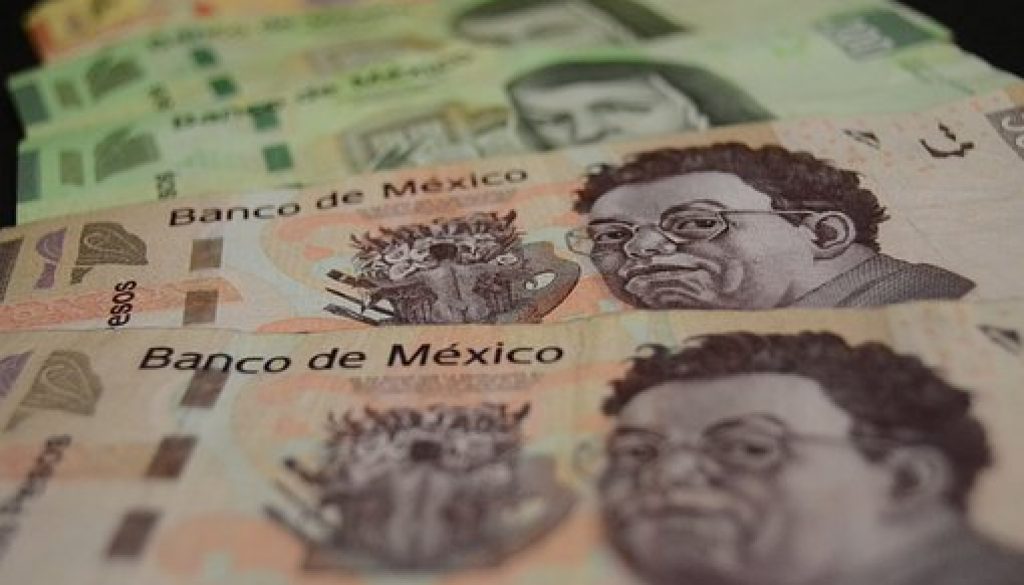
A good media supply chain workflow is crucial. It is important that companies invest in the latest technology to ensure the delivery of their content in the most efficient way. Cloud-based, purpose-built platforms are a great option to ensure that media assets are being used efficiently. It allows you to streamline processes, which can allow for greater insight into the business.
You need to be familiar with the various components of your media supply chains workflow to make the most of them. The workflow might include quality control to ensure your media files are in the correct format, audio mapping and codec. This is important to ensure that the content is being delivered in the correct way and that it is preserved correctly. A good metadata framework can also help you to understand the content being delivered and assist you in finding content quicker.
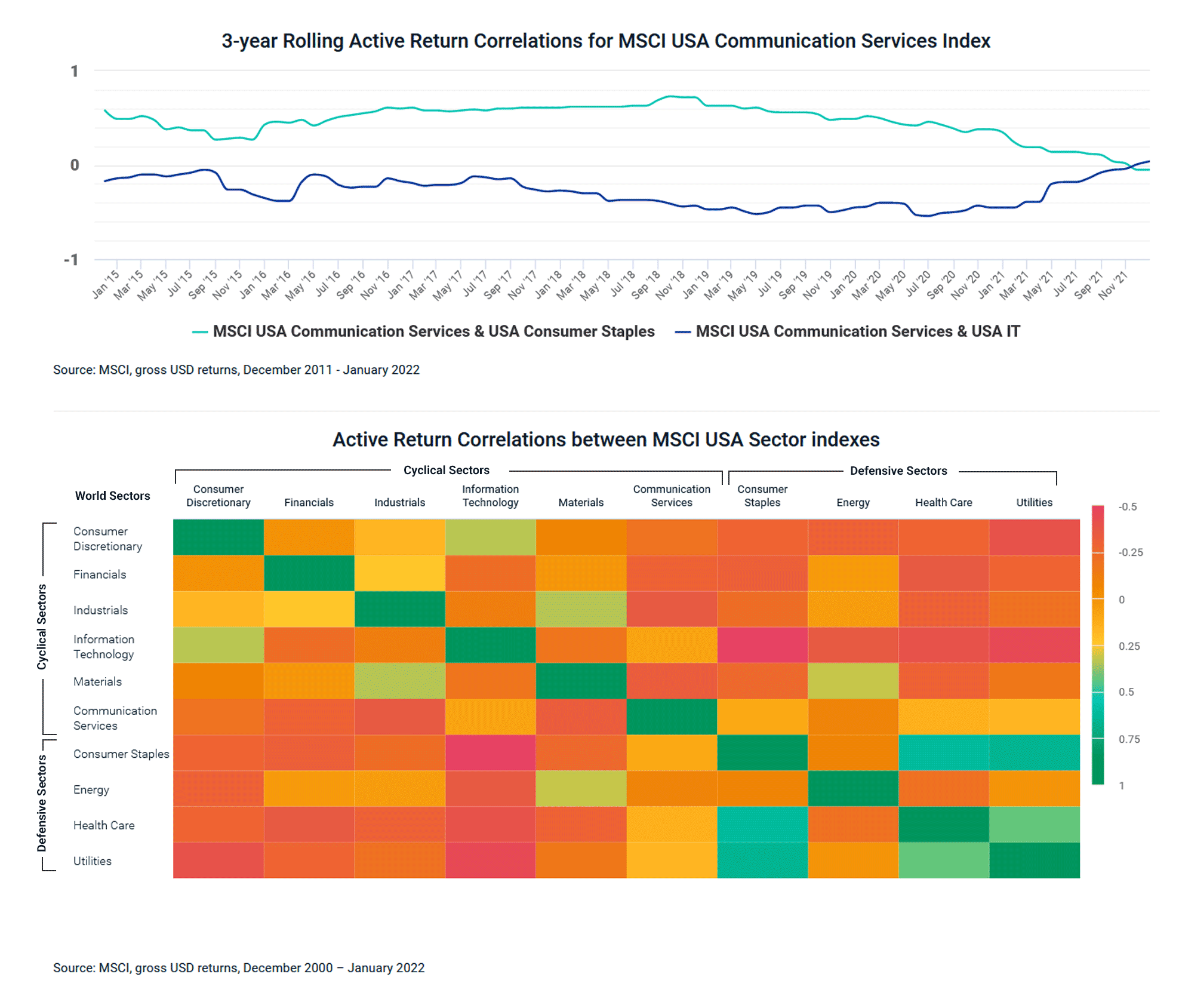
Other companies and third parties may provide content as part your media supply chains workflow. This can present challenges as files may arrive in multiple formats. Also, you may have to modify the files in order to make them usable. This could include changing the format of the master files or transcoding them into smaller proxy files. This can have a negative impact on your business' continuity and be very costly.
The media supply chain workflows have become more complex than they were in the past. It is long past the days of inserting tape in a machine. Streaming services and video editing technology have changed the way that content is being produced. You can now create multiple copies of a piece, which ensures you get the best quality. This allows you to keep costs low and produce the best content possible.
In order to get the most out your media supply chain workflow, you need to have an expert level understanding of the processes involved. Expertise in server and client operating systems, networking, as well as media terminology is essential. Additionally, you will need to be familiar with deploying software in cloud environments. An IT Analyst with expertise in cloud environments may be able to help you if you have any questions.
Video engineers work closely together with client teams to develop a media supply-chain workflow. They are responsible in improving functionality, working with vendors and delivering media to the user. They are also responsible in developing new features.
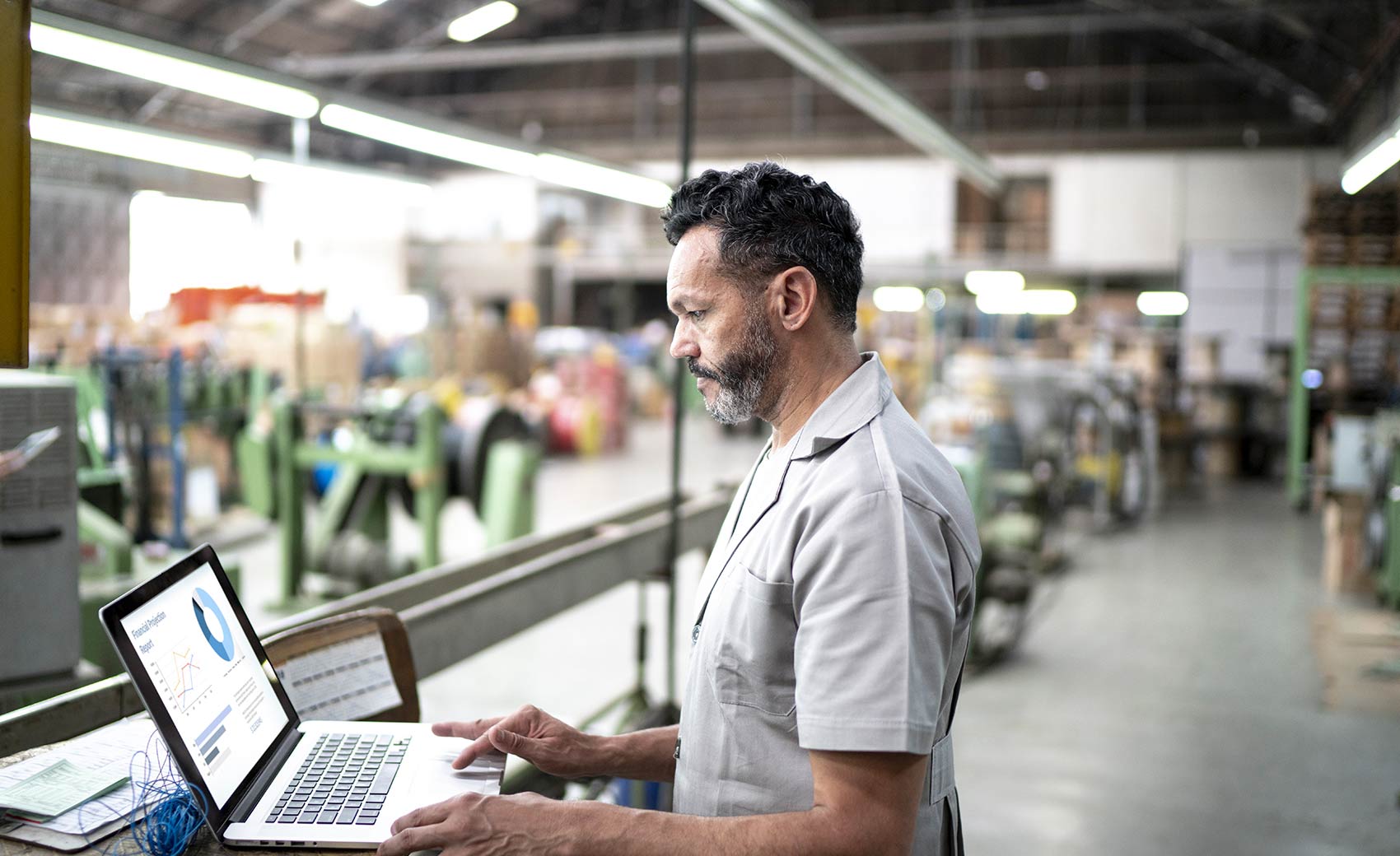
Paramount Global Media Supply Chain Platforms Operations workflows lead by the Director Product. They will collaborate with external and internal collaborators to design and implement Paramount's solutions. They will also review product requirements and provide feedback on a regular basis. They will also lead product development cycles using Agile methodology. They will communicate product needs to development teams and oversee translation of these requirements into products.
FAQ
What is the difference between manufacturing and logistics
Manufacturing refers to the process of making goods using raw materials and machines. Logistics is the management of all aspects of supply chain activities, including procurement, production planning, distribution, warehousing, inventory control, transportation, and customer service. Manufacturing and logistics can often be grouped together to describe a larger term that covers both the creation of products, and the delivery of them to customers.
Can we automate some parts of manufacturing?
Yes! Automation has been around since ancient times. The wheel was invented by the Egyptians thousands of years ago. We now use robots to help us with assembly lines.
There are many applications for robotics in manufacturing today. These include:
-
Assembly line robots
-
Robot welding
-
Robot painting
-
Robotics inspection
-
Robots create products
There are many other examples of how manufacturing could benefit from automation. 3D printing is a way to make custom products quickly and without waiting weeks or months for them to be manufactured.
What is the role of a production manager?
Production planners ensure that all project aspects are completed on time, within budget and within the scope. They ensure that the product or service is of high quality and meets client requirements.
Statistics
- In 2021, an estimated 12.1 million Americans work in the manufacturing sector.6 (investopedia.com)
- It's estimated that 10.8% of the U.S. GDP in 2020 was contributed to manufacturing. (investopedia.com)
- According to a Statista study, U.S. businesses spent $1.63 trillion on logistics in 2019, moving goods from origin to end user through various supply chain network segments. (netsuite.com)
- You can multiply the result by 100 to get the total percent of monthly overhead. (investopedia.com)
- [54][55] These are the top 50 countries by the total value of manufacturing output in US dollars for its noted year according to World Bank.[56] (en.wikipedia.org)
External Links
How To
How to Use Lean Manufacturing in the Production of Goods
Lean manufacturing is a management system that aims at increasing efficiency and reducing waste. It was developed in Japan during the 1970s and 1980s by Taiichi Ohno, who received the Toyota Production System (TPS) award from TPS founder Kanji Toyoda. Michael L. Watkins published the "The Machine That Changed the World", the first book about lean manufacturing. It was published in 1990.
Lean manufacturing, often described as a set and practice of principles, is aimed at improving the quality, speed, cost, and efficiency of products, services, and other activities. It is about eliminating defects and waste from all stages of the value stream. Lean manufacturing is called just-in-time (JIT), zero defect, total productive maintenance (TPM), or 5S. Lean manufacturing seeks to eliminate non-value added activities, such as inspection, work, waiting, and rework.
Lean manufacturing improves product quality and costs. It also helps companies reach their goals quicker and decreases employee turnover. Lean manufacturing has been deemed one of the best ways to manage the entire value-chain, including customers, distributors as well retailers and employees. Lean manufacturing is widely used in many industries. Toyota's philosophy is a great example of this. It has helped to create success in automobiles as well electronics, appliances and healthcare.
Lean manufacturing includes five basic principles:
-
Define Value - Identify the value your business adds to society and what makes you different from competitors.
-
Reduce waste - Stop any activity that isn't adding value to the supply chains.
-
Create Flow: Ensure that the work process flows without interruptions.
-
Standardize and simplify – Make processes as repeatable and consistent as possible.
-
Build Relationships- Develop personal relationships with both internal as well as external stakeholders.
Although lean manufacturing isn't a new concept in business, it has gained popularity due to renewed interest in the economy after the 2008 global financial crisis. Many businesses have adopted lean manufacturing techniques to help them become more competitive. Economists think that lean manufacturing is a crucial factor in economic recovery.
Lean manufacturing has many benefits in the automotive sector. These include higher customer satisfaction, lower inventory levels, lower operating expenses, greater productivity, and improved overall safety.
Lean manufacturing can be applied to almost every aspect of an organization. This is because it ensures efficiency and effectiveness in all stages of the value chain.
There are three types of lean manufacturing.
-
Just-in-Time Manufacturing (JIT): This type of lean manufacturing is commonly referred to as "pull systems." JIT stands for a system where components are assembled on the spot rather than being made in advance. This approach aims to reduce lead times, increase the availability of parts, and reduce inventory.
-
Zero Defects Manufacturing (ZDM),: ZDM is a system that ensures no defective units are left the manufacturing facility. If a part is required to be repaired on the assembly line, it should not be scrapped. This is also true for finished products that require minor repairs before shipping.
-
Continuous Improvement: Continuous Improvement aims to improve efficiency by continually identifying problems and making adjustments to eliminate or minimize waste. Continuous improvement refers to continuous improvement of processes as well people and tools.