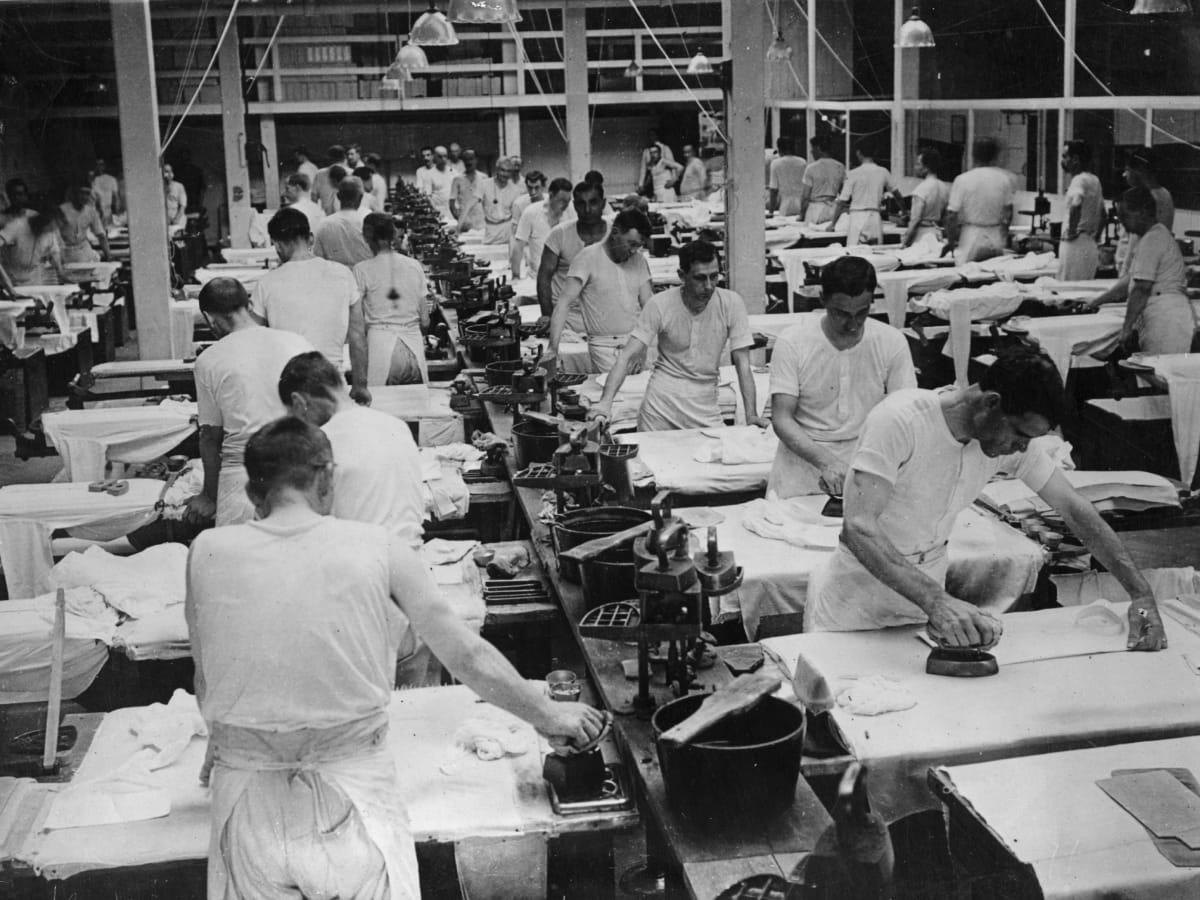
There are a wide variety of logistics jobs in Tampa. You will find many in the construction, healthcare and manufacturing industries. But you can also get a job in the wholesale industry or consult for firms that help different types of companies streamline their supply chains.
A degree or diploma in logistics can offer a range of career possibilities. An associate degree can help you find entry-level roles such as shipping clerks. However, bachelor's level jobs are reserved for those with a higher education. Depending on what you want to do, and your goals, it may be best for you to choose a specialization in logistics.
BLS data predicts that careers in logistics will grow. Between 2018 and 2028, employment for these professionals is expected to increase by 5%. Even more job growth is expected for professionals who are focused on business operation.
You can earn a Logistics degree at either a Community College or a Four-Year University. These programs often offer different logistics concentrations to help you develop your skills and be more employable.
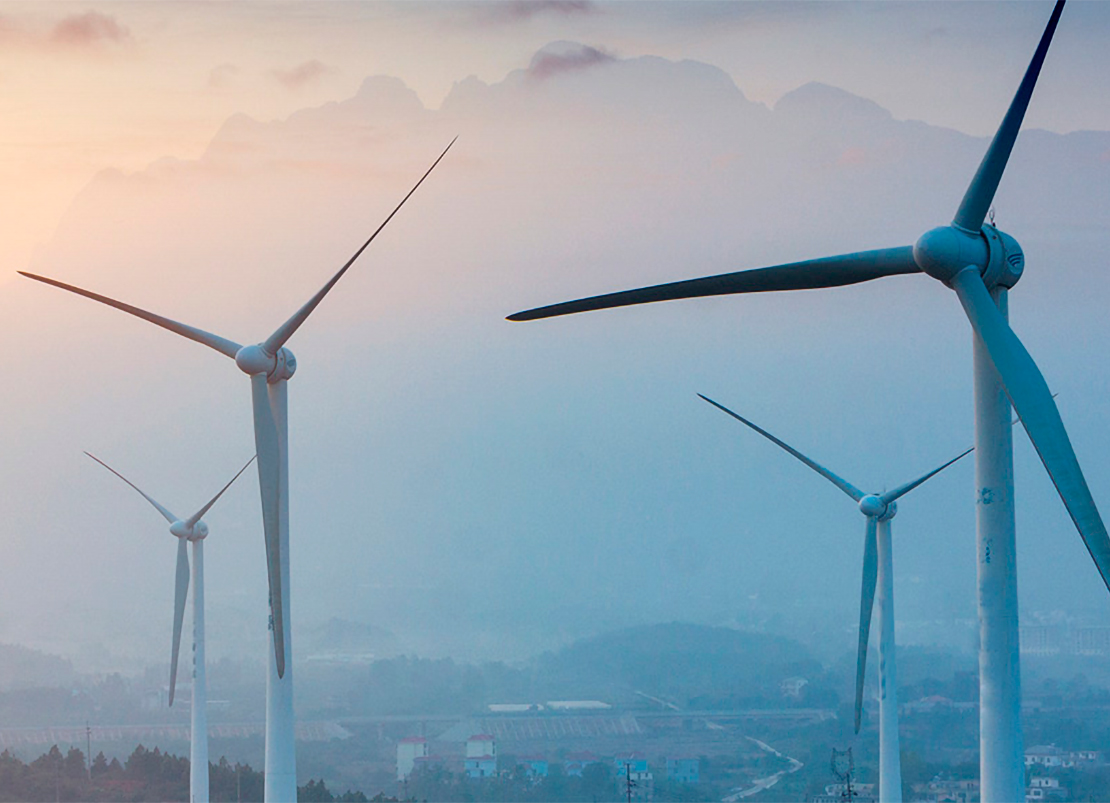
As well as pursuing their bachelor's degrees, students are encouraged to take advantage of internships and networking events. These opportunities can give you invaluable experience and help you land your first logistics position.
The logistics sector has a diverse work force, and the job prospects are usually good. You can find jobs in logistics all over the country, and especially in big and growing states like California or Texas. You can also find careers in a number of specific sectors, such as aerospace and oil and gas.
When selecting a third-party logistics company, consider the company's size and capabilities. You should choose a 3PL who understands your business, and can provide you with a tailored solution that meets your needs. This will enable you to lower your overall costs while increasing your efficiencies.
Your company's supply chain is essential to the success of your business. You must have the right people and the right tools to ensure that your products arrive at the correct time and in perfect condition. You can improve the efficiency of your supply chain by selecting a third-party logistics provider that has expertise in your industry and can deliver the goods on time, every time.
Sheer, a full-service 3PL based in Tampa, can increase the efficiency and speed of your supply chain as well as reduce your costs. We provide a range of services to our customers, including transportation, inventory management, and shipping.
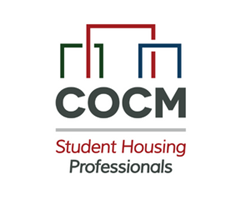
Our suite of tools will also help you to track and manage the supply chain. Our cloud-based system integrates with your existing ERP, allowing you to easily monitor and control your entire business.
With Sheer, you can take advantage of our multimodal freight network and transform your supply chain from a liability to an asset. We can ensure that your products will be delivered on time, safely and securely every single time.
FAQ
How can manufacturing reduce production bottlenecks?
To avoid production bottlenecks, ensure that all processes run smoothly from the moment you receive your order to the time the product ships.
This includes planning to meet capacity requirements and quality control.
Continuous improvement techniques such Six Sigma are the best method to accomplish this.
Six Sigma management is a system that improves quality and reduces waste within your organization.
It's all about eliminating variation and creating consistency in work.
What do you mean by warehouse?
A warehouse, or storage facility, is where goods are stored prior to being sold. It can be either an indoor or outdoor space. In some cases it could be both indoors and outdoors.
How can manufacturing overproduction be reduced?
Improved inventory management is the key to reducing overproduction. This would reduce the amount of time spent on unnecessary activities such as purchasing, storing, and maintaining excess stock. This would allow us to use our resources for more productive tasks.
This can be done by using a Kanban system. A Kanban board can be used to monitor work progress. In a Kanban system, work items move through a sequence of states until they reach their final destination. Each state is assigned a different priority.
When work is completed, it can be transferred to the next stage. If a task is still in its beginning stages, it will continue to be so until it reaches the end.
This helps to keep work moving forward while ensuring that no work is left behind. Managers can see how much work has been done and the status of each task at any time with a Kanban Board. This information allows them to adjust their workflow based on real-time data.
Lean manufacturing is another way to manage inventory levels. Lean manufacturing focuses on eliminating waste throughout the entire production chain. Waste includes anything that does not add value to the product. The following are examples of common waste types:
-
Overproduction
-
Inventory
-
Packaging that is not necessary
-
Exceed materials
By implementing these ideas, manufacturers can improve efficiency and cut costs.
What are the 7 Rs of logistics?
The acronym 7Rs of Logistics refers to the seven core principles of logistics management. It was developed by International Association of Business Logisticians (IABL), and published as part of their "Seven Principles of Logistics Management Series" in 2004.
The following letters make up the acronym:
-
Responsive - ensure all actions are legal and not harmful to others.
-
Reliable – have faith in your ability and capability to keep promises.
-
It is reasonable to use resources efficiently and not waste them.
-
Realistic – Consider all aspects, including cost-effectiveness as well as environmental impact.
-
Respectful - treat people fairly and equitably.
-
You are resourceful and look for ways to save money while increasing productivity.
-
Recognizable provides value-added products and services to customers
What is the responsibility for a logistics manager
Logistics managers are responsible for ensuring that all goods arrive in perfect condition and on time. This is done by using his/her experience and knowledge of the company's products. He/she must also ensure sufficient stock to meet the demand.
What's the difference between Production Planning & Scheduling?
Production Planning (PP), is the process of deciding what production needs to take place at any given time. Forecasting demand is one way to do this.
Scheduling is the process that assigns dates to tasks so they can get completed within a given timeframe.
How can efficiency in manufacturing be improved?
First, we need to identify which factors are most critical in affecting production times. The next step is to identify the most important factors that affect production time. You can start by identifying the most important factors that impact production time. Once you've identified them, try to find solutions for each of those factors.
Statistics
- (2:04) MTO is a production technique wherein products are customized according to customer specifications, and production only starts after an order is received. (oracle.com)
- Job #1 is delivering the ordered product according to specifications: color, size, brand, and quantity. (netsuite.com)
- In the United States, for example, manufacturing makes up 15% of the economic output. (twi-global.com)
- It's estimated that 10.8% of the U.S. GDP in 2020 was contributed to manufacturing. (investopedia.com)
- You can multiply the result by 100 to get the total percent of monthly overhead. (investopedia.com)
External Links
How To
Six Sigma and Manufacturing
Six Sigma is defined by "the application SPC (statistical process control) techniques to achieve continuous improvements." It was developed by Motorola's Quality Improvement Department at their plant in Tokyo, Japan, in 1986. Six Sigma is a method to improve quality through standardization and elimination of defects. Since there are no perfect products, or services, this approach has been adopted by many companies over the years. Six Sigma's main objective is to reduce variations from the production average. This means that if you take a sample of your product, then measure its performance against the average, you can find out what percentage of the time the process deviates from the norm. If it is too large, it means that there are problems.
Understanding the nature of variability in your business is the first step to Six Sigma. Once you understand this, you can then identify the causes of variation. It is important to identify whether the variations are random or systemic. Random variations are caused when people make mistakes. While systematic variations are caused outside of the process, they can occur. Random variations would include, for example, the failure of some widgets to fall from the assembly line. It would be considered a systematic problem if every widget that you build falls apart at the same location each time.
Once you have identified the problem, you can design solutions. You might need to change the way you work or completely redesign the process. You should then test the changes again after they have been implemented. If they didn't work, then you'll need to go back to the drawing board and come up with another plan.