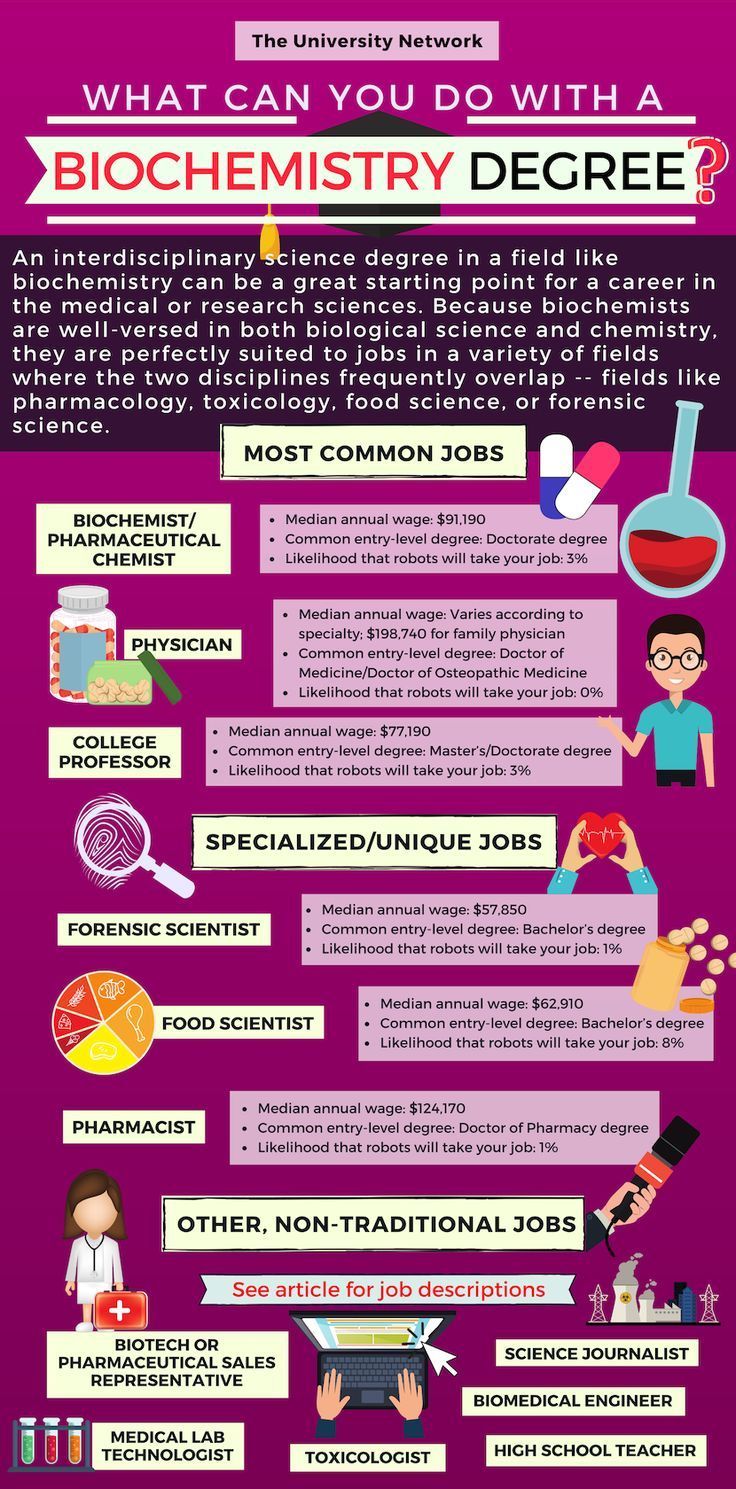
They are responsible for analysing process data and offering technical support to maintenance staff. They assist with short-term outage planning and system improvement.
This is an increasingly popular field. A professional mechanic must be able speak with customers and show his or her knowledge. For this job, you will need to be able to communicate in technical language, manage time well, and work well with others.
These engineers have the technical skills to work in sales and marketing. They can also manage and troubleshoot issues. As the demand for new and more efficient machinery grows, the quality of work expected from these professionals increases.
This field requires high education. To achieve this goal mechanical engineers must be educated about the science behind product design and manufacturing. For example, in the field of heat engineering, they study the flow of heat in structures. In heat engineering, equipment is developed for transportation and air conditioning.
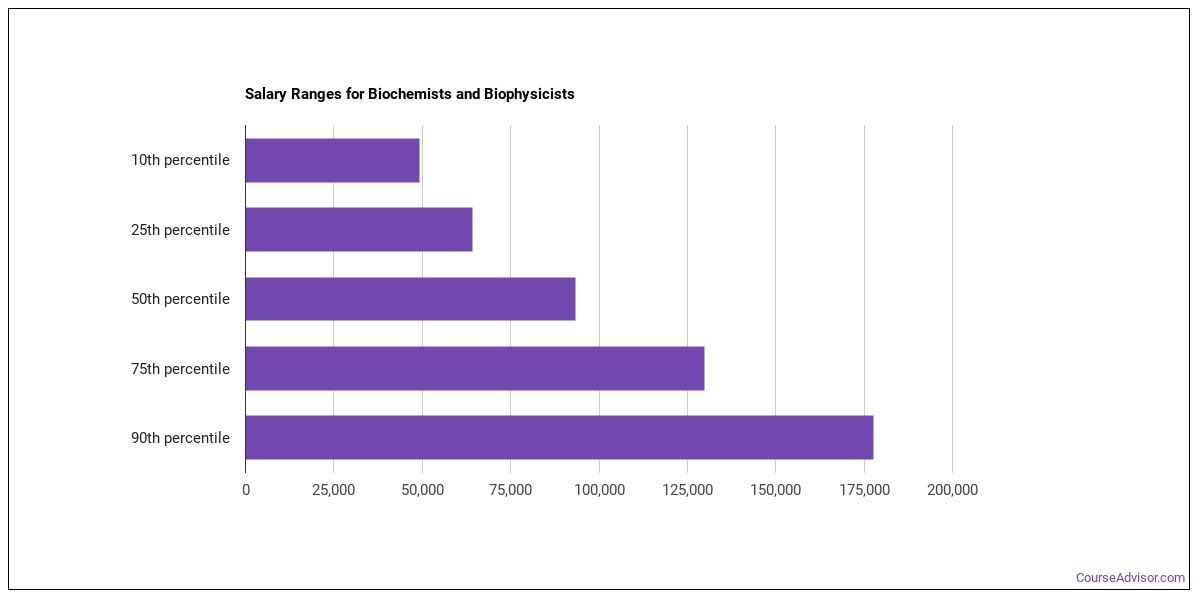
Since the dawn of technology, mechanics have been at forefront. With the advent of computer-aided design, mechanical engineers have been able to develop new designs and materials for smaller and more complex machines. The advancement of nanotechnology has also allowed for the creation of materials that can be used to design on a very small scale. Also, mechanics can work with composites which combine several materials into one product.
These professionals employ rationalized designs and manufacturing processes. Value engineering, which aims to make the best use of existing resources, is one example. Another approach to operations research is also available.
Mechanics are always on the lookout for jobs, and many aspire to establish commercial exchanges with foreigners. For a job abroad, they will need to be able speak and write English fluently.
A good vocabulary is essential. You can improve your English as a mechanic by attending industry events or reading specialized magazines in English. They can also take an online course to improve their skills.
In addition to these skills, mechanics must be able to manage their time well. A minimum of two years experience in the relevant field is required for Mechanical Technicians. They should possess excellent analytical and critical skills, as well the ability to use diagnostic software.
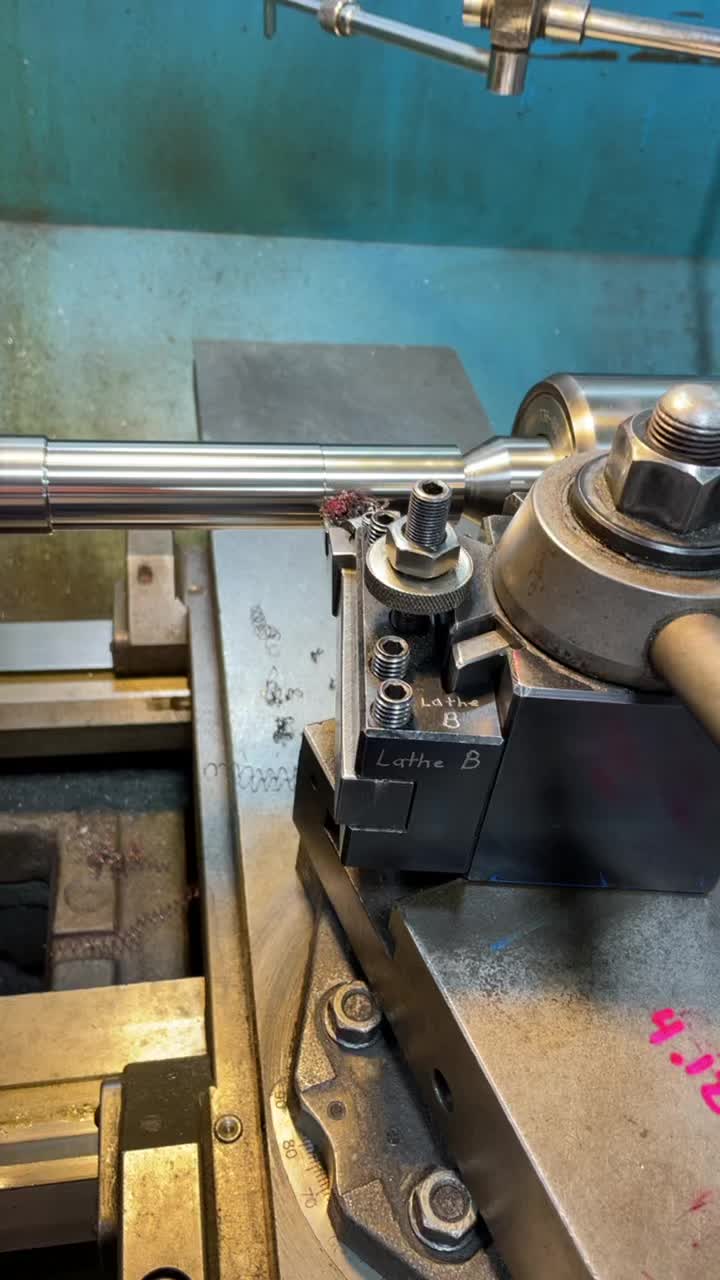
While pursuing a career in this field, it is necessary to have a good understanding of computers, especially the use of computer-aided design. An associate's degree is recommended in mechanical engineering technology.
These specialists assist craftsmen by analyzing process data, assisting them with their daily management, and providing technical leadership to employees. They also find solutions to common problems.
Mechanical engineers work closely with civil engineers, electrical engineers, and chemical engineers in order to improve the performance of vehicles, equipment and systems. They also participate in research, design, and construction. Many mechanical engineers work full time or as an adjunct to their day job.
FAQ
What makes a production planner different from a project manger?
The difference between a product planner and project manager is that a planer is typically the one who organizes and plans the entire project. A production planner, however, is mostly involved in the planning stages.
How important is automation in manufacturing?
Not only is automation important for manufacturers, but it's also vital for service providers. They can provide services more quickly and efficiently thanks to automation. It reduces human errors and improves productivity, which in turn helps them lower their costs.
How can we reduce manufacturing overproduction?
It is essential to find better ways to manage inventory to reduce overproduction. This would decrease the time that is spent on inefficient activities like purchasing, storing, or maintaining excess stock. This will allow us to free up resources for more productive tasks.
This can be done by using a Kanban system. A Kanban board can be used to monitor work progress. A Kanban system allows work items to move through several states before reaching their final destination. Each state represents an individual priority level.
As an example, if work is progressing from one stage of the process to another, then the current task is complete and can be transferred to the next. It is possible to keep a task in the beginning stages until it gets to the end.
This helps to keep work moving forward while ensuring that no work is left behind. Managers can monitor the work being done by Kanban boards to see what is happening at any given time. This information allows them to adjust their workflow based on real-time data.
Lean manufacturing can also be used to reduce inventory levels. Lean manufacturing emphasizes eliminating waste in all phases of production. Anything that does not contribute to the product's value is considered waste. There are several types of waste that you might encounter:
-
Overproduction
-
Inventory
-
Unnecessary packaging
-
Overstock materials
Manufacturers can reduce their costs and improve their efficiency by using these ideas.
Statistics
- It's estimated that 10.8% of the U.S. GDP in 2020 was contributed to manufacturing. (investopedia.com)
- You can multiply the result by 100 to get the total percent of monthly overhead. (investopedia.com)
- (2:04) MTO is a production technique wherein products are customized according to customer specifications, and production only starts after an order is received. (oracle.com)
- [54][55] These are the top 50 countries by the total value of manufacturing output in US dollars for its noted year according to World Bank.[56] (en.wikipedia.org)
- Many factories witnessed a 30% increase in output due to the shift to electric motors. (en.wikipedia.org)
External Links
How To
How to use 5S in Manufacturing to Increase Productivity
5S stands in for "Sort", the "Set In Order", "Standardize", or "Separate". Toyota Motor Corporation created the 5S methodology in 1954. It allows companies to improve their work environment, thereby achieving greater efficiency.
The basic idea behind this method is to standardize production processes, so they become repeatable, measurable, and predictable. This means that daily tasks such as cleaning and sorting, storage, packing, labeling, and packaging are possible. These actions allow workers to perform their job more efficiently, knowing what to expect.
Implementing 5S involves five steps: Sort, Set in Order, Standardize Separate, Store, and Each step involves a different action which leads to increased efficiency. If you sort items, it makes them easier to find later. Once you have placed items in an ordered fashion, you will put them together. After you have divided your inventory into groups you can store them in easy-to-reach containers. Labeling your containers will ensure that everything is correctly labeled.
This requires employees to critically evaluate how they work. Employees should understand why they do the tasks they do, and then decide if there are better ways to accomplish them. To implement the 5S system, employees must acquire new skills and techniques.
In addition to increasing efficiency, the 5S method also improves morale and teamwork among employees. They are more motivated to achieve higher efficiency levels as they start to see improvement.