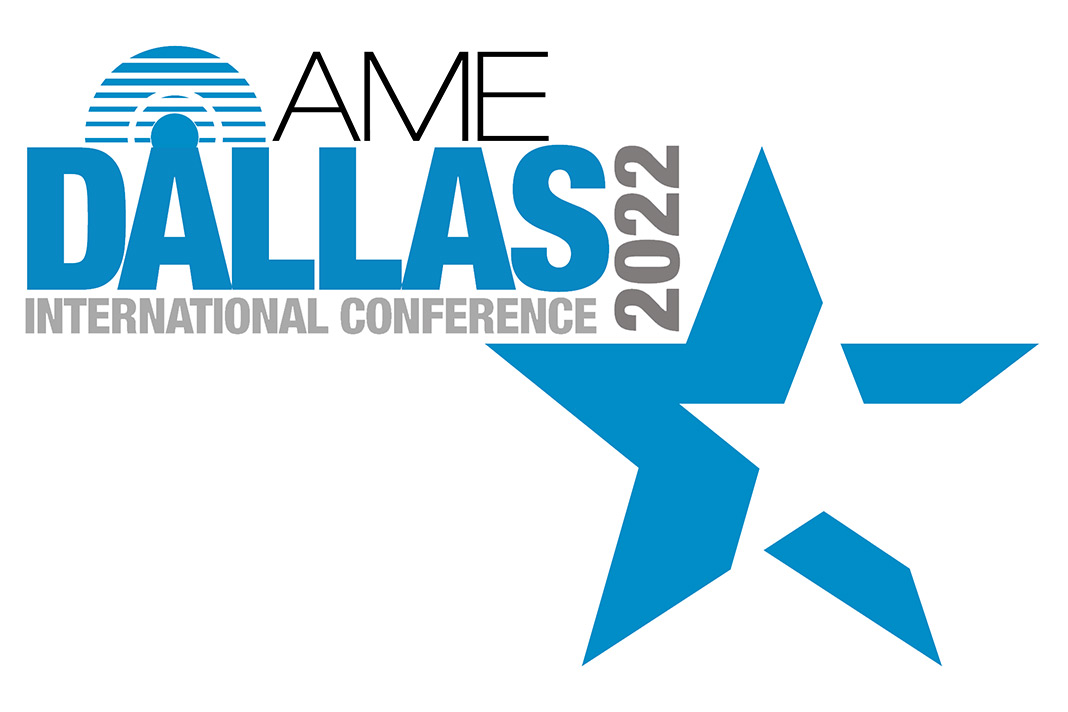
To become a drafter, one must have technical knowledge and the ability to translate design ideas into technical drawings. They also need to be able to work with other people to help produce the best results. They might need to know how to read engineering plans or how to use particular software programs. They might also need an understanding of engineering formulas that can be used to calculate measurement.
Drafters typically work for architectural and engineering firms. They create plans for buildings, structures, and other products using computer-aided design (CAD) software. Although they may work independently, many of these professionals work in teams to create unique designs. Although they are often full-time workers, they can also take on other jobs. Depending on the company they work for, they may be required to work overtime to meet deadlines.
An associate's degree is typically earned by drafting professionals from a community or technical college. A 4-year university program can allow them to continue their education. You may be able transfer your degree depending on what course you take.
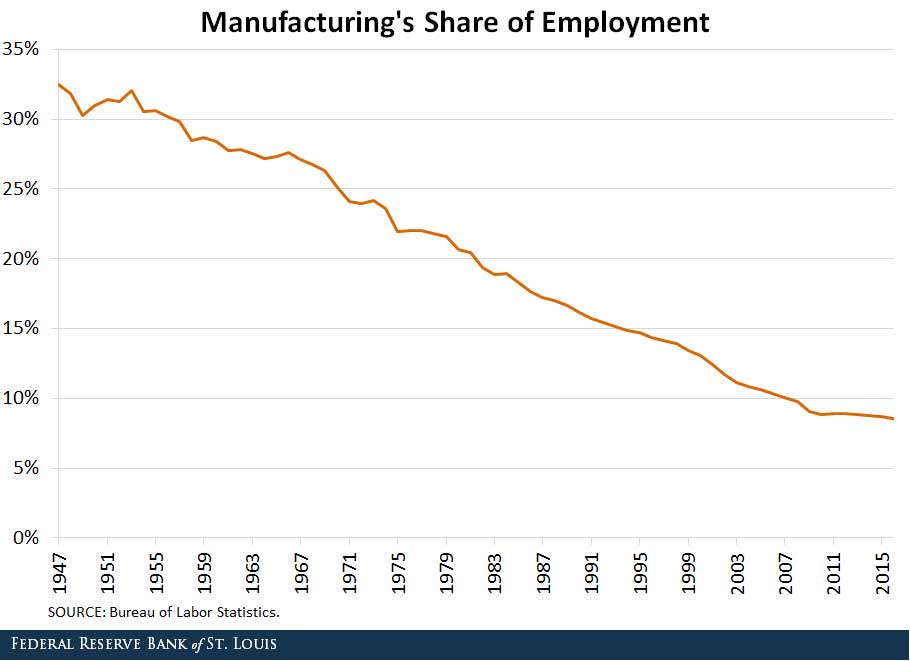
Drafters might need to have more than a degree in drafting. They may be asked to complete an internship with a firm in order to gain practical experience. This experience can help drafters land a job. A portfolio may be requested to show their drafting skills.
Also, drafters can earn certifications. American Design Drafting Association (ADDA), offers certification exams that assess drafting knowledge. These exams are intended to assess your ability to create and accept geometric designs. Many certifications can be renewed every three years. The ADDA is able to offer certification in many different drafting areas.
Drafters often work in the construction, engineering and manufacturing industries. They might also be employed in factories or with electricity. They might also have a set work schedule. However, some drafters work 40+ hours per week. They need to know how to use computer aided drafting (CAD), and manage their time.
Drafters can profit from the growing use of technology in order to increase their efficiency. To be competitive, drafters need to be proficient in CAD and other programs. They also need to keep current with building codes. If you are interested in becoming an architect, a master's is a good option. When it comes to being hired, those with a master's will be more successful than other candidates. They will also be better qualified to present technical information for clients.
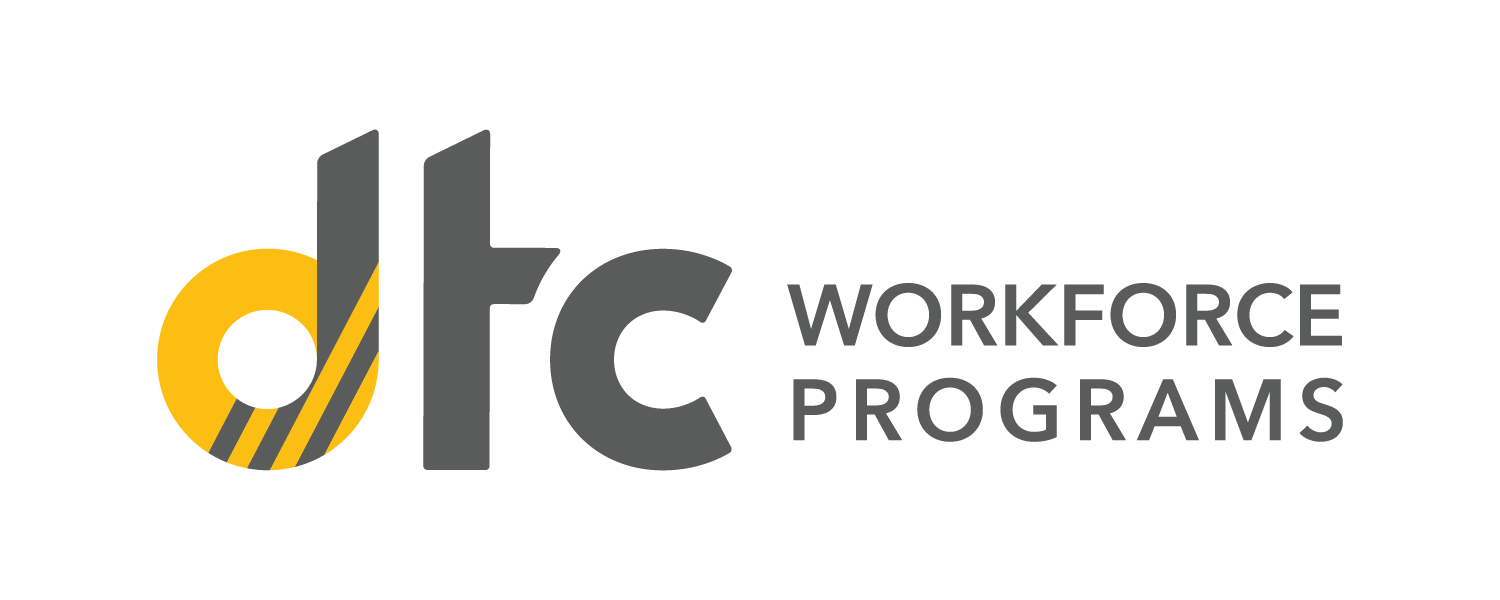
Assisting professional drafters is another option for drafters. Volunteers may be available to help out with community projects. Before you sign up for courses, make sure you know what kind of projects you are interested. Some clients prefer pencil sketches while others prefer computer-generated designs.
Draft technicians can gain professional experience once they have graduated from high school. They should pay particular attention to math and computer classes.
FAQ
Why is logistics important in manufacturing?
Logistics is an integral part of every business. Logistics can help you achieve amazing results by helping to manage product flow from raw materials to finished products.
Logistics plays a significant role in reducing cost and increasing efficiency.
Can we automate some parts of manufacturing?
Yes! Yes. The Egyptians created the wheel thousands years ago. Today, robots assist in the assembly of lines.
In fact, there are several applications of robotics in manufacturing today. They include:
-
Robots for assembly line
-
Robot welding
-
Robot painting
-
Robotics inspection
-
Robots create products
Manufacturing could also benefit from automation in other ways. For example, 3D printing allows us to make custom products without having to wait for weeks or months to get them manufactured.
What is the role of a logistics manager
Logistics managers are responsible for ensuring that all goods arrive in perfect condition and on time. This is accomplished by using the experience and knowledge gained from working with company products. He/she should ensure that sufficient stock is available in order to meet customer demand.
How can I find out more about manufacturing?
The best way to learn about manufacturing is through hands-on experience. If that is not possible, you could always read books or view educational videos.
Statistics
- Many factories witnessed a 30% increase in output due to the shift to electric motors. (en.wikipedia.org)
- It's estimated that 10.8% of the U.S. GDP in 2020 was contributed to manufacturing. (investopedia.com)
- According to the United Nations Industrial Development Organization (UNIDO), China is the top manufacturer worldwide by 2019 output, producing 28.7% of the total global manufacturing output, followed by the United States, Japan, Germany, and India.[52][53] (en.wikipedia.org)
- In 2021, an estimated 12.1 million Americans work in the manufacturing sector.6 (investopedia.com)
- According to a Statista study, U.S. businesses spent $1.63 trillion on logistics in 2019, moving goods from origin to end user through various supply chain network segments. (netsuite.com)
External Links
How To
How to Use the Just In Time Method in Production
Just-in-time (JIT) is a method that is used to reduce costs and maximize efficiency in business processes. This is where you have the right resources at the right time. This means that you only pay for what you actually use. Frederick Taylor, a 1900s foreman, first coined the term. He noticed that workers were often paid overtime when they had to work late. He then concluded that if he could ensure that workers had enough time to do their job before starting to work, this would improve productivity.
JIT is a way to plan ahead and make sure you don't waste any money. Also, you should look at the whole project from start-to-finish and make sure you have the resources necessary to address any issues. You'll be prepared to handle any potential problems if you know in advance. This way, you won't end up paying extra money for things that weren't really necessary.
There are many types of JIT methods.
-
Demand-driven JIT: You order the parts and materials you need for your project every other day. This will allow to track how much material has been used up. This will allow you to calculate how long it will take to make more.
-
Inventory-based: This is a type where you stock the materials required for your projects in advance. This allows you predict the amount you can expect to sell.
-
Project-driven: This method allows you to set aside enough funds for your project. Once you have an idea of how much material you will need, you can purchase the necessary materials.
-
Resource-based JIT: This type of JIT is most commonly used. You allocate resources based on the demand. You might assign more people to help with orders if there are many. If you don't have many orders, you'll assign fewer people to handle the workload.
-
Cost-based: This is a similar approach to resource-based but you are not only concerned with how many people you have, but also how much each one costs.
-
Price-based: This is very similar to cost-based, except that instead of looking at how much each individual worker costs, you look at the overall price of the company.
-
Material-based - This is a variant of cost-based. But instead of looking at the total company cost, you focus on how much raw material you spend per year.
-
Time-based JIT: This is another variant of resource-based JIT. Instead of focusing solely on the amount each employee costs, focus on how long it takes for the project to be completed.
-
Quality-based JIT: Another variation on resource-based JIT. Instead of thinking about how much each employee costs or how long it takes to manufacture something, you think about how good the quality of your product is.
-
Value-based JIT : This is the newest type of JIT. In this instance, you are not concerned about the product's performance or meeting customer expectations. Instead, your goal is to add value to the market.
-
Stock-based is an inventory-based system that measures the number of items produced at any given moment. This is used to increase production and minimize inventory.
-
Just-in-time planning (JIT): This is a combination JIT and supply-chain management. This refers to the scheduling of the delivery of components as soon after they are ordered. It's important because it reduces lead times and increases throughput.