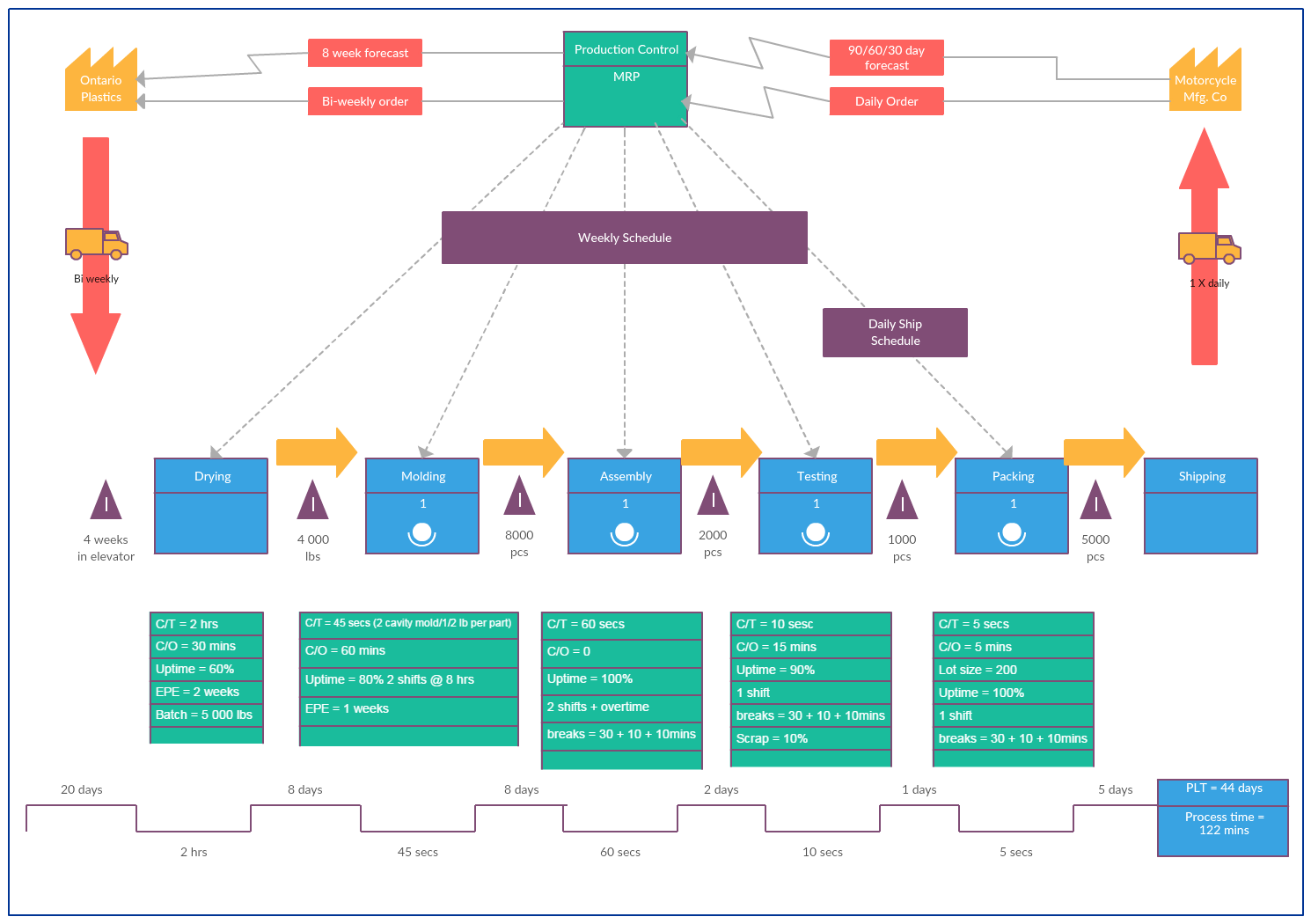
Occasionally, things go wrong, and we have to determine what caused them. These moments are when we turn to a process called the five whys, which is all about asking a series of questions to discover the root cause of a problem.
The 5 Whys can help teams solve problems by helping them communicate. It helps to foster curiosity and help teams understand each others' perspectives, so they can work with one another to find solutions. It is also used as a back-up interrogation method when team member are unsure of why a particular issue has occurred or what should be done about it.
What is the Five Whys Method?
The five whys method is a simple, but effective way of discovering the root causes behind a problem. This technique is best used to resolve simple or moderate problems, but it can also be applied in more complex situations.
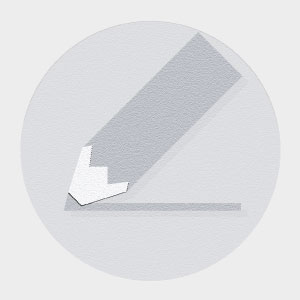
Depending on the type of problem, you may need to ask more than 5 whys. It is important to remember this when the root cause of a problem can be multiple.
The 5 Whys Method: How to Use it
To complete a five-whys analysis successfully, you need to first assemble a group of people who have experience with the problem. People from various departments and industries can be included. They will have a wider range of ideas and new perspectives to help uncover the problem's root cause.
After the team has been assembled, the members should begin by discussing the issue and asking the five Whys questions. This will allow them to determine the root cause and whether there is a solution that can be implemented immediately or if a longer-term countermeasure should be taken.
Next, they must carefully review each question and determine if a reasonable reply is produced. This is an essential step as it gives them the confidence to know that they will be able to complete a successful analysis.
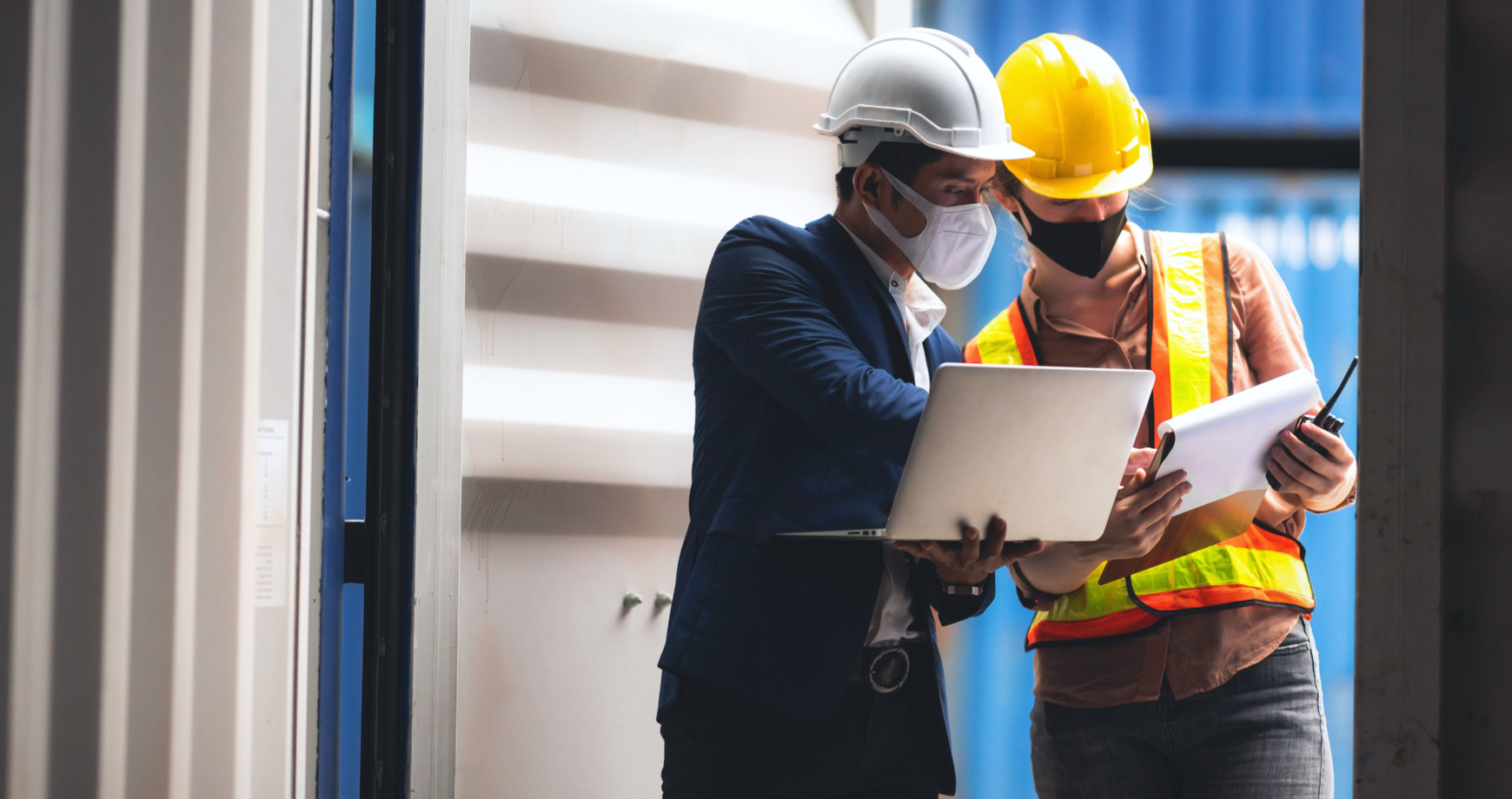
They should continue to ask the five whys until they are able to determine the root cause of the issue and come up with a list of countermeasures that will prevent the issue from occurring again in the future. They should then assign each of these corrective actions to the member of the team that can be held responsible for them.
It is possible to use the five Whys as a tool to help you determine the root cause for any issue that may be causing problems in your organization. It is most effective when used with other tools to understand root causes, like FMEA analysis or cause-and effect analysis.
FAQ
What is the difference in Production Planning and Scheduling, you ask?
Production Planning (PP), or production planning, is the process by which you determine what products are needed at any given time. Forecasting and identifying production capacity are two key elements to this process.
Scheduling involves the assignment of dates and times to tasks in order to complete them within the timeframe.
What are the 7 Rs of logistics?
The acronym 7Rs of Logistics refers to the seven core principles of logistics management. It was created by the International Association of Business Logisticians and published in 2004 under its "Seven Principles of Logistics Management".
The acronym is composed of the following letters.
-
Responsible – ensure that all actions are legal and don't cause harm to anyone else.
-
Reliable - You can have confidence that you will fulfill your promises.
-
Reasonable - use resources efficiently and don't waste them.
-
Realistic - Take into consideration all aspects of operations including cost-effectiveness, environmental impact, and other factors.
-
Respectful: Treat others with fairness and equity
-
Resourceful - look for opportunities to save money and increase productivity.
-
Recognizable provides value-added products and services to customers
Is automation necessary in manufacturing?
Automating is not just important for manufacturers, but also for service providers. They can provide services more quickly and efficiently thanks to automation. They can also reduce their costs by reducing human error and improving productivity.
What is the role and responsibility of a Production Planner?
A production planner makes sure all project elements are delivered on schedule, within budget, as well as within the agreed scope. They ensure that the product or service is of high quality and meets client requirements.
What is manufacturing and logistics?
Manufacturing is the production of goods using raw materials. Logistics encompasses the management of all aspects associated with supply chain activities such as procurement, production planning, distribution and inventory control. It also includes customer service. Logistics and manufacturing are often referred to as one thing. It encompasses both the creation of products and their delivery to customers.
What is the role of a logistics manager
A logistics manager ensures that all goods are delivered on time and without damage. This is done using his/her knowledge of the company's products. He/she must also ensure sufficient stock to meet the demand.
Statistics
- Job #1 is delivering the ordered product according to specifications: color, size, brand, and quantity. (netsuite.com)
- According to a Statista study, U.S. businesses spent $1.63 trillion on logistics in 2019, moving goods from origin to end user through various supply chain network segments. (netsuite.com)
- Many factories witnessed a 30% increase in output due to the shift to electric motors. (en.wikipedia.org)
- (2:04) MTO is a production technique wherein products are customized according to customer specifications, and production only starts after an order is received. (oracle.com)
- You can multiply the result by 100 to get the total percent of monthly overhead. (investopedia.com)
External Links
How To
How to Use 5S to Increase Productivity in Manufacturing
5S stands for "Sort", "Set In Order", "Standardize", "Separate" and "Store". Toyota Motor Corporation was the first to develop the 5S approach in 1954. This methodology helps companies improve their work environment to increase efficiency.
This method aims to standardize production processes so that they are repeatable, measurable and predictable. This means that tasks such as cleaning, sorting, storing, packing, and labeling are performed daily. Through these actions, workers can perform their jobs more efficiently because they know what to expect from them.
Five steps are required to implement 5S: Sort, Set In Order, Standardize. Separate. Each step requires a different action to increase efficiency. For example, when you sort things, you make them easy to find later. When you arrange items, you place them together. Then, after you separate your inventory into groups, you store those groups in containers that are easy to access. Labeling your containers will ensure that everything is correctly labeled.
Employees need to reflect on how they do their jobs. Employees must be able to see why they do what they do and find a way to achieve them without having to rely on their old methods. In order to use the 5S system effectively, they must be able to learn new skills.
The 5S Method not only improves efficiency, but it also helps employees to be more productive and happier. They are more motivated to achieve higher efficiency levels as they start to see improvement.