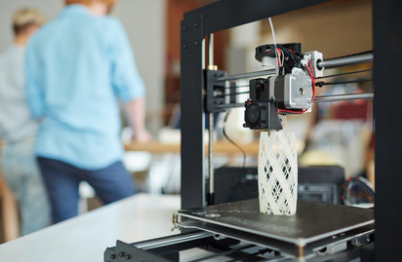
For safety engineers, a bachelor's is necessary. In addition to the education, you need to be able to work well with others. You might need to obtain additional certifications.
You will learn about the different regulations and procedures that safety engineers must follow during training. You will also learn how you can investigate accidents and identify potential hazards. You will learn to test and evaluate machinery, buildings, and consumer products. Additionally, you will learn how to create safety protocols and prepare reports. You will learn how to conduct routine compliance inspections and prepare health and safety programs for workers.
Safety engineers are usually under the direct supervision of more experienced engineers. You may also join professional safety engineering networks such as the American Society of Safety Professionals. This is a good way to build contacts in your field. This is also a chance to learn from experienced safety engineers. If you are planning on becoming a safety engineer, make sure that you keep your resume updated with your qualifications.
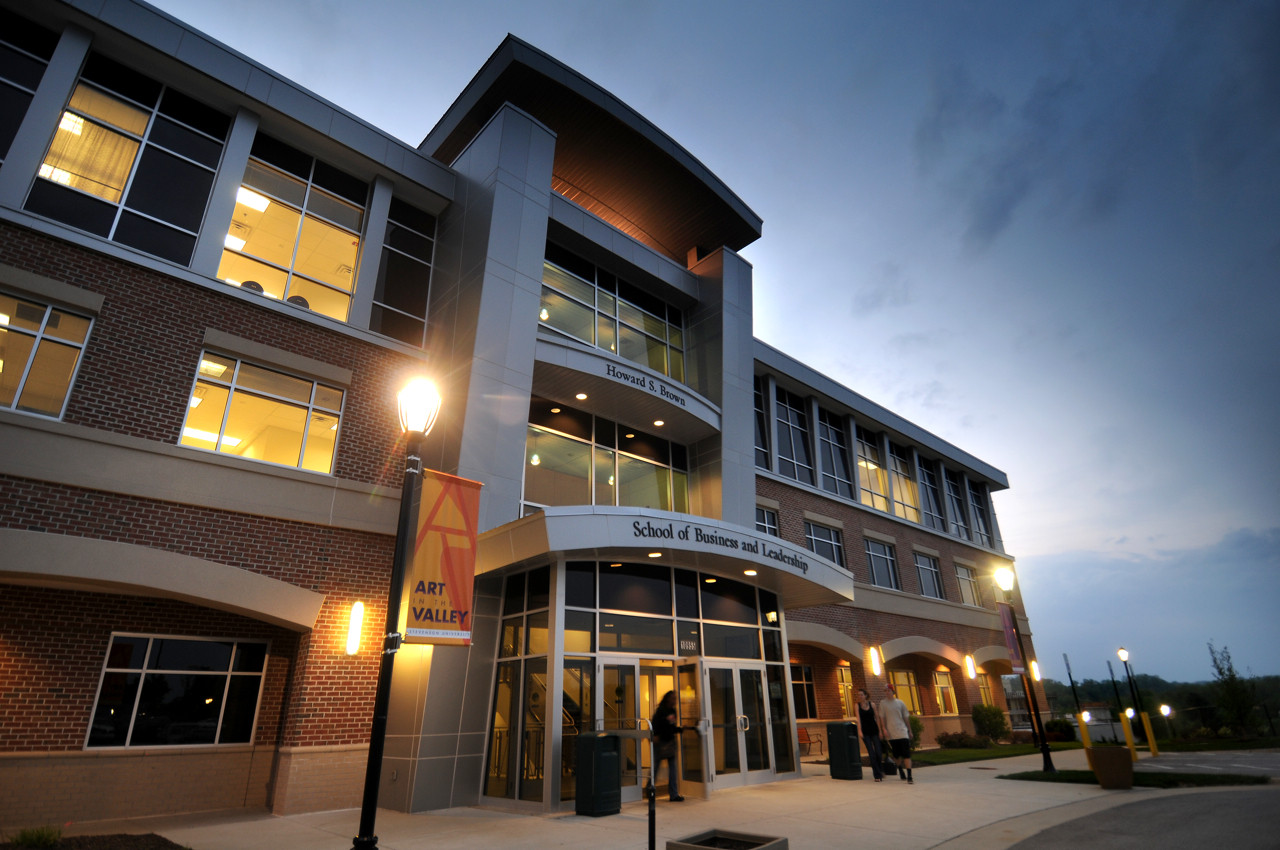
After you have finished your bachelor's degree you might want to pursue a master's in safety and health. This will make it easier to get a job. You can also use your master's degree to move up to a higher position in your field.
During your master's degree program, you will learn how to develop safety systems and how to implement organization-wide procedures. You will also learn advanced planning and analytical skills. This will help you work on more complicated projects and enable you to rise to a higher level. To be eligible for managerial positions within health and safety, you can also use your masters.
Many universities and colleges offer cooperative education programs. These programs enable you to get a bachelor's and practical experience simultaneously. This allows for you to apply for more challenging jobs without a degree. Many of these programs allow students to take part-time classes, while others allow them to work full time while they earn their degree.
A bachelor's degree is not enough. You will also need a license to work as safety engineer in your state. Licenses can be obtained in most states. You will need four years experience in the field and must pass a state exam. You may also be required to complete a course in workplace safety.
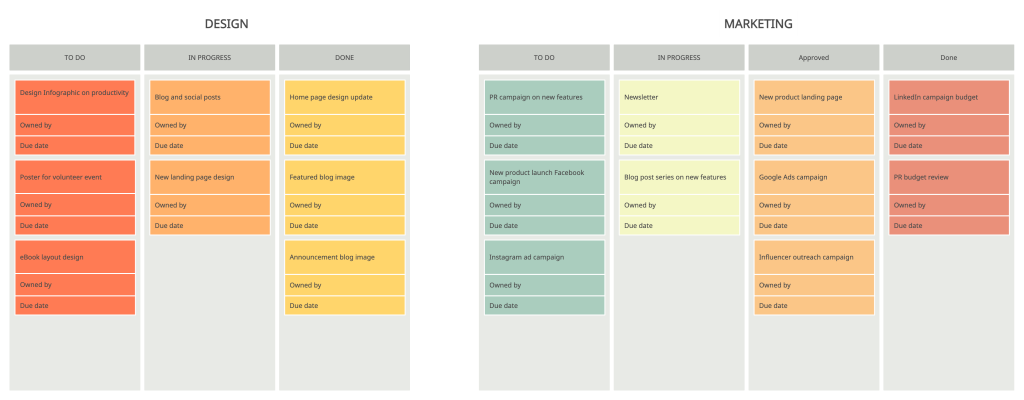
Once you are licensed, you may find that employers prefer to hire candidates with practical experience. Many schools offer cooperative education programs, and some allow students to take classes part-time. You can also search for employment online. It is possible to join professional organizations, such as American Society of Safety Engineers. You can also join Institute of Hazardous Materials Management which assists safety professionals in developing leadership skills.
It is a great career choice to work in safety and health engineering. This job requires a lot of science, math, communication and engineering skills. Also, you must be creative and skilled at solving difficult problems.
FAQ
What are my options for learning more about manufacturing
Experience is the best way for you to learn about manufacturing. However, if that's not possible, you can always read books or watch educational videos.
What is the difference in Production Planning and Scheduling, you ask?
Production Planning (PP), also known as forecasting and identifying production capacities, is the process that determines what product needs to be produced at any particular time. This is accomplished by forecasting the demand and identifying production resources.
Scheduling involves the assignment of dates and times to tasks in order to complete them within the timeframe.
What does it mean to be a manufacturer?
Manufacturing Industries is a group of businesses that produce goods for sale. Consumers are the people who purchase these products. To accomplish this goal, these companies employ a range of processes including distribution, sales, management, and production. They produce goods from raw materials by using machines and other machinery. This includes all types if manufactured goods.
What are the 7 R's of logistics?
The acronym 7Rs of Logistics refers to the seven core principles of logistics management. It was created by the International Association of Business Logisticians and published in 2004 under its "Seven Principles of Logistics Management".
The acronym is made up of the following letters:
-
Responsible - ensure that actions are in compliance with legal requirements and do not cause harm to others.
-
Reliable - have confidence in the ability to deliver on commitments made.
-
Reasonable - use resources efficiently and don't waste them.
-
Realistic - Consider all aspects of operations, including environmental impact and cost effectiveness.
-
Respectful – Treat others fairly and equitably.
-
Resourceful - look for opportunities to save money and increase productivity.
-
Recognizable provides value-added products and services to customers
What are the products of logistics?
Logistics is the process of moving goods from one point to another.
They include all aspects associated with transport including packaging, loading transporting, unloading storage, warehousing inventory management customer service, distribution returns and recycling.
Logisticians ensure the product reaches its destination in the most efficient manner. They assist companies with their supply chain efficiency through information on demand forecasts. Stock levels, production times, and availability.
They also keep track of shipments in transit, monitor quality standards, perform inventories and order replenishment, coordinate with suppliers and vendors, and provide support services for sales and marketing.
What is the responsibility of a logistics manager?
A logistics manager ensures that all goods are delivered on time and without damage. This is done using his/her knowledge of the company's products. He/she also needs to ensure adequate stock to meet demand.
Is it possible to automate certain parts of manufacturing
Yes! Automation has been around since ancient times. The Egyptians invent the wheel thousands of year ago. We now use robots to help us with assembly lines.
Actually, robotics can be used in manufacturing for many purposes. These include:
-
Robots for assembly line
-
Robot welding
-
Robot painting
-
Robotics inspection
-
Robots create products
Automation could also be used to improve manufacturing. For instance, 3D printing allows us make custom products and not have to wait for months or even weeks to get them made.
Statistics
- You can multiply the result by 100 to get the total percent of monthly overhead. (investopedia.com)
- According to the United Nations Industrial Development Organization (UNIDO), China is the top manufacturer worldwide by 2019 output, producing 28.7% of the total global manufacturing output, followed by the United States, Japan, Germany, and India.[52][53] (en.wikipedia.org)
- Job #1 is delivering the ordered product according to specifications: color, size, brand, and quantity. (netsuite.com)
- In the United States, for example, manufacturing makes up 15% of the economic output. (twi-global.com)
- In 2021, an estimated 12.1 million Americans work in the manufacturing sector.6 (investopedia.com)
External Links
How To
How to Use the 5S to Increase Productivity In Manufacturing
5S stands for "Sort", "Set In Order", "Standardize", "Separate" and "Store". Toyota Motor Corporation invented the 5S strategy in 1954. It assists companies in improving their work environments and achieving higher efficiency.
This method has the basic goal of standardizing production processes to make them repeatable. This means that daily tasks such as cleaning and sorting, storage, packing, labeling, and packaging are possible. These actions allow workers to perform their job more efficiently, knowing what to expect.
Implementing 5S involves five steps: Sort, Set in Order, Standardize Separate, Store, and Each step requires a different action, which increases efficiency. You can make it easy for people to find things later by sorting them. When items are ordered, they are put together. Next, organize your inventory into categories and store them in containers that are easily accessible. Labeling your containers will ensure that everything is correctly labeled.
Employees need to reflect on how they do their jobs. Employees should understand why they do the tasks they do, and then decide if there are better ways to accomplish them. In order to use the 5S system effectively, they must be able to learn new skills.
In addition to improving efficiency, the 5S system also increases morale and teamwork among employees. They are more motivated to achieve higher efficiency levels as they start to see improvement.