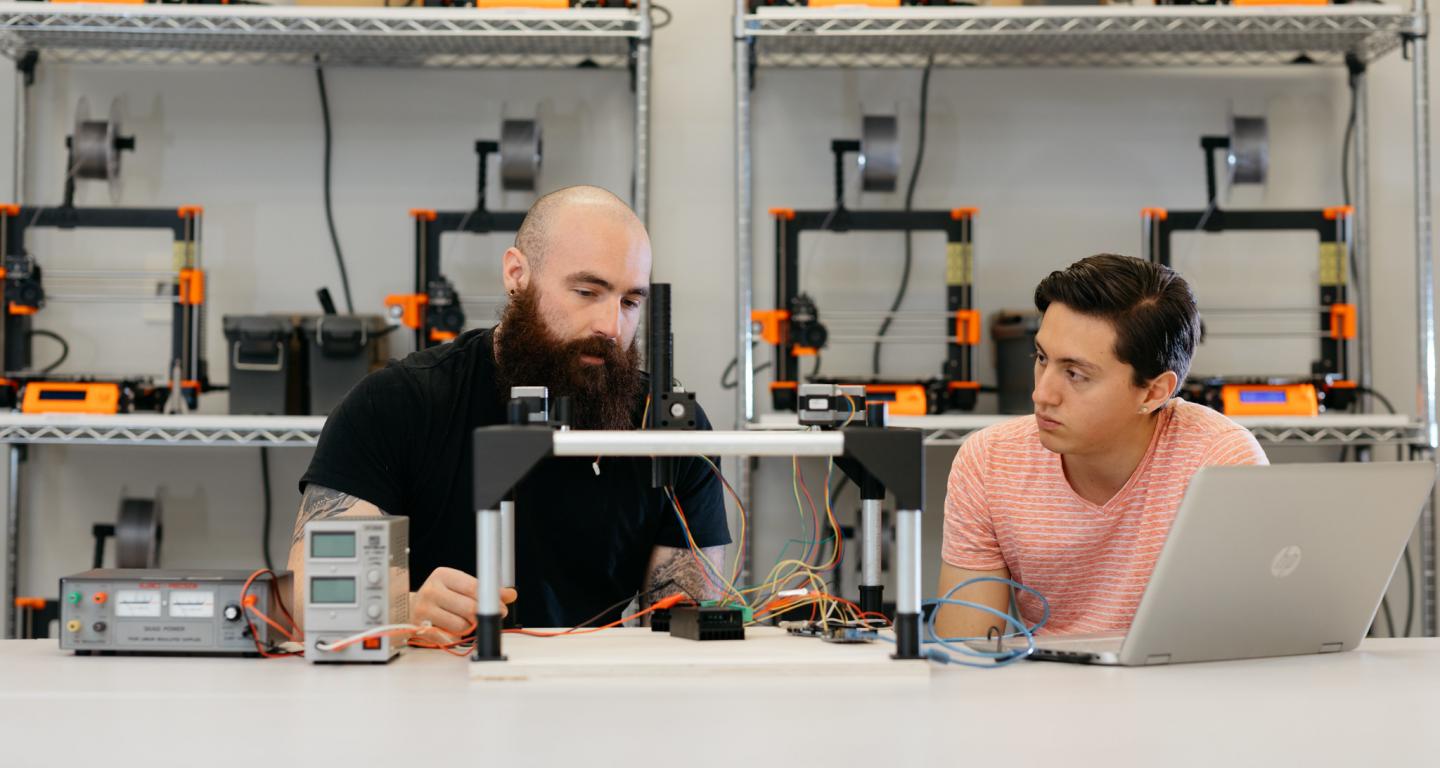
Manufacturing failures can be caused by many things. These include poor design, cost cutting initiatives, lackluster quality control, and more. Fortunately, there are a few ways to avoid these problems and improve quality.
Does lean manufacturing work?
Many companies who implement lean techniques are successful. They are able, amongst other things, to eliminate waste and improve their cycle times. These companies do this through trial-and-error and failure.
Almost all lean experts agree that the main reasons for implementation failures are due to senior management and ownership. Senior management is responsible for all that happens in an organization, but they are often unaware of what it takes to implement lean practices successfully.
It is difficult to convince employees to adopt lean practices and to get the results you expect. For this reason, it is crucial to conduct a skills evaluation well in advance. You will be able to avoid ambiguity when you know who can help achieve your goals and who needs to go.
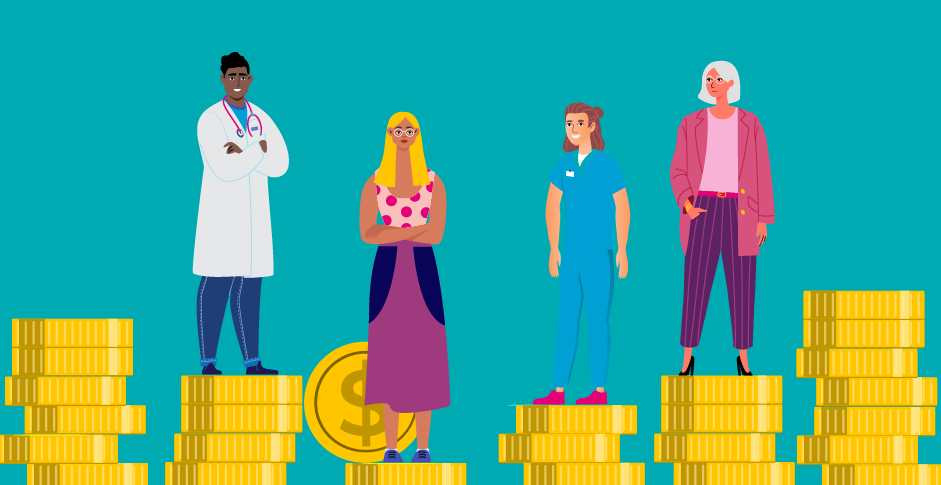
Why do manufacturers fail?
Some manufacturing mistakes are caused because the manufacturer used the wrong material or didn't implement proper quality assurance measures. Other defects occur due to manufacturing errors. A product may be made incorrectly or in a way it wasn't intended. These mistakes can be expensive to fix and can even result in loss of revenue for the company.
These problems can be costly for the manufacturer and for consumers, which is why it's so important to ensure that products are manufactured correctly. To avoid these problems, manufacturers must be able detect failures as early as possible in the manufacturing process.
To achieve this goal, manufacturers must understand the causes of failures. This can help them determine how to improve their business processes and reduce their downtime costs.
A manufacturer's failure is often due to a lack of capital. There are many reasons why this can happen, but the most important thing to remember is that a business needs enough capital to continue to produce and sell in the long run.
If a company lacks sufficient funds to produce a product, this can lead to problems for both the manufacturer and the consumer. This can result in a range of issues such as delays in delivery and lower prices.
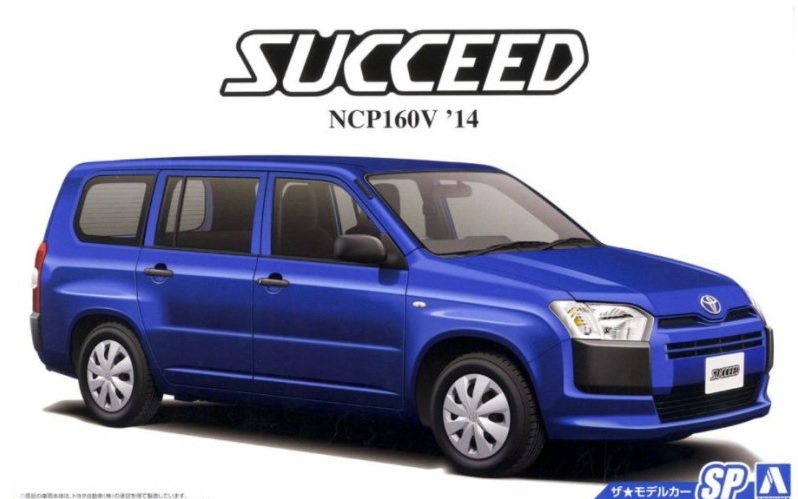
This can cause injury for the consumer if the product is being used in an unsafe manner. If, for instance, a child breaks a tooth from playing around with a lighter that ignites a fire, then the manufacturer is liable because they failed to warn him of the potential danger.
This can be a very dangerous situation, especially for children who are not yet accustomed to handling hazardous materials. It can also be a very expensive issue for the manufacturer to address, but it's vital for any company that wants to stay in business.
FAQ
What do we need to know about Manufacturing Processes in order to learn more about Logistics?
No. It doesn't matter if you don't know anything about manufacturing before you learn about logistics. However, knowing about manufacturing processes will definitely give you a better understanding of how logistics works.
What are manufacturing and logistics?
Manufacturing is the production of goods using raw materials. Logistics manages all aspects of the supply chain, including procurement, production planning and distribution, inventory control, transportation, customer service, and transport. As a broad term, manufacturing and logistics often refer to both the creation and delivery of products.
What is the responsibility for a logistics manager
Logistics managers are responsible for ensuring that all goods arrive in perfect condition and on time. This is done through his/her expertise and knowledge about the company's product range. He/she should ensure that sufficient stock is available in order to meet customer demand.
Are there ways to automate parts of manufacturing?
Yes! Yes. The Egyptians invent the wheel thousands of year ago. To help us build assembly lines, we now have robots.
Robotics is used in many manufacturing processes today. These include:
-
Automation line robots
-
Robot welding
-
Robot painting
-
Robotics inspection
-
Robots that produce products
Automation can be applied to manufacturing in many other ways. For instance, 3D printing allows us make custom products and not have to wait for months or even weeks to get them made.
Statistics
- (2:04) MTO is a production technique wherein products are customized according to customer specifications, and production only starts after an order is received. (oracle.com)
- You can multiply the result by 100 to get the total percent of monthly overhead. (investopedia.com)
- According to the United Nations Industrial Development Organization (UNIDO), China is the top manufacturer worldwide by 2019 output, producing 28.7% of the total global manufacturing output, followed by the United States, Japan, Germany, and India.[52][53] (en.wikipedia.org)
- In the United States, for example, manufacturing makes up 15% of the economic output. (twi-global.com)
- [54][55] These are the top 50 countries by the total value of manufacturing output in US dollars for its noted year according to World Bank.[56] (en.wikipedia.org)
External Links
How To
How to Use Just-In-Time Production
Just-in-time is a way to cut costs and increase efficiency in business processes. It's a way to ensure that you get the right resources at just the right time. This means that you only pay for what you actually use. Frederick Taylor developed the concept while working as foreman in early 1900s. After observing how workers were paid overtime for late work, he realized that overtime was a common practice. He realized that workers should have enough time to complete their jobs before they begin work. This would help increase productivity.
JIT teaches you to plan ahead and prepare everything so you don’t waste time. The entire project should be looked at from start to finish. You need to ensure you have enough resources to tackle any issues that might arise. If you anticipate that there might be problems, you'll have enough people and equipment to fix them. This way you won't be spending more on things that aren’t really needed.
There are many types of JIT methods.
-
Demand-driven: This is a type of JIT where you order the parts/materials needed for your project regularly. This will let you track the amount of material left over after you've used it. You'll also be able to estimate how long it will take to produce more.
-
Inventory-based: You stock materials in advance to make your projects easier. This allows you predict the amount you can expect to sell.
-
Project-driven: This is an approach where you set aside enough funds to cover the cost of your project. Knowing how much money you have available will help you purchase the correct amount of materials.
-
Resource-based JIT is the most widespread form. You assign certain resources based off demand. For example, if there is a lot of work coming in, you will have more people assigned to them. If you don’t have many orders you will assign less people to the work.
-
Cost-based: This is similar to resource-based, except that here you're not just concerned about how many people you have but how much each person costs.
-
Price-based: This is very similar to cost-based, except that instead of looking at how much each individual worker costs, you look at the overall price of the company.
-
Material-based: This approach is similar to cost-based. However, instead of looking at the total cost for the company, you look at how much you spend on average on raw materials.
-
Time-based JIT: A variation on resource-based JIT. Instead of worrying about how much each worker costs, you can focus on how long the project takes.
-
Quality-based JIT - This is another form of resource-based JIT. Instead of looking at the labor costs and time it takes to make a product, think about its quality.
-
Value-based JIT: One of the most recent forms of JIT. In this scenario, you're not concerned about how products perform or whether customers expect them to meet their expectations. Instead, you focus on the added value that you provide to your market.
-
Stock-based: This inventory-based approach focuses on how many items are being produced at any one time. It's useful when you want maximum production and minimal inventory.
-
Just-in time (JIT), planning: This is a combination JIT/supply chain management. It refers to the process of scheduling the delivery of components as soon as they are ordered. It reduces lead times and improves throughput.