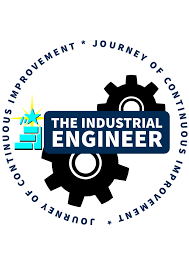
There are many reasons supply chain disruptions could occur. Examples include natural disasters as well as product recalls or transportation delays. These disruptions can lead to price increases or margin cuts. To continue production, some companies may need a change in their sourcing strategies. Companies will often need to reevaluate their supply chains, diversify production, and audit current inventories in order to be prepared for disruptions.
Supply chain disruptions have been experienced in many industries including electronics, pharmaceuticals, and transportation. Some disruptions are caused by internal issues at companies, while others were caused by a global event. A pandemic, for example, caused widespread disruptions in the health of many countries. It also had an adverse impact on retail. The pandemic forced governments into adopting policies to stop the spread of the disease.
A pandemic could affect the workforce, distribution and manufacturing processes of a company. It can impact the production of critical products. Companies will have to re-evaluate their production and supply chains. Depending upon the extent of the disruption, the impact may last for several weeks or even months. Businesses will need a re-evaluation of their inventory in the event of a pandemic. Capital can be reallocated if needed.
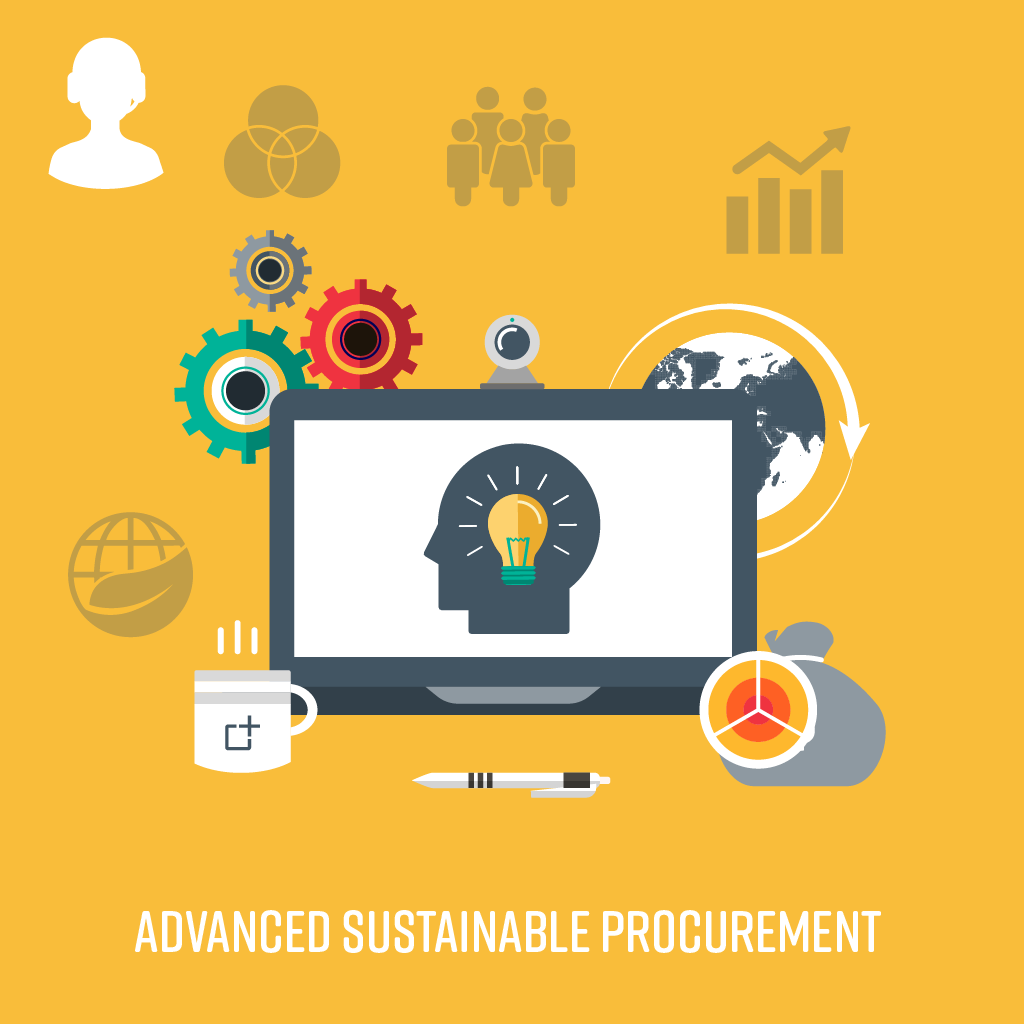
Disruption may occur at any stage in the supply chain and can impact both supply or demand. In most cases, disruptions to the supply chain will impact the demand more than the supply side. If the supply side of an epidemic is disrupted, however, the ripple effect will affect the whole economy.
Supply chain disruptions can have major consequences for a company and are often hard to predict. It's easy to recognize seasonal fluctuations, but more difficult is predicting a shift in consumer behavior. One of the best ways to mitigate these risks is to rely on a predictive analytics tool to identify potential problems.
A labor shortage is another common reason for supply chain disruption. Businesses can lose productivity when they cannot obtain parts and equipment from reliable suppliers. Similarly, a machine breakdown can disrupt the entire operation.
Natural disasters and market fluctuations are the main causes of supply chain disruptions. Natural disasters, which are expensive, can cause disruptions in the global supply chain. Another cause of disruption in supply chains is a power outage or telecommunications blackout. Additionally, businesses may need to store large quantities to protect themselves.
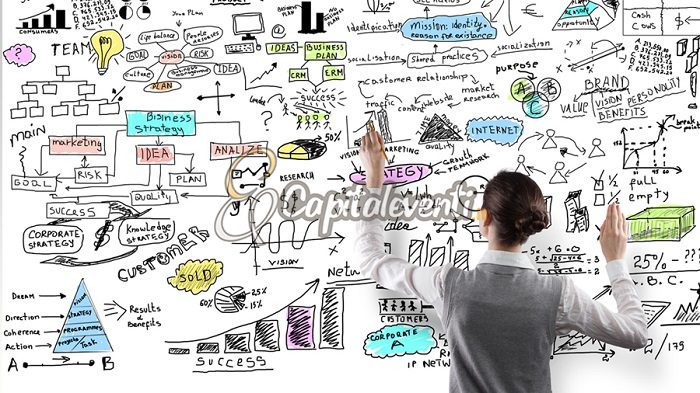
As a rule, supply chain disruptions are relatively small. Companies will need take action if they spot a disruption. The majority of companies will need to do so within a reasonable timeframe. It's important to recognize problems early in order to avoid conflict.
Ernest & Young LLP surveyed 72 percent of companies that experienced disruptions in the past year. 57 per cent reported adverse effects. Many of these problems can be addressed quickly, while others will require a more strategic approach.
FAQ
What are the products of logistics?
Logistics is the process of moving goods from one point to another.
They cover all aspects of transportation, such as packing, loading, transporting and unloading.
Logisticians ensure that the product is delivered to the correct place, at the right time, and under safe conditions. They help companies manage their supply chain efficiency by providing information on demand forecasts, stock levels, production schedules, and availability of raw materials.
They monitor shipments in transit, ensure quality standards, manage inventories, replenish orders, coordinate with suppliers and other vendors, and offer support services for sales, marketing, and customer service.
What is the difference between manufacturing and logistics
Manufacturing refers to the process of making goods using raw materials and machines. Logistics manages all aspects of the supply chain, including procurement, production planning and distribution, inventory control, transportation, customer service, and transport. As a broad term, manufacturing and logistics often refer to both the creation and delivery of products.
What does "warehouse" mean?
A warehouse or storage facility is where goods are stored before they are sold. It can be an indoor space or an outdoor area. Sometimes, it can be both an indoor and outdoor space.
Statistics
- You can multiply the result by 100 to get the total percent of monthly overhead. (investopedia.com)
- Many factories witnessed a 30% increase in output due to the shift to electric motors. (en.wikipedia.org)
- According to the United Nations Industrial Development Organization (UNIDO), China is the top manufacturer worldwide by 2019 output, producing 28.7% of the total global manufacturing output, followed by the United States, Japan, Germany, and India.[52][53] (en.wikipedia.org)
- In the United States, for example, manufacturing makes up 15% of the economic output. (twi-global.com)
- It's estimated that 10.8% of the U.S. GDP in 2020 was contributed to manufacturing. (investopedia.com)
External Links
How To
How to use lean manufacturing in the production of goods
Lean manufacturing refers to a method of managing that seeks to improve efficiency and decrease waste. It was created in Japan by Taiichi Ohno during the 1970s and 80s. He received the Toyota Production System award (TPS), from Kanji Toyoda, founder of TPS. Michael L. Watkins published the "The Machine That Changed the World", the first book about lean manufacturing. It was published in 1990.
Lean manufacturing can be described as a set or principles that are used to improve quality, speed and cost of products or services. It emphasizes eliminating waste and defects throughout the value stream. Lean manufacturing can be described as just-in–time (JIT), total productive maintenance, zero defect (TPM), or even 5S. Lean manufacturing focuses on eliminating non-value-added activities such as rework, inspection, and waiting.
Lean manufacturing not only improves product quality but also reduces costs. Companies can also achieve their goals faster by reducing employee turnover. Lean manufacturing is a great way to manage the entire value chain including customers, suppliers, distributors and retailers as well as employees. Lean manufacturing is widely used in many industries. Toyota's philosophy has been a key driver of success in many industries, including automobiles and electronics.
Lean manufacturing includes five basic principles:
-
Define Value - Determine the value that your business brings to society. Also, identify what sets you apart from your competitors.
-
Reduce waste - Get rid of any activity that does not add value to the supply chain.
-
Create Flow - Ensure work moves smoothly through the process without interruption.
-
Standardize & simplify - Make processes consistent and repeatable.
-
Build Relationships - Establish personal relationships with both internal and external stakeholders.
Although lean manufacturing has always been around, it is gaining popularity in recent years because of a renewed interest for the economy after 2008's global financial crisis. To increase their competitiveness, many businesses have turned to lean manufacturing. Some economists even believe that lean manufacturing can be a key factor in economic recovery.
With many benefits, lean manufacturing is becoming more common in the automotive industry. These include better customer satisfaction and lower inventory levels. They also result in lower operating costs.
The principles of lean manufacturing can be applied in almost any area of an organization. This is because it ensures efficiency and effectiveness in all stages of the value chain.
There are three types of lean manufacturing.
-
Just-in-Time Manufacturing: Also known as "pull systems", this type of lean manufacturing uses just-in-time manufacturing (JIT). JIT stands for a system where components are assembled on the spot rather than being made in advance. This strategy aims to decrease lead times, increase availability of parts and reduce inventory.
-
Zero Defects Manufacturing: ZDM ensures that no defective units leave the manufacturing plant. Repairing a part that is damaged during assembly should be done, not scrapping. This is also true for finished products that require minor repairs before shipping.
-
Continuous Improvement (CI),: Continuous improvement aims improve the efficiency and effectiveness of operations by continuously identifying issues and making changes to reduce waste. Continuous Improvement (CI) involves continuous improvement in processes, people, tools, and infrastructure.