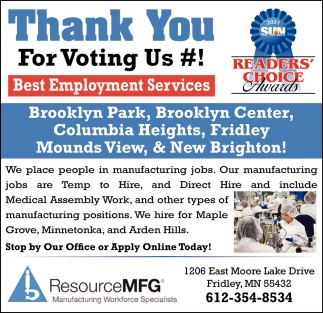
CEVA Logistics is an organization that offers logistics services. These companies offer various benefits to employees. Here's how you can apply to a logistics job at one of these companies. First, you can search by location for job opportunities.
Job description
CEVA Logistics provides a wide range of job opportunities for individuals with various educations and work experience. The company's core values revolve around customer service and prompt delivery. The company seeks people who are passionate about logistics, and who are willing work hard. If you have no prior experience in logistics, and if you have a positive attitude, then you will be preferred for the job.
CEVA Logistics needs a Process/Industrial Manager to develop new processes and improve efficiency. The ideal candidate is energetic, self-driven and able to work with other plant employees. This includes managing projects, designing and implementing process layouts, and applying analytical and modeling skills. They should also be skilled in robotics and other manufacturing processes, which will increase quality and efficiency.
Education is required
CEVA Logistics offers a variety of job opportunities for applicants interested in working as a warehouse manager or sales rep. You may also have the opportunity to become an operations supervisor, which oversees the day to day operations of the company. These positions often have a team of employees under them. Candidates for these positions usually have a bachelor’s degree in logistics, supervisory and strong leadership and management skills.
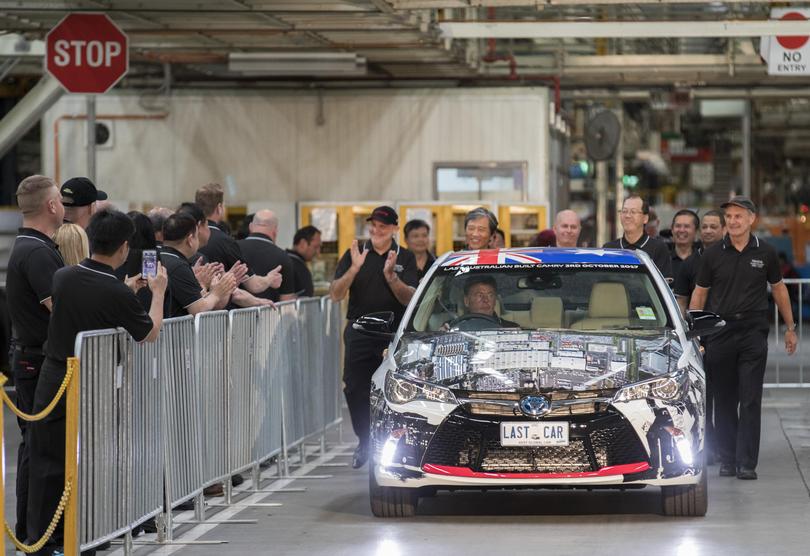
You can apply online, or through recruiters, if you are interested. To apply online, candidates first need to create a profile with the company's career portal. You can connect to your LinkedIn account to access your profile, upload your resumes, and fill in relevant information. After creating their profile, they can choose the desired country or region and get in touch to a recruiter.
Salary range
First, create a profile on the company’s online career portal to apply for a CEVA Logistics role. This will allow you to connect with LinkedIn and upload your resume. You can also add information about your qualifications, experience, and other relevant information. The next step is to select a region or country where you're interested in working. Once you've completed this, you'll be provided contact information from a recruiter.
Salaries at CEVA Logistics vary based on job title, experience, and location. An Air Break Bulk Specialist earns 24,000, while the Vice President at CEVA Logistics earns $166,000 each year. However, the economic situation in each location can impact the salary.
Locations
CEVA Logistics has a fantastic career opportunity for those looking to work in logistics. The company offers various positions at different locations, with different responsibilities and experience requirements. You can apply for a job by entering the job title and location in the search box. You can search for Edison job listings. You will need experience driving and be able and able to communicate with both internal and external customers.
CEVA Logistics offers many opportunities for career advancement, including supervisory roles. Supervisors are responsible for the company's day to day operations. They manage inventory, coordinate schedules, and oversee the activities of employees. Operations supervisors usually have a team reporting to them and require a bachelor’s degree or related experience. Strong leadership and management skills are also necessary.
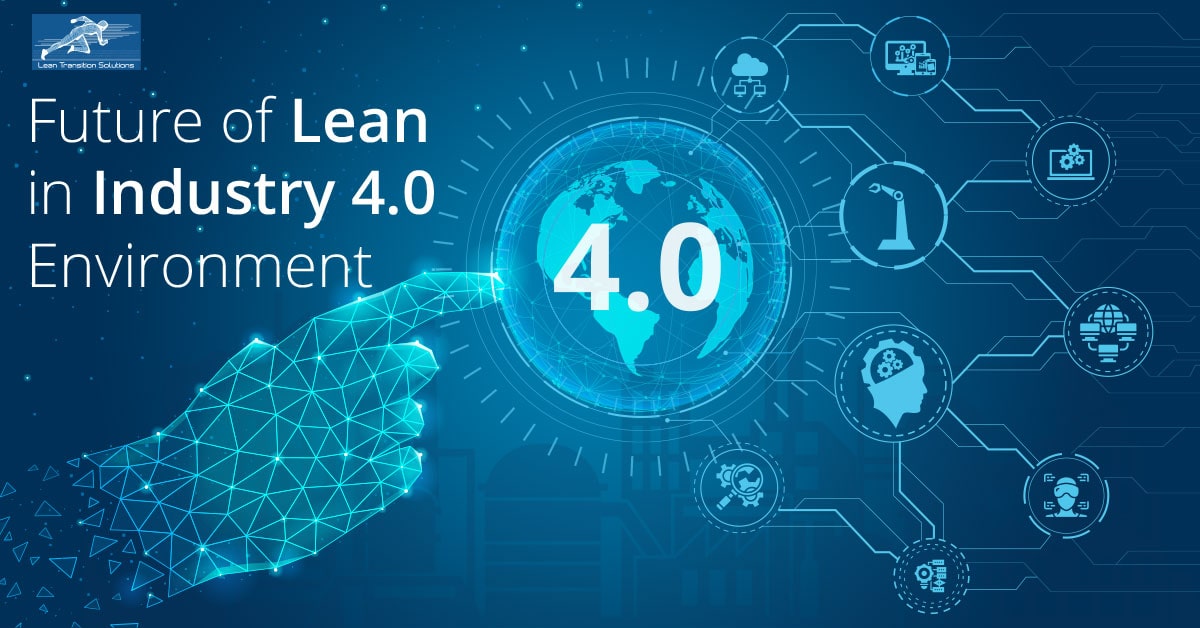
Apply online
If you're in the market for a job in the logistics industry, you can apply online for a position with CEVA Logistics. Ceva Logistics, an international logistics company, was established in 2006 as a result the merger of two Australian and Texan contracts logistics companies. It has more than 9500 employees and operates in over 170 countries. Job seekers can apply for full-time or part-time positions.
While most jobs at CEVA require some prior experience, many positions can be filled as entry-level. Other positions may require little to no experience. Customer service representative, dispatcher, and admin clerk are some of the entry-level jobs.
FAQ
What is the difference between Production Planning, Scheduling and Production Planning?
Production Planning (PP), also known as forecasting and identifying production capacities, is the process that determines what product needs to be produced at any particular time. This is accomplished by forecasting the demand and identifying production resources.
Scheduling refers the process by which tasks are assigned dates so that they can all be completed within the given timeframe.
What does manufacturing industry mean?
Manufacturing Industries are those businesses that make products for sale. The people who buy these products are called consumers. These companies use various processes such as production, distribution, retailing, management, etc., to fulfill this purpose. These companies produce goods using raw materials and other equipment. This includes all types manufactured goods such as clothing, building materials, furniture, electronics, tools and machinery.
What makes a production planner different from a project manger?
The primary difference between a producer planner and a manager of a project is that the manager usually plans and organizes the whole project, while a production planner is only involved in the planning stage.
Statistics
- Many factories witnessed a 30% increase in output due to the shift to electric motors. (en.wikipedia.org)
- According to the United Nations Industrial Development Organization (UNIDO), China is the top manufacturer worldwide by 2019 output, producing 28.7% of the total global manufacturing output, followed by the United States, Japan, Germany, and India.[52][53] (en.wikipedia.org)
- According to a Statista study, U.S. businesses spent $1.63 trillion on logistics in 2019, moving goods from origin to end user through various supply chain network segments. (netsuite.com)
- It's estimated that 10.8% of the U.S. GDP in 2020 was contributed to manufacturing. (investopedia.com)
- [54][55] These are the top 50 countries by the total value of manufacturing output in US dollars for its noted year according to World Bank.[56] (en.wikipedia.org)
External Links
How To
How to Use the Just In Time Method in Production
Just-intime (JIT), which is a method to minimize costs and maximize efficiency in business process, is one way. This is where you have the right resources at the right time. This means that you only pay for what you actually use. Frederick Taylor first coined this term while working in the early 1900s as a foreman. He observed how workers were paid overtime if there were delays in their work. He then concluded that if he could ensure that workers had enough time to do their job before starting to work, this would improve productivity.
JIT is an acronym that means you need to plan ahead so you don’t waste your money. Look at your entire project, from start to end. Make sure you have enough resources in place to deal with any unexpected problems. You can anticipate problems and have enough equipment and people available to fix them. This will prevent you from spending extra money on unnecessary things.
There are many types of JIT methods.
-
Demand-driven JIT: This is a JIT that allows you to regularly order the parts/materials necessary for your project. This will allow to track how much material has been used up. This will let you know how long it will be to produce more.
-
Inventory-based : You can stock the materials you need in advance. This allows one to predict how much they will sell.
-
Project-driven: This approach involves setting aside sufficient funds to cover your project's costs. When you know how much you need, you'll purchase the appropriate amount of materials.
-
Resource-based: This is the most common form of JIT. You allocate resources based on the demand. For example, if there is a lot of work coming in, you will have more people assigned to them. You'll have fewer orders if you have fewer.
-
Cost-based : This is similar in concept to resource-based. But here, you aren't concerned about how many people your company has but how much each individual costs.
-
Price-based: This is a variant of cost-based. However, instead of focusing on the individual workers' costs, this looks at the total price of the company.
-
Material-based - This is a variant of cost-based. But instead of looking at the total company cost, you focus on how much raw material you spend per year.
-
Time-based: Another variation of resource-based JIT. Instead of focusing only on how much each employee is costing, you should focus on how long it takes to complete your project.
-
Quality-based: This is yet another variation of resource-based JIT. Instead of thinking about the cost of each employee or the time it takes to produce something, you focus on how good your product quality.
-
Value-based JIT is the newest form of JIT. In this case, you're not concerned with how well the products perform or whether they meet customer expectations. Instead, you're focused on how much value you add to the market.
-
Stock-based is an inventory-based system that measures the number of items produced at any given moment. It's used when you want to maximize production while minimizing inventory.
-
Just-in time (JIT), planning: This is a combination JIT/supply chain management. It is the process that schedules the delivery of components within a short time of their order. It reduces lead times and improves throughput.