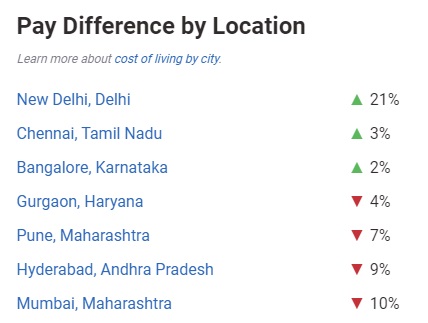
The United States is third in manufacturing in the world and saw its manufacturing output reach a record at $2.00 trillion in Q1 2018. This was nearly twice the amount it had before the Great Recession. However, despite a strong domestic economy, the United States manufacturing industry is taking a shotgun approach to its current challenges. This is either due to a lack in investment or a shortage of skilled labor. We must be more aggressive in confronting the challenges that face our industry.
The number of jobs has declined by 5,000,000 since 2000
Five million US manufacturing jobs were lost between 2000 and now. Some believe the increase in trade with China is to blame, but this explains only about a fourth of the decline in manufacturing jobs. Other than trade with China and the loss of manufacturing jobs in local markets, which aren't able to compete with Chinese imports, However, there are many reasons that manufacturing jobs have been declining. Among the reasons cited are the following:
In the last 20 years, nearly a quarter of the jobs in the US manufacturing industry have been lost. It was at 17 million in 1965 and dropped to a mere 12 million in 2010. While the decline in manufacturing jobs is not the fault of trade, it has been the result of structural problems - a decline in capital investment, output, productivity, and trade deficits - which are not sustainable. While productivity gains were a key factor in the decline, they were not sufficient to offset the loss manufacturing jobs. Automation is the problem, not productivity increases.
Demand for manufactured goods is strong
Despite the decline in consumer spending, the US still has a strong demand to manufacture goods. In 1945, 58% of personal spending on durable goods was made, while it is now only 28%. This is because both the manufacturing cost and the sale price have declined, but the content has increased. This has led to a significant drop in the price of computers, TVs, and audio equipment.
The recovery in manufacturing activity has boosted the production of manufactured goods in the US. The Fifth District Manufacturing Activity Survey shows strong demand for manufactured goods. Production is also increasing, but supply chain bottlenecks have been preventing production from reaching its full potential. Increased production has put pressure on supply chains. Many respondents reported experiencing supply chain disruptions that have affected their ability to keep necessary inventories. Backlogs and lead times for vendors have increased.
Over the past decade, the trade deficit for manufactured goods has more then doubled
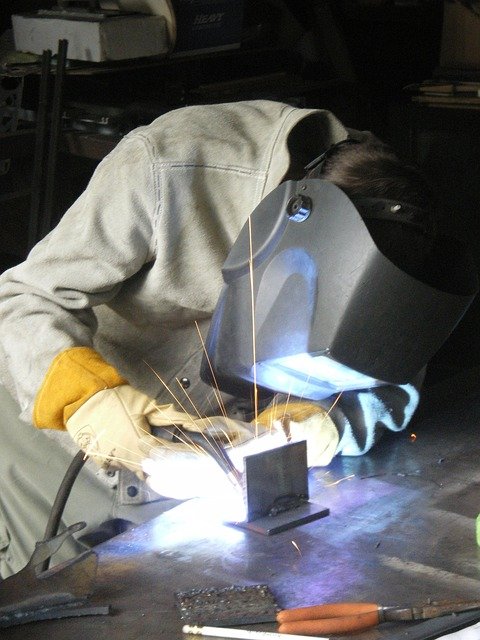
Some economists worry that the U.S.'s trade surplus will lower global growth and create more instability among its trading partners. Some argue that the high imports of manufactured goods from the United States are not necessarily bad for its economy. This is essential to maintaining global economic stability. The trade deficit may even be a necessary evil, since the U.S. relies heavily on foreign markets to generate its economic output, while high levels of foreign demand may make it difficult to achieve full employment.
The U.S. trade deficit in manufactured goods has nearly doubled since 2000. Partly, this is due to an increase in Chinese imports. The problem is even more severe: this imbalance is concentrated at the manufacturing sector, where wages are down and employment is declining since the 1990s. US manufacturing employment has declined dramatically, from 26 percent in 1970 down to 8.5 percent in 2016. Some economists attribute the decline to China's increased competition, but most attribute the decline to automation, productivity increases, and demand shifting away from goods to services.
Industry uses a shotgun approach
While the US manufacturing industry has a wide range of advanced manufacturing initiatives and is well-established in this field, some countries are taking a single-shot approach to bringing the internet of things into manufacturing. The US, on the other hand, focuses on diverse technologies and combines Internet advertising with traditional mass media. The result is a shotgun approach, where companies focus on many different technologies and aim for a broad customer base.
FAQ
What is the responsibility of a logistics manager?
Logistics managers make sure all goods are delivered on schedule and without damage. This is done using his/her knowledge of the company's products. He/she also needs to ensure adequate stock to meet demand.
How can manufacturing reduce production bottlenecks?
You can avoid bottlenecks in production by making sure that everything runs smoothly throughout the production cycle, from the moment you receive an order to the moment the product is shipped.
This includes both quality control and capacity planning.
Continuous improvement techniques such Six Sigma are the best method to accomplish this.
Six Sigma can be used to improve the quality and decrease waste in all areas of your company.
It emphasizes consistency and eliminating variance in your work.
How can manufacturing efficiency be improved?
First, we need to identify which factors are most critical in affecting production times. We must then find ways that we can improve these factors. If you don’t know where to begin, consider which factors have the largest impact on production times. Once you identify them, look for solutions.
How can excess manufacturing production be reduced?
Better inventory management is key to reducing excess production. This would reduce the amount of time spent on unnecessary activities such as purchasing, storing, and maintaining excess stock. This could help us free up our time for other productive tasks.
This can be done by using a Kanban system. A Kanban Board is a visual display that tracks work progress. Work items are moved through various states to reach their destination in a Kanban system. Each state represents an individual priority level.
For instance, when work moves from one stage to another, the current task is complete enough to be moved to the next stage. But if a task remains in the beginning stages it will stay that way until it reaches its end.
This allows work to move forward and ensures that no work is missed. Managers can monitor the work being done by Kanban boards to see what is happening at any given time. This allows them to adjust their workflows based on real-time information.
Lean manufacturing is another option to control inventory levels. Lean manufacturing focuses on eliminating waste throughout the entire production chain. Anything that does not contribute to the product's value is considered waste. These are some of the most common types.
-
Overproduction
-
Inventory
-
Unnecessary packaging
-
Overstock materials
These ideas can help manufacturers improve efficiency and reduce costs.
Is automation important in manufacturing?
Automating is not just important for manufacturers, but also for service providers. Automation allows them to deliver services quicker and more efficiently. It reduces human errors and improves productivity, which in turn helps them lower their costs.
What skills does a production planner need?
Being a production planner is not easy. You need to be organized and flexible. Communication skills are essential to ensure that you can communicate effectively with clients, colleagues, and customers.
What are the products of logistics?
Logistics is the process of moving goods from one point to another.
They include all aspects associated with transport including packaging, loading transporting, unloading storage, warehousing inventory management customer service, distribution returns and recycling.
Logisticians ensure that the right product reaches the right place at the right time and under safe conditions. They provide information on demand forecasts as well stock levels, production schedules and availability of raw material.
They also keep track of shipments in transit, monitor quality standards, perform inventories and order replenishment, coordinate with suppliers and vendors, and provide support services for sales and marketing.
Statistics
- Job #1 is delivering the ordered product according to specifications: color, size, brand, and quantity. (netsuite.com)
- It's estimated that 10.8% of the U.S. GDP in 2020 was contributed to manufacturing. (investopedia.com)
- In the United States, for example, manufacturing makes up 15% of the economic output. (twi-global.com)
- You can multiply the result by 100 to get the total percent of monthly overhead. (investopedia.com)
- According to a Statista study, U.S. businesses spent $1.63 trillion on logistics in 2019, moving goods from origin to end user through various supply chain network segments. (netsuite.com)
External Links
How To
How to Use 5S for Increasing Productivity in Manufacturing
5S stands for "Sort", "Set In Order", "Standardize", "Separate" and "Store". Toyota Motor Corporation was the first to develop the 5S approach in 1954. It allows companies to improve their work environment, thereby achieving greater efficiency.
This approach aims to standardize production procedures, making them predictable, repeatable, and easily measurable. This means that tasks such as cleaning, sorting, storing, packing, and labeling are performed daily. These actions allow workers to perform their job more efficiently, knowing what to expect.
Five steps are required to implement 5S: Sort, Set In Order, Standardize. Separate. Each step requires a different action, which increases efficiency. If you sort items, it makes them easier to find later. You arrange items by placing them in an order. Next, organize your inventory into categories and store them in containers that are easily accessible. Finally, label all containers correctly.
Employees must be able to critically examine their work practices. Employees must understand why they do certain tasks and decide if there's another way to accomplish them without relying on the old ways of doing things. In order to use the 5S system effectively, they must be able to learn new skills.
The 5S method increases efficiency and morale among employees. As they begin to see improvements, they feel motivated to continue working towards the goal of achieving higher levels of efficiency.