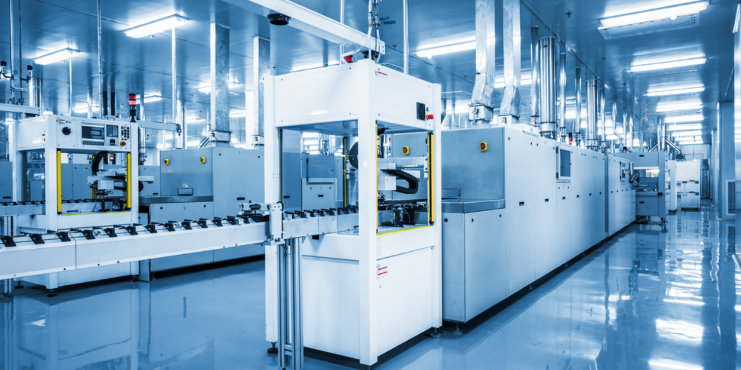
Industrial Engineering managers are essential members of the team. They are responsible for directing staff and improving production output. This includes overseeing and coordinating the layout and design for the factory floor as well the implementation of processes. Aside from providing technical expertise and knowledge, they also help organizations develop new products.
Managers in Industrial Engineering are responsible for creating and maintaining efficient manufacturing processes. This requires the knowledge of the latest trends in automation and robotics. They also need to monitor and maintain industrial procedures and ensure compliance to health and safety standards. They supervise the usage of raw materials, consumables, and other industrial processes. They also perform studies to improve workflows and space usage. The manager supervises all work projects including product cost reduction, cycle time and process improvement. They are also responsible for managing preventative maintenance plans.
This manager collaborates with other groups to develop new processes, improve efficiency, streamline operations, and create new partnerships. He or she is also responsible for the design and installation, as well as renovations to facilities. The manager also communicates technical information to other stakeholders as part of project management. A manager is responsible for securing resources and making site visits to suppliers' facilities. He/she advocates for team members, and ensures that quality compliance guidelines are followed.
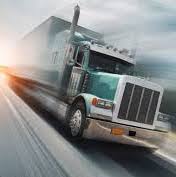
Managers in industrial engineering are expected be to be innovative, motivated, and able resolve problems. They need to be able and able to work in cold and hot environments. They must also be able communicate with all levels of employees.
A degree in engineering or another related field is necessary for industrial engineering managers. They should also have at most five years' experience in the field. Some employers prefer candidates with a postgraduate degree. Other skills they may need include project management or logistical expertise.
The Industrial Engineering Managers manage the design and development process for new products. They have a strong background for problem-solving and quality improvements. They thrive in a team environment. Managers are more successful when they are able to encourage employee growth.
Industrial Engineers excel at streamlining operations, and cutting down costs. They are skilled in manufacturing processes and can meet deadlines. They have also worked in human resources, logistics and vendor/supplier relations. They are proficient in setting goals, administering procedures, and creating budgets. They can also create strategies to increase efficiency in engineering projects.
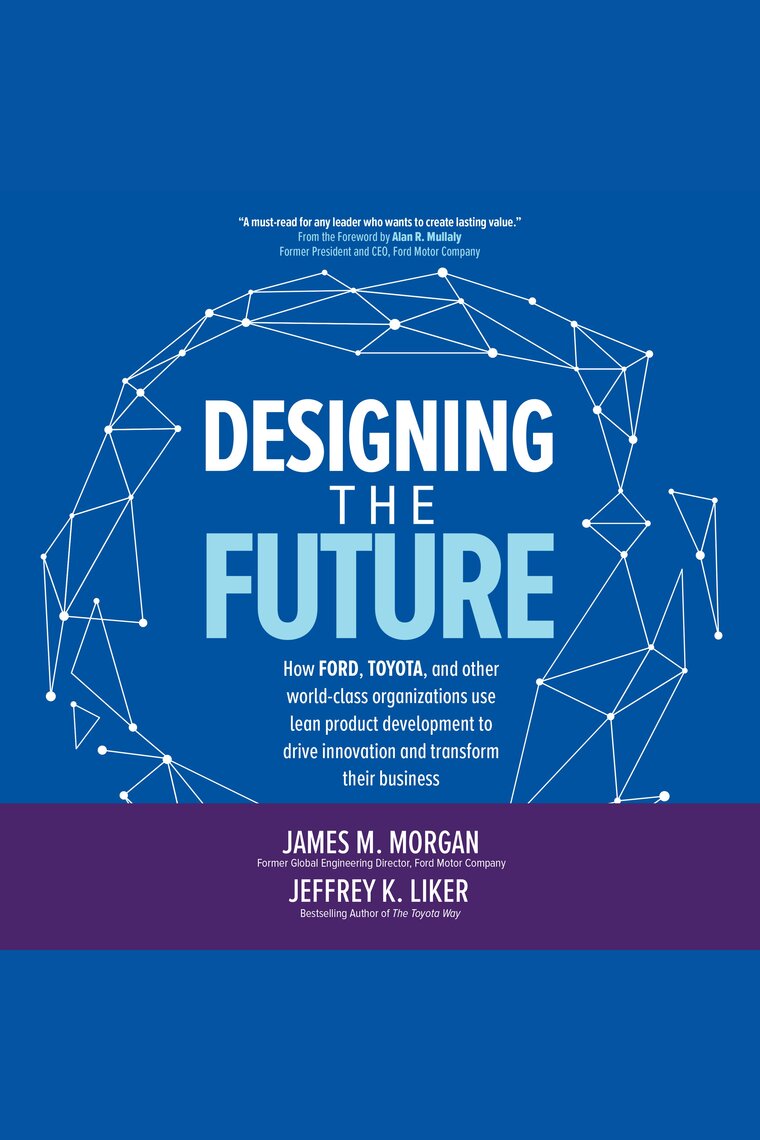
The industrial engineering manager may be responsible for the design and execution of new manufacturing procedures or operating equipment. They need to plan for new equipment and methods of operation using established standards and guidelines. They must also oversee the process of implementing waste elimination plans. They are also responsible in analyzing the factory's labor productivity.
Industrial engineering managers can contribute their expertise to the development of strategies for increasing productivity, creating new products and managing human resource. They can also aid in the development and improvement of existing processes.
FAQ
How can manufacturing reduce production bottlenecks?
Production bottlenecks can be avoided by ensuring that processes are running smoothly during the entire production process, starting with the receipt of an order and ending when the product ships.
This includes planning for both capacity requirements and quality control measures.
This can be done by using continuous improvement techniques, such as Six Sigma.
Six Sigma can be used to improve the quality and decrease waste in all areas of your company.
It seeks to eliminate variation and create consistency in your work.
How can manufacturing efficiency be improved?
The first step is to determine the key factors that impact production time. Then we need to find ways to improve these factors. You can start by identifying the most important factors that impact production time. Once you identify them, look for solutions.
What makes a production planner different from a project manger?
A production planner is more involved in the planning phase of the project than a project manger.
What skills does a production planner need?
You must be flexible and organized to become a productive production planner. Also, you must be able and willing to communicate with clients and coworkers.
How can manufacturing excess production be decreased?
It is essential to find better ways to manage inventory to reduce overproduction. This would reduce the time needed to manage inventory. This would allow us to use our resources for more productive tasks.
One way to do this is to adopt a Kanban system. A Kanban board is a visual display used to track work in progress. A Kanban system allows work items to move through several states before reaching their final destination. Each state has a different priority level.
For instance, when work moves from one stage to another, the current task is complete enough to be moved to the next stage. A task that is still in the initial stages of a process will be considered complete until it moves on to the next stage.
This allows you to keep work moving along while making sure that no work gets neglected. Managers can monitor the work being done by Kanban boards to see what is happening at any given time. This data allows them adjust their workflow based upon real-time data.
Another way to control inventory levels is to implement lean manufacturing. Lean manufacturing emphasizes eliminating waste in all phases of production. Anything that does not contribute to the product's value is considered waste. Here are some examples of common types.
-
Overproduction
-
Inventory
-
Unnecessary packaging
-
Excess materials
Manufacturers can reduce their costs and improve their efficiency by using these ideas.
What is the best way to learn about manufacturing?
The best way to learn about manufacturing is through hands-on experience. But if that is not possible you can always read books and watch educational videos.
Can some manufacturing processes be automated?
Yes! Since ancient times, automation has been in existence. The Egyptians invent the wheel thousands of year ago. Today, robots assist in the assembly of lines.
There are many uses of robotics today in manufacturing. These include:
-
Robots for assembly line
-
Robot welding
-
Robot painting
-
Robotics inspection
-
Robots that produce products
Automation could also be used to improve manufacturing. 3D printing is a way to make custom products quickly and without waiting weeks or months for them to be manufactured.
Statistics
- It's estimated that 10.8% of the U.S. GDP in 2020 was contributed to manufacturing. (investopedia.com)
- [54][55] These are the top 50 countries by the total value of manufacturing output in US dollars for its noted year according to World Bank.[56] (en.wikipedia.org)
- Job #1 is delivering the ordered product according to specifications: color, size, brand, and quantity. (netsuite.com)
- You can multiply the result by 100 to get the total percent of monthly overhead. (investopedia.com)
- According to the United Nations Industrial Development Organization (UNIDO), China is the top manufacturer worldwide by 2019 output, producing 28.7% of the total global manufacturing output, followed by the United States, Japan, Germany, and India.[52][53] (en.wikipedia.org)
External Links
How To
Six Sigma in Manufacturing
Six Sigma is defined as "the application of statistical process control (SPC) techniques to achieve continuous improvement." Motorola's Quality Improvement Department in Tokyo, Japan developed Six Sigma in 1986. Six Sigma's basic concept is to improve quality and eliminate defects through standardization. Many companies have adopted this method in recent years. They believe there is no such thing a perfect product or service. Six Sigma seeks to reduce variation between the mean production value. This means that if you take a sample of your product, then measure its performance against the average, you can find out what percentage of the time the process deviates from the norm. If there is a significant deviation from the norm, you will know that something needs to change.
The first step toward implementing Six Sigma is understanding how variability works in your business. Once you have a good understanding of the basics, you can identify potential sources of variation. Also, you will need to identify the sources of variation. Random variations occur when people do mistakes. Symmetrical variations are caused due to factors beyond the process. You could consider random variations if some widgets fall off the assembly lines. However, if you notice that every time you assemble a widget, it always falls apart at exactly the same place, then that would be a systematic problem.
Once you've identified the problem areas you need to find solutions. It might mean changing the way you do business or redesigning it entirely. Once you have implemented the changes, it is important to test them again to ensure they work. If they didn't work, then you'll need to go back to the drawing board and come up with another plan.