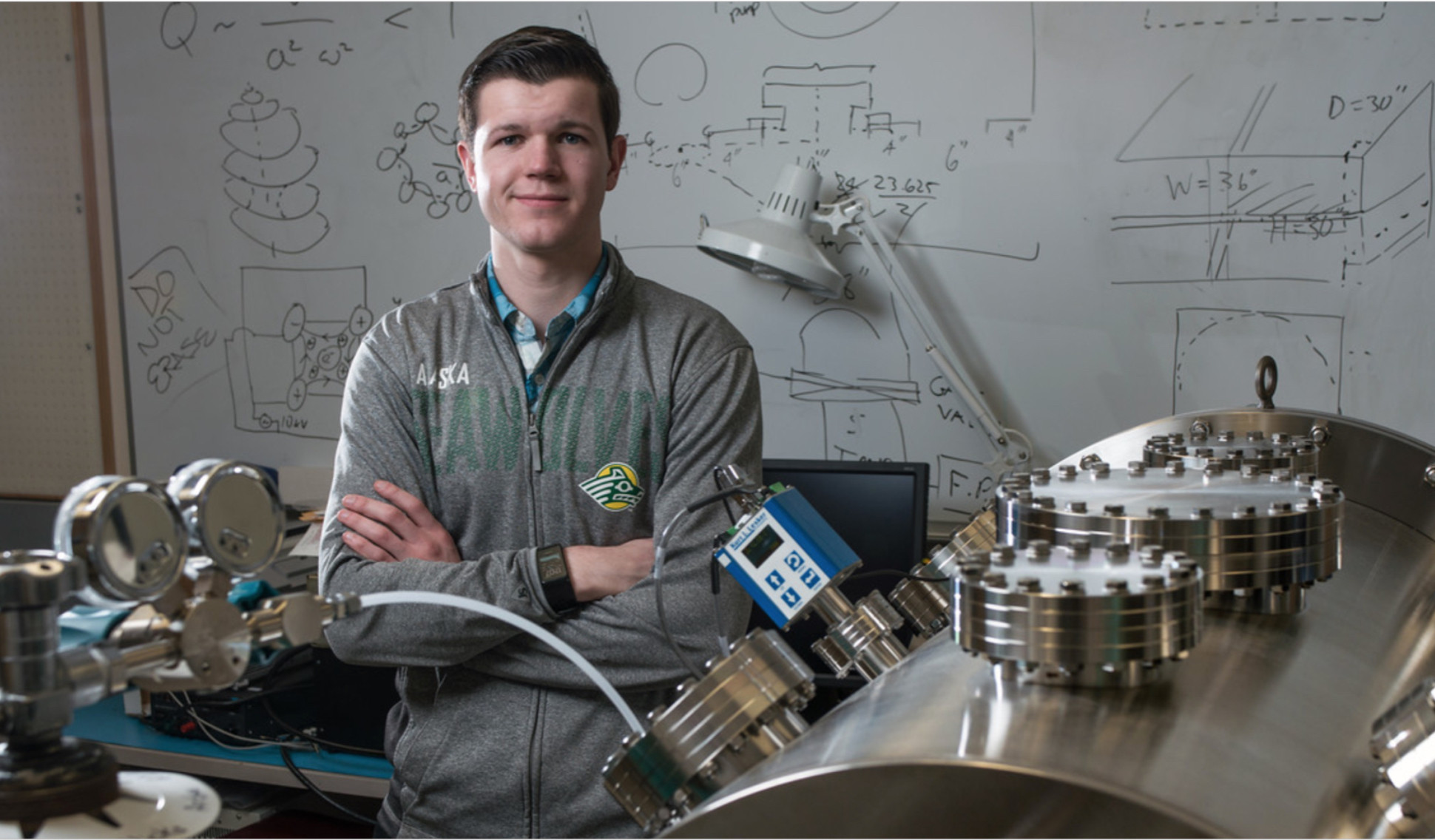
There are several good reasons to be an engineer. These include the satisfaction of solving problems in the real world and the chance to help people. The engineering field is one that's growing and has high-paying careers.
The average engineering technician salary is $52,171 a year. This is 1% higher than the national average of $51,860 and equals $2,174/check for each hour worked. Pay is based upon an estimated federal rate of 22%.
They assist the engineers in the design, development, and testing of machinery, appliances and equipment. They are often involved in the manufacturing process in factories, or in the development phase in research and development laboratories before production. They might analyze product design and create layouts of the parts to be produced. They also may inspect test equipment for quality and calibrate new devices before they are put into use.
Other engineering technicians use CAD software to transform designs created by architects and engineers into technical drawings. Other responsibilities include entering job specs into the CAD software, making adjustments to drawings already created and completing report.
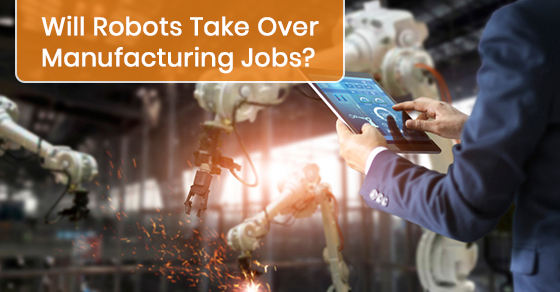
Most employers prefer to hire individuals with these degrees because they have more experience and training in the field of engineering technology than those without. Most employers prefer to hire individuals who have earned these degrees because they have more experience and training in the field of engineering technology than those with less education.
Manufacturing engineering technologists' salaries range between $32,295 and $94,100. With a median wage of $61,260, the salary range is wide. These employees range in age from 26 to 31 years, with approximately a third of them falling between 31 and 36 years.
They work in the manufacturing sector, assisting engineers with issues that could affect the manufacturing process or layout of a facility. These employees can be found in manufacturers of consumer products, food, industrial machines, and more.
The majority of them are employed full-time, and they're expected to put in more than forty hours per week. The organization in which they are employed will also determine their duties.
Under the supervision a chemical engineer, chemical engineers work as technologists to perform experiments, develop chemical process and do inventory. Also, they may be required to estimate manufacturing costs.
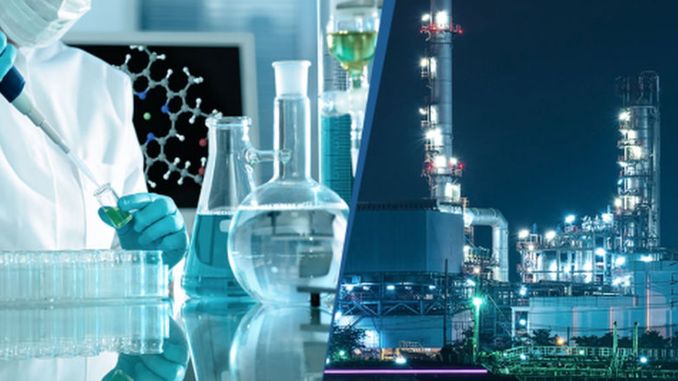
The group has a younger workforce, and the employment rate is lower than that of the total labor force. However, jobs are expected to increase slightly until 2031. This occupation was reported to have a salary median of $60,220 by the BLS in May 2021.
These jobs offer a chance to learn about electronic components and technologies. These positions are very popular with recent graduates. You can find them in manufacturing, research laboratories or engineering services.
The average engineering technologist salary in this profession is a competitive one, and it's important to consider the salary potential before accepting a job offer. You can increase your salary in several ways. These include changing employers to one that pays more, getting advanced education and managing your experiences.
FAQ
What are the differences between these four types?
Manufacturing refers the process of turning raw materials into useful products with machines and processes. It involves many different activities such as designing, building, testing, packaging, shipping, selling, servicing, etc.
How can we reduce manufacturing overproduction?
The key to reducing overproduction lies in developing better ways to manage inventory. This would reduce the time spent on unproductive activities like purchasing, storing and maintaining excess stock. By doing this, we could free up resources for other productive tasks.
A Kanban system is one way to achieve this. A Kanban board is a visual display used to track work in progress. Kanban systems are where work items travel through a series of states until reaching their final destination. Each state represents an individual priority level.
If work is moving from one stage to the other, then the current task can be completed and moved on to the next. However, if a task is still at the beginning stages, it will remain so until it reaches the end of the process.
This keeps work moving and ensures no work is lost. Managers can view the Kanban board to see how much work they have done. This information allows managers to adjust their workflow based off real-time data.
Lean manufacturing is another way to manage inventory levels. Lean manufacturing emphasizes eliminating waste in all phases of production. Anything that does nothing to add value to a product is waste. There are several types of waste that you might encounter:
-
Overproduction
-
Inventory
-
Unnecessary packaging
-
Materials in excess
Manufacturers can reduce their costs and improve their efficiency by using these ideas.
What skills should a production planner have?
You must be flexible and organized to become a productive production planner. Communication skills are essential to ensure that you can communicate effectively with clients, colleagues, and customers.
Statistics
- According to a Statista study, U.S. businesses spent $1.63 trillion on logistics in 2019, moving goods from origin to end user through various supply chain network segments. (netsuite.com)
- Many factories witnessed a 30% increase in output due to the shift to electric motors. (en.wikipedia.org)
- According to the United Nations Industrial Development Organization (UNIDO), China is the top manufacturer worldwide by 2019 output, producing 28.7% of the total global manufacturing output, followed by the United States, Japan, Germany, and India.[52][53] (en.wikipedia.org)
- [54][55] These are the top 50 countries by the total value of manufacturing output in US dollars for its noted year according to World Bank.[56] (en.wikipedia.org)
- In the United States, for example, manufacturing makes up 15% of the economic output. (twi-global.com)
External Links
How To
How to Use the Just In Time Method in Production
Just-intime (JIT), which is a method to minimize costs and maximize efficiency in business process, is one way. It is a process where you get the right amount of resources at the right moment when they are needed. This means that you only pay the amount you actually use. Frederick Taylor, a 1900s foreman, first coined the term. He observed how workers were paid overtime if there were delays in their work. He concluded that if workers were given enough time before they start work, productivity would increase.
JIT is about planning ahead. You should have all the necessary resources ready to go so that you don’t waste money. You should also look at the entire project from start to finish and make sure that you have sufficient resources available to deal with any problems that arise during the course of your project. You'll be prepared to handle any potential problems if you know in advance. This way you won't be spending more on things that aren’t really needed.
There are many types of JIT methods.
-
Demand-driven: This is a type of JIT where you order the parts/materials needed for your project regularly. This will allow for you to track the material that you have left after using it. This will allow to you estimate the time it will take for more to be produced.
-
Inventory-based : You can stock the materials you need in advance. This allows for you to anticipate how much you can sell.
-
Project-driven: This approach involves setting aside sufficient funds to cover your project's costs. Knowing how much money you have available will help you purchase the correct amount of materials.
-
Resource-based JIT is the most widespread form. Here you can allocate certain resources based purely on demand. For instance, if you have a lot of orders coming in, you'll assign more people to handle them. If you don’t have many orders you will assign less people to the work.
-
Cost-based: This approach is very similar to resource-based. However, you don't just care about the number of people you have; you also need to consider how much each person will cost.
-
Price-based pricing: This is similar in concept to cost-based but instead you look at how much each worker costs, it looks at the overall company's price.
-
Material-based: This approach is similar to cost-based. However, instead of looking at the total cost for the company, you look at how much you spend on average on raw materials.
-
Time-based: This is another variation of resource-based JIT. Instead of focusing on the cost of each employee, you will focus on the time it takes to complete a project.
-
Quality-based JIT: This is another variation of resource based JIT. Instead of looking at the labor costs and time it takes to make a product, think about its quality.
-
Value-based JIT: This is the latest form of JIT. In this scenario, you're not concerned about how products perform or whether customers expect them to meet their expectations. Instead, your goal is to add value to the market.
-
Stock-based is an inventory-based system that measures the number of items produced at any given moment. This is used to increase production and minimize inventory.
-
Just-in-time (JIT) planning: This is a combination of JIT and supply chain management. It is the process of scheduling components' delivery as soon as they have been ordered. It reduces lead times and improves throughput.