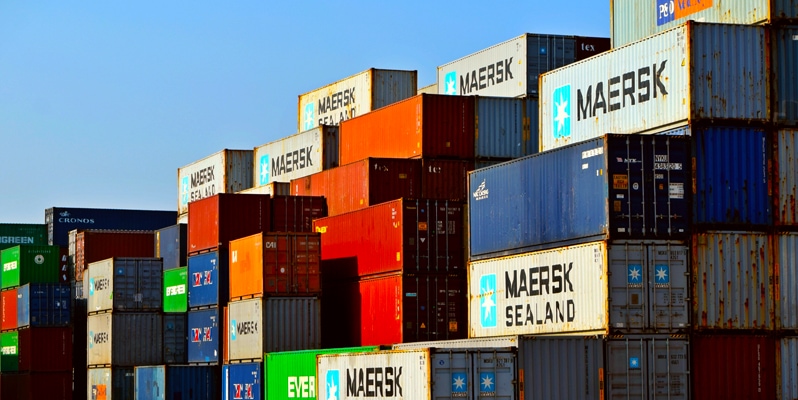
A blue collar job generally refers to manual labor. These jobs could be in manufacturing, agriculture, healthcare, hospitality or construction. While some jobs may require some level of skill (e.g., plumbers or electricians), others may not. Blue collar jobs offer great career opportunities and decent salaries.
The Fourth Industrial Revolution changes the employment market for manual workers. This revolution encompasses artificial intelligence, robotics and machine learning. For companies to succeed, it will require a skilled workforce. It will also require firms to shift away from transactional relationships, and toward more enduring ones.
As a result, companies are forced to hire workers from outside of the United States. These workers might be hired to make per-item payment in some cases. Others could be paid by a project. In any case, the rise in demand for blue collar jobs is encouraging.
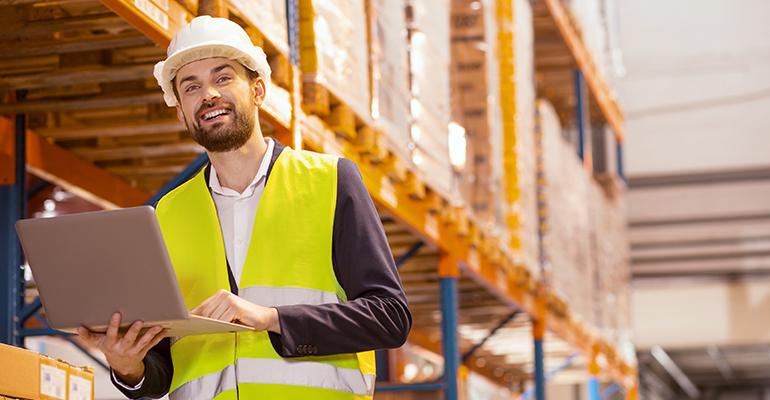
These jobs involve some manual labor, but they are better than white collar positions. Companies are willing to invest in their employees' training because these jobs can provide good income. These jobs include signal and track switch operators, electrical and electronic repairers and nuclear power reactor operator. These jobs can be done with a high school diploma. Others require additional training.
The availability of blue collar jobs is also higher than that of white collar positions. The majority of Indian workforce is made up of blue collar workers. India has approximately 210 million employees in the agriculture sector and 290 millions in the nonagricultural. Blue collar workers are in high demand.
Companies will also be able to manage their blue-collar employees differently thanks to the Fourth Industrial Revolution. Companies are moving away from transactional relationships to build lasting relationships, and replacing manual jobs by digital ones. Firms can build stronger relationships with their employees and increase productivity by prioritizing employee needs.
Although blue collar workers are highly in demand, they have to face competing realities. They might be worried about the stability and retirement of their jobs. Blue collar workers have a tendency to be optimistic about their lives, despite any worries. In fact, the percentage of blue-collar workers saving for retirement is growing. Additionally, blue collar jobs will likely increase in popularity as the economy improves.
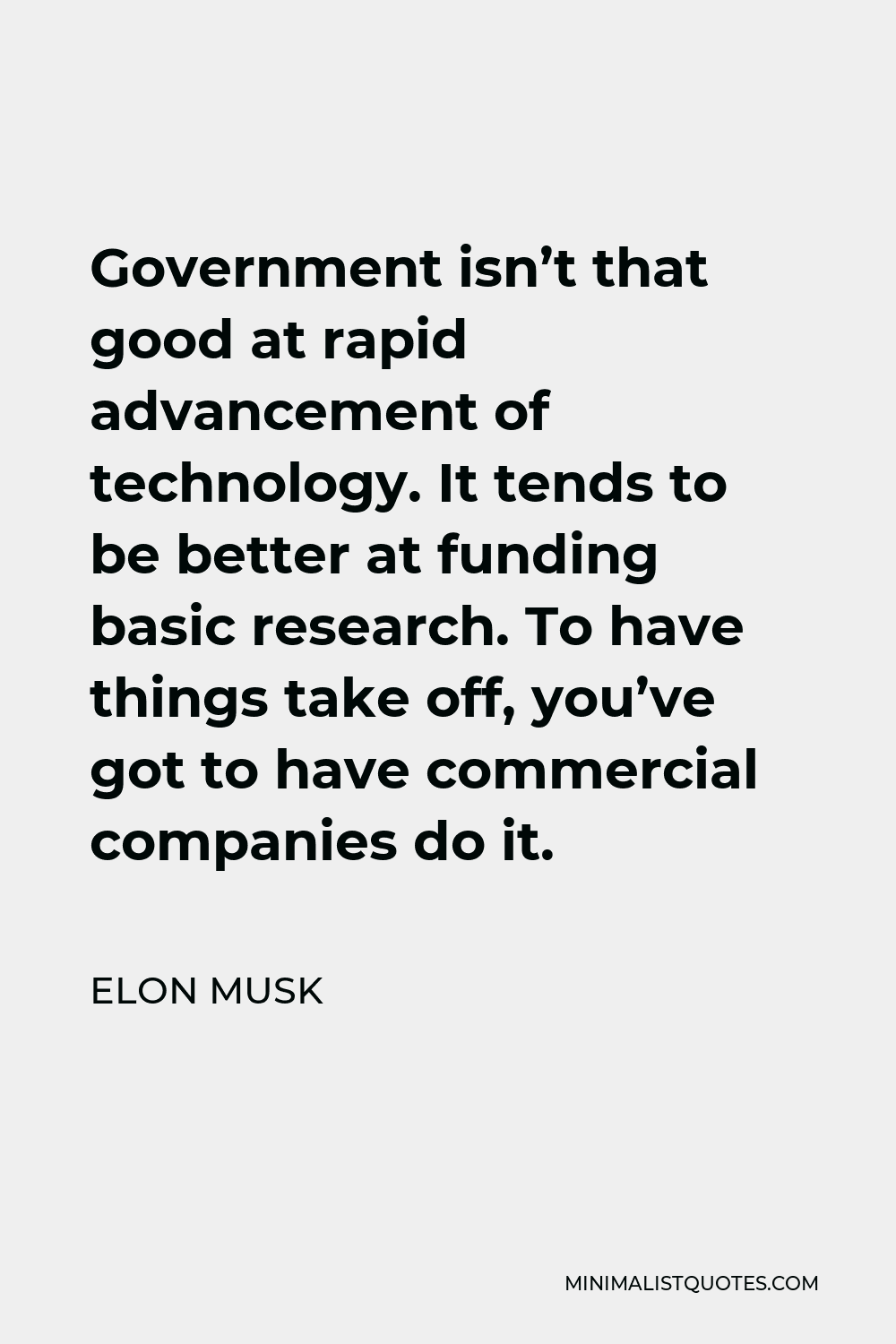
These jobs are also not threatened by automation. The Association for Manufacturing Technology actually found that for every job replaced by technology, five new jobs are created. The biggest salary increase last year went to signal and track switch repairers, who earned $76,210 on average.
In addition to being more lucrative, blue collar positions are also becoming more popular. Blue collar jobs often earn well above the average national wage, which makes them a desirable option for those who are looking for a job that pays well. In addition, many blue collar jobs require a high degree of problem-solving skills, and are more than likely to provide good career growth.
FAQ
How does a production planner differ from a project manager?
The main difference between a production planner and a project manager is that a project manager is usually the person who plans and organizes the entire project, whereas a production planner is mainly involved in the planning stage of the project.
What is the importance of automation in manufacturing?
Not only are service providers and manufacturers important, but so is automation. It enables them to provide services faster and more efficiently. In addition, it helps them reduce costs by reducing human errors and improving productivity.
What is the job of a production plan?
A production planner ensures all aspects of the project are delivered on time, within budget, and within scope. They ensure that the product or service is of high quality and meets client requirements.
Statistics
- Job #1 is delivering the ordered product according to specifications: color, size, brand, and quantity. (netsuite.com)
- In 2021, an estimated 12.1 million Americans work in the manufacturing sector.6 (investopedia.com)
- Many factories witnessed a 30% increase in output due to the shift to electric motors. (en.wikipedia.org)
- [54][55] These are the top 50 countries by the total value of manufacturing output in US dollars for its noted year according to World Bank.[56] (en.wikipedia.org)
- (2:04) MTO is a production technique wherein products are customized according to customer specifications, and production only starts after an order is received. (oracle.com)
External Links
How To
Six Sigma and Manufacturing
Six Sigma refers to "the application and control of statistical processes (SPC) techniques in order to achieve continuous improvement." Motorola's Quality Improvement Department, Tokyo, Japan, developed it in 1986. Six Sigma's main goal is to improve process quality by standardizing processes and eliminating defects. This method has been adopted by many companies in recent years as they believe there are no perfect products or services. Six Sigma seeks to reduce variation between the mean production value. This means that you can take a sample from your product and then compare its performance to the average to find out how often the process differs from the norm. If you notice a large deviation, then it is time to fix it.
Understanding the nature of variability in your business is the first step to Six Sigma. Once you've understood that, you'll want to identify sources of variation. It is important to identify whether the variations are random or systemic. Random variations are caused when people make mistakes. While systematic variations are caused outside of the process, they can occur. These are, for instance, random variations that occur when widgets are made and some fall off the production line. If however, you notice that each time you assemble a widget it falls apart in exactly the same spot, that is a problem.
After identifying the problem areas, you will need to devise solutions. The solution could involve changing how you do things, or redesigning your entire process. Test them again once you've implemented the changes. If they didn't work, then you'll need to go back to the drawing board and come up with another plan.