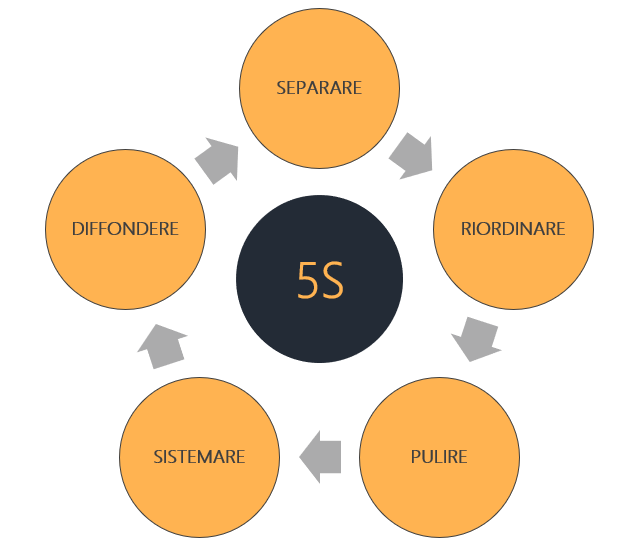
Many sources can cause supply chain disruptions. Examples include natural disasters as well as product recalls or transportation delays. These disruptions may cause price increases and margin decreases. To continue production, some companies may need a change in their sourcing strategies. Companies will often need to reevaluate their supply chains, diversify production, and audit current inventories in order to be prepared for disruptions.
Various industries, such as transportation, electronics, and pharmaceuticals, have experienced supply chain disruptions. In some cases the disruption was caused by an internal issue within a company. Other times it was caused by a global problem. One example is a pandemic that caused widespread health disruptions across several countries. It also had a negative impact on the retail sector. The pandemic forced governments to adopt policies to prevent the spread of the disease.
Pandemics can have a devastating effect on a company's workforce and distribution systems, as well as their manufacturing processes. The production of vital products can be affected, so companies will need a re-evaluation and adjustment to their production and supply chain. Depending on the severity, the impact can last several weeks to months. Businesses will need an inventory review and capital reallocation if a pandemic happens.
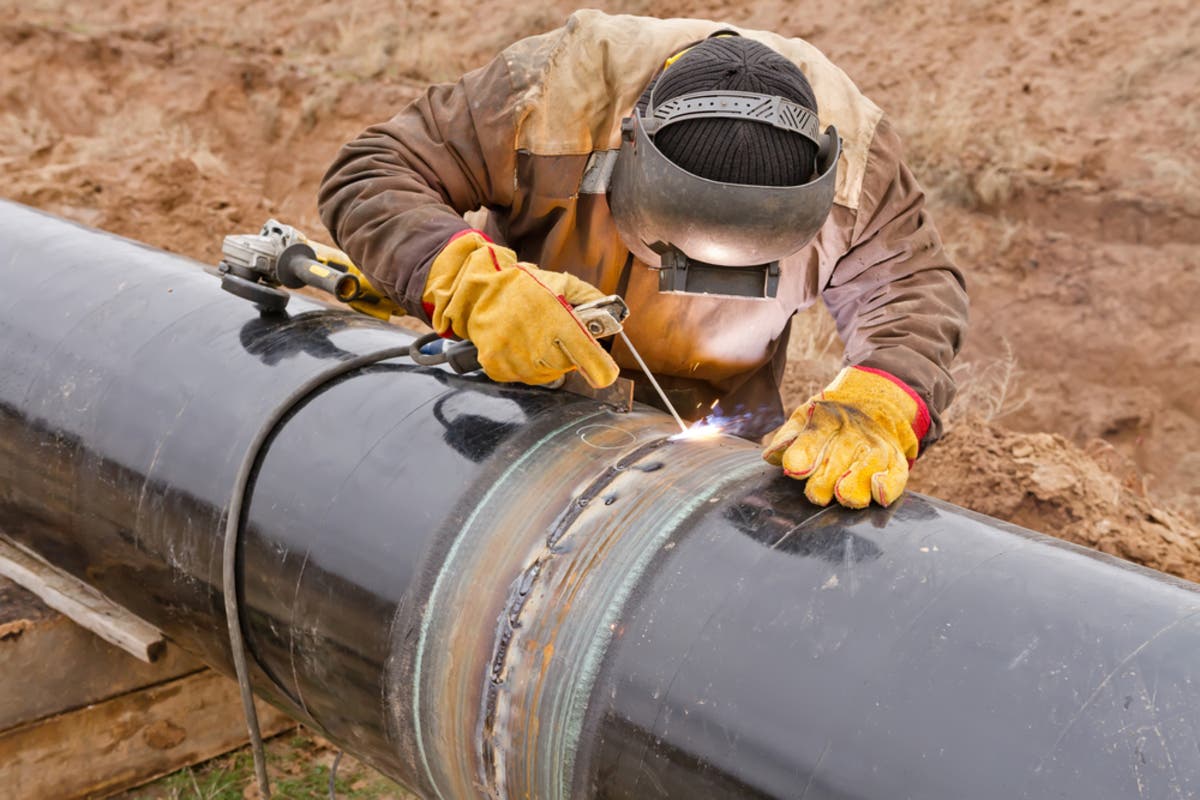
Disruption in any part of the supply chains can occur. In most cases, disruptions to the supply chain will impact the demand more than the supply side. If the supply side of an epidemic is disrupted, however, the ripple effect will affect the whole economy.
Supply chain disruptions are not only disruptive but can also have significant impacts on a business's bottom line. While seasonal fluctuations are easy to spot, it's more difficult to predict the rapid shifts in consumer behavior. A predictive analytics tool is a great way to avoid these problems.
Labor shortages are another common cause of disruption in supply chains. Unreliable suppliers can cause companies to lose productivity. Also, a breakdown of a machine can cause disruption to the entire operation.
Some of the most common causes of supply chain disruptions are natural disasters, market fluctuations, and geopolitical instability. Natural disasters are extremely expensive, and they are known to disrupt the global supply chain. Other causes of supply chain disruption include a power outage, telecommunications blackout, and border closures. Companies may have to store large quantities of stock in order to protect their businesses.
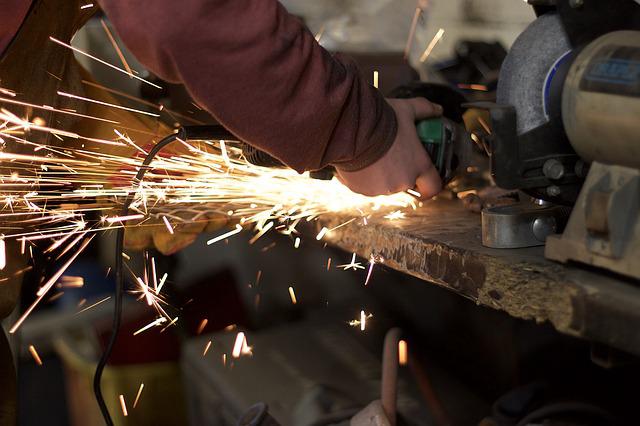
Supply chain disruptions have a relatively low impact, according to general rule. Companies must take immediate action when they notice a disruption. Most companies will have to do this at some time. It is important to identify issues quickly in order to reduce conflict.
Ernest & Young LLP surveyed 720 companies and found that 77% had experienced disruptions. 57% of those affected reported adverse consequences. Some problems can be quickly fixed, but others will require a more strategic approach.
FAQ
What is the role of a manager in manufacturing?
A manufacturing manager must ensure that all manufacturing processes are efficient and effective. They must also be alert to any potential problems and take appropriate action.
They must also be able to communicate with sales and marketing departments.
They should also be aware of the latest trends in their industry and be able to use this information to help improve productivity and efficiency.
What are the 4 types of manufacturing?
Manufacturing is the process that transforms raw materials into useful products. It involves many different activities such as designing, building, testing, packaging, shipping, selling, servicing, etc.
How can manufacturing avoid production bottlenecks
You can avoid bottlenecks in production by making sure that everything runs smoothly throughout the production cycle, from the moment you receive an order to the moment the product is shipped.
This includes planning for both capacity requirements and quality control measures.
Continuous improvement techniques such Six Sigma can help you achieve this.
Six Sigma Management System is a method to increase quality and reduce waste throughout your organization.
It emphasizes consistency and eliminating variance in your work.
Why automate your warehouse
Modern warehouses have become more dependent on automation. E-commerce has brought increased demand for more efficient and quicker delivery times.
Warehouses need to adapt quickly to meet changing needs. Technology investment is necessary to enable warehouses to respond quickly to changing demands. Automation of warehouses offers many benefits. These are just a few reasons to invest in automation.
-
Increases throughput/productivity
-
Reduces errors
-
Improves accuracy
-
Safety is boosted
-
Eliminates bottlenecks
-
Companies can scale up more easily
-
Makes workers more efficient
-
Provides visibility into everything that happens in the warehouse
-
Enhances customer experience
-
Improves employee satisfaction
-
This reduces downtime while increasing uptime
-
Quality products delivered on time
-
Eliminates human error
-
It ensures compliance with regulations
How can manufacturing overproduction be reduced?
It is essential to find better ways to manage inventory to reduce overproduction. This would decrease the time that is spent on inefficient activities like purchasing, storing, or maintaining excess stock. By doing this, we could free up resources for other productive tasks.
One way to do this is to adopt a Kanban system. A Kanbanboard is a visual tool that allows you to keep track of the work being done. In a Kanban system, work items move through a sequence of states until they reach their final destination. Each state represents a different priority.
To illustrate, work can move from one stage or another when it is complete enough for it to be moved to a new stage. But if a task remains in the beginning stages it will stay that way until it reaches its end.
This helps to keep work moving forward while ensuring that no work is left behind. Managers can see how much work has been done and the status of each task at any time with a Kanban Board. This information allows them to adjust their workflow based on real-time data.
Another way to control inventory levels is to implement lean manufacturing. Lean manufacturing emphasizes eliminating waste in all phases of production. Anything that doesn't add value to the product is considered waste. Here are some examples of common types.
-
Overproduction
-
Inventory
-
Unnecessary packaging
-
Excess materials
Manufacturers can increase efficiency and decrease costs by implementing these ideas.
What are the 7 Rs of logistics?
The acronym 7Rs of Logistics refers to the seven core principles of logistics management. It was developed and published by the International Association of Business Logisticians in 2004 as part of the "Seven Principles of Logistics Management".
The acronym is made up of the following letters:
-
Responsive - ensure all actions are legal and not harmful to others.
-
Reliable: Have faith in your ability or the ability to honor any promises made.
-
Reasonable - use resources efficiently and don't waste them.
-
Realistic – consider all aspects of operations, from cost-effectiveness to environmental impact.
-
Respectful - show respect and treat others fairly and fairly
-
You are resourceful and look for ways to save money while increasing productivity.
-
Recognizable: Provide customers with value-added service
What's the difference between Production Planning & Scheduling?
Production Planning (PP) is the process of determining what needs to be produced at any given point in time. This can be done by forecasting demand and identifying production capabilities.
Scheduling refers to the process of allocating specific dates to tasks in order that they can be completed within a specified timeframe.
Statistics
- It's estimated that 10.8% of the U.S. GDP in 2020 was contributed to manufacturing. (investopedia.com)
- According to a Statista study, U.S. businesses spent $1.63 trillion on logistics in 2019, moving goods from origin to end user through various supply chain network segments. (netsuite.com)
- [54][55] These are the top 50 countries by the total value of manufacturing output in US dollars for its noted year according to World Bank.[56] (en.wikipedia.org)
- In the United States, for example, manufacturing makes up 15% of the economic output. (twi-global.com)
- Many factories witnessed a 30% increase in output due to the shift to electric motors. (en.wikipedia.org)
External Links
How To
How to use the Just In-Time Production Method
Just-intime (JIT), which is a method to minimize costs and maximize efficiency in business process, is one way. It's a way to ensure that you get the right resources at just the right time. This means you only pay what you use. The term was first coined by Frederick Taylor, who developed his theory while working as a foreman in the early 1900s. Taylor observed that overtime was paid to workers if they were late in working. He concluded that if workers were given enough time before they start work, productivity would increase.
JIT is a way to plan ahead and make sure you don't waste any money. The entire project should be looked at from start to finish. You need to ensure you have enough resources to tackle any issues that might arise. You'll be prepared to handle any potential problems if you know in advance. This will prevent you from spending extra money on unnecessary things.
There are many JIT methods.
-
Demand-driven: This type of JIT allows you to order the parts/materials required for your project on a regular basis. This will allow you to track how much material you have left over after using it. You'll also be able to estimate how long it will take to produce more.
-
Inventory-based: This is a type where you stock the materials required for your projects in advance. This allows you to forecast how much you will sell.
-
Project-driven: This method allows you to set aside enough funds for your project. Knowing how much money you have available will help you purchase the correct amount of materials.
-
Resource-based JIT is the most widespread form. You allocate resources based on the demand. For example, if there is a lot of work coming in, you will have more people assigned to them. If you don't have many orders, you'll assign fewer people to handle the workload.
-
Cost-based : This is similar in concept to resource-based. But here, you aren't concerned about how many people your company has but how much each individual costs.
-
Price-based pricing: This is similar in concept to cost-based but instead you look at how much each worker costs, it looks at the overall company's price.
-
Material-based is an alternative to cost-based. Instead of looking at the total cost in the company, this method focuses on the average amount of raw materials that you consume.
-
Time-based: This is another variation of resource-based JIT. Instead of focusing solely on the amount each employee costs, focus on how long it takes for the project to be completed.
-
Quality-based JIT is another variant of resource-based JIT. Instead of thinking about how much each employee costs or how long it takes to manufacture something, you think about how good the quality of your product is.
-
Value-based JIT is the newest form of JIT. This is where you don't care about how the products perform or whether they meet customers' expectations. Instead, you are focused on adding value to the marketplace.
-
Stock-based is an inventory-based system that measures the number of items produced at any given moment. It's useful when you want maximum production and minimal inventory.
-
Just-in time (JIT), planning: This is a combination JIT/supply chain management. This refers to the scheduling of the delivery of components as soon after they are ordered. It's important because it reduces lead times and increases throughput.