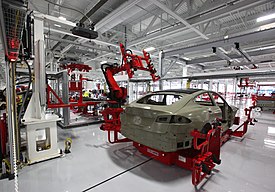
A nuclear engineer can easily make anywhere from six to seven figure salaries. Apart from their usual duties, nuclear engineers can also oversee construction of nuclear facilities or supervise work in closed areas. They may have to defend their work in public. A variety of reasons are why nuclear engineers are in high demand. They are highly sought after for their leadership abilities and technical expertise. The salary for this profession depends on a number of factors, including experience, education, and location.
A bachelor's degree earns you an average salary as a nuclear engineering engineer
The federal government is by far the largest employer for nuclear engineers. Other major employers include engineering, scientific and research and developmental services, and the manufacturing sector. The increased demand for nuclear engineers will drive growth in the engineering and research & development sectors over the next 10 years, due to the growing interest in nuclear power. While there are not currently any commercial nuclear power plants in operation, this technology could allow them to increase their production.
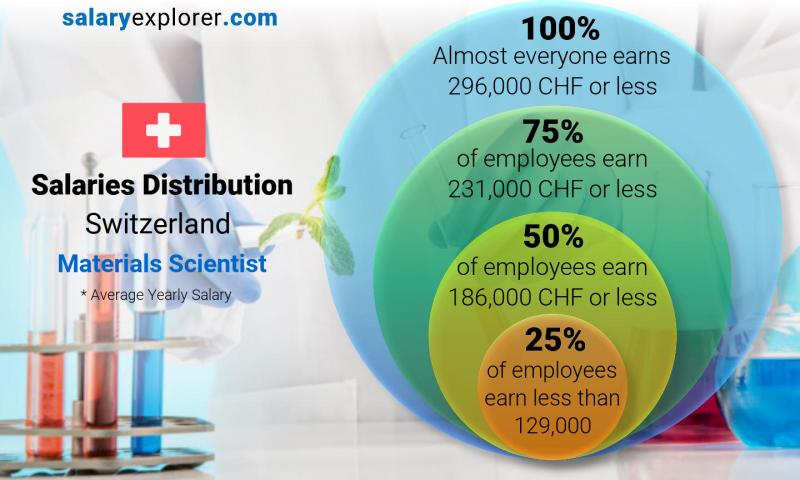
You must hold a bachelor's in engineering or another related field to be able to become a nuclear engineer. A bachelor's degree is required to get a job as an entry-level nuclear engineer. If you have a master's, it will lead to a more rewarding career. Some positions may require state licensure, as well. For the first few years of their careers, nuclear engineers work under an experienced engineer. This allows them to gain experience and responsibility.
Average salary of a nuclear engineer who has a master's degree
Consider the expected salary for a career in nuclear engineering. You can work at any nuclear power facility, but it is more common to work as an office worker. A career in nuclear power generation requires that you work in power plants. You will be working alongside electrical and mechanical engineers. They will need to integrate systems designed by these other professionals. Nuclear engineers are typically full-time workers and may even work more than their counterparts.
The average salary for a nuclear engineer with a Master's degree is $124,272 per year, which is considerably more than the median wage for all US workers. It is important to remember that salaries vary from one position to the next. An average salary for nuclear engineers is $185,550. The average starting wage is $74,800 and is among the highest paid in the field.
Starting salary for a nuclear engineer
To be a successful career in nuclear engineering you will need to understand the average starting pay. This career field requires a strong university record and several years of related work experience. Nuclear engineers can expect steady career growth. However, they are also able to move into a similar field if needed. Nuclear engineers work in various fields including manufacturing, space exploration and medical applications.
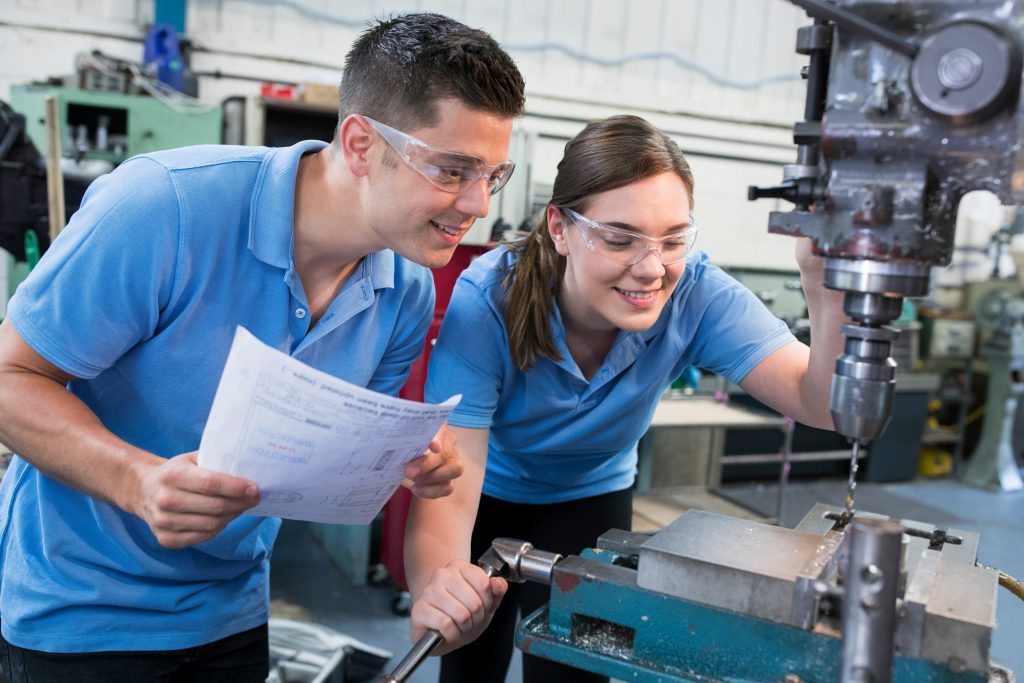
While nuclear engineers can work in a number of different industries, the federal government is their largest employer. The Office for Nuclear Regulation oversees the operations of these facilities. Other employers in the field include construction, manufacturing, and scientific research and development. As nuclear power grows, job opportunities for nuclear engineers should increase. However, there will be a shortage of graduates which will impact the prospects of finding work. Although the federal government is not currently hiring nuclear engineers, many companies are.
FAQ
What are the 7 Rs of logistics.
The acronym "7R's" of Logistics stands for seven principles that underpin logistics management. It was published in 2004 by the International Association of Business Logisticians as part of their "Seven Principles of Logistics Management" series.
The acronym is made up of the following letters:
-
Responsible - to ensure that all actions are within the legal requirements and are not detrimental to others.
-
Reliable - You can have confidence that you will fulfill your promises.
-
Be responsible - Use resources efficiently and avoid wasting them.
-
Realistic - Consider all aspects of operations, including environmental impact and cost effectiveness.
-
Respectful - show respect and treat others fairly and fairly
-
Resourceful - look for opportunities to save money and increase productivity.
-
Recognizable provides value-added products and services to customers
What skills does a production planner need?
You must be flexible and organized to become a productive production planner. Communication skills are essential to ensure that you can communicate effectively with clients, colleagues, and customers.
How does manufacturing avoid bottlenecks in production?
The key to avoiding bottlenecks in production is to keep all processes running smoothly throughout the entire production cycle, from the time you receive an order until the time when the product ships.
This includes both quality control and capacity planning.
Continuous improvement techniques like Six Sigma are the best way to achieve this.
Six Sigma can be used to improve the quality and decrease waste in all areas of your company.
It seeks to eliminate variation and create consistency in your work.
Statistics
- You can multiply the result by 100 to get the total percent of monthly overhead. (investopedia.com)
- It's estimated that 10.8% of the U.S. GDP in 2020 was contributed to manufacturing. (investopedia.com)
- Many factories witnessed a 30% increase in output due to the shift to electric motors. (en.wikipedia.org)
- [54][55] These are the top 50 countries by the total value of manufacturing output in US dollars for its noted year according to World Bank.[56] (en.wikipedia.org)
- In the United States, for example, manufacturing makes up 15% of the economic output. (twi-global.com)
External Links
How To
How to use Lean Manufacturing in the production of goods
Lean manufacturing is a management system that aims at increasing efficiency and reducing waste. It was developed in Japan during the 1970s and 1980s by Taiichi Ohno, who received the Toyota Production System (TPS) award from TPS founder Kanji Toyoda. Michael L. Watkins published the first book on lean manufacturing in 1990.
Lean manufacturing, often described as a set and practice of principles, is aimed at improving the quality, speed, cost, and efficiency of products, services, and other activities. It emphasizes reducing defects and eliminating waste throughout the value chain. Lean manufacturing can be described as just-in–time (JIT), total productive maintenance, zero defect (TPM), or even 5S. Lean manufacturing emphasizes reducing non-value-added activities like inspection, rework and waiting.
Lean manufacturing can help companies improve their product quality and reduce costs. Additionally, it helps them achieve their goals more quickly and reduces employee turnover. Lean manufacturing has been deemed one of the best ways to manage the entire value-chain, including customers, distributors as well retailers and employees. Lean manufacturing can be found in many industries. For example, Toyota's philosophy underpins its success in automobiles, electronics, appliances, healthcare, chemical engineering, aerospace, paper, food, etc.
Five basic principles of Lean Manufacturing are included in lean manufacturing
-
Define value - Find out what your business contributes to society, and what makes it different from other competitors.
-
Reduce Waste - Remove any activity which doesn't add value to your supply chain.
-
Create Flow: Ensure that the work process flows without interruptions.
-
Standardize and Simplify – Make processes as consistent, repeatable, and as simple as possible.
-
Building Relationships – Establish personal relationships with both external and internal stakeholders.
Although lean manufacturing has always been around, it is gaining popularity in recent years because of a renewed interest for the economy after 2008's global financial crisis. Many businesses are now using lean manufacturing to improve their competitiveness. Some economists even believe that lean manufacturing can be a key factor in economic recovery.
Lean manufacturing has many benefits in the automotive sector. These include higher customer satisfaction levels, reduced inventory levels as well as lower operating costs.
It can be applied to any aspect of an organisation. However, it is particularly useful when applied to the production side of an organization because it ensures that all steps in the value chain are efficient and effective.
There are three types of lean manufacturing.
-
Just-in Time Manufacturing, (JIT): This kind of lean manufacturing is also commonly known as "pull-systems." JIT is a process in which components can be assembled at the point they are needed, instead of being made ahead of time. This approach aims to reduce lead times, increase the availability of parts, and reduce inventory.
-
Zero Defects Manufacturing (ZDM),: ZDM is a system that ensures no defective units are left the manufacturing facility. You should repair any part that needs to be repaired during an assembly line. This also applies to finished products that need minor repairs before being shipped.
-
Continuous Improvement (CI: Continuous improvement aims to increase the efficiency of operations by constantly identifying and making improvements to reduce or eliminate waste. It involves continuous improvement of processes, people, and tools.