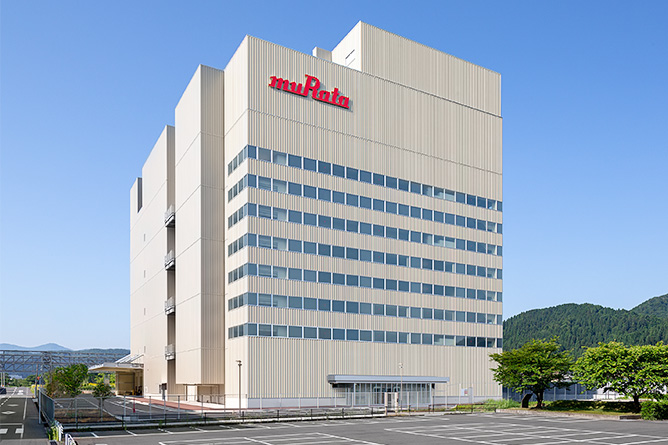
Despite the many benefits that lean manufacturing brings, companies often face difficulties in implementing this strategy. It is crucial that companies create a comprehensive plan to overcome any obstacles. Companies who have implemented Lean found three main problems that hamper the success rate of the initiative.
Whatever the company's size, it is essential that they are committed to lean manufacturing. There is no one way to tell if a company is committed to lean manufacturing, but it is crucial that the management educates employees about the changes in corporate culture.
It is crucial to ensure resources are correctly allocated. Many public institutions have found that they are spending their allocated budgets on things that aren't necessary. Reports also indicate that some managers purchase equipment that isn't necessary to make use of the budget. This can lead to operational bottlenecks which can result in inefficient implementations of lean manufacturing.
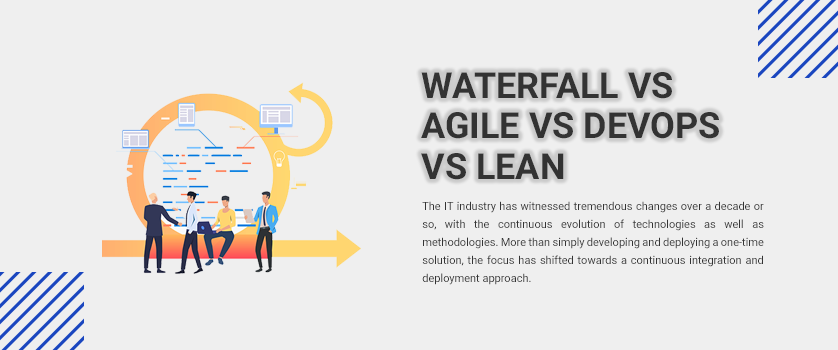
Resistance to cultural change is one of the greatest challenges when implementing lean manufacturing. Many employees, especially those who have been with the company a long time, don't like change. Some of these employees may be reluctant to accept change, even if the majority supports it. Management must communicate the advantages of the program and the reasons for the change in order to break the resistance.
Another significant challenge is the lack of a strategic transformation plan. Even though many companies transform their business operations simultaneously, it is important that you have a long-term plan. This strategy allows companies mentor future leaders and keeps them competitive in the face technology advances. It also helps to improve operational efficiency. It can also help identify and resolve operational bottlenecks as well as identify growth opportunities.
It is vital to train workers to overcome resistance. A proper training program helps workers understand what their responsibilities are and what they can expect. This training helps workers acquire multi skills that can be used to help them work independently. Training also helps workers develop problem solving skills, which helps them sustain Lean through improvements in performance.
To overcome resistance, management needs to engage with workers frequently. Managers may put pressure on workers to follow instructions, but managers need to be open and honest with workers about why the change is needed. Managers have been accused of giving incorrect instructions to employees, leading sometimes to ineffective implementation.
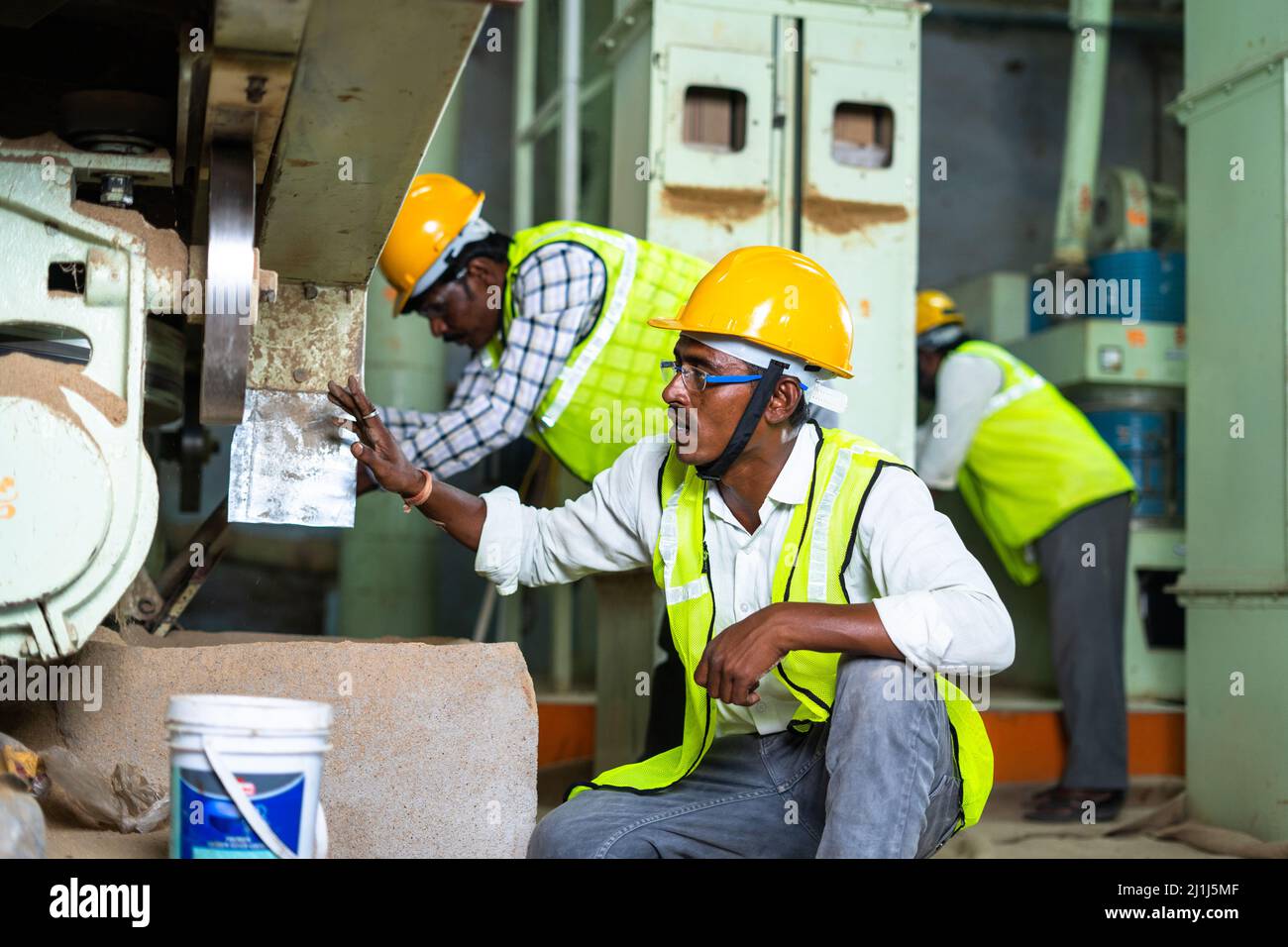
Managers need to be present at work, no matter how large or small the company. They can identify the areas where improvements can be made. Managers should also be able to create structured training modules for their staff and introduce new digital work tools to them. These tools, such as 5S, improve visual management.
A clear vision is essential for lean manufacturing implementation. This vision should contain information about employees' responsibilities, the schedule for lean implementation, and how to measure success.
FAQ
How can manufacturing reduce production bottlenecks?
To avoid production bottlenecks, ensure that all processes run smoothly from the moment you receive your order to the time the product ships.
This includes both planning for capacity and quality control.
Continuous improvement techniques such Six Sigma are the best method to accomplish this.
Six Sigma can be used to improve the quality and decrease waste in all areas of your company.
It seeks to eliminate variation and create consistency in your work.
What can I do to learn more about manufacturing?
Experience is the best way for you to learn about manufacturing. You can also read educational videos or take classes if this isn't possible.
What does "warehouse" mean?
Warehouses and storage facilities are where goods are kept before being sold. It can be either an indoor or outdoor space. In some cases, it may be a combination of both.
What makes a production planner different from a project manger?
The major difference between a Production Planner and a Project Manager is that a Project Manager is often the person responsible for organizing and planning the entire project. While a Production Planner is involved mainly in the planning stage,
What are manufacturing and logistic?
Manufacturing is the production of goods using raw materials. Logistics covers all aspects involved in managing supply chains, including procurement and production planning. Manufacturing and logistics are often considered together as a broader term that encompasses both the process of creating products and delivering them to customers.
Statistics
- According to the United Nations Industrial Development Organization (UNIDO), China is the top manufacturer worldwide by 2019 output, producing 28.7% of the total global manufacturing output, followed by the United States, Japan, Germany, and India.[52][53] (en.wikipedia.org)
- [54][55] These are the top 50 countries by the total value of manufacturing output in US dollars for its noted year according to World Bank.[56] (en.wikipedia.org)
- Many factories witnessed a 30% increase in output due to the shift to electric motors. (en.wikipedia.org)
- Job #1 is delivering the ordered product according to specifications: color, size, brand, and quantity. (netsuite.com)
- According to a Statista study, U.S. businesses spent $1.63 trillion on logistics in 2019, moving goods from origin to end user through various supply chain network segments. (netsuite.com)
External Links
How To
How to use Lean Manufacturing in the production of goods
Lean manufacturing (or lean manufacturing) is a style of management that aims to increase efficiency, reduce waste and improve performance through continuous improvement. It was first developed in Japan in the 1970s/80s by Taiichi Ahno, who was awarded the Toyota Production System (TPS), award from KanjiToyoda, the founder of TPS. The first book published on lean manufacturing was titled "The Machine That Changed the World" written by Michael L. Watkins and published in 1990.
Lean manufacturing refers to a set of principles that improve the quality, speed and costs of products and services. It emphasizes the elimination of defects and waste throughout the value stream. Lean manufacturing is also known as just in time (JIT), zero defect total productive maintenance(TPM), and five-star (S). Lean manufacturing seeks to eliminate non-value added activities, such as inspection, work, waiting, and rework.
Lean manufacturing not only improves product quality but also reduces costs. Companies can also achieve their goals faster by reducing employee turnover. Lean manufacturing is considered one of the most effective ways to manage the entire value chain, including suppliers, customers, distributors, retailers, and employees. Lean manufacturing practices are widespread in many industries. Toyota's philosophy, for example, is what has enabled it to be successful in electronics, automobiles, medical devices, healthcare and chemical engineering as well as paper and food.
Five principles are the basis of lean manufacturing:
-
Define Value - Identify the value your business adds to society and what makes you different from competitors.
-
Reduce waste - Stop any activity that isn't adding value to the supply chains.
-
Create Flow – Ensure that work flows smoothly throughout the process.
-
Standardize and simplify - Make your processes as consistent as possible.
-
Develop Relationships: Establish personal relationships both with internal and external stakeholders.
Although lean manufacturing isn't a new concept in business, it has gained popularity due to renewed interest in the economy after the 2008 global financial crisis. To increase their competitiveness, many businesses have turned to lean manufacturing. Many economists believe lean manufacturing will play a major role in economic recovery.
With many benefits, lean manufacturing is becoming more common in the automotive industry. These include improved customer satisfaction, reduced inventory levels, lower operating costs, increased productivity, and better overall safety.
Any aspect of an enterprise can benefit from Lean manufacturing. Lean manufacturing is most useful in the production sector of an organisation because it ensures that each step in the value-chain is efficient and productive.
There are three main types of lean manufacturing:
-
Just-in Time Manufacturing, (JIT): This kind of lean manufacturing is also commonly known as "pull-systems." JIT is a method in which components are assembled right at the moment of use, rather than being manufactured ahead of time. This approach aims to reduce lead times, increase the availability of parts, and reduce inventory.
-
Zero Defects Manufacturing, (ZDM): ZDM is focused on ensuring that no defective products leave the manufacturing facility. It is better to repair a part than have it removed from the production line if it needs to be fixed. This also applies to finished products that need minor repairs before being shipped.
-
Continuous Improvement (CI),: Continuous improvement aims improve the efficiency and effectiveness of operations by continuously identifying issues and making changes to reduce waste. Continuous Improvement (CI) involves continuous improvement in processes, people, tools, and infrastructure.