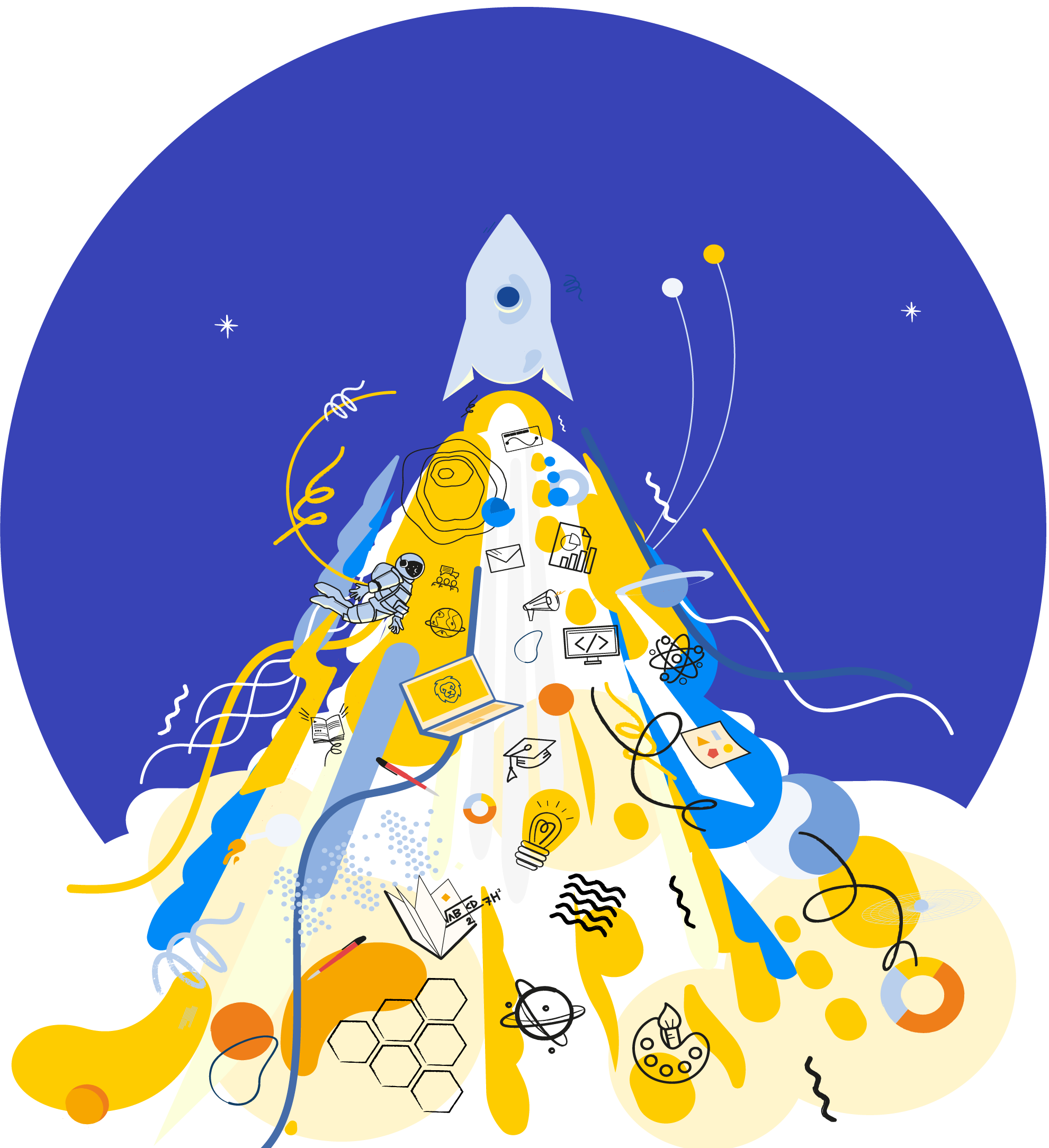
The Production Development Engineer is responsible to optimize production processes within the manufacturing environment. This includes creating a team environment that ensures quality and timely delivery of products. It is important that you are adaptable, innovative, and a good communicator. You must also have strong analytical skills and a development-oriented mentality.
As part of the Advanced Manufacturing Engineering Team the Production Development Engineer works with cross-functional teams. He or she will be responsible for identifying problems in product and development processes. Then, they will use process technology as a tool to increase productivity, improve quality and lower costs. To solve technical problems, the Production Development Engineer may also collaborate with external vendors.
This position requires a bachelor of engineering degree. Candidates must have at minimum three years of manufacturing experience. An understanding of Lean manufacturing is essential. It is necessary to have a good knowledge of technical communication and report writing programs. You can make a valuable contribution to the Production Development Team if you are passionate about innovative solutions and cost-effectiveness.
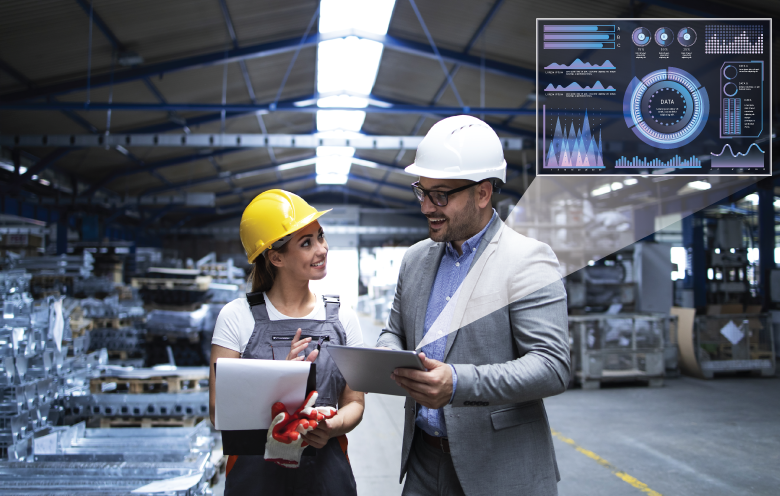
Product engineers are the ones responsible for creating new product concepts. Their duties include identifying and analyzing consumer preferences and needs, designing prototypes, and implementing those designs. They provide production specifications as well as quality control procedures. At the same time, they analyze and test the proposed product to determine any problems or design tolerances. These tasks require good mathematical and analytical abilities.
A Production Development Engineer with a high level of success will be creative, efficient, and resourceful. He or she must not only be creative in designing new products but also be able meet the budgetary expectations and satisfy stakeholder needs. You will need to have extensive product knowledge and be familiar with manufacturing processes.
Product engineers usually work in specific areas like electrical, software, and materials. Other areas of specialization include optics and mechanics as well as testing. The production development engineer is involved in all stages of a project. When it comes to the production of a new product, he or she will have to ensure that the production methods and equipment used are based on the target's cost, time, and quality goals.
During product design, the Product Development Engineer will examine and test the product in order to find any problems or design tolerances. Then, he or she will create a new prototype with built-in control features that saves money during the manufacturing process.
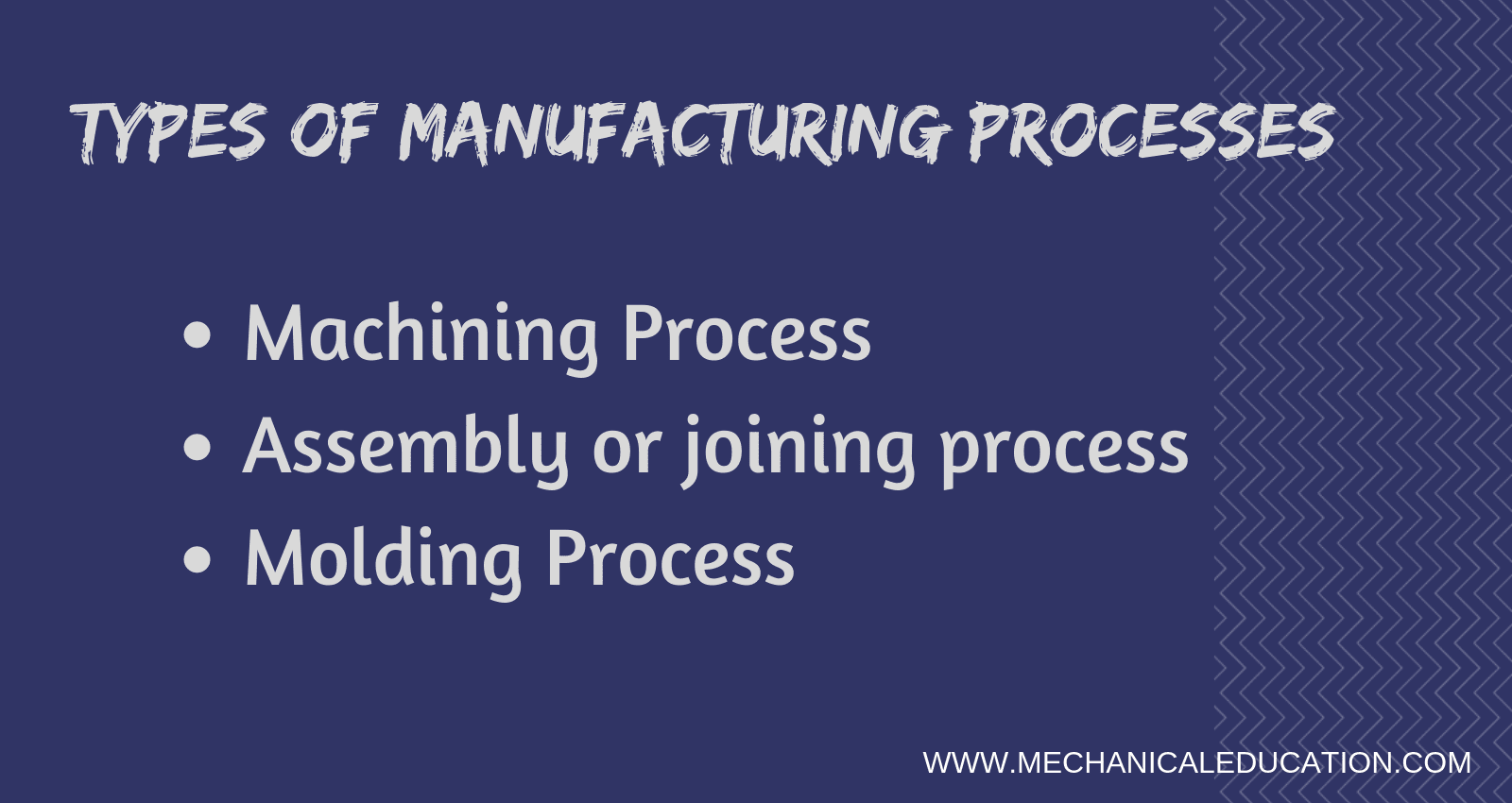
Once the design has been finalized, the Product Development Engineer will coordinate production activities and other departments. Finally, he/she will create a quality assurance program to ensure the product meets specifications. This includes all safety and environmental issues. The engineer will then deliver the approved product plans to production.
A Production Development Engineer should have an excellent working knowledge of surface modeling software and 3D modeling. It is a plus if a candidate has experience working in the Assembly Industry.
FAQ
Are there ways to automate parts of manufacturing?
Yes! Yes! Automation has existed since ancient times. The Egyptians invent the wheel thousands of year ago. We now use robots to help us with assembly lines.
In fact, there are several applications of robotics in manufacturing today. These include:
-
Robots for assembly line
-
Robot welding
-
Robot painting
-
Robotics inspection
-
Robots that produce products
Manufacturing can also be automated in many other ways. For example, 3D printing allows us to make custom products without having to wait for weeks or months to get them manufactured.
What are the 7 R's of logistics?
The 7R's of Logistics is an acronym for the seven basic principles of logistics management. It was developed by the International Association of Business Logisticians (IABL) and published in 2004 as part of its "Seven Principles of Logistics Management" series.
The acronym consists of the following letters:
-
Responsible - ensure that all actions taken are within legal requirements and are not harmful to others.
-
Reliable - You can have confidence that you will fulfill your promises.
-
Reasonable - make sure you use your resources well and don't waste them.
-
Realistic – consider all aspects of operations, from cost-effectiveness to environmental impact.
-
Respectful – Treat others fairly and equitably.
-
Resourceful - look for opportunities to save money and increase productivity.
-
Recognizable is a company that provides customers with value-added solutions.
Why is logistics important in manufacturing
Logistics is an integral part of every business. Logistics can help you achieve amazing results by helping to manage product flow from raw materials to finished products.
Logistics also play a major role in reducing costs and increasing efficiency.
Is there anything we should know about Manufacturing Processes prior to learning about Logistics.
No. No. But, being familiar with manufacturing processes will give you a better understanding about how logistics works.
What is the responsibility for a logistics manager
Logistics managers ensure that goods arrive on time and are unharmed. This is accomplished by using the experience and knowledge gained from working with company products. He/she also needs to ensure adequate stock to meet demand.
How can manufacturing overproduction be reduced?
Better inventory management is key to reducing excess production. This would reduce the time spent on unproductive activities like purchasing, storing and maintaining excess stock. This would allow us to use our resources for more productive tasks.
This can be done by using a Kanban system. A Kanban board, a visual display to show the progress of work, is called a Kanban board. Kanban systems allow work items to move through different states until they reach their final destination. Each state represents an individual priority level.
For instance, when work moves from one stage to another, the current task is complete enough to be moved to the next stage. A task that is still in the initial stages of a process will be considered complete until it moves on to the next stage.
This allows for work to continue moving forward, while also ensuring that there is no work left behind. With a Kanban board, managers can see exactly how much work is being done at any given moment. This allows them to adjust their workflows based on real-time information.
Lean manufacturing, another method to control inventory levels, is also an option. Lean manufacturing is about eliminating waste from all stages of the production process. Any product that isn't adding value can be considered waste. Some common types of waste include:
-
Overproduction
-
Inventory
-
Packaging that is not necessary
-
Excess materials
Manufacturers can reduce their costs and improve their efficiency by using these ideas.
How can we improve manufacturing efficiency?
First, identify the factors that affect production time. We then need to figure out how to improve these variables. You can start by identifying the most important factors that impact production time. Once you have identified them, it is time to identify solutions.
Statistics
- In the United States, for example, manufacturing makes up 15% of the economic output. (twi-global.com)
- According to a Statista study, U.S. businesses spent $1.63 trillion on logistics in 2019, moving goods from origin to end user through various supply chain network segments. (netsuite.com)
- Job #1 is delivering the ordered product according to specifications: color, size, brand, and quantity. (netsuite.com)
- In 2021, an estimated 12.1 million Americans work in the manufacturing sector.6 (investopedia.com)
- Many factories witnessed a 30% increase in output due to the shift to electric motors. (en.wikipedia.org)
External Links
How To
Six Sigma in Manufacturing:
Six Sigma refers to "the application and control of statistical processes (SPC) techniques in order to achieve continuous improvement." Motorola's Quality Improvement Department in Tokyo, Japan developed Six Sigma in 1986. Six Sigma's basic concept is to improve quality and eliminate defects through standardization. This method has been adopted by many companies in recent years as they believe there are no perfect products or services. The main goal of Six Sigma is to reduce variation from the mean value of production. This means that you can take a sample from your product and then compare its performance to the average to find out how often the process differs from the norm. If this deviation is too big, you know something needs fixing.
Understanding how your business' variability is a key step towards Six Sigma implementation is the first. Once you've understood that, you'll want to identify sources of variation. You'll also want to determine whether these variations are random or systematic. Random variations occur when people make mistakes; systematic ones are caused by factors outside the process itself. You could consider random variations if some widgets fall off the assembly lines. You might notice that your widgets always fall apart at the same place every time you put them together.
Once you've identified where the problems lie, you'll want to design solutions to eliminate those problems. That solution might involve changing the way you do things or redesigning the process altogether. You should then test the changes again after they have been implemented. If they don't work you need to rework them and come up a better plan.