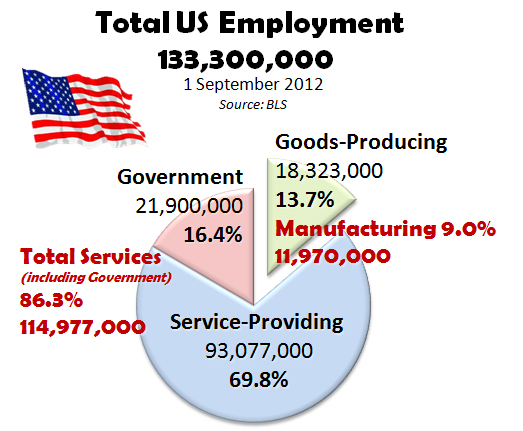
You need to know what you can expect to make, whether you are seeking a job or studying industrial engineering. The salary for industrial engineers varies depending on the type of degree you earn, your industry, and your experience. The average industrial engineer salary is $95,300. The highest-paid metropolitan areas have higher salaries.
Industrial engineers are responsible for designing, developing and installing systems that increase the productivity of the production process. They can also help make workplaces safer. An industrial engineer may also design equipment and plan facilities. This is possible by analysing how changes to design impact the cost of manufacturing the product.
Experienced industrial engineers can get a high salary. They can also earn a higher salary if they have a master's degree in industrial engineering. This degree is very popular with international students and can lead to a career as a manufacturing, healthcare, or engineering service professional.
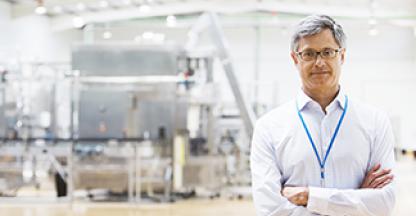
The next decade will see a rapid increase in the number of industrial engineers. From 2021 to 2031, the employment of industrial engineers will grow by 10 percent. This is higher that the average for all occupations. The top 10% of industrial engineers earn more than $85,000 per year. With management experience, they are likely to earn more. Industrial engineers who have advanced degrees in industrial engineering can perform cost-benefit analyses, evaluate cost distribution in operational processes, negotiate for purchasing decisions, and even conduct cost-benefit reviews.
Industrial engineers have the ability to think outside of the box and find creative ways to make processes more efficient. Many industrial engineers work in offices, and they may interact with production workers. Industrial engineers can also handle telephone calls, emails and face-to–face conversations. They may also present their plans in written reports or oral presentations.
You can expect to find employment as an industrial engineer in many industries such as construction, transport, energy, and pharmaceuticals. They may also be responsible for developing systems that reduce waste in production, depending on their industry.
A bachelor's degree is usually required for industrial engineers. A master's degree can be obtained in industrial engineering for a career as an engineer consultant or manufacturer. The majority of programs offer courses in math, science, general engineering, and other subjects. The program can take two to seven years to complete.
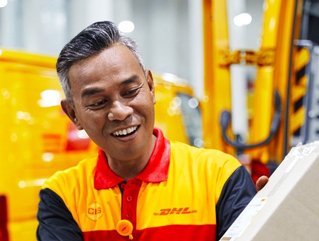
The average salary of an entry-level industrial engineering engineer is $65,000 to $75,000. However, the range of salaries increases as one gets more experience. A salary for an experienced industrial engineering engineer is $86,809 per annum. An industrial engineer's annual salary can rise if they are awarded a masters or doctorate in the field.
A good technical and communication skill is essential for industrial engineers. They must be able solve problems outside of their usual scope. They need to know how to integrate materials, equipment, and workers to create efficient systems. They should also possess good interpersonal skills. The job is challenging and can be rewarding.
FAQ
What is the difference between Production Planning, Scheduling and Production Planning?
Production Planning (PP) is the process of determining what needs to be produced at any given point in time. This is done through forecasting demand and identifying production capacities.
Scheduling involves the assignment of dates and times to tasks in order to complete them within the timeframe.
What are the responsibilities of a logistic manager?
Logistics managers ensure that goods arrive on time and are unharmed. This is accomplished by using the experience and knowledge gained from working with company products. He/she should ensure that sufficient stock is available in order to meet customer demand.
What is meant by manufacturing industries?
Manufacturing Industries are those businesses that make products for sale. Consumers are those who purchase these products. These companies employ many processes to achieve this purpose, such as production and distribution, retailing, management and so on. They manufacture goods from raw materials using machines and other equipment. This includes all types and varieties of manufactured goods, such as food items, clothings, building supplies, furnitures, toys, electronics tools, machinery vehicles, pharmaceuticals medical devices, chemicals, among others.
What are the differences between these four types?
Manufacturing is the process by which raw materials are transformed into useful products through machines and processes. It can involve many activities like designing, manufacturing, testing packaging, shipping, selling and servicing.
What is the importance of automation in manufacturing?
Not only are service providers and manufacturers important, but so is automation. It allows them provide faster and more efficient services. They can also reduce their costs by reducing human error and improving productivity.
Why automate your warehouse
Modern warehouses have become more dependent on automation. E-commerce has increased the demand for quicker delivery times and more efficient processes.
Warehouses need to adapt quickly to meet changing needs. Technology investment is necessary to enable warehouses to respond quickly to changing demands. Automation of warehouses offers many benefits. Here are some reasons why it's worth investing in automation:
-
Increases throughput/productivity
-
Reduces errors
-
Accuracy is improved
-
Safety is boosted
-
Eliminates bottlenecks
-
Companies can scale more easily
-
It makes workers more efficient
-
It gives visibility to everything that happens inside the warehouse
-
Enhances customer experience
-
Improves employee satisfaction
-
Reducing downtime and increasing uptime
-
High quality products delivered on-time
-
Removing human error
-
It ensures compliance with regulations
What is manufacturing and logistics?
Manufacturing refers to the process of making goods using raw materials and machines. Logistics covers all aspects involved in managing supply chains, including procurement and production planning. Logistics and manufacturing are often referred to as one thing. It encompasses both the creation of products and their delivery to customers.
Statistics
- Job #1 is delivering the ordered product according to specifications: color, size, brand, and quantity. (netsuite.com)
- [54][55] These are the top 50 countries by the total value of manufacturing output in US dollars for its noted year according to World Bank.[56] (en.wikipedia.org)
- (2:04) MTO is a production technique wherein products are customized according to customer specifications, and production only starts after an order is received. (oracle.com)
- Many factories witnessed a 30% increase in output due to the shift to electric motors. (en.wikipedia.org)
- You can multiply the result by 100 to get the total percent of monthly overhead. (investopedia.com)
External Links
How To
How to use lean manufacturing in the production of goods
Lean manufacturing is a management style that aims to increase efficiency and reduce waste through continuous improvement. It was developed in Japan during the 1970s and 1980s by Taiichi Ohno, who received the Toyota Production System (TPS) award from TPS founder Kanji Toyoda. Michael L. Watkins published the first book on lean manufacturing in 1990.
Lean manufacturing, often described as a set and practice of principles, is aimed at improving the quality, speed, cost, and efficiency of products, services, and other activities. It is about eliminating defects and waste from all stages of the value stream. Lean manufacturing is also known as just in time (JIT), zero defect total productive maintenance(TPM), and five-star (S). Lean manufacturing focuses on eliminating non-value-added activities such as rework, inspection, and waiting.
Lean manufacturing improves product quality and costs. It also helps companies reach their goals quicker and decreases employee turnover. Lean manufacturing is a great way to manage the entire value chain including customers, suppliers, distributors and retailers as well as employees. Lean manufacturing is widely practiced in many industries around the world. For example, Toyota's philosophy underpins its success in automobiles, electronics, appliances, healthcare, chemical engineering, aerospace, paper, food, etc.
Lean manufacturing is based on five principles:
-
Define Value- Identify the added value your company brings to society. What makes you stand out from your competitors?
-
Reduce waste - Stop any activity that isn't adding value to the supply chains.
-
Create Flow - Make sure work runs smoothly without interruptions.
-
Standardize and Simplify – Make processes as consistent, repeatable, and as simple as possible.
-
Building Relationships – Establish personal relationships with both external and internal stakeholders.
Although lean manufacturing isn't a new concept in business, it has gained popularity due to renewed interest in the economy after the 2008 global financial crisis. Many businesses are now using lean manufacturing to improve their competitiveness. In fact, some economists believe that lean manufacturing will be an important factor in economic recovery.
Lean manufacturing is becoming a popular practice in automotive. It has many advantages. These include better customer satisfaction and lower inventory levels. They also result in lower operating costs.
You can apply Lean Manufacturing to virtually any aspect of your organization. Because it makes sure that all value chains are efficient and effectively managed, Lean Manufacturing is particularly helpful for organizations.
There are three main types in lean manufacturing
-
Just-in-Time Manufacturing (JIT): This type of lean manufacturing is commonly referred to as "pull systems." JIT refers to a system in which components are assembled at the point of use instead of being produced ahead of time. This approach reduces lead time, increases availability and reduces inventory.
-
Zero Defects Manufacturing (ZDM): ZDM focuses on ensuring that no defective units leave the manufacturing facility. If a part needs to be fixed during the assembly line, it should be repaired rather than scrapped. This applies to finished products, which may need minor repairs before they are shipped.
-
Continuous Improvement (CI),: Continuous improvement aims improve the efficiency and effectiveness of operations by continuously identifying issues and making changes to reduce waste. Continuous improvement involves continuous improvement of processes and people as well as tools.