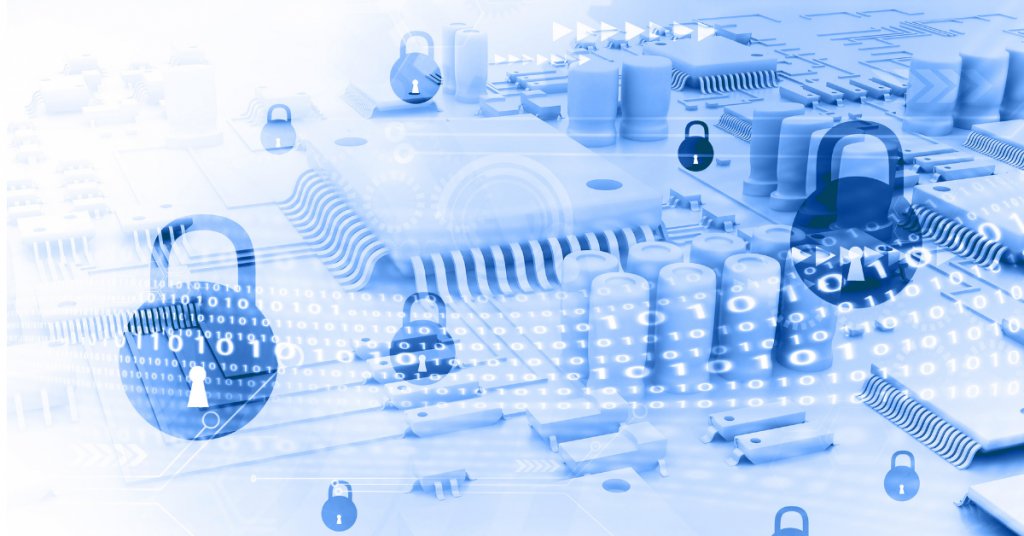
A continuous flow of goods through the supply chain is what time manufacturing involves. It is an efficient and effective way to manufacture goods and avoid overproduction.
Just in Time Production
Toyota Production System, or TPS, is a manufacturing system that employs just-in time production. It allows companies to deliver parts and raw materials directly to the manufacturing plant, so that they are available for use when needed by the production line.
This also allows businesses to save money on their storage and inventory. This will allow the company to make less product but have more cash available to invest in other areas.
The automobile industry is a good example of just-in-time production. Car manufacturers can't afford to produce too many vehicles, as they have to sell them in a short time. Instead, they wait for orders from customers and keep as little inventory as possible.
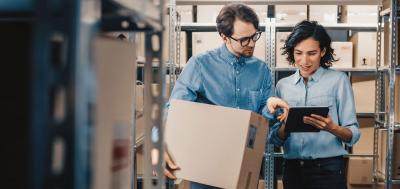
The PPS system allows them to see which parts are in stock and which have been ordered. Using the PPS system, they can see which parts have already been ordered and which ones are still in stock.
They can also order raw materials from suppliers, which can reduce the cost of their production process and ensure that the components they use are high quality.
When a new vehicle needs to be built, they can create a purchase order that says when they want the parts to arrive at their facility. Then they receive the parts from the supplier and begin building the vehicle.
The company then delivers the car in good time to the client. The company can provide a consistent and reliable product to its customers.
Just in time production is often used for small companies that need to create a product but do not have large quantities of inventory or a complex supply chain. This can help to build relationships with vendors and supply chains that minimizes the risk for stockouts and shortages.
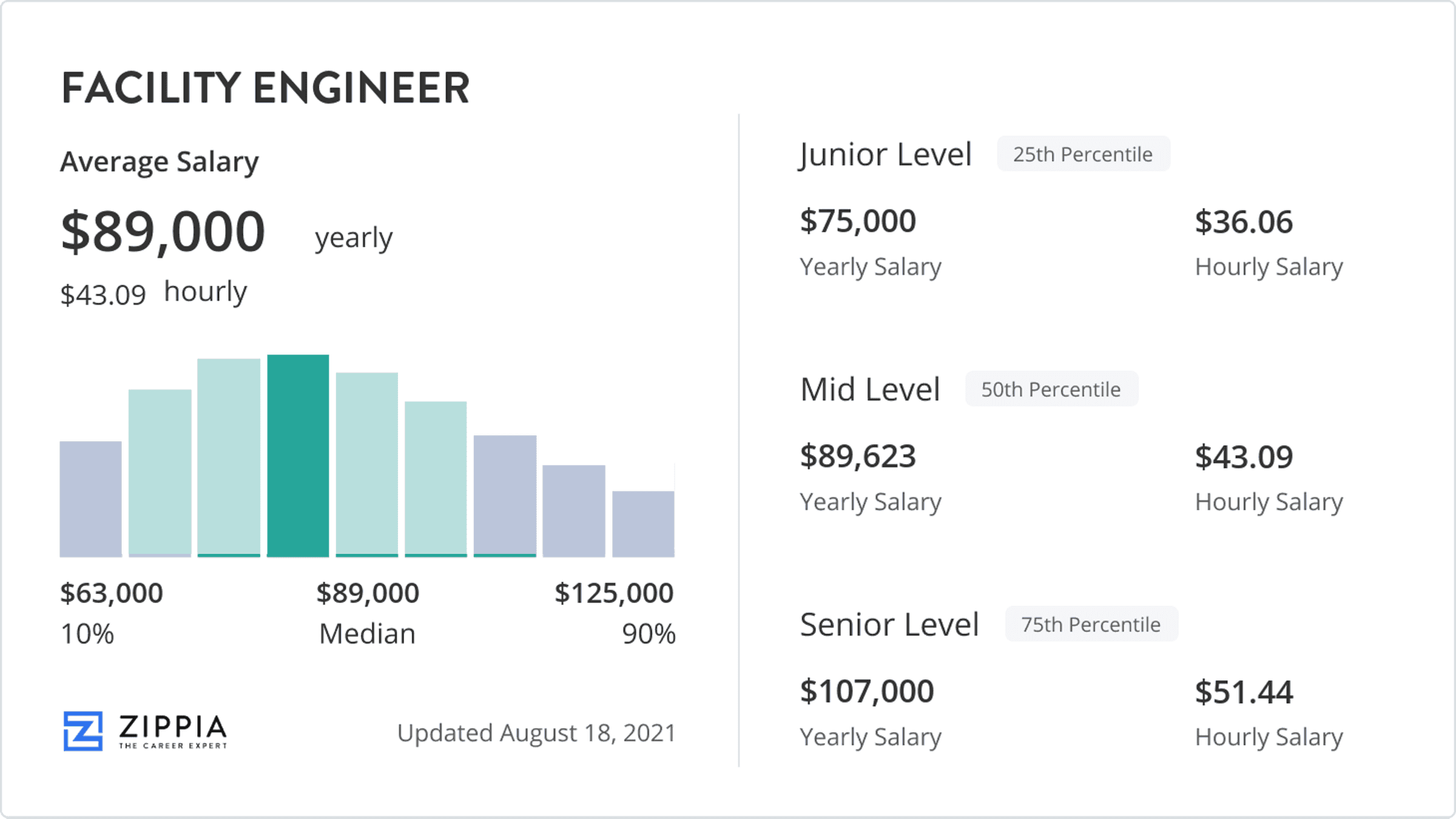
Just-in time is especially useful for manufacturers who are located close to a large city or have suppliers nearby that can deliver their parts easily and quickly. The method also helps to retain employees by allowing them to stay with the company for long periods of time.
A just in time delivery is a supply chain management method that is based on having a product arrive at a location and ready to be shipped when it is needed by the customer. This type of delivery is important for any business that has an ecommerce presence and customers who need their products delivered as soon as possible.
Just in time delivery is popular because it allows retailers and customers to choose from more convenient and quicker shipping options. It lets customers choose the fastest, most convenient delivery option available to them for their purchase. This allows them to make an informed decision.
Just-in time delivery can be a good way for businesses react to supply chains that fail due to unforeseeable delays or accidents. It can help businesses stay competitive and in business.
FAQ
What are the 4 types manufacturing?
Manufacturing is the process that transforms raw materials into useful products. It involves many different activities such as designing, building, testing, packaging, shipping, selling, servicing, etc.
What are the jobs in logistics?
There are different kinds of jobs available in logistics. Some examples are:
-
Warehouse workers – They load and unload pallets and trucks.
-
Transport drivers - These are people who drive trucks and trailers to transport goods or perform pick-ups.
-
Freight handlers are people who sort and pack freight into warehouses.
-
Inventory managers - These are responsible for overseeing the stock of goods in warehouses.
-
Sales representatives - They sell products to customers.
-
Logistics coordinators - They plan and organize logistics operations.
-
Purchasing agents - They purchase goods and services needed for company operations.
-
Customer service representatives are available to answer customer calls and emails.
-
Shippers clerks - They process shipping order and issue bills.
-
Order fillers are people who fill orders based only on what was ordered.
-
Quality control inspectors (QCI) - They inspect all incoming and departing products for potential defects.
-
Other - Logistics has many other job opportunities, including transportation supervisors, logistics specialists, and cargo specialists.
How can we improve manufacturing efficiency?
First, we need to identify which factors are most critical in affecting production times. We must then find ways that we can improve these factors. If you don't know where to start, then think about which factor(s) have the biggest impact on production time. Once you've identified them, try to find solutions for each of those factors.
What is the importance of automation in manufacturing?
Not only is automation important for manufacturers, but it's also vital for service providers. Automation allows them to deliver services quicker and more efficiently. It helps them to lower costs by reducing human errors, and improving productivity.
What is the job of a manufacturer manager?
The manufacturing manager should ensure that every manufacturing process is efficient and effective. They should also be aware of any problems within the company and act accordingly.
They must also be able to communicate with sales and marketing departments.
They should also be knowledgeable about the latest trends in the industry so they can use this information for productivity and efficiency improvements.
What does it mean to warehouse?
A warehouse is an area where goods are stored before being sold. It can be an indoor space or an outdoor area. It may also be an indoor space or an outdoor area.
How can I learn about manufacturing?
The best way to learn about manufacturing is through hands-on experience. You can also read educational videos or take classes if this isn't possible.
Statistics
- According to the United Nations Industrial Development Organization (UNIDO), China is the top manufacturer worldwide by 2019 output, producing 28.7% of the total global manufacturing output, followed by the United States, Japan, Germany, and India.[52][53] (en.wikipedia.org)
- Job #1 is delivering the ordered product according to specifications: color, size, brand, and quantity. (netsuite.com)
- It's estimated that 10.8% of the U.S. GDP in 2020 was contributed to manufacturing. (investopedia.com)
- Many factories witnessed a 30% increase in output due to the shift to electric motors. (en.wikipedia.org)
- (2:04) MTO is a production technique wherein products are customized according to customer specifications, and production only starts after an order is received. (oracle.com)
External Links
How To
Six Sigma in Manufacturing:
Six Sigma refers to "the application and control of statistical processes (SPC) techniques in order to achieve continuous improvement." Motorola's Quality Improvement Department developed it at their Tokyo plant in Japan in 1986. The basic idea behind Six Sigma is to improve quality by improving processes through standardization and eliminating defects. Many companies have adopted Six Sigma in recent years because they believe that there are no perfect products and services. Six Sigma aims to reduce variation in the production's mean value. If you take a sample and compare it with the average, you will be able to determine how much of the production process is different from the norm. If there is a significant deviation from the norm, you will know that something needs to change.
Understanding how variability works in your company is the first step to Six Sigma. Once you've understood that, you'll want to identify sources of variation. Also, you will need to identify the sources of variation. Random variations happen when people make errors; systematic variations are caused externally. You could consider random variations if some widgets fall off the assembly lines. You might notice that your widgets always fall apart at the same place every time you put them together.
Once you identify the problem areas, it is time to create solutions. That solution might involve changing the way you do things or redesigning the process altogether. Once you have implemented the changes, it is important to test them again to ensure they work. If they don't work, you will need to go back to the drawing boards and create a new plan.