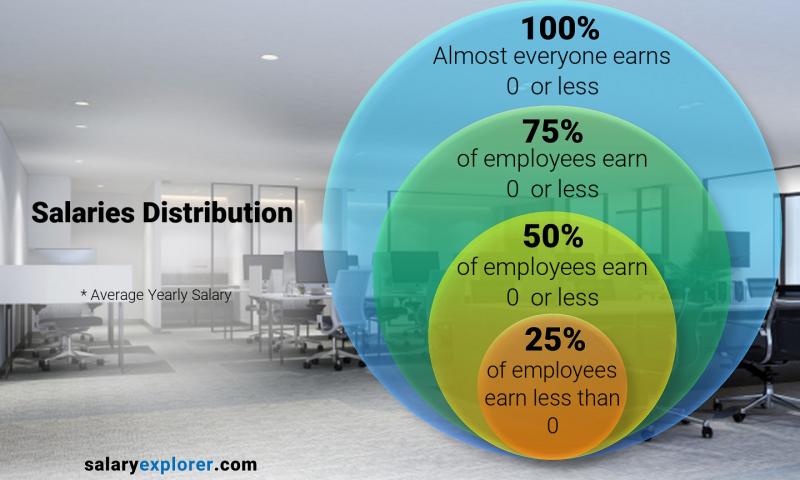
Industrial management is an engineering field where different engineering processes are integrated in order to create a management system. A industrial manager is responsible for integrating these engineering processes into one integrated management system. These are the basics of your job. These are some of the benefits and requirements to become an industrial manager. This is the right career path for you if you have the necessary qualifications and are looking to take on a challenging, rewarding job. Continue reading to learn more.
Job description
An industrial manager oversees manufacturing and the production of goods or services. This job will cover many aspects of production, but it will also include how to source raw materials or implement equipment. As computers play an increasingly important role in the coordination between different departments, suppliers, customers, and employees, industrial production managers need to be computer-literate. Industrial production managers must also be familiar with the latest production technologies as well as management practices. Managers are often involved in professional organizations and attend trade shows and industry conferences. They also take courses to become certified in their fields.
Industrial managers coordinate activities across a company's departments. They make sure that production lines run smoothly and meet customer demands in terms of quality, time and delivery. They may also supervise staffing levels or change production levels as required to minimize inventory. They may also oversee quality control programs and coordinate communication with suppliers and other departments. Majority of their responsibilities involve managing people. This involves identifying, training, motivating and motivating employees.
Education is necessary
To be qualified as an industrial manger, you will need a bachelor's degree either in management or business administration. Some employers prefer candidates with a background or education in these areas. Also, industrial managers must be computer-literate. Computers are becoming increasingly essential in the manufacturing process. They help coordinate production between departments, suppliers, clients, and other parties. For this job, you will need the necessary education and experience.
Many industrial production managers begin their careers as workers, and then move up to supervisory positions. To advance to an industrial manager position, most professionals must earn a college degree in business management. Some entry-level workers might be able to get this education while on the job or through classes sponsored by their employers. But, managers should have at least two- to five years of relevant experience to be considered for managerial positions.
Earning potential
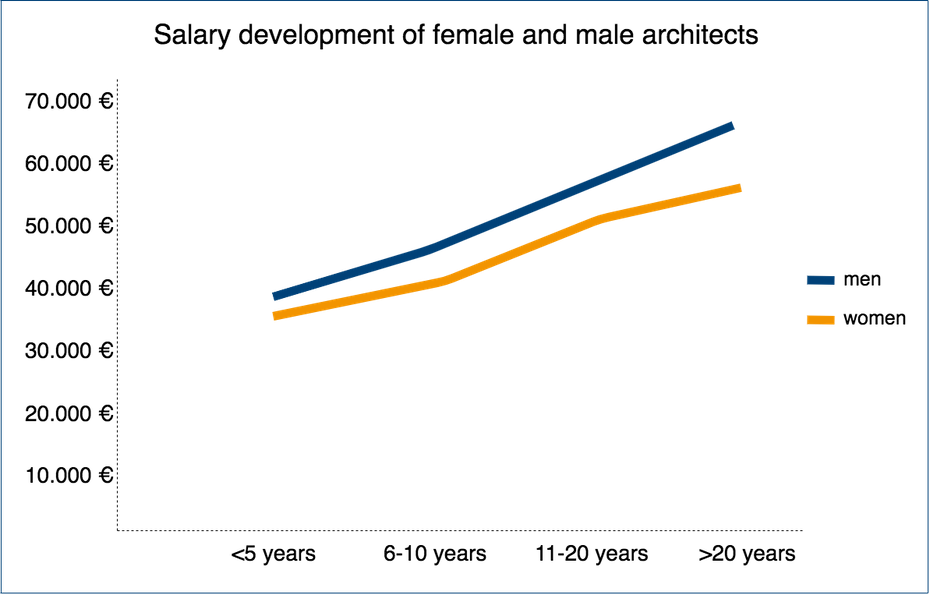
Managers in industrial plants oversee the smooth functioning of the whole process. They help to determine the best use of employees and equipment, establish production standards, and make strategic and tactical decisions. These people are responsible for evaluating and hiring workers. They also set production schedules and ensure safety. They supervise the day-today activities of a workforce and monitor the entire production process to ensure it operates efficiently and at peak efficiency.
The experience and employer of an industrial production manager will determine the potential earnings. Although it's hard for anyone to predict what the future earnings will be, the median industrial manager salary was $103,380 as of May 2016. The highest paid industrial production workers earned $172,000. Also, higher earnings are possible for industrial production managers who have had advanced training and certification. According to the U.S. Bureau of Labor Statistics, industrial production managers who have earned a bachelor's degree or higher may earn more.
Work environment
An industrial production manager splits his or her time between a production floor and an office. Often, the offices are located in the same building. When working in production areas, industrial production managers should adhere to established health and safety procedures and wear the appropriate protective equipment. They spend a lot of time meeting with their subordinates and analysing production data. These managers might also create reports. As a result, an industrial production manager's work environment is often dynamic.
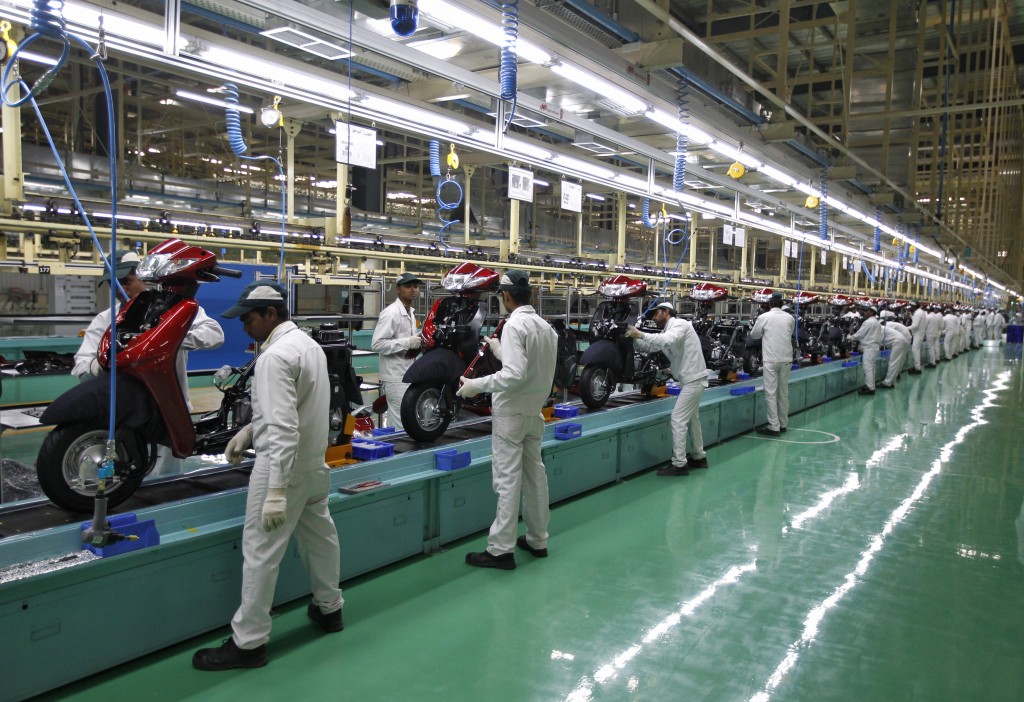
Industrial production managers play an important role in the management of a business. They are responsible for coordinating the activities of workers and increasing productivity. A manager of industrial production is responsible for increasing productivity and safety. Many levels of management have been eliminated, and support staff has been reduced. This leaves more work for production managers. This can be a significant challenge for any manager, and can make it difficult to do the job as a production manager.
FAQ
Why automate your factory?
Modern warehousing is becoming more automated. Increased demand for efficient and faster delivery has resulted in a rise in e-commerce.
Warehouses have to be flexible to meet changing requirements. Technology investment is necessary to enable warehouses to respond quickly to changing demands. Automating warehouses is a great way to save money. These are some of the benefits that automation can bring to warehouses:
-
Increases throughput/productivity
-
Reduces errors
-
Improves accuracy
-
Safety enhancements
-
Eliminates bottlenecks
-
Allows companies scale more easily
-
Workers are more productive
-
It gives visibility to everything that happens inside the warehouse
-
Enhances customer experience
-
Improves employee satisfaction
-
This reduces downtime while increasing uptime
-
Ensures quality products are delivered on time
-
Human error can be eliminated
-
This helps to ensure compliance with regulations
What are the differences between these four types?
Manufacturing is the process that transforms raw materials into useful products. It involves many different activities such as designing, building, testing, packaging, shipping, selling, servicing, etc.
What type of jobs is there in logistics
There are many types of jobs in logistics. These are some of the jobs available in logistics:
-
Warehouse workers - They load and unload trucks and pallets.
-
Transportation drivers - They drive trucks and trailers to deliver goods and carry out pick-ups.
-
Freight handlers – They sort and package freight at warehouses.
-
Inventory managers - They oversee the inventory of goods in warehouses.
-
Sales reps - They sell products and services to customers.
-
Logistics coordinators: They plan and manage logistics operations.
-
Purchasing agents are those who purchase goods and services for the company.
-
Customer service representatives - Answer calls and email from customers.
-
Shipping clerks: They process shipping requests and issue bills.
-
Order fillers - They fill orders based on what is ordered and shipped.
-
Quality control inspectors: They inspect outgoing and incoming products for any defects.
-
Others - There are many other types of jobs available in logistics, such as transportation supervisors, cargo specialists, etc.
What is the role of a production manager?
Production planners make sure that every aspect of the project is delivered on-time, within budget, and within schedule. They also ensure that the product/service meets the client’s needs.
Is automation important in manufacturing?
Automation is important not only for manufacturers but also for service providers. It allows them provide faster and more efficient services. It helps them to lower costs by reducing human errors, and improving productivity.
Is it possible to automate certain parts of manufacturing
Yes! Yes. The Egyptians created the wheel thousands years ago. We now use robots to help us with assembly lines.
There are many uses of robotics today in manufacturing. They include:
-
Automation line robots
-
Robot welding
-
Robot painting
-
Robotics inspection
-
Robots create products
There are many other examples of how manufacturing could benefit from automation. 3D printing makes it possible to produce custom products in a matter of days or weeks.
Statistics
- Many factories witnessed a 30% increase in output due to the shift to electric motors. (en.wikipedia.org)
- (2:04) MTO is a production technique wherein products are customized according to customer specifications, and production only starts after an order is received. (oracle.com)
- According to a Statista study, U.S. businesses spent $1.63 trillion on logistics in 2019, moving goods from origin to end user through various supply chain network segments. (netsuite.com)
- It's estimated that 10.8% of the U.S. GDP in 2020 was contributed to manufacturing. (investopedia.com)
- In the United States, for example, manufacturing makes up 15% of the economic output. (twi-global.com)
External Links
How To
How to use 5S to increase Productivity in Manufacturing
5S stands for "Sort", 'Set In Order", 'Standardize', & Separate>. Toyota Motor Corporation developed the 5S method in 1954. It allows companies to improve their work environment, thereby achieving greater efficiency.
The idea behind standardizing production processes is to make them repeatable and measurable. This means that daily tasks such as cleaning and sorting, storage, packing, labeling, and packaging are possible. These actions allow workers to perform their job more efficiently, knowing what to expect.
Implementing 5S requires five steps. These are Sort, Set In Order, Standardize. Separate. And Store. Each step is a different action that leads to greater efficiency. If you sort items, it makes them easier to find later. When you set items in an order, you put items together. After you have divided your inventory into groups you can store them in easy-to-reach containers. You can also label your containers to ensure everything is properly labeled.
This process requires employees to think critically about how they do their job. Employees must be able to see why they do what they do and find a way to achieve them without having to rely on their old methods. To implement the 5S system, employees must acquire new skills and techniques.
The 5S method increases efficiency and morale among employees. They feel more motivated to work towards achieving greater efficiency as they see the results.