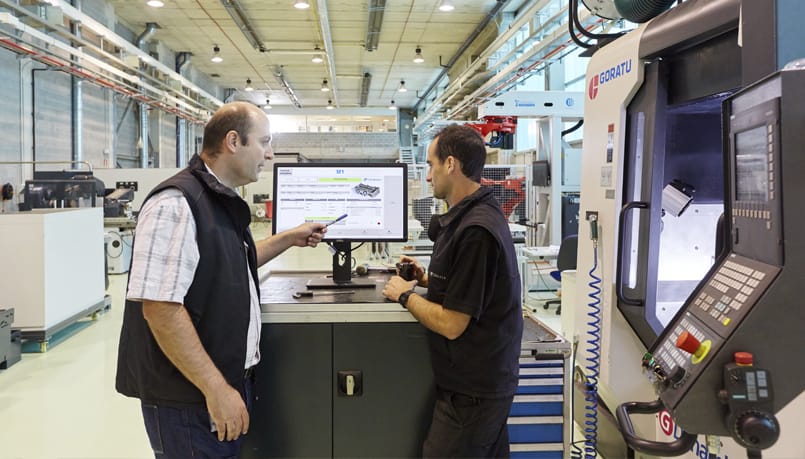
What does an environmental scientist do in mining?
Engineers in the mineral industry play an essential role in making it possible to gather, refine, and transport the raw materials that we use in everyday life. Engineers in the mineral industry also design systems to make mining and refinement profitable for companies that mine the material and sell it.
How much money does a mine engineer make?
The salary of a mining engineering depends on several factors, including company and position. An entry-level mining engineer may earn as much as PS22,000 per annum, but with experience, this figure can reach PS50,000. Senior engineers are able to earn PS80,000 per annum or even more.
What subjects is mining engineering concerned with?
The career of a mining engineer requires an understanding of a range of disciplines, such as electrical, mechanical, and geological engineering. They must have the ability to design and operate equipment, manage mining operations, and provide technical support to their fellow engineers.
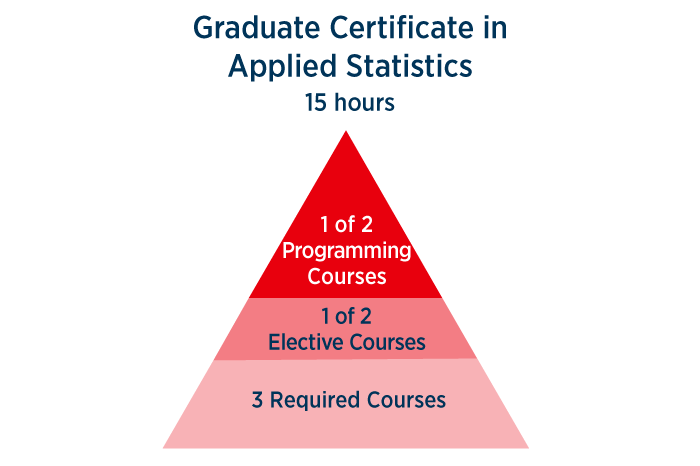
How to get a mining engineer job
It is important to have a college degree and work experience before you can pursue a career in mining engineering. This will give you the chance to show off your skills and demonstrate to prospective employers that you have the right attitude and qualifications. You can also seek opportunities to do a placement with a mining engineering firm, which will allow you to apply your knowledge in a real-life setting.
How to find a mining engineer job
The majority of mining engineering jobs are located overseas, although there are some opportunities in the UK, particularly at larger international companies. These jobs often involve long-term travel and working on the job site.
How to choose a career in mining engineering
A mining engineer career can be challenging, yet it offers ample opportunities for progress and professional growth. You can advance to become a leader or senior engineer. Then, you will be able to take on managerial and strategy responsibilities.
How to prepare a Mining Engineer job
The requirements for a career as a mining engineer include a university degree and relevant work experience. Graduating students can start their careers by working as trainees under the guidance of an experienced professional. This gives you the opportunity to enhance your skills while building a network.
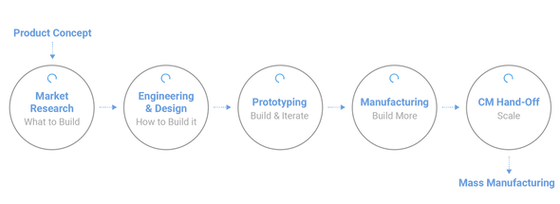
How to seek a mining engineer job
It is best to search for mining engineering jobs at major mining companies. These firms have vacancies that you can search for online, through specialist recruitment agencies, or in publications like targetjobs Engineering Mining Journal and InfoMine. You can search for speculative vacancies in the Directory of Mines and Quarries published by the British Geological Survey.
How to become a mining engineer
Earning a bachelor's, master's, or PhD in a subject related to geology will help you start your career in mining. You'll also need practical experience. If you are interested in the topic, you might also consider a PhD.
FAQ
What is the distinction between Production Planning or Scheduling?
Production Planning (PP) refers to the process of determining how much production is needed at any given moment. This can be done by forecasting demand and identifying production capabilities.
Scheduling is the process of assigning specific dates to tasks so they can be completed within the specified timeframe.
What do we need to know about Manufacturing Processes in order to learn more about Logistics?
No. You don't have to know about manufacturing processes before learning about logistics. It is important to know about the manufacturing processes in order to understand how logistics works.
How does manufacturing avoid bottlenecks in production?
The key to avoiding bottlenecks in production is to keep all processes running smoothly throughout the entire production cycle, from the time you receive an order until the time when the product ships.
This includes both planning for capacity and quality control.
This can be done by using continuous improvement techniques, such as Six Sigma.
Six Sigma is a management system used to improve quality and reduce waste in every aspect of your organization.
It emphasizes consistency and eliminating variance in your work.
What is the job of a production plan?
Production planners ensure that all project aspects are completed on time, within budget and within the scope. They also ensure the quality of the product and service meets the client's requirements.
Statistics
- According to the United Nations Industrial Development Organization (UNIDO), China is the top manufacturer worldwide by 2019 output, producing 28.7% of the total global manufacturing output, followed by the United States, Japan, Germany, and India.[52][53] (en.wikipedia.org)
- In 2021, an estimated 12.1 million Americans work in the manufacturing sector.6 (investopedia.com)
- You can multiply the result by 100 to get the total percent of monthly overhead. (investopedia.com)
- In the United States, for example, manufacturing makes up 15% of the economic output. (twi-global.com)
- Job #1 is delivering the ordered product according to specifications: color, size, brand, and quantity. (netsuite.com)
External Links
How To
How to Use lean manufacturing in the Production of Goods
Lean manufacturing is a management style that aims to increase efficiency and reduce waste through continuous improvement. It was created in Japan by Taiichi Ohno during the 1970s and 80s. He received the Toyota Production System award (TPS), from Kanji Toyoda, founder of TPS. Michael L. Watkins published the book "The Machine That Changed the World", which was the first to be published about lean manufacturing.
Lean manufacturing is often defined as a set of principles used to improve the quality, speed, and cost of products and services. It emphasizes reducing defects and eliminating waste throughout the value chain. The five-steps of Lean Manufacturing are just-in time (JIT), zero defect and total productive maintenance (TPM), as well as 5S. Lean manufacturing seeks to eliminate non-value added activities, such as inspection, work, waiting, and rework.
In addition to improving product quality and reducing costs, lean manufacturing helps companies achieve their goals faster and reduces employee turnover. Lean Manufacturing is one of the most efficient ways to manage the entire value chains, including suppliers and customers as well distributors and retailers. Lean manufacturing practices are widespread in many industries. For example, Toyota's philosophy underpins its success in automobiles, electronics, appliances, healthcare, chemical engineering, aerospace, paper, food, etc.
Five principles are the basis of lean manufacturing:
-
Define value - Find out what your business contributes to society, and what makes it different from other competitors.
-
Reduce waste - Stop any activity that isn't adding value to the supply chains.
-
Create Flow. Ensure that your work is uninterrupted and flows seamlessly.
-
Standardize and Simplify – Make processes as consistent, repeatable, and as simple as possible.
-
Building Relationships – Establish personal relationships with both external and internal stakeholders.
Lean manufacturing, although not new, has seen renewed interest in the economic sector since 2008. Many businesses are now using lean manufacturing to improve their competitiveness. Some economists even believe that lean manufacturing can be a key factor in economic recovery.
Lean manufacturing is becoming a popular practice in automotive. It has many advantages. These include better customer satisfaction and lower inventory levels. They also result in lower operating costs.
It can be applied to any aspect of an organisation. It is especially useful for the production aspect of an organization, as it ensures that every step in the value chain is efficient and effective.
There are three main types in lean manufacturing
-
Just-in Time Manufacturing: This lean manufacturing method is commonly called "pull systems." JIT is a process in which components can be assembled at the point they are needed, instead of being made ahead of time. This strategy aims to decrease lead times, increase availability of parts and reduce inventory.
-
Zero Defects Manufacturing - ZDM: ZDM focuses its efforts on making sure that no defective units leave a manufacturing facility. It is better to repair a part than have it removed from the production line if it needs to be fixed. This is true even for finished products that only require minor repairs prior to shipping.
-
Continuous Improvement (CI: Continuous improvement aims to increase the efficiency of operations by constantly identifying and making improvements to reduce or eliminate waste. Continuous Improvement (CI) involves continuous improvement in processes, people, tools, and infrastructure.