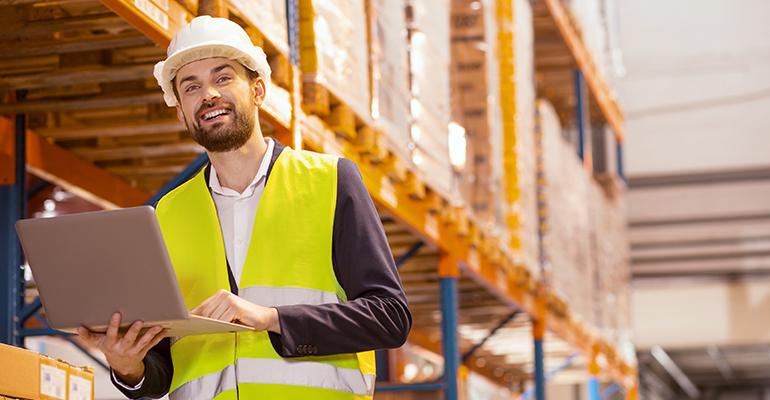
Amazon is seeking Supply Chain Managements with proven track records and senior leadership experience to oversee strategic cross-functional operations. These positions will be responsible for overseeing projects that support new products or operations and working closely with business teams across the globe. They will manage large-scale projects and develop cross-functional teams.
Manager, Supply Chain and Purchasing
Amazon Purchasing and Supply Chain managers are charged with a wide range of responsibilities. This includes driving cost savings, optimizing processes and mitigating risk. These responsibilities require strong analytical, negotiation, and communication skills.
The ideal candidate for this position is a self-starter who has strong communication and attention to detail. He or she should be able work independently, meet tight deadlines and manage their workload well.
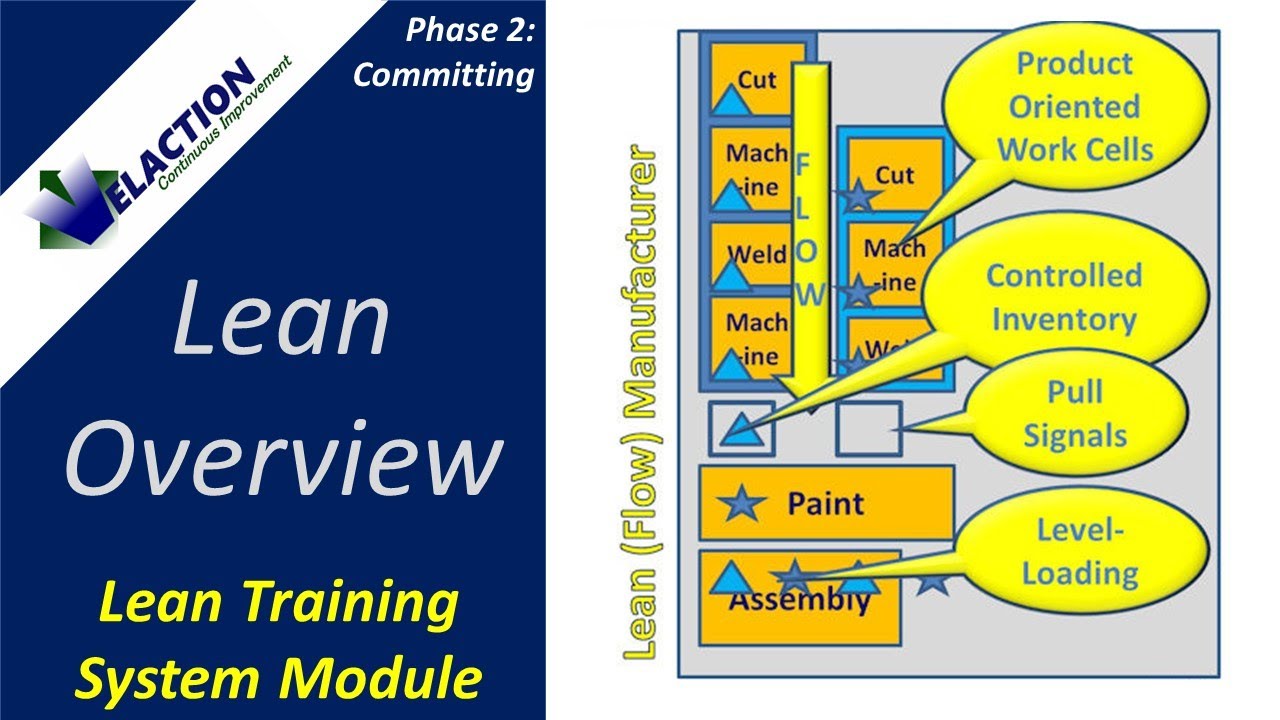
Analyze cost
Amazon's supply-chain is an integral part to its success. It involves all aspects of fulfillment, transportation, and forecasting. This job requires an analytical person who is passionate about details. The person will use data analysis to help understand the company's operation. The analyst will be working with global stakeholders and interpret data to draw conclusions. They can use MS Excel, SQL or both to perform their analysis.
Amazon's supply network is one of most innovative in world. Amazon is constantly investing in warehouse technology, trucking capabilities, as well as other infrastructure. Amazon is also investing heavily into drones and cargo planes.
Program manager
Amazon supply chain job program managers require knowledge in all areas of supply chains planning, manufacturing, logistics. In addition, a successful applicant will be able to integrate across a team and make data-driven decisions. Additionally, the successful applicant will be required to manage and build systems and processes for quality control, scale, and risk management.
A Supply Chain Program Manager's salary varies widely depending on the city in which the position is located. Some earn over $168,000 a year, while others earn as little as $52,500. On average, Program managers earn between $87,500 and $127,500 annually. The salary ranges can be as high as $40,000 depending on their experience and where they work.
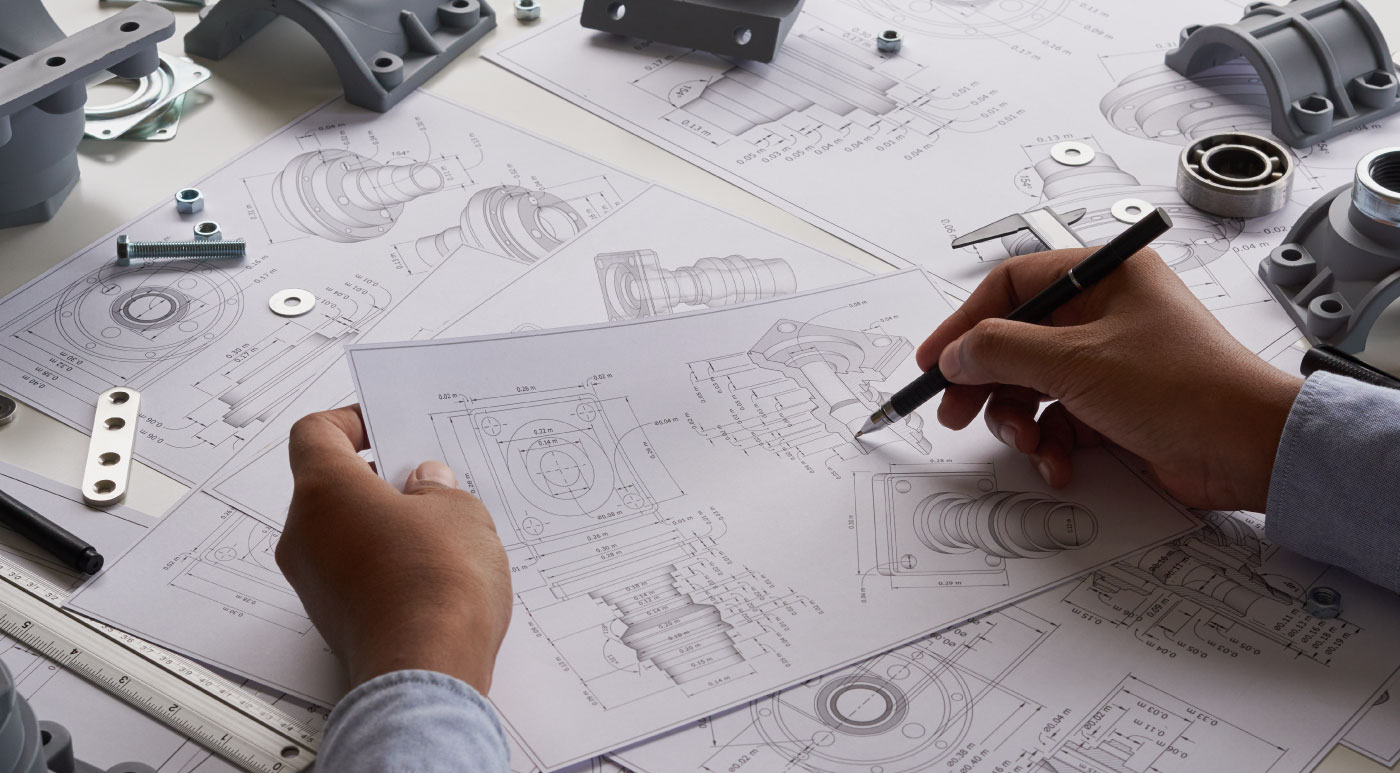
Warehouse manager
Warehouse management is a highly-sought-after job, and there is a growing demand. Although there are not any specific education requirements for warehouse managers, employers prefer to hire people with some experience. However, a bachelor's is an advantage for this job.
Warehouse managers have many responsibilities, including customer service and inventory management. They have a major impact on the experience of shippers and operators. These individuals are responsible for the overall performance of the supply chain and can develop strategies to improve efficiency. They can also work with many Amazon teams and have broad exposure to their operations.
FAQ
What are the differences between these four types?
Manufacturing refers to the transformation of raw materials into useful products by using machines and processes. Manufacturing can include many activities such as designing and building, testing, packaging shipping, selling, servicing, and other related activities.
What is the difference between Production Planning and Scheduling?
Production Planning (PP), also known as forecasting and identifying production capacities, is the process that determines what product needs to be produced at any particular time. Forecasting and identifying production capacity are two key elements to this process.
Scheduling involves the assignment of dates and times to tasks in order to complete them within the timeframe.
Is automation important for manufacturing?
Not only are service providers and manufacturers important, but so is automation. It allows them to offer services faster and more efficiently. It also helps to reduce costs and improve productivity.
Do we need to know about Manufacturing Processes before learning about Logistics?
No. No. However, knowing about manufacturing processes will definitely give you a better understanding of how logistics works.
How can manufacturing overproduction be reduced?
In order to reduce excess production, you need to develop better inventory management methods. This would reduce the amount of time spent on unnecessary activities such as purchasing, storing, and maintaining excess stock. By doing this, we could free up resources for other productive tasks.
This can be done by using a Kanban system. A Kanbanboard is a visual tool that allows you to keep track of the work being done. Kanban systems are where work items travel through a series of states until reaching their final destination. Each state has a different priority level.
As an example, if work is progressing from one stage of the process to another, then the current task is complete and can be transferred to the next. A task that is still in the initial stages of a process will be considered complete until it moves on to the next stage.
This helps to keep work moving forward while ensuring that no work is left behind. Managers can see how much work has been done and the status of each task at any time with a Kanban Board. This information allows managers to adjust their workflow based off real-time data.
Another way to control inventory levels is to implement lean manufacturing. Lean manufacturing emphasizes eliminating waste in all phases of production. Anything that does nothing to add value to a product is waste. These are some of the most common types.
-
Overproduction
-
Inventory
-
Packaging not required
-
Material surplus
These ideas will help manufacturers increase efficiency and lower costs.
What does manufacturing industry mean?
Manufacturing Industries are companies that manufacture products. These products are sold to consumers. These companies employ many processes to achieve this purpose, such as production and distribution, retailing, management and so on. These companies produce goods using raw materials and other equipment. This includes all types if manufactured goods.
What is the importance of logistics in manufacturing?
Logistics are an integral part any business. They help you achieve great results by helping you manage all aspects of product flow, from raw materials to finished goods.
Logistics play a key role in reducing expenses and increasing efficiency.
Statistics
- It's estimated that 10.8% of the U.S. GDP in 2020 was contributed to manufacturing. (investopedia.com)
- According to the United Nations Industrial Development Organization (UNIDO), China is the top manufacturer worldwide by 2019 output, producing 28.7% of the total global manufacturing output, followed by the United States, Japan, Germany, and India.[52][53] (en.wikipedia.org)
- In the United States, for example, manufacturing makes up 15% of the economic output. (twi-global.com)
- In 2021, an estimated 12.1 million Americans work in the manufacturing sector.6 (investopedia.com)
- (2:04) MTO is a production technique wherein products are customized according to customer specifications, and production only starts after an order is received. (oracle.com)
External Links
How To
Six Sigma: How to Use it in Manufacturing
Six Sigma is defined as "the application of statistical process control (SPC) techniques to achieve continuous improvement." It was developed by Motorola's Quality Improvement Department at their plant in Tokyo, Japan, in 1986. Six Sigma's core idea is to improve the quality of processes by standardizing and eliminating defects. Since there are no perfect products, or services, this approach has been adopted by many companies over the years. The main goal of Six Sigma is to reduce variation from the mean value of production. You can calculate the percentage of deviation from the norm by taking a sample of your product and comparing it to the average. If you notice a large deviation, then it is time to fix it.
Understanding the dynamics of variability within your business is the first step in Six Sigma. Once you've understood that, you'll want to identify sources of variation. You'll also want to determine whether these variations are random or systematic. Random variations are caused by human errors. Systematic variations can be caused by outside factors. Random variations would include, for example, the failure of some widgets to fall from the assembly line. However, if you notice that every time you assemble a widget, it always falls apart at exactly the same place, then that would be a systematic problem.
Once you identify the problem areas, it is time to create solutions. The solution could involve changing how you do things, or redesigning your entire process. You should then test the changes again after they have been implemented. If they fail, you can go back to the drawing board to come up with a different plan.