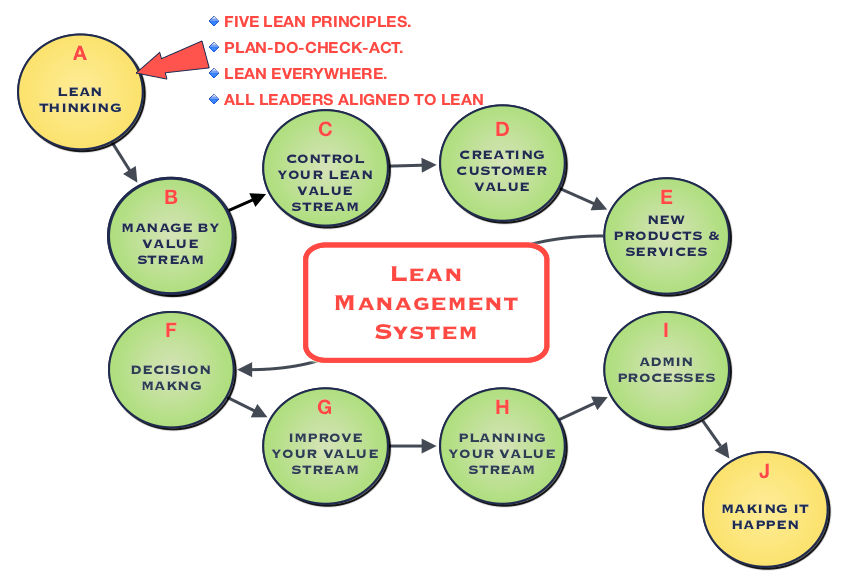
A sustainable supply chain is not easy to establish. The logistics of transportation and packaging can contribute to greenhouse gas emissions and waste. For example, investing in compact packaging can reduce the shipping weight and lower costs. It can reduce waste and protect the bottom-line.
Supply chain sustainability requires a combination of processes, policies, and technology. Many companies are looking for ways to use sustainable materials, measure performance, and make operational improvements. To make their suppliers more sustainable, some companies offer training.
A sustainable supply system can bring benefits to both the company's bottom line and the wider community. Companies can choose suppliers that emphasize renewables and recycled materials, and they can reduce the number of offerings they make. They can also encourage suppliers who use sustainable material and establish a code to ensure the integrity of their suppliers.
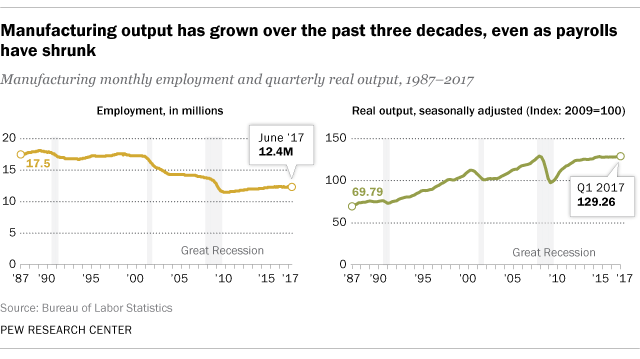
Companies can also reduce waste through the remarketing of unused products. They can also recycle the water that they use. Companies can set goals that are measurable to improve their supply chains and can involve internal and external stakeholders to bring about change. They can also establish strong governance that will help them meet their sustainability targets.
Many companies have taken steps to reduce emissions from their facilities, purchased energy, and transportation partners. Most companies have not yet addressed indirect emissions from their supply chains partners. These include transport and distribution partners. The Carbon Disclosure Project has reported that some companies have made progress in reducing greenhouse gas emissions, but there is still more work to be done.
To increase supply chain sustainability, companies must set clear goals, engage with internal and external stakeholders, measure performance, and establish quantifiable targets. They should also engage their suppliers and customers to ensure that they are meeting their goals. They should also use data for their decisions and create a clear plan of how they will get there.
Companies can also improve their supply chain resilience with strong risk management and nearshoring/diversifying their suppliers. Bed Bath & Beyond created eight owned brands to increase its control over their supply chain. It claims that at minimum half of its wood, cotton and other materials are sustainably sourced. It has also identified key locations for warehousing.
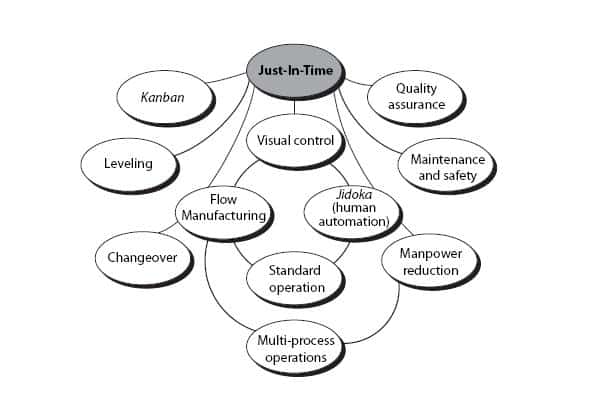
Companies should also be aware of the impact that packaging has on the environment. Some innovations may allow products to either be recycled or reused. These innovations also can help reduce the size of shipments, as well the number of trips they make. Additionally, companies can invest in compact packaging or update warehouse refrigeration equipment. These innovations can have long-lasting effects and they can reduce their carbon footprint.
Many companies are also adopting more circular economy models. They are developing products that can either be reused or repurposed, and are focusing their attention on the finite resources they do have. This will help decrease greenhouse gas emissions and reduce the waste.
FAQ
What are the goods of logistics?
Logistics involves the transportation of goods from point A and point B.
They include all aspects of transport, including packaging, loading, transporting, unloading, storing, warehousing, inventory management, customer service, distribution, returns, and recycling.
Logisticians ensure that the right product reaches the right place at the right time and under safe conditions. They help companies manage their supply chain efficiency by providing information on demand forecasts, stock levels, production schedules, and availability of raw materials.
They coordinate with vendors and suppliers, keep track of shipments, monitor quality standards and perform inventory and order replenishment.
What are the jobs in logistics?
Logistics can offer many different jobs. Here are some:
-
Warehouse workers – They load and unload pallets and trucks.
-
Transportation drivers - They drive trucks and trailers to deliver goods and carry out pick-ups.
-
Freight handlers - They sort and pack freight in warehouses.
-
Inventory managers - They oversee the inventory of goods in warehouses.
-
Sales reps - They sell products and services to customers.
-
Logistics coordinators - They organize and plan logistics operations.
-
Purchasing agents – They buy goods or services necessary to run a company.
-
Customer service representatives - Answer calls and email from customers.
-
Shippers clerks - They process shipping order and issue bills.
-
Order fillers - These people fill orders based on what has been ordered.
-
Quality control inspectors – They inspect incoming and outgoing products to ensure that there are no defects.
-
Others – There are many other types available in logistics. They include transport supervisors, cargo specialists and others.
What are the responsibilities of a manufacturing manager
A manufacturing manager must ensure that all manufacturing processes are efficient and effective. They must also be alert to any potential problems and take appropriate action.
They must also be able to communicate with sales and marketing departments.
They should be informed about industry trends and be able make use of this information to improve their productivity and efficiency.
Statistics
- According to the United Nations Industrial Development Organization (UNIDO), China is the top manufacturer worldwide by 2019 output, producing 28.7% of the total global manufacturing output, followed by the United States, Japan, Germany, and India.[52][53] (en.wikipedia.org)
- Job #1 is delivering the ordered product according to specifications: color, size, brand, and quantity. (netsuite.com)
- You can multiply the result by 100 to get the total percent of monthly overhead. (investopedia.com)
- In the United States, for example, manufacturing makes up 15% of the economic output. (twi-global.com)
- In 2021, an estimated 12.1 million Americans work in the manufacturing sector.6 (investopedia.com)
External Links
How To
How to Use Just-In-Time Production
Just-in time (JIT), is a process that reduces costs and increases efficiency in business operations. This is where you have the right resources at the right time. This means that only what you use is charged to your account. Frederick Taylor was the first to coin this term. He developed it while working as a foreman during the early 1900s. Taylor observed that overtime was paid to workers if they were late in working. He decided to ensure workers have enough time to do their jobs before starting work to improve productivity.
JIT is an acronym that means you need to plan ahead so you don’t waste your money. Also, you should look at the whole project from start-to-finish and make sure you have the resources necessary to address any issues. You can anticipate problems and have enough equipment and people available to fix them. This will ensure that you don't spend more money on things that aren't necessary.
There are many JIT methods.
-
Demand-driven: This JIT is where you place regular orders for the parts/materials that are needed for your project. This will allow to track how much material has been used up. It will also allow you to predict how long it takes to produce more.
-
Inventory-based : You can stock the materials you need in advance. This allows you to predict how much you can expect to sell.
-
Project-driven: This approach involves setting aside sufficient funds to cover your project's costs. When you know how much you need, you'll purchase the appropriate amount of materials.
-
Resource-based JIT : This is probably the most popular type of JIT. Here you can allocate certain resources based purely on demand. For instance, if you have a lot of orders coming in, you'll assign more people to handle them. You'll have fewer orders if you have fewer.
-
Cost-based: This is a similar approach to resource-based but you are not only concerned with how many people you have, but also how much each one costs.
-
Price-based pricing: This is similar in concept to cost-based but instead you look at how much each worker costs, it looks at the overall company's price.
-
Material-based - This is a variant of cost-based. But instead of looking at the total company cost, you focus on how much raw material you spend per year.
-
Time-based JIT: A variation on resource-based JIT. Instead of worrying about how much each worker costs, you can focus on how long the project takes.
-
Quality-based JIT: Another variation on resource-based JIT. Instead of worrying about the costs of each employee or how long it takes for something to be made, you should think about how quality your product is.
-
Value-based JIT: One of the most recent forms of JIT. This is where you don't care about how the products perform or whether they meet customers' expectations. Instead, you're focused on how much value you add to the market.
-
Stock-based is an inventory-based system that measures the number of items produced at any given moment. It's used when you want to maximize production while minimizing inventory.
-
Just-intime (JIT), planning is a combination JIT management and supply chain management. It is the process that schedules the delivery of components within a short time of their order. It is essential because it reduces lead-times and increases throughput.