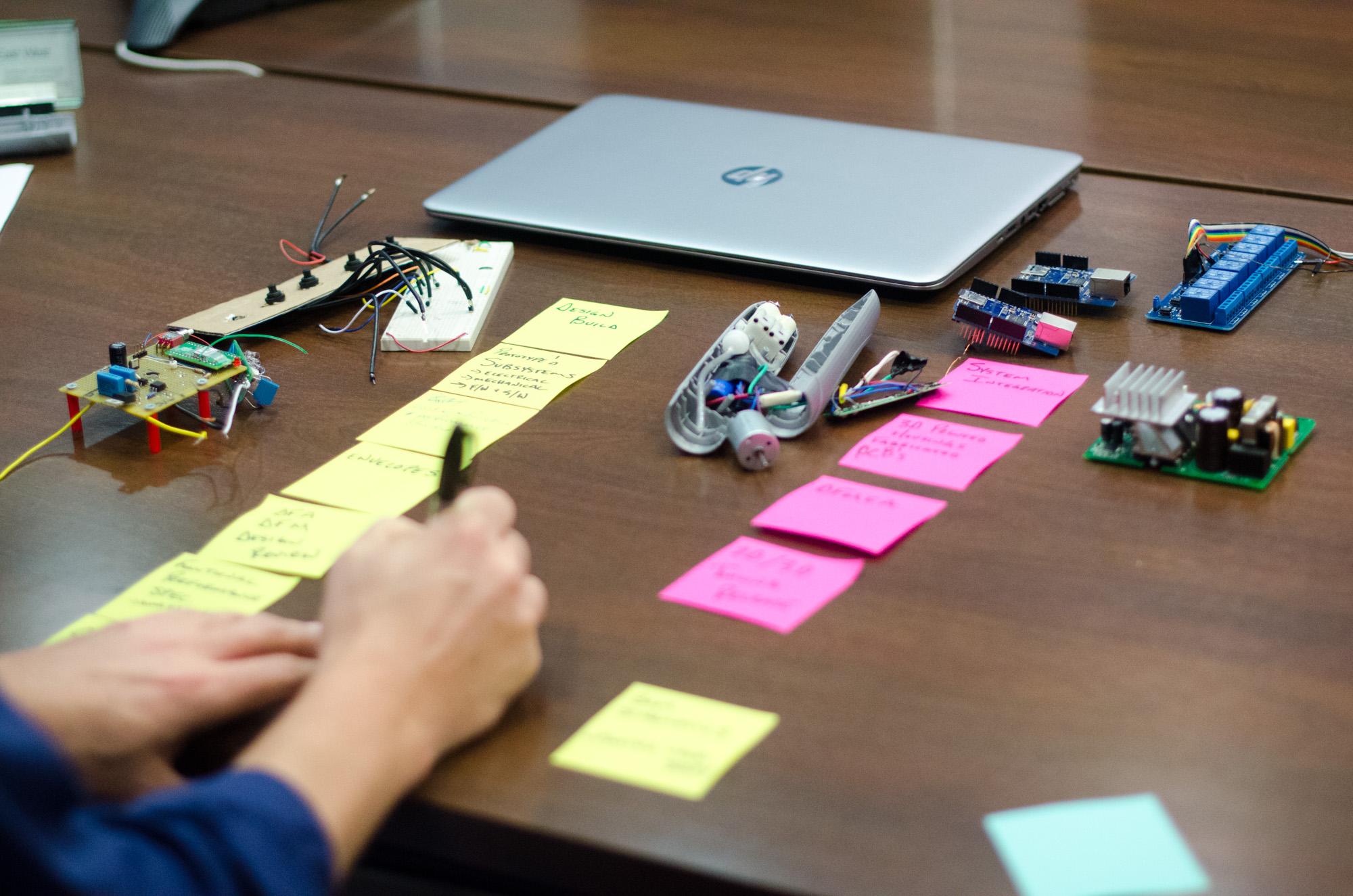
Manufacturing jobs are not just a job. These jobs require a high degree of education and training to get the most out of the industry. The region's average annual income for a factory worker is $88,406, and this number is expected to rise by 2.5%. Many manufacturing companies have put in place safety measures to keep workers safe and healthy.
In fact, Texas' Capital Region is home to 30% of its manufacturing jobs. Although the sector's number declined by -800 by February 2021 it was not a drop in employment. Acme Brick (Samsung Austin Semiconductor) are among the top-ranked companies in the area. This is one of the reasons that the metroplex is one of the most vibrant in the nation.
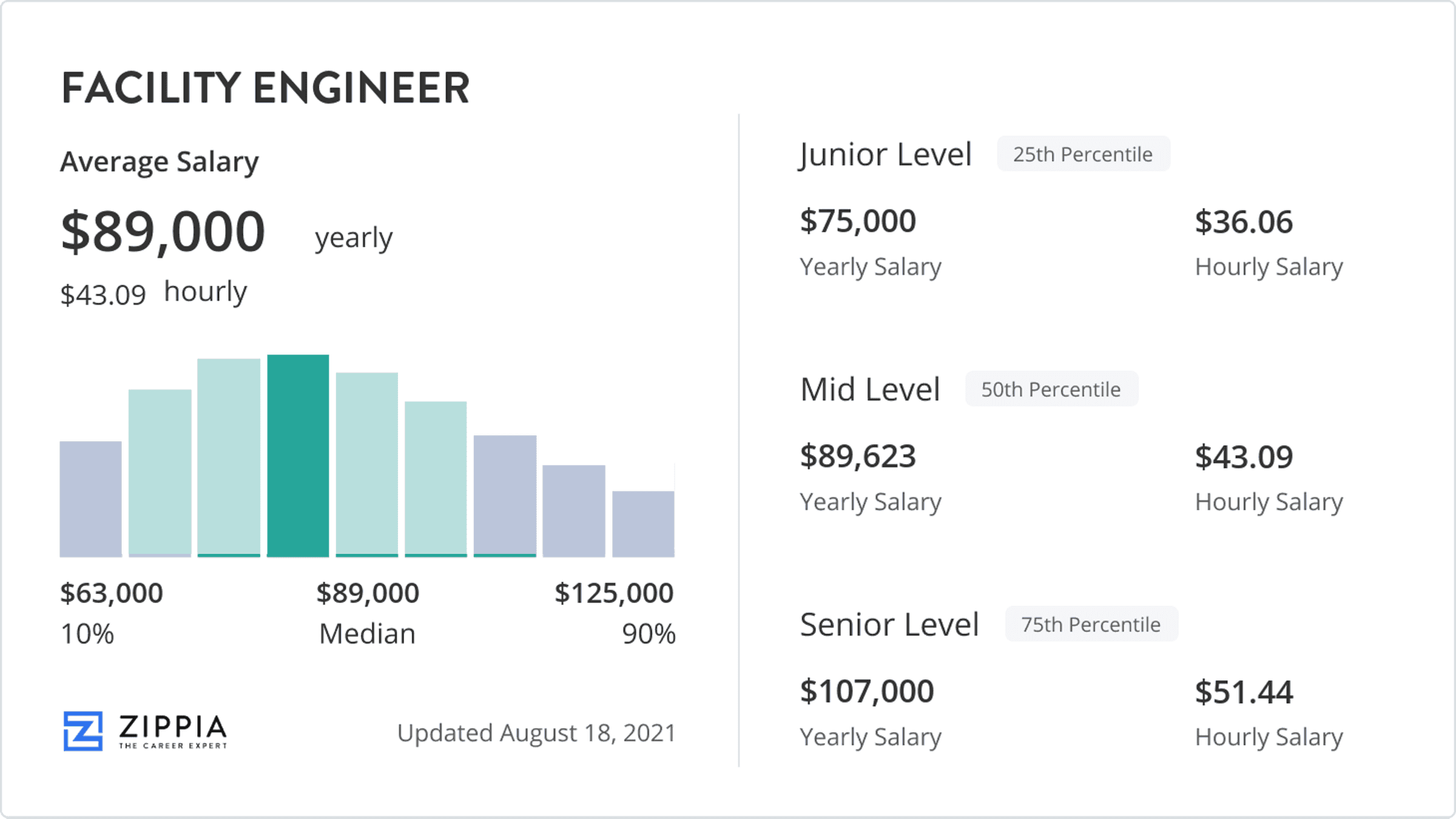
Texas Commission on Economic Opportunity created an interactive exhibit on the topic to show the Capital Region's impressive manufacturing industry. It includes an interesting chart on the manufacturing industry in the area, as well as a plethora of useful information on a variety of topics. One of the most attractive features is the "Essential Texas” mobile app. It allows visitors easy access to data on local tourism, business and the area's past. Another cool feature is the virtual visitor's center, where you can learn about the region's most important industries and how they benefit the community.
The interactive exhibit is definitely impressive. However, you'll also want to look at other TCEO resource. Among them is the Capital Region of Texas, a comprehensive look at a swath of the state stretching from Llano to San Marcos. Here you can see how the region has managed a recovery from the recession and how it is able continue to grow with new industries. It is also a great place for a new job, because it has a lot of skilled and qualified people. You have many options, whether you're looking for a part-time or full-time job.
Many of the world's most prominent companies in technology are located in this area, including Apple, Dell, Oracle, and others. The capital city also houses Rhythm Superfoods - a natural and organic snack company. The Capital Region has a wide range of talented and skilled individuals who make manufacturing exciting.
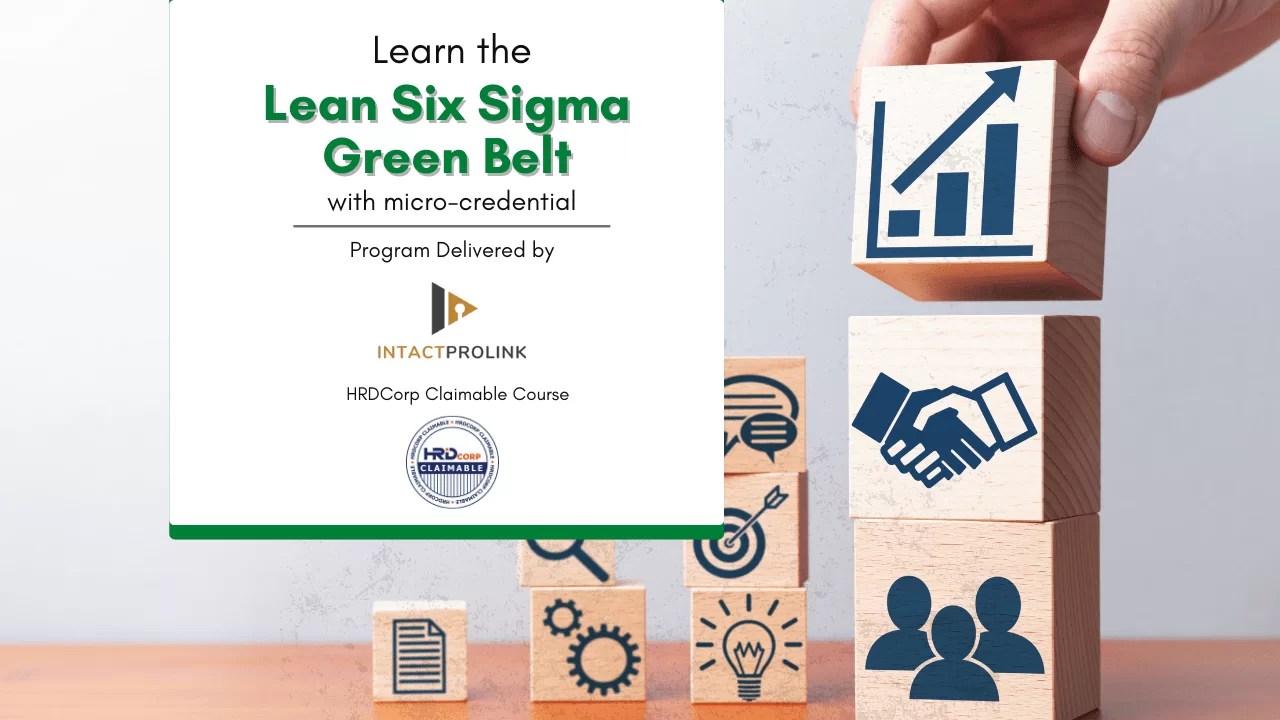
The manufacturing sector of the capital is not a monopoly. Despite the aforementioned recession, the area has maintained a robust employment base, which has resulted in more than 65,000 manufacturing jobs in the region alone. These jobs pay well, but the achievements of the region in manufacturing are far less than those of the entire nation.
FAQ
What are the four types of manufacturing?
Manufacturing is the process of transforming raw materials into useful products using machines and processes. It includes many different activities like designing, building and testing, packaging, shipping and selling, as well as servicing.
What are the jobs in logistics?
Logistics can offer many different jobs. Some of them are:
-
Warehouse workers: They load and unload trucks, pallets, and other cargo.
-
Transport drivers - These are people who drive trucks and trailers to transport goods or perform pick-ups.
-
Freight handlers are people who sort and pack freight into warehouses.
-
Inventory managers - They oversee the inventory of goods in warehouses.
-
Sales representatives - They sell products.
-
Logistics coordinators – They plan and coordinate logistics operations.
-
Purchasing agents - They buy goods and services that are necessary for company operations.
-
Customer service representatives are available to answer customer calls and emails.
-
Ship clerks - They issue bills and process shipping orders.
-
Order fillers – They fill orders based upon what was ordered and shipped.
-
Quality control inspectors - They check incoming and outgoing products for defects.
-
Others - There are many other types of jobs available in logistics, such as transportation supervisors, cargo specialists, etc.
What is the job of a production plan?
Production planners ensure all aspects of the project are delivered within time and budget. They also ensure the quality of the product and service meets the client's requirements.
What are manufacturing and logistics?
Manufacturing refers the process of producing goods from raw materials through machines and processes. Logistics is the management of all aspects of supply chain activities, including procurement, production planning, distribution, warehousing, inventory control, transportation, and customer service. Manufacturing and logistics can often be grouped together to describe a larger term that covers both the creation of products, and the delivery of them to customers.
How can we reduce manufacturing overproduction?
Improved inventory management is the key to reducing overproduction. This would reduce time spent on activities such as purchasing, stocking, and maintaining excess stock. This could help us free up our time for other productive tasks.
Kanban systems are one way to achieve this. A Kanban Board is a visual display that tracks work progress. Work items are moved through various states to reach their destination in a Kanban system. Each state represents a different priority.
If work is moving from one stage to the other, then the current task can be completed and moved on to the next. However, if a task is still at the beginning stages, it will remain so until it reaches the end of the process.
This allows you to keep work moving along while making sure that no work gets neglected. Managers can see how much work has been done and the status of each task at any time with a Kanban Board. This allows them the ability to adjust their workflow using real-time data.
Another way to control inventory levels is to implement lean manufacturing. Lean manufacturing seeks to eliminate waste from every step of the production cycle. Any product that isn't adding value can be considered waste. Some common types of waste include:
-
Overproduction
-
Inventory
-
Packaging not required
-
Materials in excess
Manufacturers can reduce their costs and improve their efficiency by using these ideas.
How can manufacturing reduce production bottlenecks?
Avoiding production bottlenecks is as simple as keeping all processes running smoothly, from the time an order is received until the product ships.
This includes planning to meet capacity requirements and quality control.
Continuous improvement techniques like Six Sigma are the best way to achieve this.
Six Sigma Management System is a method to increase quality and reduce waste throughout your organization.
It emphasizes consistency and eliminating variance in your work.
Statistics
- In 2021, an estimated 12.1 million Americans work in the manufacturing sector.6 (investopedia.com)
- (2:04) MTO is a production technique wherein products are customized according to customer specifications, and production only starts after an order is received. (oracle.com)
- It's estimated that 10.8% of the U.S. GDP in 2020 was contributed to manufacturing. (investopedia.com)
- In the United States, for example, manufacturing makes up 15% of the economic output. (twi-global.com)
- You can multiply the result by 100 to get the total percent of monthly overhead. (investopedia.com)
External Links
How To
How to use 5S to increase Productivity in Manufacturing
5S stands for "Sort", 'Set In Order", 'Standardize', & Separate>. Toyota Motor Corporation created the 5S methodology in 1954. This methodology helps companies improve their work environment to increase efficiency.
This approach aims to standardize production procedures, making them predictable, repeatable, and easily measurable. Cleaning, sorting and packing are all done daily. This knowledge allows workers to be more efficient in their work because they are aware of what to expect.
Five steps are required to implement 5S: Sort, Set In Order, Standardize. Separate. Each step has a different action and leads to higher efficiency. Sorting things makes it easier to find them later. When items are ordered, they are put together. Next, organize your inventory into categories and store them in containers that are easily accessible. Labeling your containers will ensure that everything is correctly labeled.
Employees must be able to critically examine their work practices. Employees must be able to see why they do what they do and find a way to achieve them without having to rely on their old methods. To implement the 5S system, employees must acquire new skills and techniques.
The 5S Method not only improves efficiency, but it also helps employees to be more productive and happier. As they begin to see improvements, they feel motivated to continue working towards the goal of achieving higher levels of efficiency.