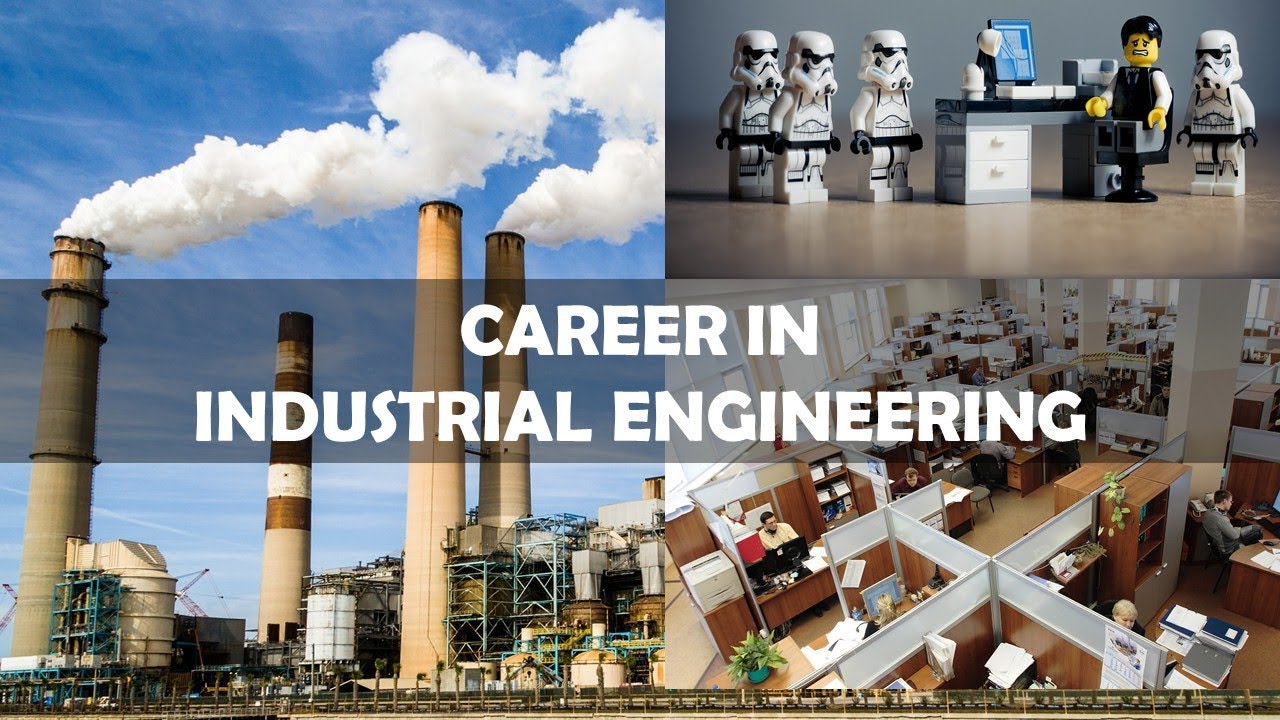
Manufacturing in the US is a big part of the American economy. This sector accounts for approximately eleven percent of the country's total economic output. It is also a large contributor to the global economy, accounting for 18.2 percent of world goods. However, manufacturing has seen a slowdown in growth in recent years.
Since 2000, the US has lost a third its factory jobs. According to BLS, manufacturing productivity increased by 4.5% annually between 1995-2000. While once manufacturing was seen as a declining job generator but automation and other technological advances have led to a reexamination regarding how technology is impacting the employment market.
Walmart made an announcement in January 2013 that it would support American jobs. Over the next ten year, Walmart will purchase $250 billion of American products. As a result of this commitment, Walmart is able to support additional U.S. manufacturing and encourage diverse companies to explore opportunities with the giant retailer.
However, while the United States has become a leading player in the global market, it has faced challenges. Some of these challenges are caused by the rising cost of labor overseas, a soaring corporate tax rate, and a lack of skills in trade negotiations. These issues could have a negative impact on the sector's long-term future.
A skills crisis is also facing the US, with an estimated 1.4million factory workers in need of additional training. Trump's policies are aimed at expanding apprenticeship programs and training, but there have been concerns about the quality.
Despite all the problems, however the US manufacturing sector has recovered from the Great Recession. The first quarter 2018 saw record manufacturing output of $2.00 trillion. This was higher than the $1.95 Trillion that was achieved in the year preceding the recession.
The US manufacturing industry has been growing at a slower rate that the overall economy. However, growth is expected in the coming years. The sector's growth is expected to be 2.4 percent in 2020, and 1.9% by 2021.
Manufacturing sector is expected to benefit from an increase in exports. Additionally, the industry has seen its energy costs drop due to shale. The United States also has a competitive corporate rate that is higher than many other countries around the globe.
Meanwhile, China, Japan, and South Korea are experiencing manufacturing contraction. This is the first time the S&P Global purchasing management index has been below 50 in these countries for almost two years.
Trump is said to be working on a less bureaucratic federal program for supporting the manufacturing sector. Manufacturing Extension Partnership (MEP), one of the most critical federal programs, is one of its most important. A MEP generates $21 in new client investment for every $21 that the federal government invests. MEPs have centers in all fifty states and Canada, Mexico, Canada, Europe.
The US is in a weaker position than other industrial countries when it comes to trade negotiations. It is therefore difficult for the government to negotiate bilateral agreements with other nations. Consequently, the US is facing challenges in luring more manufacturers and retaining existing firms.
FAQ
What are manufacturing and logistics?
Manufacturing refers to the process of making goods using raw materials and machines. Logistics manages all aspects of the supply chain, including procurement, production planning and distribution, inventory control, transportation, customer service, and transport. As a broad term, manufacturing and logistics often refer to both the creation and delivery of products.
How can manufacturing efficiency be improved?
The first step is to identify the most important factors affecting production time. We must then find ways that we can improve these factors. If you don’t know where to begin, consider which factors have the largest impact on production times. Once you've identified them, try to find solutions for each of those factors.
What are the products and services of logistics?
Logistics is the process of moving goods from one point to another.
They include all aspects of transport, including packaging, loading, transporting, unloading, storing, warehousing, inventory management, customer service, distribution, returns, and recycling.
Logisticians ensure that the right product reaches the right place at the right time and under safe conditions. Logisticians assist companies in managing their supply chains by providing information such as demand forecasts, stock levels and production schedules.
They coordinate with vendors and suppliers, keep track of shipments, monitor quality standards and perform inventory and order replenishment.
Is it possible to automate certain parts of manufacturing
Yes! Since ancient times, automation has been in existence. The wheel was invented by the Egyptians thousands of years ago. Nowadays, we use robots for assembly lines.
There are many applications for robotics in manufacturing today. These include:
-
Assembly line robots
-
Robot welding
-
Robot painting
-
Robotics inspection
-
Robots that make products
There are many other examples of how manufacturing could benefit from automation. 3D printing is a way to make custom products quickly and without waiting weeks or months for them to be manufactured.
What is the role and responsibility of a Production Planner?
Production planners ensure all aspects of the project are delivered within time and budget. They also ensure that the product/service meets the client’s needs.
Statistics
- Many factories witnessed a 30% increase in output due to the shift to electric motors. (en.wikipedia.org)
- According to the United Nations Industrial Development Organization (UNIDO), China is the top manufacturer worldwide by 2019 output, producing 28.7% of the total global manufacturing output, followed by the United States, Japan, Germany, and India.[52][53] (en.wikipedia.org)
- In the United States, for example, manufacturing makes up 15% of the economic output. (twi-global.com)
- In 2021, an estimated 12.1 million Americans work in the manufacturing sector.6 (investopedia.com)
- [54][55] These are the top 50 countries by the total value of manufacturing output in US dollars for its noted year according to World Bank.[56] (en.wikipedia.org)
External Links
How To
How to Use Lean Manufacturing for the Production of Goods
Lean manufacturing (or lean manufacturing) is a style of management that aims to increase efficiency, reduce waste and improve performance through continuous improvement. It was created in Japan by Taiichi Ohno during the 1970s and 80s. He received the Toyota Production System award (TPS), from Kanji Toyoda, founder of TPS. Michael L. Watkins published the first book on lean manufacturing in 1990.
Lean manufacturing is often described as a set if principles that help improve the quality and speed of products and services. It emphasizes the elimination and minimization of waste in the value stream. The five-steps of Lean Manufacturing are just-in time (JIT), zero defect and total productive maintenance (TPM), as well as 5S. Lean manufacturing eliminates non-value-added tasks like inspection, rework, waiting.
In addition to improving product quality and reducing costs, lean manufacturing helps companies achieve their goals faster and reduces employee turnover. Lean manufacturing can be used to manage all aspects of the value chain. Customers, suppliers, distributors, retailers and employees are all included. Lean manufacturing can be found in many industries. Toyota's philosophy is the foundation of its success in automotives, electronics and appliances, healthcare, chemical engineers, aerospace, paper and food, among other industries.
Five fundamental principles underlie lean manufacturing.
-
Define Value - Identify the value your business adds to society and what makes you different from competitors.
-
Reduce waste - Get rid of any activity that does not add value to the supply chain.
-
Create Flow – Ensure that work flows smoothly throughout the process.
-
Standardize and Simplify – Make processes as consistent, repeatable, and as simple as possible.
-
Develop Relationships: Establish personal relationships both with internal and external stakeholders.
Lean manufacturing isn’t new, but it has seen a renewed interest since 2008 due to the global financial crisis. Many businesses are now using lean manufacturing to improve their competitiveness. In fact, some economists believe that lean manufacturing will be an important factor in economic recovery.
Lean manufacturing is becoming a popular practice in automotive. It has many advantages. These include better customer satisfaction and lower inventory levels. They also result in lower operating costs.
It can be applied to any aspect of an organisation. It is especially useful for the production aspect of an organization, as it ensures that every step in the value chain is efficient and effective.
There are three main types in lean manufacturing
-
Just-in Time Manufacturing, (JIT): This kind of lean manufacturing is also commonly known as "pull-systems." JIT means that components are assembled at the time of use and not manufactured in advance. This strategy aims to decrease lead times, increase availability of parts and reduce inventory.
-
Zero Defects Manufacturing (ZDM),: ZDM is a system that ensures no defective units are left the manufacturing facility. If a part is required to be repaired on the assembly line, it should not be scrapped. This also applies to finished products that need minor repairs before being shipped.
-
Continuous Improvement (CI), also known as Continuous Improvement, aims at improving the efficiency of operations through continuous identification and improvement to minimize or eliminate waste. Continuous improvement refers to continuous improvement of processes as well people and tools.