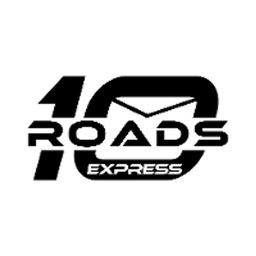
American Factory
In post-industrial Ohio, a Chinese billionaire reopens a factory, hiring two thousand Americans, creating a new sense of hope and promise. But a culture clash ensues as high-tech China and the blue-collar American workers struggle to get along.
The Obamas are launching a Netflix production company. This week, they released the trailer for American Factory, a documentary that tells about a Chinese plant opening in an old General Motors factory in Ohio. The film is produced by Barack Obama's and Michelle Obama's Higher Ground production company and is scheduled to be released on Netflix August 21.
American Factory comes along at exactly the right time. The Last Truck: Closing a GM Plant, directed by Steven Bognar (and Julia Reichert), and winner of Best Documentary at the Sundance Film Festival is American Factory. It is a compelling and timely look at what happens to a factory that has been closed for many years when it is revived by a Chinese auto glass manufacturer.
When a shuttered General Motors plant outside Dayton, Ohio, was bought by a Chinese manufacturer in 2014, it created a sense of hope and promise for the local community. But the factory's arrival also brought with it a clash of cultures and a serious consideration of the prospects for unionization.
As they get used to the Chinese style of management and the expectations that their new colleagues have, the American workers wonder if their work goals will still be met. Also, they're afraid of being labeled 'uncommitted, sloppy and inefficient.
Wong He, an Chinese furnace technician, discusses his work ethic, how much he enjoys it, and how it's difficult to make a decent living in this kind of environment. He says he is required to work long hours and does not have time to see his loved ones.
He is a supporter of unionization and a member in the China Labor Alliance. But his boss does not support unions. He believes that they will make the company inefficient.
This is different from the American management style, which is more concerned about protecting their bottom line. It's not a stance that most American workers agree with, but it's the way things are going for a lot of companies today.
It's important that you understand what this means for your workplace. As a result, it's not a good idea to be too defensive about your rights as an employee.
There are many people in the United States who believe that their power is becoming more centralized. They're more likely to accept the notion that their job doesn't require them to do all the time, and they may even be willing to do it without pay.
Millennials born between 1990 and now will be the most affected by the shift in the workplace. It's a generation raised with a single-child policy. They have strong desires for a lifestyle outside of work. They don't like to be asked to work overtime, and they don't like it when their boss makes them do so.
FAQ
What is production planning?
Production Planning includes planning for all aspects related to production. This document ensures that everything is prepared and available when you are ready for shooting. You should also have information to ensure the best possible results on set. This includes shooting schedules, locations, cast lists, crew details, and equipment requirements.
The first step is to outline what you want to film. You may already know where you want the film to be shot, or perhaps you have specific locations and sets you wish to use. Once you've identified the locations and scenes you want to use, you can begin to plan what elements you need for each scene. You might decide you need a car, but not sure what make or model. This is where you can look up car models online and narrow down your options by choosing from different makes and models.
After you have chosen the right car, you will be able to begin thinking about accessories. You might need to have people in the front seats. Perhaps you have someone who needs to be able to walk around the back of your car. You may want to change the interior's color from black or white. These questions can help you decide the right look for your car. It is also worth considering the types of shots that you wish to take. Will you be filming close-ups or wide angles? Maybe the engine or steering wheel is what you are looking to film. These factors will help you determine which car style you want to film.
Once you have determined all of the above, you can move on to creating a schedule. You can use a schedule to determine when and where you need it to be shot. The schedule will show you when to get there, what time to leave, and when to return home. Everyone will know what they need and when. Book extra staff ahead of time if you need them. It is not worth hiring someone who won’t show up because you didn’t tell him.
Also, consider how many days you will be filming your schedule. Some projects may only take a couple of days, while others could last for weeks. You should consider whether you will need more than one shot per week when creating your schedule. Multiple takes at the same place will result in higher costs and longer completion times. If you aren't sure whether you need multiple shots, it is best to take fewer photos than you would like.
Another important aspect of production planning is setting budgets. It is important to set a realistic budget so you can work within your budget. Keep in mind that you can always reduce your budget if you face unexpected difficulties. However, you shouldn't overestimate the amount of money you will spend. If you underestimate the cost of something, you will have less money left after paying for other items.
Production planning is a complicated process. But once you understand how everything works together, it becomes much easier to plan future project.
What is manufacturing and logistics?
Manufacturing is the act of producing goods from raw materials using machines and processes. Logistics is the management of all aspects of supply chain activities, including procurement, production planning, distribution, warehousing, inventory control, transportation, and customer service. As a broad term, manufacturing and logistics often refer to both the creation and delivery of products.
What does it take for a logistics enterprise to succeed?
You need to have a lot of knowledge and skills to manage a successful logistic business. For clients and suppliers to be successful, you need to have excellent communication skills. You will need to know how to interpret data and draw conclusions. You must be able to work well under pressure and handle stressful situations. In order to innovate and create new ways to improve efficiency, creativity is essential. You must be a strong leader to motivate others and direct them to achieve organizational goals.
You must be organized to meet tight deadlines.
What are the four types of manufacturing?
Manufacturing is the process by which raw materials are transformed into useful products through machines and processes. It can involve many activities like designing, manufacturing, testing packaging, shipping, selling and servicing.
Statistics
- Job #1 is delivering the ordered product according to specifications: color, size, brand, and quantity. (netsuite.com)
- According to a Statista study, U.S. businesses spent $1.63 trillion on logistics in 2019, moving goods from origin to end user through various supply chain network segments. (netsuite.com)
- [54][55] These are the top 50 countries by the total value of manufacturing output in US dollars for its noted year according to World Bank.[56] (en.wikipedia.org)
- You can multiply the result by 100 to get the total percent of monthly overhead. (investopedia.com)
- In the United States, for example, manufacturing makes up 15% of the economic output. (twi-global.com)
External Links
How To
How to use the Just-In Time Method in Production
Just-in-time (JIT) is a method that is used to reduce costs and maximize efficiency in business processes. It's a way to ensure that you get the right resources at just the right time. This means you only pay what you use. Frederick Taylor, a 1900s foreman, first coined the term. He observed how workers were paid overtime if there were delays in their work. He concluded that if workers were given enough time before they start work, productivity would increase.
The idea behind JIT is that you should plan ahead and have everything ready so you don't waste money. You should also look at the entire project from start to finish and make sure that you have sufficient resources available to deal with any problems that arise during the course of your project. You'll be prepared to handle any potential problems if you know in advance. This will ensure that you don't spend more money on things that aren't necessary.
There are several types of JIT techniques:
-
Demand-driven JIT: This is a JIT that allows you to regularly order the parts/materials necessary for your project. This will enable you to keep track of how much material is left after you use it. It will also allow you to predict how long it takes to produce more.
-
Inventory-based: You stock materials in advance to make your projects easier. This allows you to predict how much you can expect to sell.
-
Project-driven : This is a method where you make sure that enough money is set aside to pay the project's cost. If you know the amount you require, you can buy the materials you need.
-
Resource-based: This is the most common form of JIT. Here, you allocate certain resources based on demand. For instance, if you have a lot of orders coming in, you'll assign more people to handle them. If you don't receive many orders, then you'll assign fewer employees to handle the load.
-
Cost-based: This is the same as resource-based except that you don't care how many people there are but how much each one of them costs.
-
Price-based pricing: This is similar in concept to cost-based but instead you look at how much each worker costs, it looks at the overall company's price.
-
Material-based: This approach is similar to cost-based. However, instead of looking at the total cost for the company, you look at how much you spend on average on raw materials.
-
Time-based: Another variation of resource-based JIT. Instead of focusing on how much each employee costs, you focus on how long it takes to complete the project.
-
Quality-based: This is yet another variation of resource-based JIT. Instead of looking at the labor costs and time it takes to make a product, think about its quality.
-
Value-based JIT : This is the newest type of JIT. In this instance, you are not concerned about the product's performance or meeting customer expectations. Instead, your goal is to add value to the market.
-
Stock-based: This is an inventory-based method that focuses on the actual number of items being produced at any given time. It's useful when you want maximum production and minimal inventory.
-
Just-intime planning (JIT), is a combination JIT/sales chain management. It's the process of scheduling delivery of components immediately after they are ordered. It's important as it reduces leadtimes and increases throughput.