
Blue collar jobs are generally manual labor jobs. These jobs might be in the fields of agriculture, manufacturing, healthcare or hospitality. Some require some level or skill, such a plumber, electrician, etc. While others are less skilled. Blue collar jobs pay good salaries and provide great career growth.
The Fourth Industrial Revolution changes the employment market for manual workers. This revolution encompasses artificial intelligence, robotics and machine learning. To be successful, companies will need to have a new workforce with higher skills. It will also require that firms shift away from transactional relations and move towards more enduring relationships.
Therefore, many companies have to hire workers outside the United States. In certain cases, these workers may also be paid per-item. Others might be paid by the project. It is encouraging to see the demand for blue collar work rising.
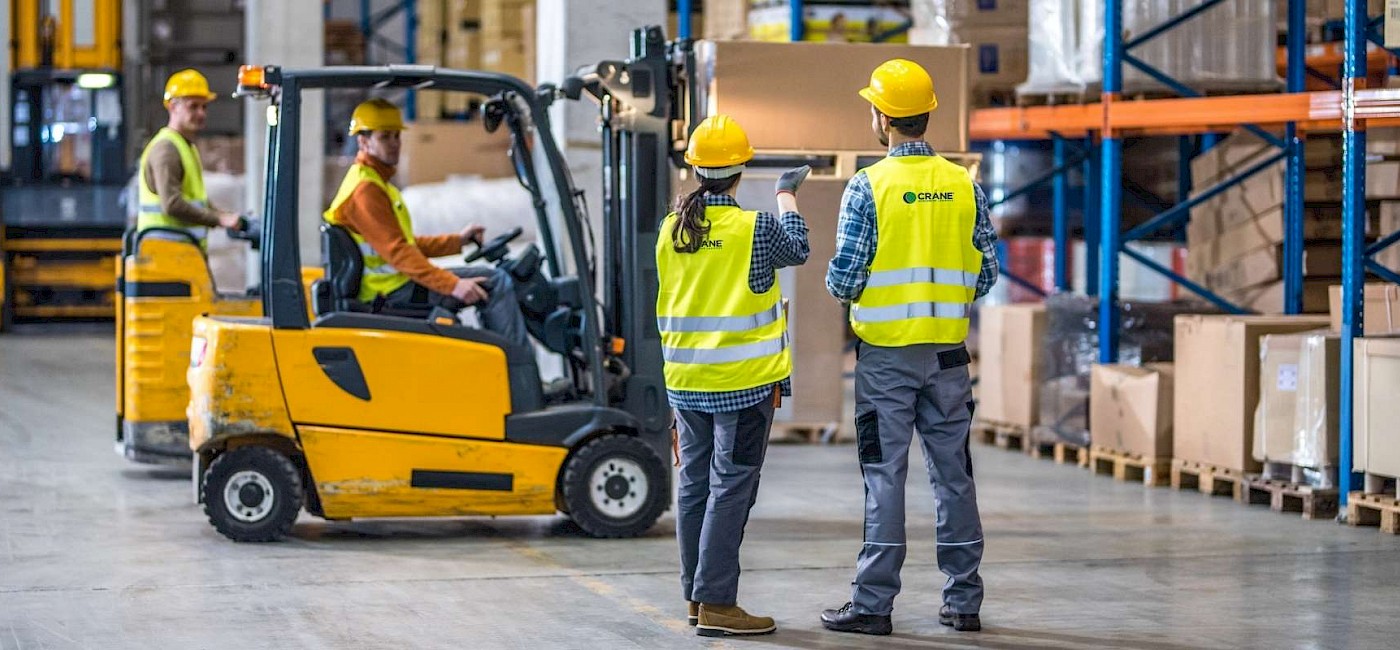
These jobs require some physical labor, but they are often better-paid than white collar work. Because these jobs are a good source of income, companies are willing to invest in training their employees. Some examples of these jobs are signal and track switching repairers, nuclear power reactor operators, and electrical and electronics repairers. These jobs require only a high school diploma, while others require on-the-job training.
It is also easier to find blue collar work than white collar job. A significant portion of Indian workers is blue-collar. India has approximately 210 million employees in the agriculture sector and 290 millions in the nonagricultural. The demand for blue collar workers is growing at a rapid pace.
The Fourth Industrial Revolution is also changing the way companies manage their blue-collar workforce. Firms are not only replacing manual jobs with digital jobs, but they also shift away from transactional relationships towards lasting ones. Firms can create stronger relationships and better productivity by prioritizing their employees.
They are also in high demand as blue collar workers, but they face different realities. They may be worried about the stability of their jobs, or about retiring. Blue collar workers can be optimistic about their prospects, regardless of any concerns. Actually, blue-collar employees are more likely to save for retirement. Additionally, blue collar jobs will likely increase in popularity as the economy improves.
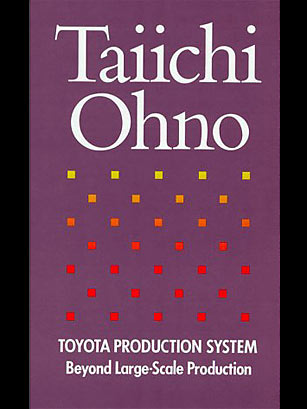
These jobs are also not in danger from automation. The Association for Manufacturing Technology actually found that for every job replaced by technology, five new jobs are created. Signal and track switch technicians earned $76,210 per year, the average salary.
Blue collar jobs are also increasingly better paid. The earnings of many blue collar jobs are well above the national average, making it an ideal option for those looking for a job with good pay. In addition, many blue collar jobs require a high degree of problem-solving skills, and are more than likely to provide good career growth.
FAQ
Why automate your factory?
Modern warehousing has seen automation take center stage. Increased demand for efficient and faster delivery has resulted in a rise in e-commerce.
Warehouses should be able adapt quickly to new needs. To do so, they must invest heavily in technology. Automation warehouses can bring many benefits. These are some of the benefits that automation can bring to warehouses:
-
Increases throughput/productivity
-
Reduces errors
-
Accuracy is improved
-
Safety Boosts
-
Eliminates bottlenecks
-
This allows companies to scale easily
-
Workers are more productive
-
This gives you visibility into what happens in the warehouse
-
Enhances customer experience
-
Improves employee satisfaction
-
This reduces downtime while increasing uptime
-
Ensures quality products are delivered on time
-
Eliminates human error
-
This helps to ensure compliance with regulations
Are there any Manufacturing Processes that we should know before we can learn about Logistics?
No. No. It is important to know about the manufacturing processes in order to understand how logistics works.
What skills should a production planner have?
To become a successful production planner, you need to be organized, flexible, and able to multitask. It is also important to be able communicate with colleagues and clients.
What does "warehouse" mean?
A warehouse, or storage facility, is where goods are stored prior to being sold. It can be an outdoor or indoor area. Sometimes, it can be both an indoor and outdoor space.
What is meant by manufacturing industries?
Manufacturing Industries are those businesses that make products for sale. The people who buy these products are called consumers. These companies use a variety processes such as distribution, retailing and management to accomplish their purpose. They manufacture goods from raw materials using machines and other equipment. This covers all types of manufactured goods including clothing, food, building supplies and furniture, as well as electronics, tools, machinery, vehicles and pharmaceuticals.
Are there ways to automate parts of manufacturing?
Yes! Yes! Automation has existed since ancient times. The Egyptians invented the wheel thousands of years ago. Today, robots assist in the assembly of lines.
Actually, robotics can be used in manufacturing for many purposes. They include:
-
Robots for assembly line
-
Robot welding
-
Robot painting
-
Robotics inspection
-
Robots create products
Manufacturing can also be automated in many other ways. For example, 3D printing allows us to make custom products without having to wait for weeks or months to get them manufactured.
How can manufacturing avoid production bottlenecks
Production bottlenecks can be avoided by ensuring that processes are running smoothly during the entire production process, starting with the receipt of an order and ending when the product ships.
This includes both planning for capacity and quality control.
This can be done by using continuous improvement techniques, such as Six Sigma.
Six Sigma management is a system that improves quality and reduces waste within your organization.
It seeks to eliminate variation and create consistency in your work.
Statistics
- You can multiply the result by 100 to get the total percent of monthly overhead. (investopedia.com)
- In 2021, an estimated 12.1 million Americans work in the manufacturing sector.6 (investopedia.com)
- Many factories witnessed a 30% increase in output due to the shift to electric motors. (en.wikipedia.org)
- In the United States, for example, manufacturing makes up 15% of the economic output. (twi-global.com)
- Job #1 is delivering the ordered product according to specifications: color, size, brand, and quantity. (netsuite.com)
External Links
How To
How to Use the Just In Time Method in Production
Just-intime (JIT), which is a method to minimize costs and maximize efficiency in business process, is one way. It is a process where you get the right amount of resources at the right moment when they are needed. This means that you only pay for what you actually use. Frederick Taylor first coined this term while working in the early 1900s as a foreman. He saw how overtime was paid to workers for work that was delayed. He then concluded that if he could ensure that workers had enough time to do their job before starting to work, this would improve productivity.
The idea behind JIT is that you should plan ahead and have everything ready so you don't waste money. It is important to look at your entire project from beginning to end and ensure that you have enough resources to handle any issues that may arise. You'll be prepared to handle any potential problems if you know in advance. This will ensure that you don't spend more money on things that aren't necessary.
There are different types of JIT methods:
-
Demand-driven: This is a type of JIT where you order the parts/materials needed for your project regularly. This will allow for you to track the material that you have left after using it. This will allow to you estimate the time it will take for more to be produced.
-
Inventory-based: This allows you to store the materials necessary for your projects in advance. This allows you predict the amount you can expect to sell.
-
Project-driven: This method allows you to set aside enough funds for your project. Once you have an idea of how much material you will need, you can purchase the necessary materials.
-
Resource-based JIT: This is the most popular form of JIT. This is where you assign resources based upon demand. For example, if there is a lot of work coming in, you will have more people assigned to them. If you don’t have many orders you will assign less people to the work.
-
Cost-based: This is similar to resource-based, except that here you're not just concerned about how many people you have but how much each person costs.
-
Price-based: This is similar to cost-based but instead of looking at individual workers' salaries, you look at the total company price.
-
Material-based: This is very similar to cost-based but instead of looking at total costs of the company you are concerned with how many raw materials you use on an average.
-
Time-based JIT is another form of resource-based JIT. Instead of worrying about how much each worker costs, you can focus on how long the project takes.
-
Quality-based JIT is another variant of resource-based JIT. Instead of worrying about the costs of each employee or how long it takes for something to be made, you should think about how quality your product is.
-
Value-based: This is one of the newest forms of JIT. In this instance, you are not concerned about the product's performance or meeting customer expectations. Instead, your focus is on the value you bring to the market.
-
Stock-based is an inventory-based system that measures the number of items produced at any given moment. It is used when production goals are met while inventory is kept to a minimum.
-
Just-intime (JIT), planning is a combination JIT management and supply chain management. It is the process of scheduling components' delivery as soon as they have been ordered. It's important as it reduces leadtimes and increases throughput.