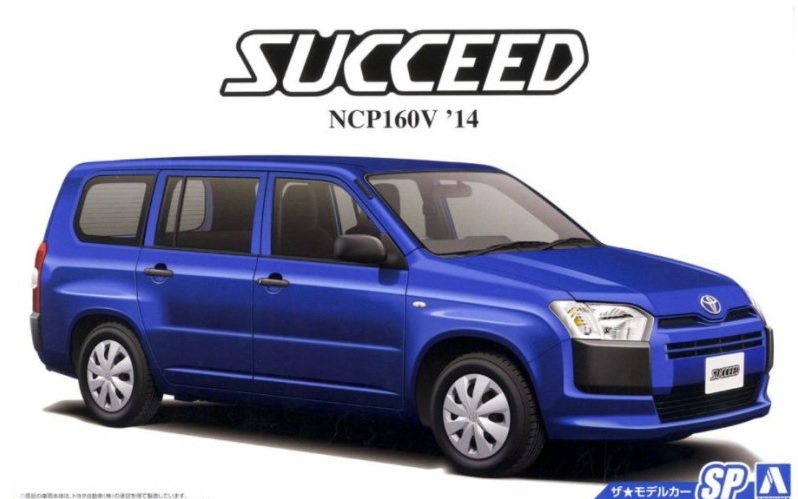
People who wish to become industrial engineers must have strong math skills, a background and ability to solve complex problems. These people can work in various sectors, such as manufacturing and construction. They could work in an office or on the factory floor.
Industrial engineers analyse production processes, design manufacturing techniques, improve efficiency, and make decisions about how to improve them. They also develop quality control procedures. They may also create manufacturing standards, and train staff. People who want to become industrial engineers need to be open-minded and willing work with others. They should be driven to improve efficiency and streamline their processes. They must be able to communicate and lead effectively and should be able to solve problems.
Industrial engineers create cost analysis systems and systems that help robots perform more efficiently. They analyze data to determine if processes are efficient or not. They will also need to develop design standards and manufacturing standards. They may also develop equipment control and inventory control procedures. Additionally, they will create documentation. They might present their plans in written reports or oral presentations.
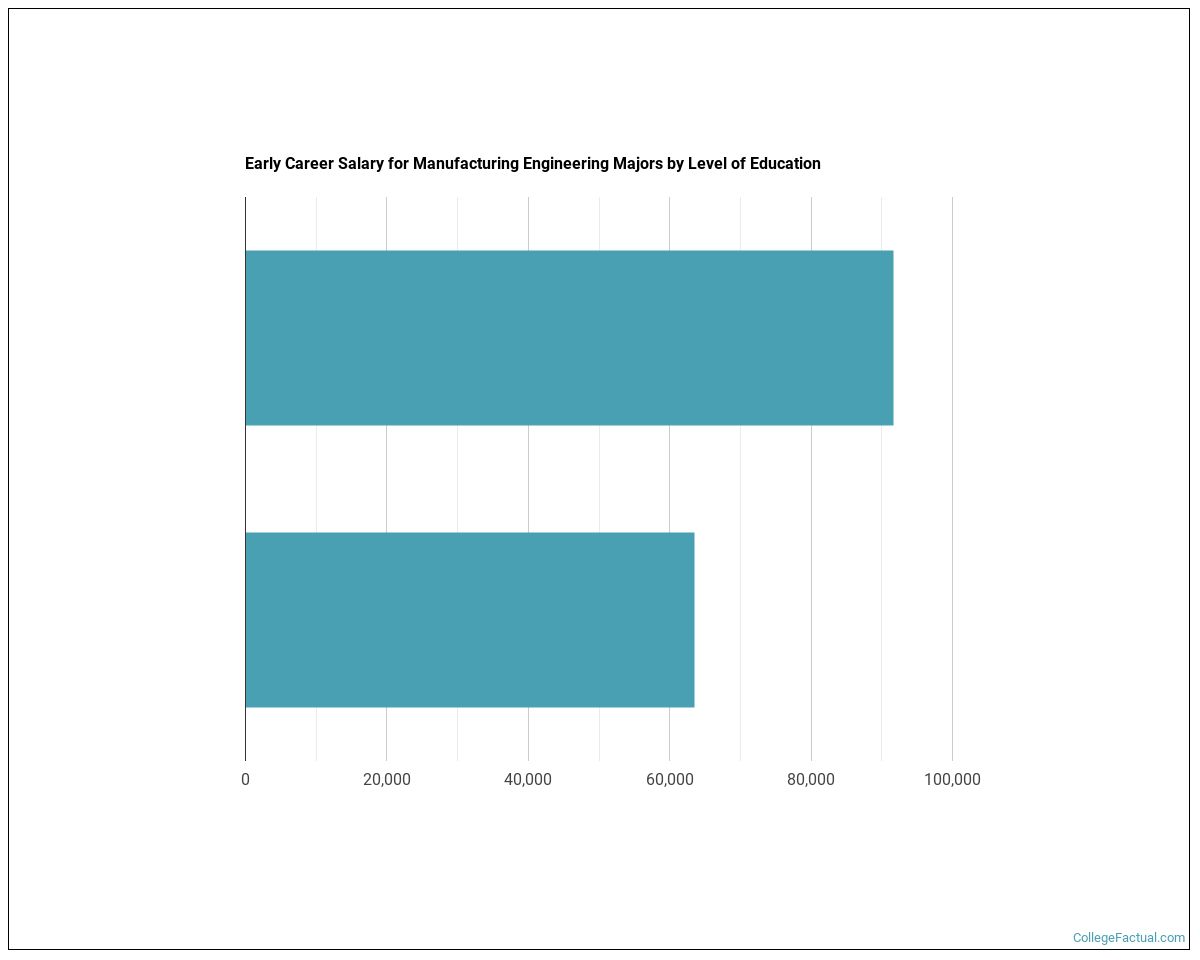
Industrial engineers work in offices, warehouses, or manufacturing facilities, and they may also travel to client sites. They may be required to work in noisy and cramped areas. They may also need to wear protective safety clothing. Sometimes, they may need to take longer hours than normal to meet production deadlines.
Industrial engineers are responsible for designing and implementing processes, ensuring that they operate efficiently and that the products are of high quality. They can also solve production problems. Some industrial engineers also start manufacturing companies. They may have to train new workers and make sure that they know how to do their jobs properly. They may also need to make sure raw materials are meeting quality standards before using them in manufacturing.
The industrial engineer works with other departments to develop integrated systems that manage industrial production. They might also be experts in one particular area of engineering. They might have to work in noisy or cramped environments and may need to work overtime to solve unexpected manufacturing problems. They may need to travel to warehouses or construction sites to gather data, and they may have to work with other professionals to find solutions to manufacturing problems.
They can move up the ladder by gaining experience or education. They might also open their own consulting companies or become experts in a specific area. They might also be skilled in facility planning or quality control. They may also be responsible design layouts. They could also be responsible in developing wage and pay administration systems. They may also be responsible scheduling deliveries based in production forecasts, storage, handling, and maintenance requirements. They might also travel to other places and do administrative tasks. They may also supervise technicians.
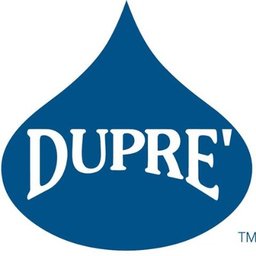
Industrial engineers might work for a company or as consultants. They might work a 40-hour workweek or more depending upon the company's needs. They may also be required to work for more hours in a consultancy service, if they are providing technical assistance for a business.
FAQ
What are the essential elements of running a logistics firm?
To run a successful logistics company, you need a lot knowledge and skills. To communicate effectively with clients and suppliers, you must be able to communicate well. You should be able analyse data and draw inferences. You need to be able work under pressure and manage stressful situations. To increase efficiency and creativity, you need to be creative. You will need strong leadership skills to motivate and direct your team members towards achieving their organizational goals.
It is also important to be efficient and well organized in order meet deadlines.
What does it mean to be a manufacturer?
Manufacturing Industries are those businesses that make products for sale. These products are sold to consumers. This is accomplished by using a variety of processes, including production, distribution and retailing. These companies produce goods using raw materials and other equipment. This includes all types if manufactured goods.
How can excess manufacturing production be reduced?
Better inventory management is key to reducing excess production. This would decrease the time that is spent on inefficient activities like purchasing, storing, or maintaining excess stock. By doing this, we could free up resources for other productive tasks.
A Kanban system is one way to achieve this. A Kanban board, a visual display to show the progress of work, is called a Kanban board. Kanban systems are where work items travel through a series of states until reaching their final destination. Each state represents a different priority.
When work is completed, it can be transferred to the next stage. It is possible to keep a task in the beginning stages until it gets to the end.
This allows work to move forward and ensures that no work is missed. Managers can monitor the work being done by Kanban boards to see what is happening at any given time. This information allows them to adjust their workflow based on real-time data.
Lean manufacturing, another method to control inventory levels, is also an option. Lean manufacturing seeks to eliminate waste from every step of the production cycle. Anything that does not contribute to the product's value is considered waste. Some common types of waste include:
-
Overproduction
-
Inventory
-
Unnecessary packaging
-
Materials in excess
By implementing these ideas, manufacturers can improve efficiency and cut costs.
What are manufacturing & logistics?
Manufacturing is the act of producing goods from raw materials using machines and processes. Logistics includes all aspects related to supply chain management, such as procurement, distribution planning, inventory control and transportation. As a broad term, manufacturing and logistics often refer to both the creation and delivery of products.
What is the job of a production plan?
A production planner makes sure all project elements are delivered on schedule, within budget, as well as within the agreed scope. They also ensure that the product/service meets the client’s needs.
Statistics
- In 2021, an estimated 12.1 million Americans work in the manufacturing sector.6 (investopedia.com)
- According to a Statista study, U.S. businesses spent $1.63 trillion on logistics in 2019, moving goods from origin to end user through various supply chain network segments. (netsuite.com)
- Many factories witnessed a 30% increase in output due to the shift to electric motors. (en.wikipedia.org)
- In the United States, for example, manufacturing makes up 15% of the economic output. (twi-global.com)
- It's estimated that 10.8% of the U.S. GDP in 2020 was contributed to manufacturing. (investopedia.com)
External Links
How To
How to Use Six Sigma in Manufacturing
Six Sigma refers to "the application and control of statistical processes (SPC) techniques in order to achieve continuous improvement." Motorola's Quality Improvement Department developed it at their Tokyo plant in Japan in 1986. Six Sigma's core idea is to improve the quality of processes by standardizing and eliminating defects. This method has been adopted by many companies in recent years as they believe there are no perfect products or services. Six Sigma aims to reduce variation in the production's mean value. This means that if you take a sample of your product, then measure its performance against the average, you can find out what percentage of the time the process deviates from the norm. If the deviation is excessive, it's likely that something needs to be fixed.
Understanding the nature of variability in your business is the first step to Six Sigma. Once you have this understanding, you will need to identify sources and causes of variation. You'll also want to determine whether these variations are random or systematic. Random variations occur when people make mistakes; systematic ones are caused by factors outside the process itself. Random variations would include, for example, the failure of some widgets to fall from the assembly line. It would be considered a systematic problem if every widget that you build falls apart at the same location each time.
Once you've identified the problem areas you need to find solutions. It might mean changing the way you do business or redesigning it entirely. After implementing the new changes, you should test them again to see if they worked. If they don't work, you will need to go back to the drawing boards and create a new plan.