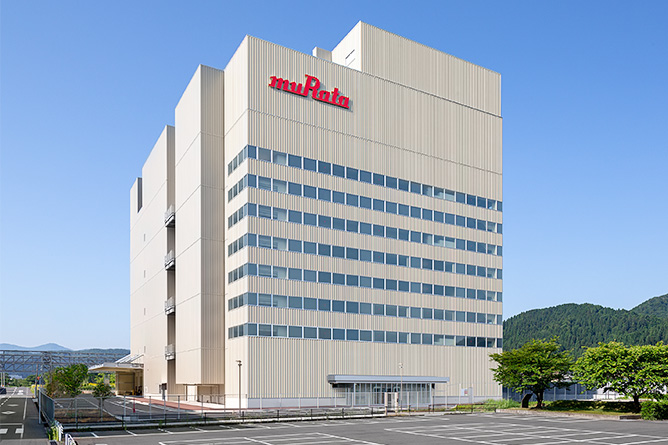
Being a logistics manger requires that you manage large quantities. You will also be responsible to ensure the delivery of products to customers in a timely manner. As a manager, you will have to oversee a group of employees that perform different tasks. You will also need to make sure that every company follows the rules and regulations in the industry. As such, you need to understand the logistics process and the different steps involved in its implementation. This is why it's important to get enough education.
Doing job
A logistics manager is responsible for planning and directing both reverse and comprehensive logistical functions. This role includes communicating freight shipping information to customers, negotiating rates for transportation, and supervising employees in the shipping department. The logistics manager analyses the environmental impact and implements and maintains carbon management systems. They also create and implement policies, training programs and other activities for personnel in the shipping department. They determine carrier selection and other transportation issues.
To succeed in this role, a logistics manager must have excellent organizational skills, a keen attention to detail, and a thorough knowledge of inventory systems. A logistics manager must be skilled at problem solving, be able manage employees, and adhere to company regulations. To be effective as a logistic manager, one must have great interpersonal and communication skills. A logistics manager should be proficient in information technology and strong analytical skills.
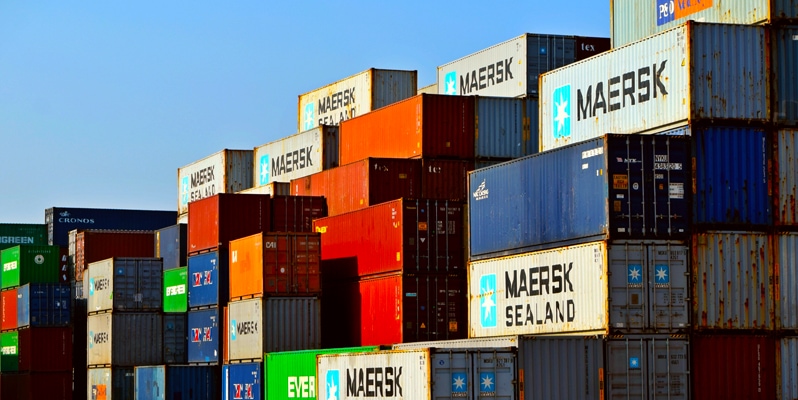
Education is required
If you're interested in a career within logistics, you might wonder what education is needed. The job is analytical and requires knowledge of mathematics as well as business principles. You must be detail-oriented and have worked with spreadsheet data and logistics systems. In order to fully understand supply chain management, you must be able and proficient with analytics software. Logistics managers will be able to spot inefficiencies and trouble areas by having a good understanding of the components of supply chains.
A bachelor's Degree in Logistics is not essential for this job. However, a Master's Degree in Supply Chain Management or Logistics may offer you more detailed training. You might have to spend less time in an entry-level job. This time can be used to gain valuable work experience. Find internship opportunities and work placement programmes. If you choose to obtain a master's degree, consider applying for positions in the field that require an MBA.
Salary
A logistics manager's pay can vary depending on his or her location. Logistics managers working for large companies or other large employers make the best-paying jobs. However, these sites don't always agree on which places pay the highest. The following are some of the highest-paying locations for a logistics manager. Other factors also influence the salary of logistics managers.
Experience is a must for logistics managers. Even though freshers are unlikely to be hired, part-time work is a good way to gain experience. If experience is not enough, they should consider getting an MBA. There are also a few other jobs in Logistics Management that they might find helpful. However, these positions may not always be the highest paying jobs in the industry.
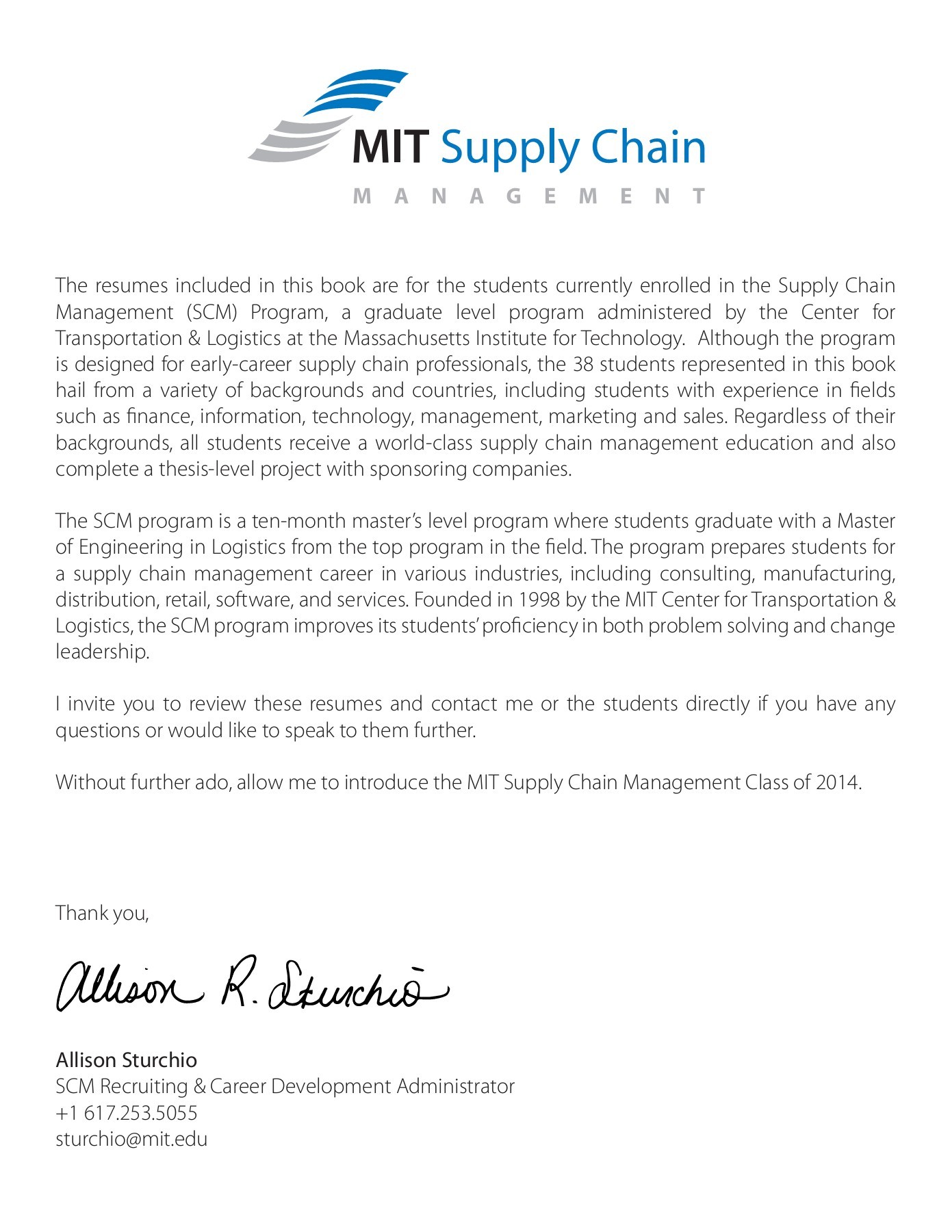
Job outlook
There are many paths to a career as a logistic manager. You can position yourself to maximize career growth opportunities depending on your education, training, experience, and other factors. Respondents ranked continuing education the best way to progress in their careers, according to the Logistics Management Annual Salary Survey. Additionally, 22% said that pursuing a degree or certificate in transportation or logistics is important for their career advancement. This makes logistics management a lucrative career choice for those with the right education and training.
In terms of job prospects, logisticians will find that there is a strong demand for skilled labor in the coming years. The job prospects for logisticians will improve over the next few years with a projected 7% increase in employment over 10 years. Technology like blockchain and public ledger tech will also have a significant impact on the supply chain. These technologies will affect the jobs of logistics managers in the coming years, as they will make the entire supply chain more efficient.
FAQ
How can I learn about manufacturing?
The best way to learn about manufacturing is through hands-on experience. You can also read educational videos or take classes if this isn't possible.
What is the distinction between Production Planning or Scheduling?
Production Planning (PP), also known as forecasting and identifying production capacities, is the process that determines what product needs to be produced at any particular time. This is done through forecasting demand and identifying production capacities.
Scheduling refers the process by which tasks are assigned dates so that they can all be completed within the given timeframe.
What are the responsibilities of a logistic manager?
Logistics managers are responsible for ensuring that all goods arrive in perfect condition and on time. This is done using his/her knowledge of the company's products. He/she should ensure that sufficient stock is available in order to meet customer demand.
What is the job of a production plan?
Production planners ensure all aspects of the project are delivered within time and budget. A production planner ensures that the service and product meet the client's expectations.
How does a Production Planner differ from a Project Manager?
The difference between a product planner and project manager is that a planer is typically the one who organizes and plans the entire project. A production planner, however, is mostly involved in the planning stages.
What is it like to manage a logistics company?
To run a successful logistics company, you need a lot knowledge and skills. You must have good communication skills to interact effectively with your clients and suppliers. You must be able analyze data and draw out conclusions. You must be able to work well under pressure and handle stressful situations. In order to innovate and create new ways to improve efficiency, creativity is essential. You must be a strong leader to motivate others and direct them to achieve organizational goals.
To meet tight deadlines, you must also be efficient and organized.
Statistics
- According to a Statista study, U.S. businesses spent $1.63 trillion on logistics in 2019, moving goods from origin to end user through various supply chain network segments. (netsuite.com)
- It's estimated that 10.8% of the U.S. GDP in 2020 was contributed to manufacturing. (investopedia.com)
- (2:04) MTO is a production technique wherein products are customized according to customer specifications, and production only starts after an order is received. (oracle.com)
- Many factories witnessed a 30% increase in output due to the shift to electric motors. (en.wikipedia.org)
- In 2021, an estimated 12.1 million Americans work in the manufacturing sector.6 (investopedia.com)
External Links
How To
How to Use the 5S to Increase Productivity In Manufacturing
5S stands for "Sort", 'Set In Order", 'Standardize', & Separate>. The 5S methodology was developed at Toyota Motor Corporation in 1954. It allows companies to improve their work environment, thereby achieving greater efficiency.
This method aims to standardize production processes so that they are repeatable, measurable and predictable. This means that daily tasks such as cleaning and sorting, storage, packing, labeling, and packaging are possible. Workers can be more productive by knowing what to expect.
Implementing 5S involves five steps: Sort, Set in Order, Standardize Separate, Store, and Each step requires a different action, which increases efficiency. If you sort items, it makes them easier to find later. When you set items in an order, you put items together. Once you have separated your inventory into groups and organized them, you will store these groups in easily accessible containers. Finally, label all containers correctly.
Employees must be able to critically examine their work practices. Employees must be able to see why they do what they do and find a way to achieve them without having to rely on their old methods. To implement the 5S system, employees must acquire new skills and techniques.
In addition to improving efficiency, the 5S system also increases morale and teamwork among employees. They will feel motivated to strive for higher levels of efficiency once they start to see results.