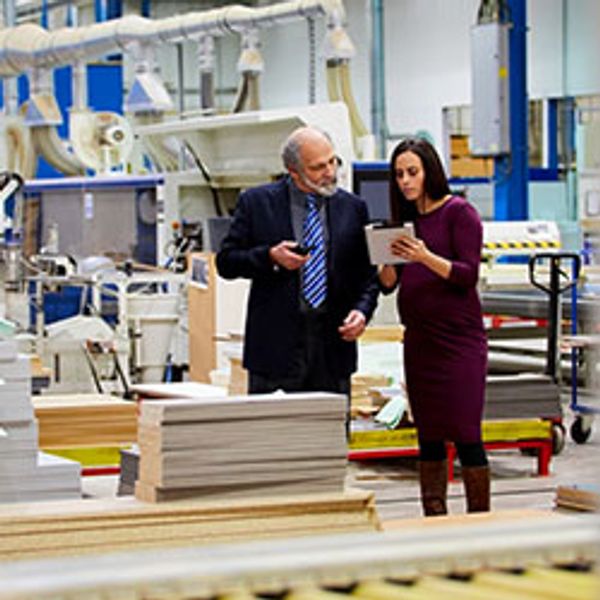
A blue collar job, in general, is one that requires manual labor. These jobs might be in the fields of agriculture, manufacturing, healthcare or hospitality. Some require some level or skill, such a plumber, electrician, etc. While others are less skilled. Blue collar jobs often pay decent wages and offer excellent career growth.
The Fourth Industrial Revolution will transform the labor market for manual workers. This revolution involves artificial intelligence (AI), robotics, machine-learning, and 3D printing. It will require a new, more skilled workforce for companies to succeed. It will also require firms to shift away from transactional relationships, and toward more enduring ones.
This means that companies may have to hire workers from other countries. In certain cases, these workers may also be paid per-item. Others could be paid by a project. In any event, it is encouraging to see a rise in demand for blue-collar jobs.
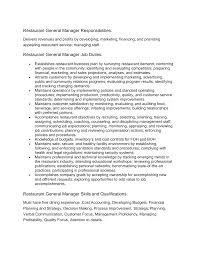
These jobs do require some physical labor but are generally more lucrative than white collar jobs. These jobs provide a steady income source and companies are prepared to invest in training employees. There are many examples of these jobs, including signal and track switches repairers and nuclear power plant operators. These jobs are only for those with a high-school diploma. Some require on-the job training.
Also, blue collar jobs are more common than white collar jobs. The majority of Indian workforce is made up of blue collar workers. India has 210million workers in agriculture, while 290million are employed in non-agricultural sectors. The demand for blue-collar workers is increasing at an alarming rate.
Companies are also being transformed by the Fourth Industrial Revolution in how they manage their blue-collar workers. Firms are not only replacing manual jobs with digital jobs, but they also shift away from transactional relationships towards lasting ones. By putting employee needs first, firms are able to build stronger relationships and improved productivity.
The demand for blue collar workers is also high, but they are faced with competing realities. They might be worried about the stability and retirement of their jobs. Blue collar workers can be optimistic about their prospects, regardless of any concerns. The percentage of blue-collar workers who are saving for retirement is actually increasing. And, as the economy recovers, blue collar jobs are likely to increase in popularity.
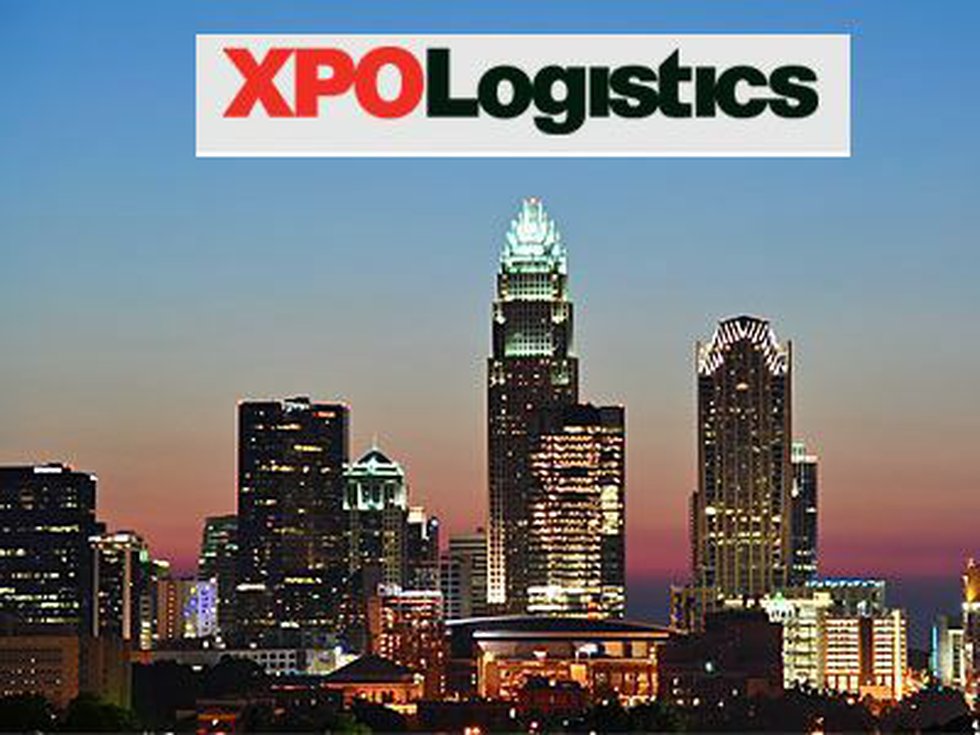
Automation is not threatening these jobs. The Association for Manufacturing Technology has found that for every job that is replaced by technology there are five new jobs. The biggest salary increase last year went to signal and track switch repairers, who earned $76,210 on average.
Also, blue collar jobs are becoming more well-paid. Blue collar jobs often earn well above the average national wage, which makes them a desirable option for those who are looking for a job that pays well. Additionally, blue collar jobs often require a high level in problem-solving skills. They are also likely to offer career growth.
FAQ
What is manufacturing and logistics?
Manufacturing refers to the process of making goods using raw materials and machines. Logistics covers all aspects involved in managing supply chains, including procurement and production planning. Sometimes manufacturing and logistics are combined to refer to a wider term that includes both the process of creating products as well as their delivery to customers.
How does a Production Planner differ from a Project Manager?
The primary difference between a producer planner and a manager of a project is that the manager usually plans and organizes the whole project, while a production planner is only involved in the planning stage.
How can excess manufacturing production be reduced?
Better inventory management is key to reducing excess production. This would reduce time spent on activities such as purchasing, stocking, and maintaining excess stock. We could use these resources to do other productive tasks.
Kanban systems are one way to achieve this. A Kanban board is a visual display used to track work in progress. Kanban systems are where work items travel through a series of states until reaching their final destination. Each state represents a different priority.
To illustrate, work can move from one stage or another when it is complete enough for it to be moved to a new stage. It is possible to keep a task in the beginning stages until it gets to the end.
This keeps work moving and ensures no work is lost. Managers can see how much work has been done and the status of each task at any time with a Kanban Board. This information allows managers to adjust their workflow based off real-time data.
Lean manufacturing is another option to control inventory levels. Lean manufacturing emphasizes eliminating waste in all phases of production. Waste includes anything that does not add value to the product. Some common types of waste include:
-
Overproduction
-
Inventory
-
Unnecessary packaging
-
Material surplus
These ideas can help manufacturers improve efficiency and reduce costs.
Statistics
- According to a Statista study, U.S. businesses spent $1.63 trillion on logistics in 2019, moving goods from origin to end user through various supply chain network segments. (netsuite.com)
- Job #1 is delivering the ordered product according to specifications: color, size, brand, and quantity. (netsuite.com)
- It's estimated that 10.8% of the U.S. GDP in 2020 was contributed to manufacturing. (investopedia.com)
- [54][55] These are the top 50 countries by the total value of manufacturing output in US dollars for its noted year according to World Bank.[56] (en.wikipedia.org)
- In the United States, for example, manufacturing makes up 15% of the economic output. (twi-global.com)
External Links
How To
How to use 5S in Manufacturing to Increase Productivity
5S stands for "Sort", 'Set In Order", 'Standardize', & Separate>. Toyota Motor Corporation developed the 5S method in 1954. It improves the work environment and helps companies to achieve greater efficiency.
This method aims to standardize production processes so that they are repeatable, measurable and predictable. This means that tasks such as cleaning, sorting, storing, packing, and labeling are performed daily. Because workers know what they can expect, this helps them perform their jobs more efficiently.
Implementing 5S involves five steps: Sort, Set in Order, Standardize Separate, Store, and Each step has a different action and leads to higher efficiency. You can make it easy for people to find things later by sorting them. You arrange items by placing them in an order. Once you have separated your inventory into groups and organized them, you will store these groups in easily accessible containers. You can also label your containers to ensure everything is properly labeled.
This process requires employees to think critically about how they do their job. Employees need to understand the reasons they do certain jobs and determine if there is a better way. They will need to develop new skills and techniques in order for the 5S system to be implemented.
The 5S method increases efficiency and morale among employees. They feel more motivated to work towards achieving greater efficiency as they see the results.