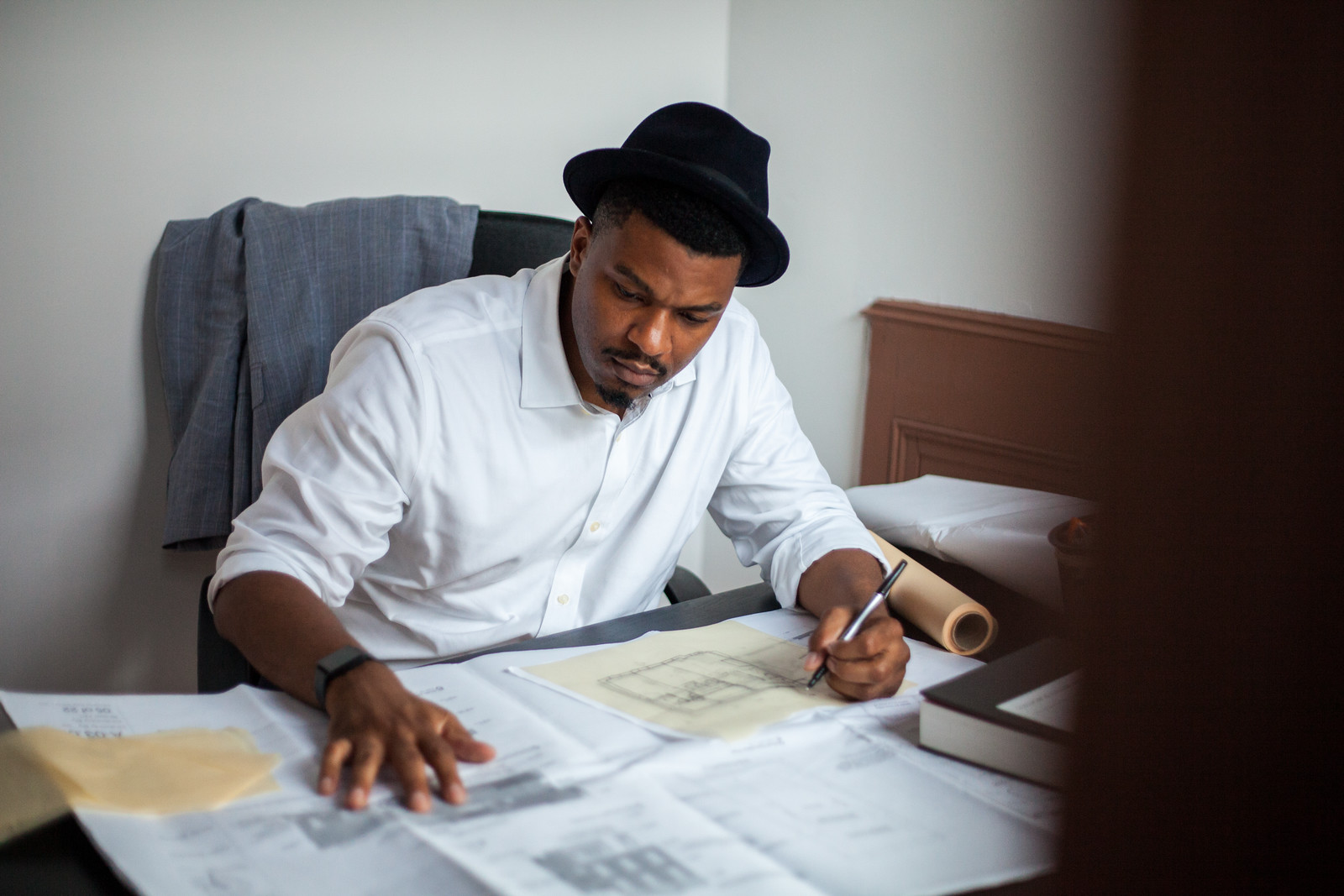
If you want to ensure your product is profitable, it is important to factor in manufacturing costs. For example, if you want to sell wooden tabletops furniture, you might need to purchase wood glue and other materials. You need to find a reliable supplier of the best quality raw material so that your end product will last. You could end up with a damaged item or lost revenue if you don't use the best quality raw materials.
The most effective way to understand manufacturing cost is to break it down into three main categories. These costs have an impact on the final price of your product. The unit cost, which represents the cost of producing an item, is one of the most important elements of a manufacturing cost. It is a good place for you to start but can be tricky to define.
A good rule of thumb when trying to determine the most cost-effective manufacturing option for your company is the units per hour or unit/unit ratio. By calculating how many hours each project takes, you can determine the average cost to make 5,000 wooden furniture tables.
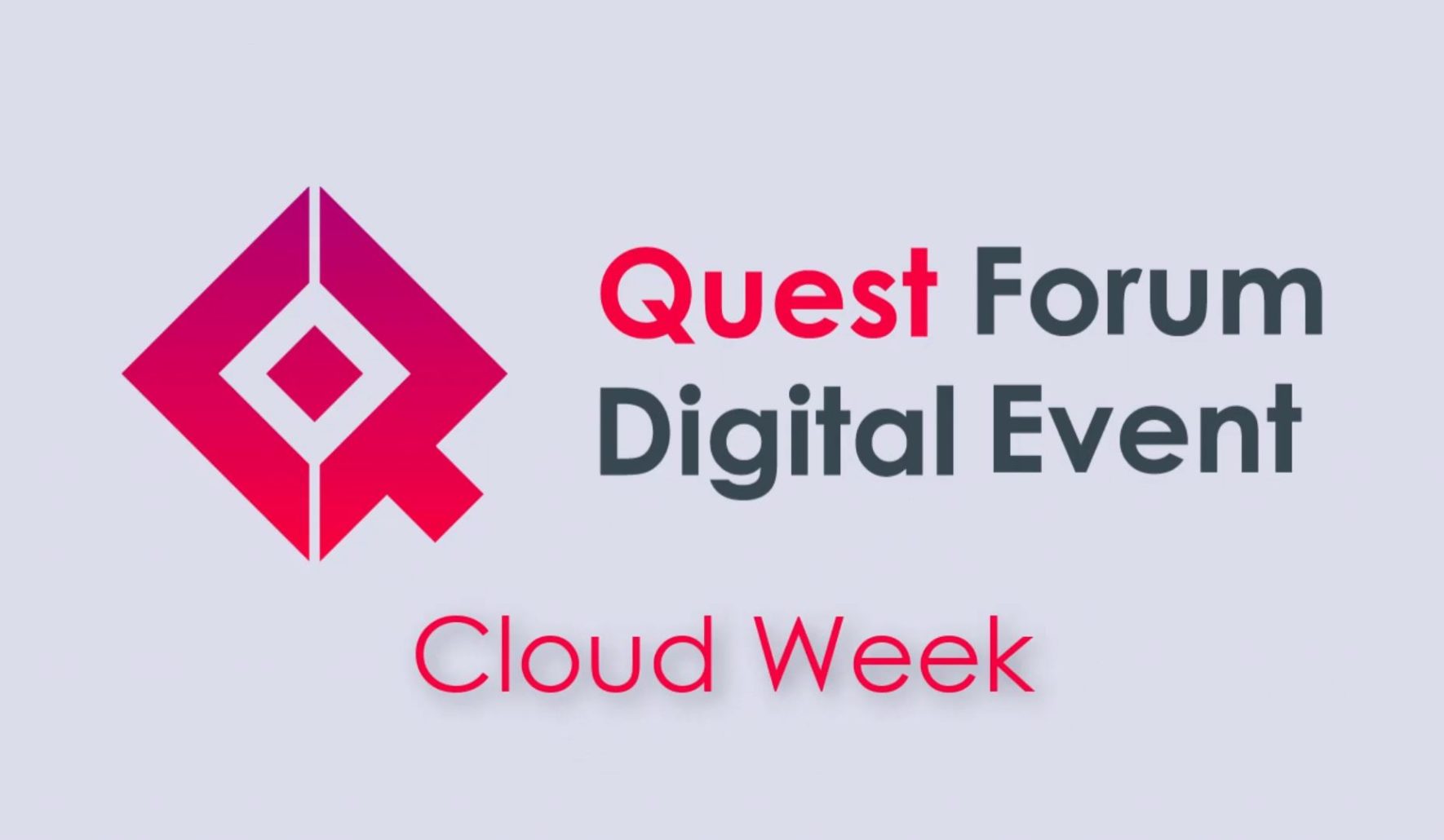
You will need to budget for general and administrative expenses, in addition to direct labor. These can include advertising costs, office supplies, rent, and sales commissions. Compliance with regulatory requirements will require you to spend substantial amounts. Online inventory control software can be used to track and forecast production.
Direct labor costs are the wages paid to workers in a factory, and includes employees engaged in the actual preparation of the goods for manufacturing. These costs may include staff such as maintenance, sanitation, and bookkeepers. In general, direct labor costs about $150 an hour.
Indirect expenses are part and parcel of manufacturing. These costs include utility bills as well as equipment maintenance. Calculating the unit-per hour will require you to factor in the cost of material preparation, assembly, and delivery costs. You can calculate the cost of manufacturing and get an estimate of the overhead costs for the following fiscal year by creating a manufacturing overhead account.
Other items to consider when calculating the manufacturing cost are the direct and indirect materials used to manufacture a particular product. The materials used to manufacture a product include thread, wood, and cotton. Low quality materials can result in inferior products. Food manufacturers in some parts of the world will need to test their products to ensure that they are safe for consumption.
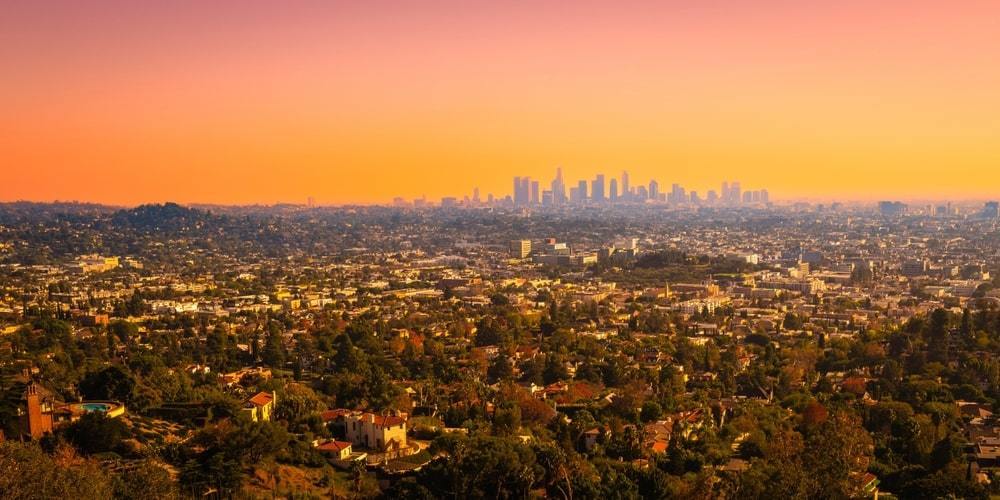
You can determine whether to start manufacturing a new product by knowing the unit-per-unit cost and the manufacturing cost. It's also a good idea to know how much to charge for your products so that you can increase the profitability of your business.
FAQ
What are the 4 types manufacturing?
Manufacturing is the process by which raw materials are transformed into useful products through machines and processes. It can involve many activities like designing, manufacturing, testing packaging, shipping, selling and servicing.
Are there any Manufacturing Processes that we should know before we can learn about Logistics?
No. No. It is important to know about the manufacturing processes in order to understand how logistics works.
What does it mean to warehouse?
A warehouse, or storage facility, is where goods are stored prior to being sold. It can be indoors or out. In some cases it could be both indoors and outdoors.
What are the products and services of logistics?
Logistics refers to the movement of goods from one place to another.
They encompass all aspects transport, including packaging and loading, transporting, storage, unloading.
Logisticians ensure the product reaches its destination in the most efficient manner. They provide information on demand forecasts as well stock levels, production schedules and availability of raw material.
They monitor shipments in transit, ensure quality standards, manage inventories, replenish orders, coordinate with suppliers and other vendors, and offer support services for sales, marketing, and customer service.
Is automation necessary in manufacturing?
Automation is essential for both manufacturers and service providers. They can provide services more quickly and efficiently thanks to automation. It reduces human errors and improves productivity, which in turn helps them lower their costs.
What are my options for learning more about manufacturing
The best way to learn about manufacturing is through hands-on experience. But if that is not possible you can always read books and watch educational videos.
Statistics
- Many factories witnessed a 30% increase in output due to the shift to electric motors. (en.wikipedia.org)
- According to a Statista study, U.S. businesses spent $1.63 trillion on logistics in 2019, moving goods from origin to end user through various supply chain network segments. (netsuite.com)
- (2:04) MTO is a production technique wherein products are customized according to customer specifications, and production only starts after an order is received. (oracle.com)
- According to the United Nations Industrial Development Organization (UNIDO), China is the top manufacturer worldwide by 2019 output, producing 28.7% of the total global manufacturing output, followed by the United States, Japan, Germany, and India.[52][53] (en.wikipedia.org)
- It's estimated that 10.8% of the U.S. GDP in 2020 was contributed to manufacturing. (investopedia.com)
External Links
How To
How to Use the Just-In-Time Method in Production
Just-in-time is a way to cut costs and increase efficiency in business processes. It's the process of obtaining the right amount and timing of resources when you need them. This means that only what you use is charged to your account. Frederick Taylor, a 1900s foreman, first coined the term. Taylor observed that overtime was paid to workers if they were late in working. He decided to ensure workers have enough time to do their jobs before starting work to improve productivity.
The idea behind JIT is that you should plan ahead and have everything ready so you don't waste money. Also, you should look at the whole project from start-to-finish and make sure you have the resources necessary to address any issues. You will have the resources and people to solve any problems you anticipate. This will prevent you from spending extra money on unnecessary things.
There are many JIT methods.
-
Demand-driven: This is a type of JIT where you order the parts/materials needed for your project regularly. This will allow to track how much material has been used up. You'll also be able to estimate how long it will take to produce more.
-
Inventory-based: This type allows you to stock the materials needed for your projects ahead of time. This allows you to predict how much you can expect to sell.
-
Project-driven: This approach involves setting aside sufficient funds to cover your project's costs. When you know how much you need, you'll purchase the appropriate amount of materials.
-
Resource-based JIT: This type of JIT is most commonly used. Here, you allocate certain resources based on demand. For example, if there is a lot of work coming in, you will have more people assigned to them. If you don’t have many orders you will assign less people to the work.
-
Cost-based: This approach is very similar to resource-based. However, you don't just care about the number of people you have; you also need to consider how much each person will cost.
-
Price-based: This is similar to cost-based but instead of looking at individual workers' salaries, you look at the total company price.
-
Material-based - This is a variant of cost-based. But instead of looking at the total company cost, you focus on how much raw material you spend per year.
-
Time-based: This is another variation of resource-based JIT. Instead of worrying about how much each worker costs, you can focus on how long the project takes.
-
Quality-based JIT - This is another form of resource-based JIT. Instead of thinking about the cost of each employee or the time it takes to produce something, you focus on how good your product quality.
-
Value-based JIT: One of the most recent forms of JIT. In this scenario, you're not concerned about how products perform or whether customers expect them to meet their expectations. Instead, your goal is to add value to the market.
-
Stock-based: This inventory-based approach focuses on how many items are being produced at any one time. It's useful when you want maximum production and minimal inventory.
-
Just-in time (JIT), planning: This is a combination JIT/supply chain management. This refers to the scheduling of the delivery of components as soon after they are ordered. It's important because it reduces lead times and increases throughput.