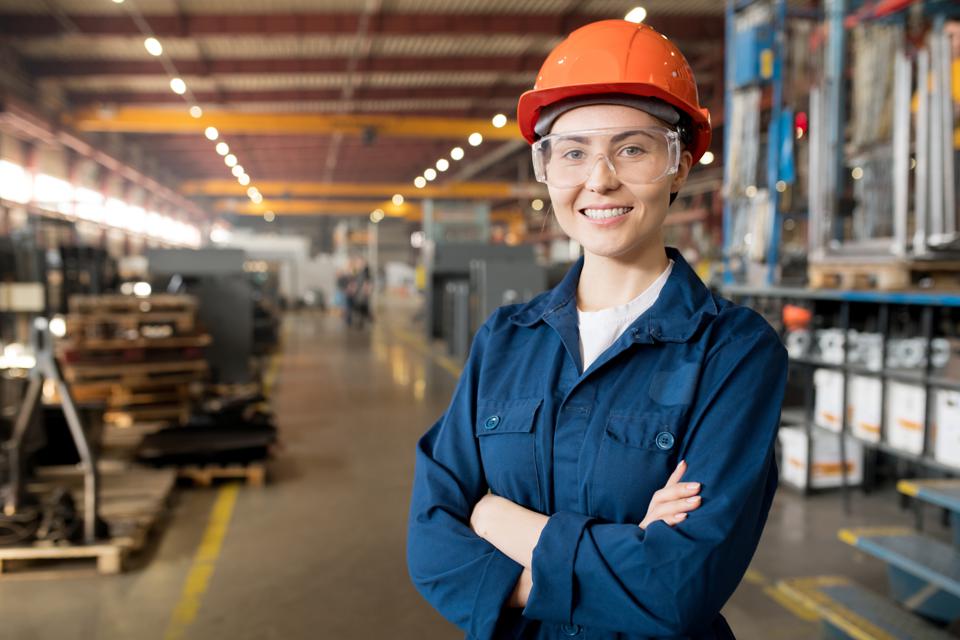
Interested in learning about the environmental engineers salary? Here's an overview of the average annual income for environmental engineers. You can also read the following to learn more about the job outlook, and what it takes to be a environmental engineer. In this article, we'll talk about the salary requirements and the employment outlook for environmental engineers. Average annual salaries for environmental engineers are $59,870. You should realize that you can earn more. A bachelor's degree is required in environmental engineering, or an equivalent.
Average annual salary
The average annual salary of environmental engineers is $96,820. It is expected to rise slightly faster than that for all other occupations. The number of job openings will increase by four percent in the next decade. Around 4,000 jobs are expected each year due to workers retiring or changing careers. Check out the salaries of similar jobs to see if your experience or degree matches what is required for an environmental engineer.
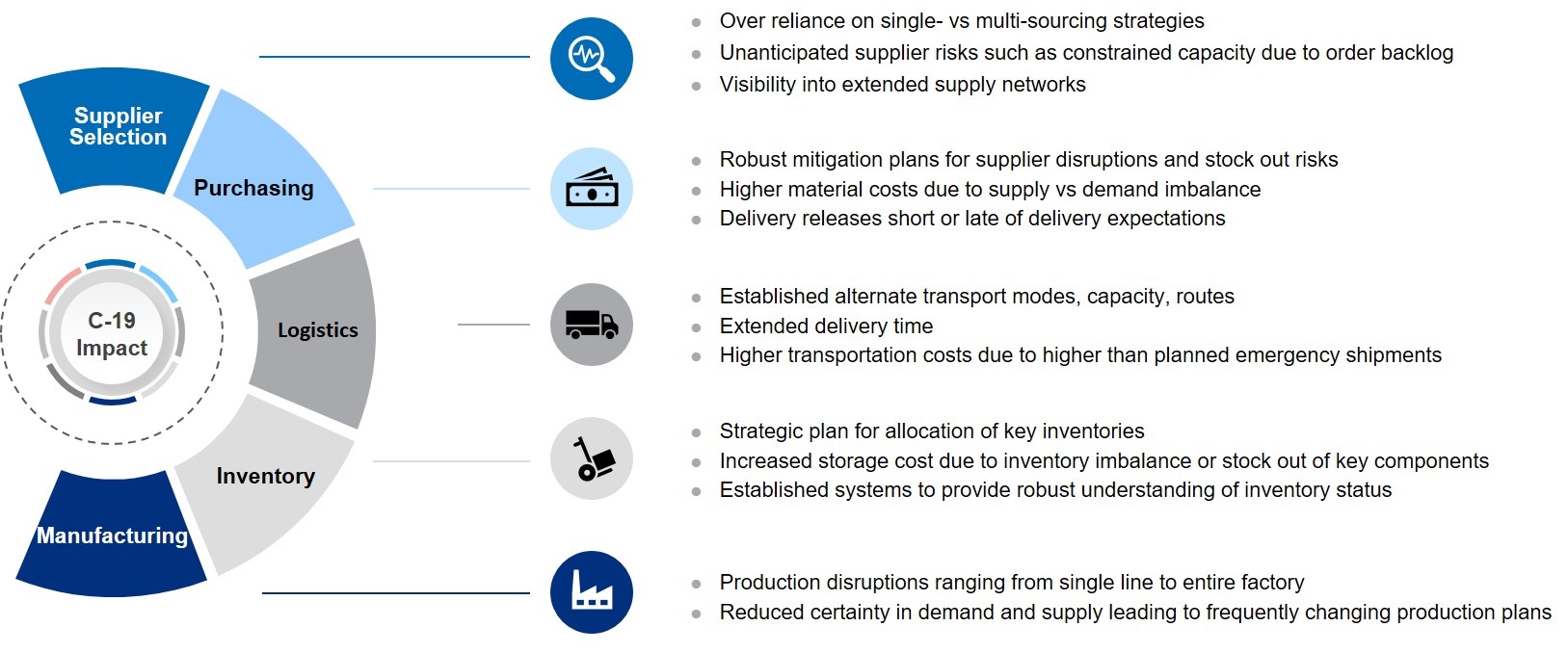
Although there isn't a single average salary for environmental engineers, the field has both meaning and financial work. The BLS reported an average annual wage of $101,640 for federal government environmental engineers, with the top 10 percent earning more than $128,000. However, there are variations within the occupation, with the highest-paid individuals making over $150,000 and the lowest-paid employees earning less than $67,000.
Employment outlook for environmental engineers
According to the Bureau of Labor Statistics the outlook for environmental engineers' employment is good. There will be an increase of 3.23% in the number of environmental engineer jobs from 2004 to 2024. That's slightly below the national average. There will be another 7,350 job openings in the near future. This is an increase of 1.63 percent per year. But, there is only moderate growth in job openings.
As people are more conscious of the environmental effects of human activity on the environment, the demand to be an environmental engineer will grow. This is due to an increasing awareness of environmental damage and the need to find alternatives to reduce the negative effects. This makes the job market for environmental engineering very attractive. According to U.S. Bureau of Labor Statistics in 2014, the demand for engineers is expected to increase by 12 per cent between 2014-2024. It is therefore a good time in your life to obtain a degree of environmental engineering.
To become an environmental engineer, you must meet the following requirements
After completing a bachelor's level in engineering, environmental engineers can sit for the Foundational Examination. This is a test that assesses their knowledge and understanding regarding the environment. These engineers are also called "engineer interns" or "engineer in training" until they can take the Principles and Practice of Engineering (PPE) exam. Although many states require that environmental engineers continue their education, most will accept previous licensure. Additionally, environmental engineers can earn board certification from the American Academy of Environmental Engineers (AACE), a mark of experience that demonstrates the level of expertise they have in a particular area of environmental engineering.
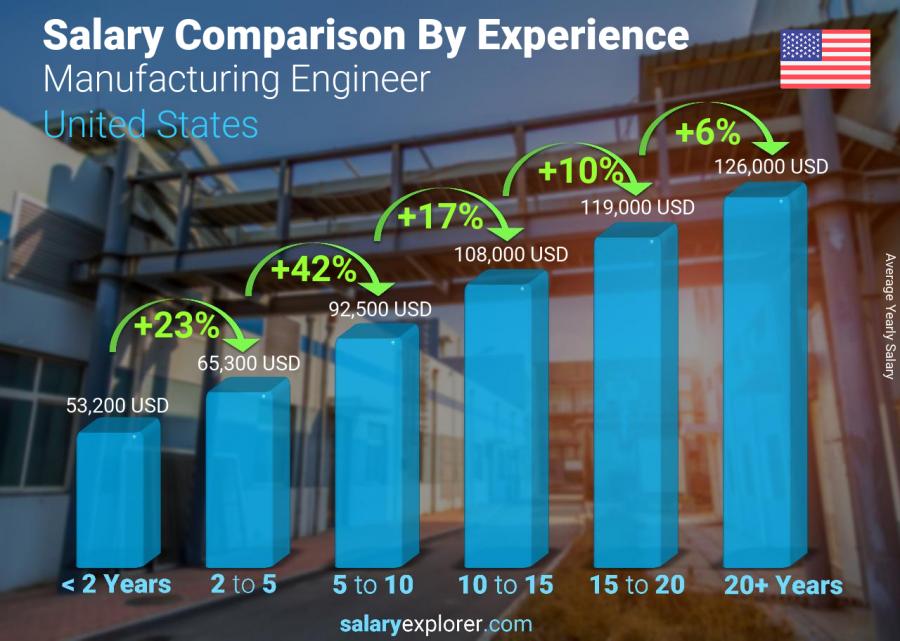
You will need other skills than a bachelor's. An environmental engineer must be creative and able see how their designs and solutions might affect larger systems. They must be able to communicate clearly with people and work independently. They should be able collaborate with many professionals, including scientists and engineers from other specialties. They must be able to communicate clearly.
FAQ
Is it possible to automate certain parts of manufacturing
Yes! Yes. Automation has been around since ancient time. The Egyptians created the wheel thousands years ago. We now use robots to help us with assembly lines.
In fact, there are several applications of robotics in manufacturing today. These include:
-
Robots for assembly line
-
Robot welding
-
Robot painting
-
Robotics inspection
-
Robots that produce products
Automation can be applied to manufacturing in many other ways. 3D printing, for example, allows us to create custom products without waiting for them to be made.
What skills does a production planner need?
To become a successful production planner, you need to be organized, flexible, and able to multitask. It is also important to be able communicate with colleagues and clients.
Why automate your warehouse
Modern warehousing has seen automation take center stage. E-commerce has brought increased demand for more efficient and quicker delivery times.
Warehouses have to be flexible to meet changing requirements. They must invest heavily in technology to do this. The benefits of automating warehouses are numerous. These are just a few reasons to invest in automation.
-
Increases throughput/productivity
-
Reduces errors
-
Improves accuracy
-
Safety increases
-
Eliminates bottlenecks
-
Companies can scale more easily
-
It makes workers more efficient
-
Provides visibility into everything that happens in the warehouse
-
Enhances customer experience
-
Improves employee satisfaction
-
Reducing downtime and increasing uptime
-
High quality products delivered on-time
-
Eliminates human error
-
Helps ensure compliance with regulations
What is production planning?
Production Planning refers to the development of a plan for every aspect of production. This document is designed to make sure everything is ready for when you're ready to shoot. This document should also include information on how to get the best result on set. It should include information about shooting locations, casting lists, crew details, equipment requirements, and shooting schedules.
The first step in filming is to define what you want. You may have decided where to shoot or even specific locations you want to use. Once you have determined your scenes and locations, it is time to start figuring out the elements that you will need for each scene. Perhaps you have decided that you need to buy a car but aren't sure which model. If this is the case, you might start searching online for car models and then narrow your options by selecting from different makes.
Once you have found the right vehicle, you can think about adding accessories. What about additional seating? Or maybe you just need someone to push the car around. You may want to change the interior's color from black or white. These questions will help you determine the exact look and feel of your car. Also, think about what kind of shots you would like to capture. Do you want to film close-ups, or wider angles? Maybe the engine or steering wheel is what you are looking to film. This will allow you to determine the type of car you want.
Once you have determined all of the above, you can move on to creating a schedule. You can create a schedule that will outline when you must start and finish your shoots. The schedule will show you when to get there, what time to leave, and when to return home. Everyone knows exactly what they should do and when. If you need to hire extra staff, you can make sure you book them in advance. It is not worth hiring someone who won’t show up because you didn’t tell him.
When creating your schedule, you will also need to consider the number of days you need to film. Some projects are quick and easy, while others take weeks. It is important to consider whether you require more than one photo per day when you create your schedule. Shooting multiple takes over the same location will increase costs and take longer to complete. If you are unsure if you need multiple takes, it is better to err on the side of caution and shoot fewer takes rather than risk wasting money.
Budgeting is another crucial aspect of production plan. A realistic budget will help you work within your means. It is possible to reduce the budget at any time if you experience unexpected problems. It is important to not overestimate how much you will spend. You will end up spending less money if you underestimate the cost of something.
Production planning is a complicated process. But once you understand how everything works together, it becomes much easier to plan future project.
What are the requirements to start a logistics business?
To be a successful businessman in logistics, you will need many skills and knowledge. For clients and suppliers to be successful, you need to have excellent communication skills. You must be able analyze data and draw out conclusions. You need to be able work under pressure and manage stressful situations. To increase efficiency and creativity, you need to be creative. To motivate and guide your team towards reaching organizational goals, you must have strong leadership skills.
To meet tight deadlines, you must also be efficient and organized.
What are manufacturing and logistic?
Manufacturing is the production of goods using raw materials. Logistics includes all aspects related to supply chain management, such as procurement, distribution planning, inventory control and transportation. Sometimes manufacturing and logistics are combined to refer to a wider term that includes both the process of creating products as well as their delivery to customers.
What is the role of a production manager?
Production planners ensure that all project aspects are completed on time, within budget and within the scope. They ensure that the product or service is of high quality and meets client requirements.
Statistics
- [54][55] These are the top 50 countries by the total value of manufacturing output in US dollars for its noted year according to World Bank.[56] (en.wikipedia.org)
- (2:04) MTO is a production technique wherein products are customized according to customer specifications, and production only starts after an order is received. (oracle.com)
- You can multiply the result by 100 to get the total percent of monthly overhead. (investopedia.com)
- In 2021, an estimated 12.1 million Americans work in the manufacturing sector.6 (investopedia.com)
- Many factories witnessed a 30% increase in output due to the shift to electric motors. (en.wikipedia.org)
External Links
How To
How to use the Just-In Time Method in Production
Just-intime (JIT), a method used to lower costs and improve efficiency in business processes, is called just-in-time. It's a way to ensure that you get the right resources at just the right time. This means you only pay what you use. Frederick Taylor was the first to coin this term. He developed it while working as a foreman during the early 1900s. Taylor observed that overtime was paid to workers if they were late in working. He decided to ensure workers have enough time to do their jobs before starting work to improve productivity.
The idea behind JIT is that you should plan ahead and have everything ready so you don't waste money. The entire project should be looked at from start to finish. You need to ensure you have enough resources to tackle any issues that might arise. You can anticipate problems and have enough equipment and people available to fix them. This way, you won't end up paying extra money for things that weren't really necessary.
There are several types of JIT techniques:
-
Demand-driven JIT: This is a JIT that allows you to regularly order the parts/materials necessary for your project. This will allow you to track how much material you have left over after using it. This will allow you to calculate how long it will take to make more.
-
Inventory-based: This type allows you to stock the materials needed for your projects ahead of time. This allows for you to anticipate how much you can sell.
-
Project-driven: This method allows you to set aside enough funds for your project. You will be able to purchase the right amount of materials if you know what you need.
-
Resource-based JIT : This is probably the most popular type of JIT. You assign certain resources based off demand. For example, if there is a lot of work coming in, you will have more people assigned to them. If you don't receive many orders, then you'll assign fewer employees to handle the load.
-
Cost-based: This is the same as resource-based except that you don't care how many people there are but how much each one of them costs.
-
Price-based pricing: This is similar in concept to cost-based but instead you look at how much each worker costs, it looks at the overall company's price.
-
Material-based is an alternative to cost-based. Instead of looking at the total cost in the company, this method focuses on the average amount of raw materials that you consume.
-
Time-based JIT: This is another variant of resource-based JIT. Instead of focusing on the cost of each employee, you will focus on the time it takes to complete a project.
-
Quality-based JIT - This is another form of resource-based JIT. Instead of looking at the labor costs and time it takes to make a product, think about its quality.
-
Value-based JIT: One of the most recent forms of JIT. In this instance, you are not concerned about the product's performance or meeting customer expectations. Instead, your focus is on the value you bring to the market.
-
Stock-based: This is an inventory-based method that focuses on the actual number of items being produced at any given time. It is used when production goals are met while inventory is kept to a minimum.
-
Just-in time (JIT), planning: This is a combination JIT/supply chain management. It is the process that schedules the delivery of components within a short time of their order. This is important as it reduces lead time and increases throughput.