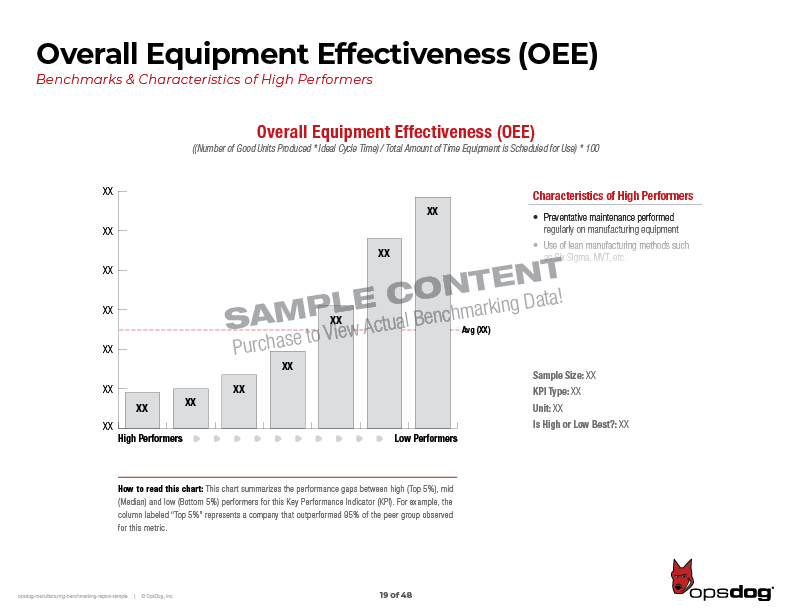
Blue collar jobs are generally manual labor jobs. These jobs might be in the fields of agriculture, manufacturing, healthcare or hospitality. Some may require some degree of skill, such as a plumber or electrician, while others may be unskilled. Blue collar jobs are good for career growth and pay decent salaries.
The Fourth Industrial Revolution is changing the landscape for manual workers. This revolution includes artificial intelligence, robotics, machine learning, and 3D printing. It will require a new, more skilled workforce for companies to succeed. It will also require firms to shift away from transactional relationships, and toward more enduring ones.
Therefore, many companies have to hire workers outside the United States. In some cases, these workers may be hired for per-item payments. Others may be paid by the project. In any case, the rise in demand for blue collar jobs is encouraging.
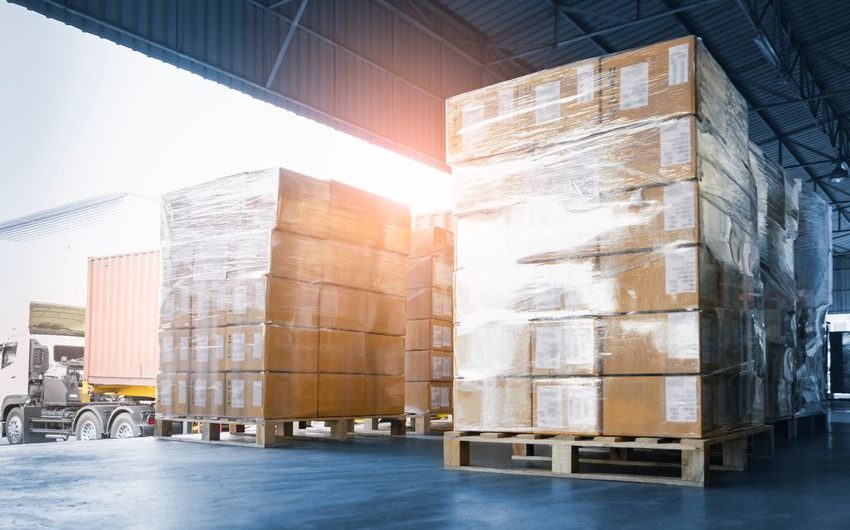
These jobs are more physically demanding than white collar jobs, but they tend to be well-paid. These jobs provide a steady income source and companies are prepared to invest in training employees. These jobs include signal and track switch operators, electrical and electronic repairers and nuclear power reactor operator. These jobs require only a high school diploma, while others require on-the-job training.
There are also more blue collar jobs than there are white collar ones. In fact, blue collar workers make up a substantial part of the Indian workforce. India has approximately 210 million employees in the agriculture sector and 290 millions in the nonagricultural. The demand is for blue collar workers growing rapidly.
Companies are also being transformed by the Fourth Industrial Revolution in how they manage their blue-collar workers. Companies are moving away from transactional relationships to build lasting relationships, and replacing manual jobs by digital ones. By putting employee needs first, firms are able to build stronger relationships and improved productivity.
The demand for blue collar workers is also high, but they are faced with competing realities. They might be worried about the stability and retirement of their jobs. Blue collar workers are optimistic about their future, regardless of their concerns. Actually, blue-collar employees are more likely to save for retirement. As the economy recovers, blue-collar jobs are expected to rise in popularity.
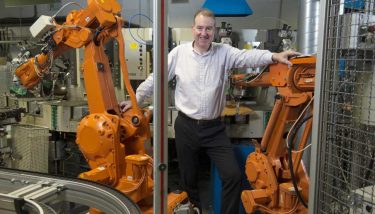
Automation is not threatening these jobs. The Association for Manufacturing Technology actually found that for every job replaced by technology, five new jobs are created. Signal and track-switch repairers received the highest average salary increase of $76,210 last year.
Blue collar jobs are also increasingly better paid. The earnings of many blue collar jobs are well above the national average, making it an ideal option for those looking for a job with good pay. Many blue collar jobs demand a high level of problem solving skills and can provide excellent career growth opportunities.
FAQ
What is it like to manage a logistics company?
You need to have a lot of knowledge and skills to manage a successful logistic business. Effective communication skills are necessary to work with suppliers and clients. You must be able analyze data and draw out conclusions. You need to be able work under pressure and manage stressful situations. In order to innovate and create new ways to improve efficiency, creativity is essential. You must be a strong leader to motivate others and direct them to achieve organizational goals.
You should also be organized and efficient to meet tight deadlines.
What is the responsibility of a production planner?
Production planners ensure that all project aspects are completed on time, within budget and within the scope. They make sure that the product and services meet client expectations.
How can we improve manufacturing efficiency?
First, we need to identify which factors are most critical in affecting production times. The next step is to identify the most important factors that affect production time. If you don’t know where to begin, consider which factors have the largest impact on production times. Once you've identified them all, find solutions to each one.
Is automation important for manufacturing?
Not only are service providers and manufacturers important, but so is automation. It allows them to offer services faster and more efficiently. In addition, it helps them reduce costs by reducing human errors and improving productivity.
What is the difference between a production planner and a project manager?
A production planner is more involved in the planning phase of the project than a project manger.
What skills does a production planner need?
You must be flexible and organized to become a productive production planner. Communication skills are essential to ensure that you can communicate effectively with clients, colleagues, and customers.
What is meant by manufacturing industries?
Manufacturing Industries is a group of businesses that produce goods for sale. These products are sold to consumers. These companies use various processes such as production, distribution, retailing, management, etc., to fulfill this purpose. They make goods from raw materials with machines and other equipment. This includes all types manufactured goods such as clothing, building materials, furniture, electronics, tools and machinery.
Statistics
- According to a Statista study, U.S. businesses spent $1.63 trillion on logistics in 2019, moving goods from origin to end user through various supply chain network segments. (netsuite.com)
- It's estimated that 10.8% of the U.S. GDP in 2020 was contributed to manufacturing. (investopedia.com)
- You can multiply the result by 100 to get the total percent of monthly overhead. (investopedia.com)
- [54][55] These are the top 50 countries by the total value of manufacturing output in US dollars for its noted year according to World Bank.[56] (en.wikipedia.org)
- In 2021, an estimated 12.1 million Americans work in the manufacturing sector.6 (investopedia.com)
External Links
How To
How to use lean manufacturing in the production of goods
Lean manufacturing is an approach to management that aims for efficiency and waste reduction. It was developed by Taiichi Okono in Japan, during the 1970s & 1980s. TPS founder Kanji Takoda awarded him the Toyota Production System Award (TPS). Michael L. Watkins published the first book on lean manufacturing in 1990.
Lean manufacturing is often described as a set if principles that help improve the quality and speed of products and services. It emphasizes the elimination and minimization of waste in the value stream. Lean manufacturing is called just-in-time (JIT), zero defect, total productive maintenance (TPM), or 5S. Lean manufacturing is about eliminating activities that do not add value, such as inspection, rework, and waiting.
Lean manufacturing is a way for companies to achieve their goals faster, improve product quality, and lower costs. Lean manufacturing has been deemed one of the best ways to manage the entire value-chain, including customers, distributors as well retailers and employees. Lean manufacturing is widely used in many industries. For example, Toyota's philosophy underpins its success in automobiles, electronics, appliances, healthcare, chemical engineering, aerospace, paper, food, etc.
Five fundamental principles underlie lean manufacturing.
-
Define Value: Identify the social value of your business and what sets you apart.
-
Reduce Waste – Eliminate all activities that don't add value throughout the supply chain.
-
Create Flow – Ensure that work flows smoothly throughout the process.
-
Standardize & simplify - Make processes consistent and repeatable.
-
Build Relationships- Develop personal relationships with both internal as well as external stakeholders.
Although lean manufacturing has always been around, it is gaining popularity in recent years because of a renewed interest for the economy after 2008's global financial crisis. Many companies have adopted lean manufacturing methods to increase their marketability. Economists think that lean manufacturing is a crucial factor in economic recovery.
Lean manufacturing is now becoming a common practice in the automotive industry, with many benefits. These include higher customer satisfaction, lower inventory levels, lower operating expenses, greater productivity, and improved overall safety.
You can apply Lean Manufacturing to virtually any aspect of your organization. Because it makes sure that all value chains are efficient and effectively managed, Lean Manufacturing is particularly helpful for organizations.
There are three main types of lean manufacturing:
-
Just-in Time Manufacturing: This lean manufacturing method is commonly called "pull systems." JIT means that components are assembled at the time of use and not manufactured in advance. This approach aims to reduce lead times, increase the availability of parts, and reduce inventory.
-
Zero Defects Manufacturing: ZDM ensures that no defective units leave the manufacturing plant. If a part is required to be repaired on the assembly line, it should not be scrapped. This also applies to finished products that need minor repairs before being shipped.
-
Continuous Improvement: Continuous Improvement aims to improve efficiency by continually identifying problems and making adjustments to eliminate or minimize waste. It involves continuous improvement of processes, people, and tools.