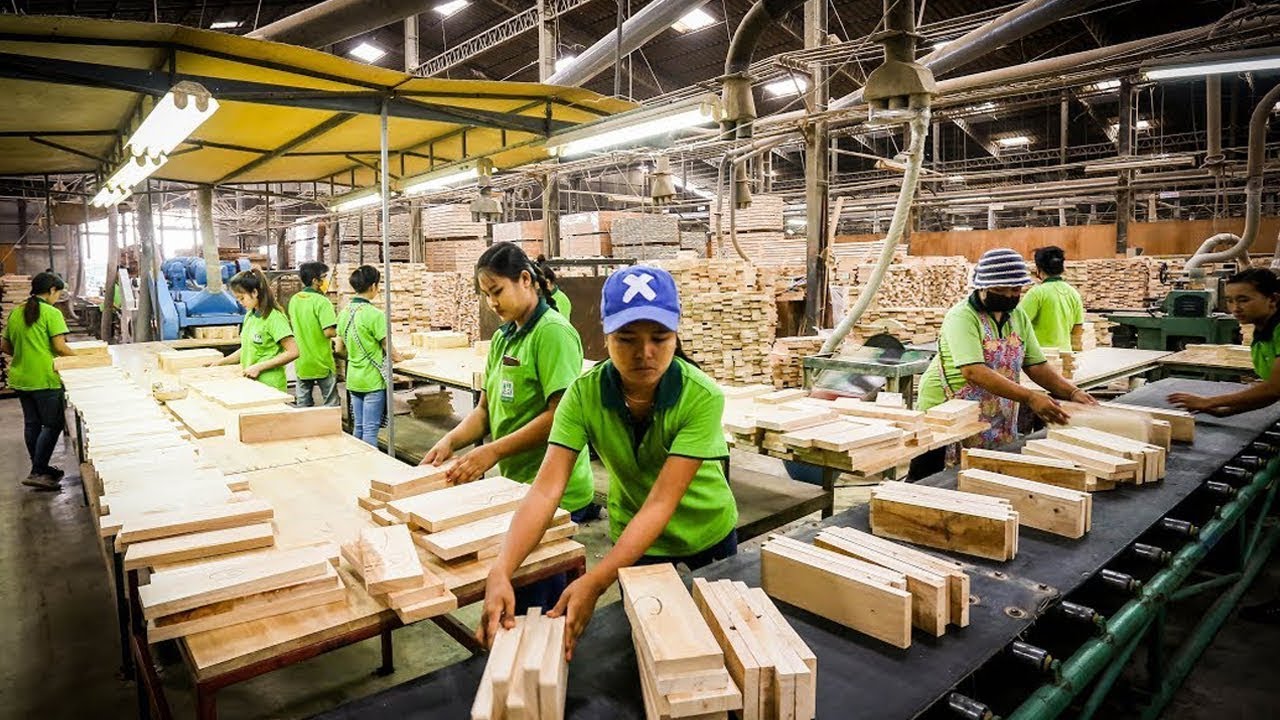
Purchasing Managers, also known as Materials Managers, are responsible for sourcing and coordinating all purchasing activities. They interact with suppliers, vendors, and other purchasing agents. They need to be familiar with the company's buying process and how they can improve it. They must also be able to negotiate the best deals for the company.
Purchaser managers must also keep accurate and current purchasing records. They assess customer needs, analyze financial statements, evaluate vendors' capabilities, and evaluate price trends. They also coordinate purchasing activities. They may be required to work overtime if the company needs supplies from international markets.
As well as managing inventory and logistics, purchasing managers coordinate and manage them. They also determine the best purchasing method and make sure that all purchased items meet company quality standards. They also manage budgets, and collaborate with their staff in order to ensure that purchases are made for the best price. They are also able to negotiate contracts and find the best suppliers.
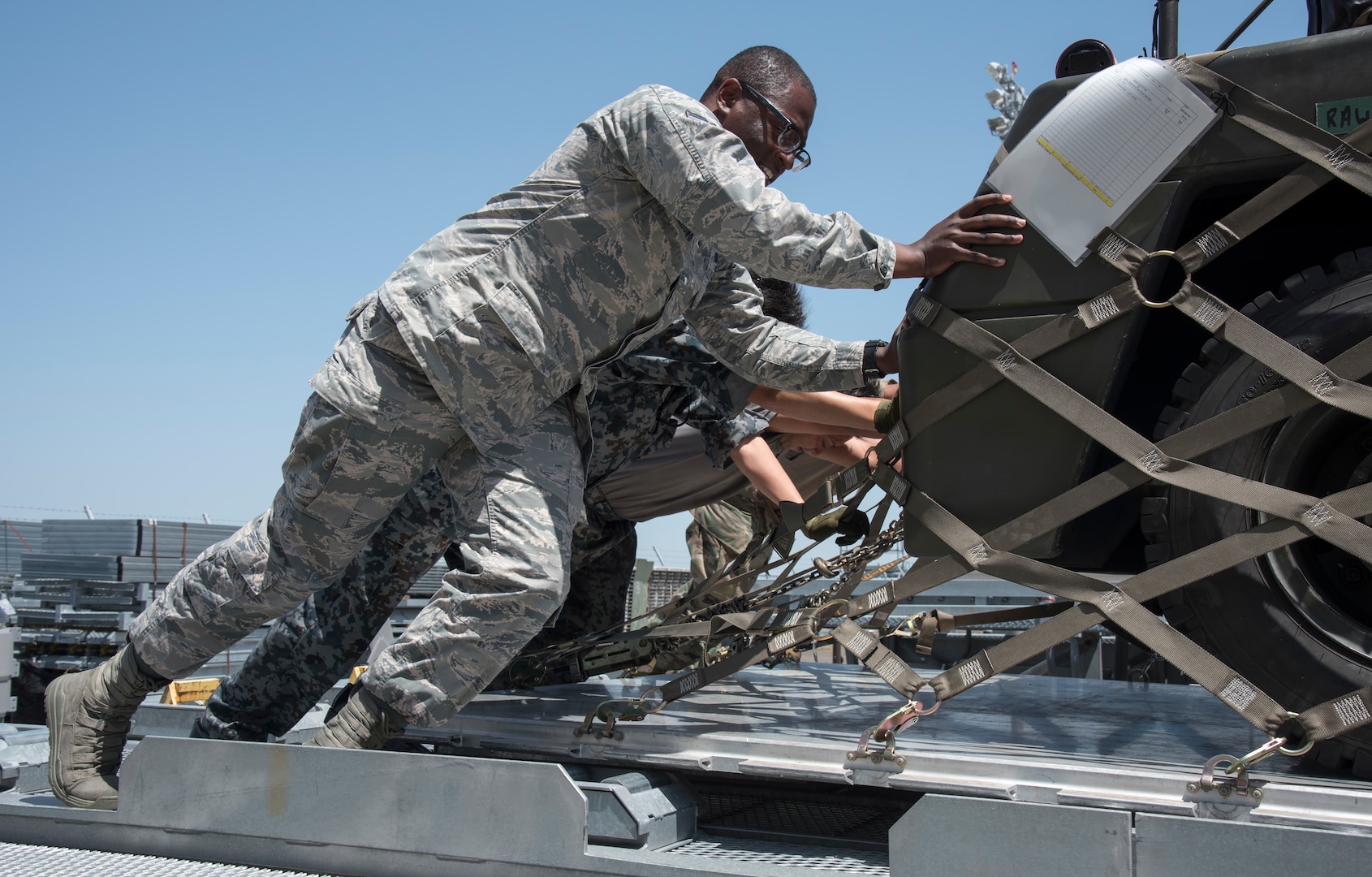
Purchasing Managers also monitor and manage the time schedules of all purchasing employees. They evaluate the quality, speed, and cost of all purchased goods. They also visit distributor centers and make contact with sellers. They also check that suppliers are adhering to the terms of the contract. They may also be responsible for disciplinary matters and team building.
Effective communication skills, analytical skills, and strategic thinking skills are required for purchasing managers. They need to be able analyse the effects of various products on the company. They must be able manage suppliers and their relationships. They should also be able take business decisions and increase sales. They must be able deal with complicated purchases. They need to be able analyze potential vendors and choose the best one for their company.
A bachelor's degree is required for most purchasing managers. It's also beneficial to have experience in inventory and supply chain management. They will also need to be proficient in Microsoft Office as well as other programs.
The best purchasing manager must be able to negotiate the most advantageous contracts and find the best deals. They must also be able coordinate all purchasing activities, manage inventories and track supplier and vendor performance. They should also be capable of managing a team consisting of purchasing agents.
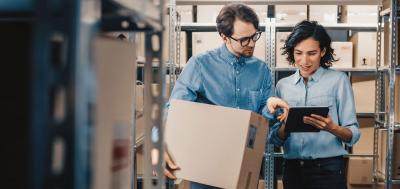
The purchase manager job description should also be able to mention how purchasing is essential to the company's success. It should also mention how important it is for the company to stay ahead of the curve. It should mention how employees are valued by the company. It should also contain a call to actions to encourage applicants.
If the company has to buy materials or equipment for international markets, Purchasing Managers might work overtime. They may also have to deal with vendors and sellers and attend trade shows.
FAQ
What skills do production planners need?
You must be flexible and organized to become a productive production planner. Effective communication with clients and colleagues is essential.
Can some manufacturing processes be automated?
Yes! Automation has been around since ancient times. The wheel was invented by the Egyptians thousands of years ago. We now use robots to help us with assembly lines.
There are many uses of robotics today in manufacturing. They include:
-
Automation line robots
-
Robot welding
-
Robot painting
-
Robotics inspection
-
Robots create products
Automation can be applied to manufacturing in many other ways. 3D printing is a way to make custom products quickly and without waiting weeks or months for them to be manufactured.
How can excess manufacturing production be reduced?
Better inventory management is key to reducing excess production. This would reduce the amount of time spent on unnecessary activities such as purchasing, storing, and maintaining excess stock. This will allow us to free up resources for more productive tasks.
One way to do this is to adopt a Kanban system. A Kanbanboard is a visual tool that allows you to keep track of the work being done. Work items are moved through various states to reach their destination in a Kanban system. Each state has a different priority level.
As an example, if work is progressing from one stage of the process to another, then the current task is complete and can be transferred to the next. But if a task remains in the beginning stages it will stay that way until it reaches its end.
This keeps work moving and ensures no work is lost. With a Kanban board, managers can see exactly how much work is being done at any given moment. This allows them to adjust their workflows based on real-time information.
Lean manufacturing can also be used to reduce inventory levels. Lean manufacturing seeks to eliminate waste from every step of the production cycle. Anything that doesn't add value to the product is considered waste. Some common types of waste include:
-
Overproduction
-
Inventory
-
Unnecessary packaging
-
Excess materials
Manufacturers can reduce their costs and improve their efficiency by using these ideas.
What's the difference between Production Planning & Scheduling?
Production Planning (PP), or production planning, is the process by which you determine what products are needed at any given time. Forecasting demand is one way to do this.
Scheduling is the process of assigning specific dates to tasks so they can be completed within the specified timeframe.
What is the role of a logistics manager
A logistics manager makes sure that all goods are delivered on-time and in good condition. This is done by using his/her experience and knowledge of the company's products. He/she should make sure that enough stock is on hand to meet the demands.
How can manufacturing prevent production bottlenecks?
Production bottlenecks can be avoided by ensuring that processes are running smoothly during the entire production process, starting with the receipt of an order and ending when the product ships.
This includes planning for capacity requirements as well as quality control measures.
Continuous improvement techniques like Six Sigma are the best way to achieve this.
Six Sigma is a management system used to improve quality and reduce waste in every aspect of your organization.
It is focused on creating consistency and eliminating variation in your work.
What is production planning?
Production Planning includes planning for all aspects related to production. This document is designed to make sure everything is ready for when you're ready to shoot. This document should include information about how to achieve the best results on-set. This information includes locations, crew details and equipment requirements.
First, you need to plan what you want to film. You may have already chosen the location you want, or there are locations or sets you prefer. Once you have determined your scenes and locations, it is time to start figuring out the elements that you will need for each scene. You might decide you need a car, but not sure what make or model. This is where you can look up car models online and narrow down your options by choosing from different makes and models.
Once you have found the right vehicle, you can think about adding accessories. Do you have people who need to be seated in the front seat? Perhaps you have someone who needs to be able to walk around the back of your car. Perhaps you would like to change the interior colour from black to white. These questions will help to determine the style and feel of your car. Also, think about what kind of shots you would like to capture. Will you be filming close-ups or wide angles? Maybe you want to show the engine and the steering wheel. These factors will help you determine which car style you want to film.
Once you have made all the necessary decisions, you can start to create a schedule. A schedule will tell you when you need to start shooting and when you need to finish. You will need to know when you have to be there, what time you have to leave and when your return home. This way, everyone knows what they need to do and when. You can also make sure to book extra staff in advance if you have to hire them. You should not hire anyone who doesn't show up because of your inaction.
You will need to factor in the days that you have to film when creating your schedule. Some projects only take one or two days, while others may last weeks. It is important to consider whether you require more than one photo per day when you create your schedule. Multiple takes at the same place will result in higher costs and longer completion times. It's better to be safe than sorry and shoot less takes if you're not certain whether you need more takes.
Budget setting is an important part of production planning. As it will allow you and your team to work within your financial means, setting a realistic budget is crucial. Remember that you can always reduce the budget later on if you run into unforeseen problems. You shouldn't underestimate the amount you'll spend. You will end up spending less money if you underestimate the cost of something.
Production planning is a complicated process. But once you understand how everything works together, it becomes much easier to plan future project.
Statistics
- Job #1 is delivering the ordered product according to specifications: color, size, brand, and quantity. (netsuite.com)
- It's estimated that 10.8% of the U.S. GDP in 2020 was contributed to manufacturing. (investopedia.com)
- [54][55] These are the top 50 countries by the total value of manufacturing output in US dollars for its noted year according to World Bank.[56] (en.wikipedia.org)
- You can multiply the result by 100 to get the total percent of monthly overhead. (investopedia.com)
- According to a Statista study, U.S. businesses spent $1.63 trillion on logistics in 2019, moving goods from origin to end user through various supply chain network segments. (netsuite.com)
External Links
How To
How to Use 5S to Increase Productivity in Manufacturing
5S stands in for "Sort", the "Set In Order", "Standardize", or "Separate". The 5S methodology was developed at Toyota Motor Corporation in 1954. This methodology helps companies improve their work environment to increase efficiency.
The idea behind standardizing production processes is to make them repeatable and measurable. It means tasks like cleaning, sorting or packing, labeling, and storing are done every day. Through these actions, workers can perform their jobs more efficiently because they know what to expect from them.
Implementing 5S requires five steps. These are Sort, Set In Order, Standardize. Separate. And Store. Each step is a different action that leads to greater efficiency. By sorting, for example, you make it easy to find the items later. You arrange items by placing them in an order. Then, after you separate your inventory into groups, you store those groups in containers that are easy to access. Labeling your containers will ensure that everything is correctly labeled.
Employees need to reflect on how they do their jobs. Employees must be able to see why they do what they do and find a way to achieve them without having to rely on their old methods. To be successful in the 5S system, employees will need to acquire new skills and techniques.
The 5S method not only increases efficiency but also boosts morale and teamwork. They will feel motivated to strive for higher levels of efficiency once they start to see results.