.
-
Recognizable provides value-added products and services to customers
Statistics
- According to the United Nations Industrial Development Organization (UNIDO), China is the top manufacturer worldwide by 2019 output, producing 28.7% of the total global manufacturing output, followed by the United States, Japan, Germany, and India.[52][53] (en.wikipedia.org)
- In 2021, an estimated 12.1 million Americans work in the manufacturing sector.6 (investopedia.com)
- Many factories witnessed a 30% increase in output due to the shift to electric motors. (en.wikipedia.org)
- In the United States, for example, manufacturing makes up 15% of the economic output. (twi-global.com)
- [54][55] These are the top 50 countries by the total value of manufacturing output in US dollars for its noted year according to World Bank.[56] (en.wikipedia.org)
External Links
How To
How to use lean manufacturing in the production of goods
Lean manufacturing refers to a method of managing that seeks to improve efficiency and decrease waste. It was developed in Japan during the 1970s and 1980s by Taiichi Ohno, who received the Toyota Production System (TPS) award from TPS founder Kanji Toyoda. Michael L. Watkins published the first book on lean manufacturing in 1990.
Lean manufacturing is often defined as a set of principles used to improve the quality, speed, and cost of products and services. It emphasizes the elimination and minimization of waste in the value stream. Lean manufacturing is also known as just in time (JIT), zero defect total productive maintenance(TPM), and five-star (S). Lean manufacturing eliminates non-value-added tasks like inspection, rework, waiting.
In addition to improving product quality and reducing costs, lean manufacturing helps companies achieve their goals faster and reduces employee turnover. Lean Manufacturing is one of the most efficient ways to manage the entire value chains, including suppliers and customers as well distributors and retailers. Lean manufacturing is widely used in many industries. Toyota's philosophy is a great example of this. It has helped to create success in automobiles as well electronics, appliances and healthcare.
Five fundamental principles underlie lean manufacturing.
-
Define Value- Identify the added value your company brings to society. What makes you stand out from your competitors?
-
Reduce waste - Stop any activity that isn't adding value to the supply chains.
-
Create Flow. Ensure that your work is uninterrupted and flows seamlessly.
-
Standardize & Simplify - Make processes as consistent and repeatable as possible.
-
Develop Relationships: Establish personal relationships both with internal and external stakeholders.
Lean manufacturing, although not new, has seen renewed interest in the economic sector since 2008. Many businesses have adopted lean production techniques to make them more competitive. In fact, some economists believe that lean manufacturing will be an important factor in economic recovery.
With many benefits, lean manufacturing is becoming more common in the automotive industry. These benefits include increased customer satisfaction, reduced inventory levels and lower operating costs.
Lean manufacturing can be applied to almost every aspect of an organization. This is because it ensures efficiency and effectiveness in all stages of the value chain.
There are three types of lean manufacturing.
-
Just-in Time Manufacturing (JIT), also known as "pull system": This form of lean manufacturing is often referred to simply as "pull". JIT is a method in which components are assembled right at the moment of use, rather than being manufactured ahead of time. This approach reduces lead time, increases availability and reduces inventory.
-
Zero Defects Manufacturing, (ZDM): ZDM is focused on ensuring that no defective products leave the manufacturing facility. If a part needs to be fixed during the assembly line, it should be repaired rather than scrapped. This is true even for finished products that only require minor repairs prior to shipping.
-
Continuous Improvement (CI: Continuous improvement aims to increase the efficiency of operations by constantly identifying and making improvements to reduce or eliminate waste. Continuous Improvement involves continuous improvement of processes.