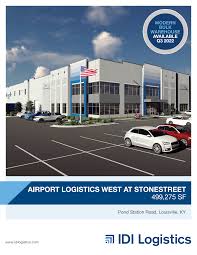
Kanban is a method of reducing costs and improving efficiency in manufacturing. These principles minimize downtime and reduce inefficiencies. They result in faster manufacturing, delivery and customer service. It also allows continuous improvement.
Kanban is a method to manage and organize work flow. It allows manufacturers and teams to monitor and track their work and increase productivity. Kanban is a visual system that displays all the steps in a process and helps to identify and minimize inefficiencies.
The kanban method can be implemented manually, or with the use of a software application. The software will help team members decide what to do and who to do it. This software will optimize the process. Kanban allows employees to give feedback and improve their processes. It can also be used as a brainstorming tool.
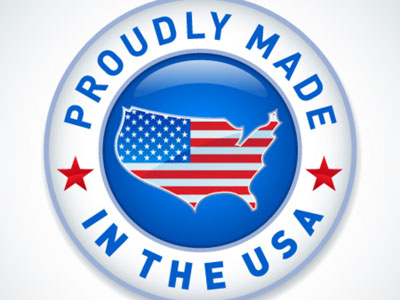
Kanban boards are a very popular example of Kanban. These boards depict a process. The board displays the sequence of steps involved in the process and their priority. First, contact a supplier. The second task will be to order the supplies required to complete your work. The third task, manufacturing. The fourth task, testing and shipping the final product.
Kanban allows teams to visualize their process and make small adjustments as needed. You can use the kanban board to improve communication between teams and identify and fix any bottlenecks.
Kanban also helps to eliminate waste and promote information sharing. This is especially helpful when the company wants to adopt lean principles. It is possible to accumulate waste over the course of a manufacturing operation in many ways. If a manufacturer eliminates waste, it adds true value to all phases of the production process. Kanban can also be used for inventory management. It can be used to manage inventory overstocking.
Kanban is a great way of visualizing the process and to cut costs. Kanban can help improve efficiency and reduce the number of items required to complete a job. It improves communication and minimizes downtime. The kanban approach is a wonderful example of how technology can be used in order to complete a seemingly difficult task.
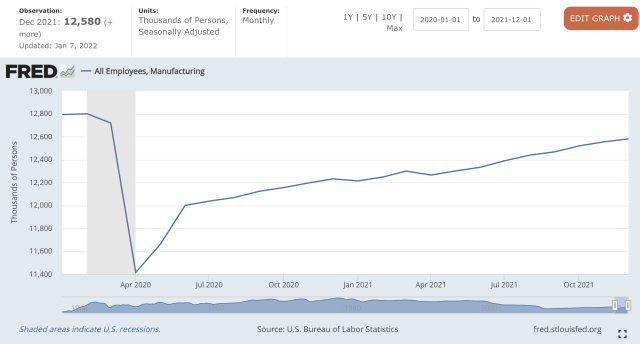
The kanban method is also useful as a brainstorming tool, and to improve productivity. It can be used for connecting companies with suppliers and improving communication. It helps improve quality and speed up the production process.
A board is one of the most popular Kanban examples in manufacturing. Here tasks are grouped by priority and time taken to complete them. The board also displays the steps involved in a process, such as design, manufacturing, and testing.
FAQ
What is the best way to learn about manufacturing?
You can learn the most about manufacturing by getting involved in it. If that is not possible, you could always read books or view educational videos.
What is production planning?
Production planning is the process of creating a plan that covers all aspects of production. This includes scheduling, budgeting and crew, location, equipment, props, and more. This document will ensure everything is in order and ready to go when you need it. It should also provide information about how best to produce the best results while on set. This information includes locations, crew details and equipment requirements.
The first step in filming is to define what you want. You may have already decided where you would like to shoot, or maybe there are specific locations or sets that you want to use. Once you have identified the scenes and locations, you can start to determine which elements are required for each scene. One example is if you are unsure of the exact model you want but decide that you require a car. If this is the case, you might start searching online for car models and then narrow your options by selecting from different makes.
Once you have found the right vehicle, you can think about adding accessories. Do you need people sitting in the front seats? You might also need someone to help you get around the back. You may want to change the interior's color from black or white. These questions will help you determine the exact look and feel of your car. The type of shots that you are looking for is another thing to consider. You will be filming close-ups and wide angles. Perhaps you want to show the engine or the steering wheel? All of these things will help you identify the exact style of car you want to film.
Once you have established all the details, you can create a schedule. You will know when you should start and when you should finish shooting. The schedule will show you when to get there, what time to leave, and when to return home. It will help everyone know exactly what they have to do and when. If you need to hire extra staff, you can make sure you book them in advance. You should not hire anyone who doesn't show up because of your inaction.
Also, consider how many days you will be filming your schedule. Some projects are quick and easy, while others take weeks. When creating your schedule, be aware of whether you need more shots per day. Multiple takes at the same place will result in higher costs and longer completion times. If you are unsure if you need multiple takes, it is better to err on the side of caution and shoot fewer takes rather than risk wasting money.
Another important aspect of production planning is setting budgets. You will be able to manage your resources if you have a realistic budget. If you have to reduce your budget due to unexpected circumstances, you can always lower it later. It is important to not overestimate how much you will spend. If you underestimate how much something costs, you'll have less money to pay for other items.
Production planning is a complicated process. But once you understand how everything works together, it becomes much easier to plan future project.
Why is logistics important for manufacturing?
Logistics are an essential part of any business. They can help you achieve great success by helping you manage product flow from raw material to finished goods.
Logistics plays a significant role in reducing cost and increasing efficiency.
What is the difference between Production Planning and Scheduling?
Production Planning (PP) refers to the process of determining how much production is needed at any given moment. This is accomplished by forecasting the demand and identifying production resources.
Scheduling refers to the process of allocating specific dates to tasks in order that they can be completed within a specified timeframe.
What are the goods of logistics?
Logistics is the process of moving goods from one point to another.
They include all aspects associated with transport including packaging, loading transporting, unloading storage, warehousing inventory management customer service, distribution returns and recycling.
Logisticians ensure that the right product reaches the right place at the right time and under safe conditions. They provide information on demand forecasts as well stock levels, production schedules and availability of raw material.
They monitor shipments in transit, ensure quality standards, manage inventories, replenish orders, coordinate with suppliers and other vendors, and offer support services for sales, marketing, and customer service.
What does warehouse mean?
A warehouse is an area where goods are stored before being sold. It can be indoors or out. Sometimes, it can be both an indoor and outdoor space.
Why automate your factory?
Modern warehousing is becoming more automated. With the rise of ecommerce, there is a greater demand for faster delivery times as well as more efficient processes.
Warehouses have to be flexible to meet changing requirements. To do so, they must invest heavily in technology. Automation warehouses can bring many benefits. These are some of the benefits that automation can bring to warehouses:
-
Increases throughput/productivity
-
Reduces errors
-
Improves accuracy
-
Safety Boosts
-
Eliminates bottlenecks
-
This allows companies to scale easily
-
Makes workers more efficient
-
Gives you visibility into all that is happening in your warehouse
-
Enhances customer experience
-
Improves employee satisfaction
-
Reducing downtime and increasing uptime
-
High quality products delivered on-time
-
Human error can be eliminated
-
Helps ensure compliance with regulations
Statistics
- According to a Statista study, U.S. businesses spent $1.63 trillion on logistics in 2019, moving goods from origin to end user through various supply chain network segments. (netsuite.com)
- It's estimated that 10.8% of the U.S. GDP in 2020 was contributed to manufacturing. (investopedia.com)
- According to the United Nations Industrial Development Organization (UNIDO), China is the top manufacturer worldwide by 2019 output, producing 28.7% of the total global manufacturing output, followed by the United States, Japan, Germany, and India.[52][53] (en.wikipedia.org)
- Job #1 is delivering the ordered product according to specifications: color, size, brand, and quantity. (netsuite.com)
- In the United States, for example, manufacturing makes up 15% of the economic output. (twi-global.com)
External Links
How To
How to use Lean Manufacturing in the production of goods
Lean manufacturing is an approach to management that aims for efficiency and waste reduction. It was first developed in Japan in the 1970s/80s by Taiichi Ahno, who was awarded the Toyota Production System (TPS), award from KanjiToyoda, the founder of TPS. Michael L. Watkins published the "The Machine That Changed the World", the first book about lean manufacturing. It was published in 1990.
Lean manufacturing can be described as a set or principles that are used to improve quality, speed and cost of products or services. It emphasizes eliminating waste and defects throughout the value stream. Lean manufacturing is called just-in-time (JIT), zero defect, total productive maintenance (TPM), or 5S. Lean manufacturing seeks to eliminate non-value added activities, such as inspection, work, waiting, and rework.
Lean manufacturing not only improves product quality but also reduces costs. Companies can also achieve their goals faster by reducing employee turnover. Lean manufacturing can be used to manage all aspects of the value chain. Customers, suppliers, distributors, retailers and employees are all included. Lean manufacturing is widely used in many industries. For example, Toyota's philosophy underpins its success in automobiles, electronics, appliances, healthcare, chemical engineering, aerospace, paper, food, etc.
Five basic principles of Lean Manufacturing are included in lean manufacturing
-
Define Value: Identify the social value of your business and what sets you apart.
-
Reduce Waste – Eliminate all activities that don't add value throughout the supply chain.
-
Create Flow – Ensure that work flows smoothly throughout the process.
-
Standardize and simplify – Make processes as repeatable and consistent as possible.
-
Build Relationships - Establish personal relationships with both internal and external stakeholders.
Although lean manufacturing has always been around, it is gaining popularity in recent years because of a renewed interest for the economy after 2008's global financial crisis. Many businesses have adopted lean production techniques to make them more competitive. Many economists believe lean manufacturing will play a major role in economic recovery.
Lean manufacturing is becoming a popular practice in automotive. It has many advantages. These benefits include increased customer satisfaction, reduced inventory levels and lower operating costs.
It can be applied to any aspect of an organisation. Because it makes sure that all value chains are efficient and effectively managed, Lean Manufacturing is particularly helpful for organizations.
There are three types principally of lean manufacturing:
-
Just-in Time Manufacturing, (JIT): This kind of lean manufacturing is also commonly known as "pull-systems." JIT stands for a system where components are assembled on the spot rather than being made in advance. This approach reduces lead time, increases availability and reduces inventory.
-
Zero Defects Manufacturing, (ZDM): ZDM is focused on ensuring that no defective products leave the manufacturing facility. You should repair any part that needs to be repaired during an assembly line. This applies to finished goods that may require minor repairs before shipment.
-
Continuous Improvement (CI), also known as Continuous Improvement, aims at improving the efficiency of operations through continuous identification and improvement to minimize or eliminate waste. It involves continuous improvement of processes, people, and tools.