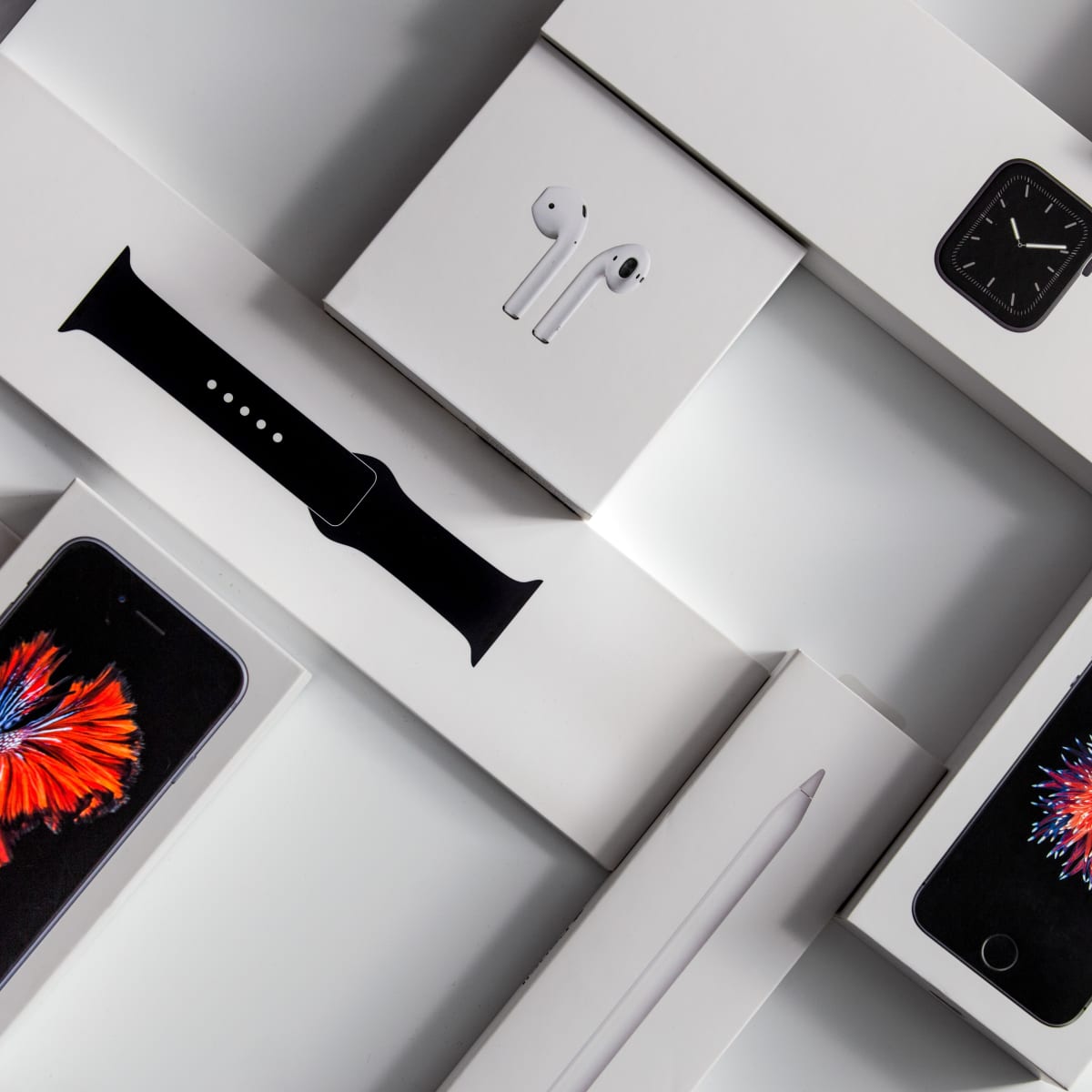
The field of manufacturing engineering is often referred to as production engineering. This type is similar to other engineering fields in that it shares many of the same ideas and concepts. The person who is an expert in this area of engineering could find their niche in the industry and be an integral part of a company’s success. These engineers can ensure that products and services meet high quality standards.
Job duties
As a production engineer, you will be responsible for coordinating and analysing the entire production process from design through implementation. This position requires meticulous attention to detail as well as a commitment for the safety of the workplace. Production engineers ensure that the company meets high quality standards and protects the environment. They also evaluate current production activities and identify ways to improve.
Production engineers are key to a company's ability to produce goods quickly and economically. They also play an important role in the implementation of automation. The job of a production engineer may involve them analysing current production processes and/or focusing on a particular area. They may also train production workers and adjust software.
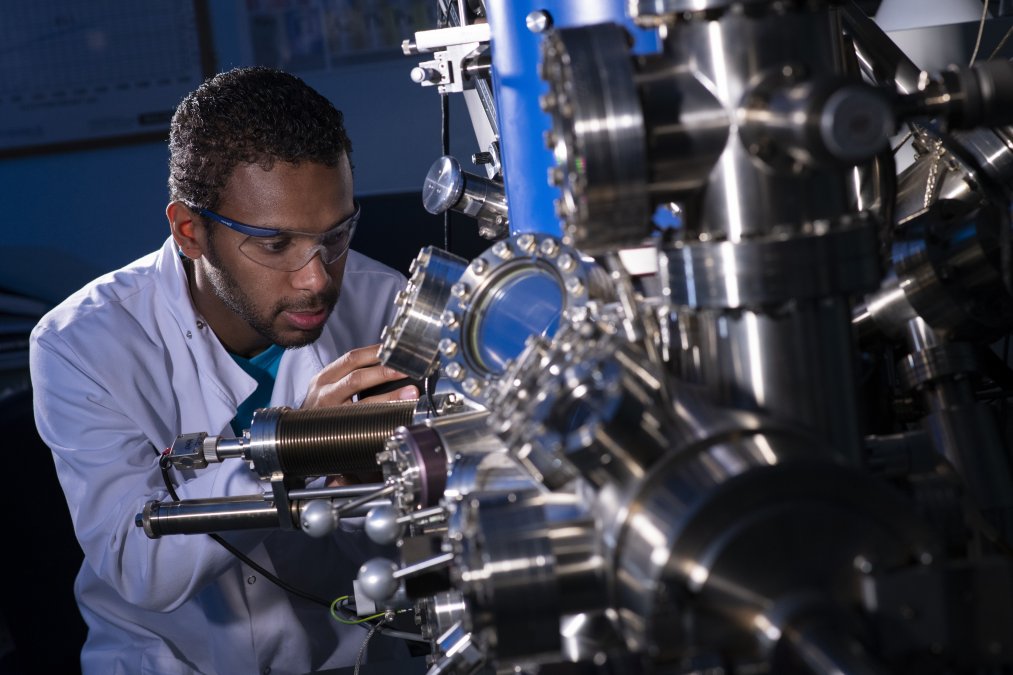
Communication skills are essential in this job. Engineers need to be able communicate complex engineering concepts in a simple and understandable way. Engineering often involves complicated calculations and mathematics. A production engineer may use equations for determining the cost of finished products, or solving manufacturing line problems.
Education required
The first step toward a career as a production engineer is to acquire a bachelor's degree in manufacturing or industrial engineering. For research-oriented positions in manufacturing, some employers prefer a master’s degree. Additionally, it is beneficial to be proficient in a number of specialized areas.
Industrial engineers use their creativity and analytical skills to improve the efficiency of production processes. They strive to eliminate waste and create new ways to use equipment, materials, or employees more efficiently. Because they must communicate complex processes to non-technical audience, they should also possess excellent communication skills. Communication skills include the ability to listen and understand others' views and opinions.
Manufacturing engineers are trained in the field during their degree program. They will also learn safety procedures and regulations. In addition, they will be required to obtain a Professional Engineer license, issued by the National Society of Professional Engineers. This license proves to employers and clients you have the right credentials. Renewing your license should be done according to the state's requirements.
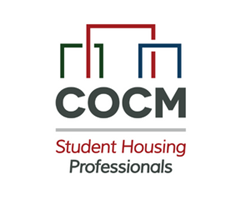
Salary
The salary of a producer engineer will vary depending on the company and where you live. Although they are primarily employed in offices, production engineers may travel to work on site to inspect equipment and improve processes. Some production engineers work for themselves, while others are employed by larger companies. Production engineers are expected not only to earn a good salary but also to finish their work promptly.
Production engineers collaborate with other professionals to ensure that the product is safe and quality. They also work closely alongside designers to ensure efficient production processes. In some cases they will also be responsible to maintain safety standards on the factory floor as well as train workers on safe procedures. This job description does not include all of the responsibilities and duties of a production engineers.
The salary for a production engineer is dependent on the level of experience. However, entry-level production engineers can expect to earn around Rs2.5 lakhs per year. Mid-level engineers could earn Rs3.8 Lakhs. For experienced production engineers, the annual salary can rise to Rs3.8 lakhs.
FAQ
What is the role and responsibility of a Production Planner?
Production planners ensure all aspects of the project are delivered within time and budget. A production planner ensures that the service and product meet the client's expectations.
How can overproduction in manufacturing be reduced?
In order to reduce excess production, you need to develop better inventory management methods. This would reduce the time needed to manage inventory. This would allow us to use our resources for more productive tasks.
Kanban systems are one way to achieve this. A Kanban Board is a visual display that tracks work progress. Kanban systems allow work items to move through different states until they reach their final destination. Each state has a different priority level.
To illustrate, work can move from one stage or another when it is complete enough for it to be moved to a new stage. A task that is still in the initial stages of a process will be considered complete until it moves on to the next stage.
This allows work to move forward and ensures that no work is missed. Managers can see how much work has been done and the status of each task at any time with a Kanban Board. This information allows managers to adjust their workflow based off real-time data.
Lean manufacturing is another way to manage inventory levels. Lean manufacturing seeks to eliminate waste from every step of the production cycle. Waste includes anything that does not add value to the product. Some common types of waste include:
-
Overproduction
-
Inventory
-
Unnecessary packaging
-
Material surplus
Manufacturers can reduce their costs and improve their efficiency by using these ideas.
How does a Production Planner differ from a Project Manager?
The major difference between a Production Planner and a Project Manager is that a Project Manager is often the person responsible for organizing and planning the entire project. While a Production Planner is involved mainly in the planning stage,
What is the role of a manager in manufacturing?
A manufacturing manager must make sure that all manufacturing processes run smoothly and effectively. They must also be alert to any potential problems and take appropriate action.
They should also know how to communicate with other departments such as sales and marketing.
They should also be aware of the latest trends in their industry and be able to use this information to help improve productivity and efficiency.
What is the role of a logistics manager
Logistics managers are responsible for ensuring that all goods arrive in perfect condition and on time. This is done using his/her knowledge of the company's products. He/she also needs to ensure adequate stock to meet demand.
How can we improve manufacturing efficiency?
First, we need to identify which factors are most critical in affecting production times. Then we need to find ways to improve these factors. If you don’t know where to begin, consider which factors have the largest impact on production times. Once you've identified them, try to find solutions for each of those factors.
What are the 7 Rs of logistics?
The acronym 7R's for Logistics stands to represent the seven basic principles in logistics management. It was developed by the International Association of Business Logisticians (IABL) and published in 2004 as part of its "Seven Principles of Logistics Management" series.
The acronym is composed of the following letters.
-
Responsible - to ensure that all actions are within the legal requirements and are not detrimental to others.
-
Reliable - Have confidence in your ability to fulfill all of your commitments.
-
It is reasonable to use resources efficiently and not waste them.
-
Realistic - Consider all aspects of operations, including environmental impact and cost effectiveness.
-
Respectful: Treat others with fairness and equity
-
Responsive - Look for ways to save time and increase productivity.
-
Recognizable provides value-added products and services to customers
Statistics
- According to a Statista study, U.S. businesses spent $1.63 trillion on logistics in 2019, moving goods from origin to end user through various supply chain network segments. (netsuite.com)
- (2:04) MTO is a production technique wherein products are customized according to customer specifications, and production only starts after an order is received. (oracle.com)
- According to the United Nations Industrial Development Organization (UNIDO), China is the top manufacturer worldwide by 2019 output, producing 28.7% of the total global manufacturing output, followed by the United States, Japan, Germany, and India.[52][53] (en.wikipedia.org)
- Job #1 is delivering the ordered product according to specifications: color, size, brand, and quantity. (netsuite.com)
- In 2021, an estimated 12.1 million Americans work in the manufacturing sector.6 (investopedia.com)
External Links
How To
How to Use Lean Manufacturing in the Production of Goods
Lean manufacturing refers to a method of managing that seeks to improve efficiency and decrease waste. It was developed in Japan between 1970 and 1980 by Taiichi Ohno. TPS founder Kanji Tyoda gave him the Toyota Production System, or TPS award. Michael L. Watkins published the original book on lean manufacturing, "The Machine That Changed the World," in 1990.
Lean manufacturing can be described as a set or principles that are used to improve quality, speed and cost of products or services. It emphasizes reducing defects and eliminating waste throughout the value chain. Lean manufacturing can be described as just-in–time (JIT), total productive maintenance, zero defect (TPM), or even 5S. Lean manufacturing is about eliminating activities that do not add value, such as inspection, rework, and waiting.
Lean manufacturing is a way for companies to achieve their goals faster, improve product quality, and lower costs. Lean Manufacturing is one of the most efficient ways to manage the entire value chains, including suppliers and customers as well distributors and retailers. Lean manufacturing practices are widespread in many industries. Toyota's philosophy is the foundation of its success in automotives, electronics and appliances, healthcare, chemical engineers, aerospace, paper and food, among other industries.
Five fundamental principles underlie lean manufacturing.
-
Define Value - Determine the value that your business brings to society. Also, identify what sets you apart from your competitors.
-
Reduce waste - Get rid of any activity that does not add value to the supply chain.
-
Create Flow – Ensure that work flows smoothly throughout the process.
-
Standardize and simplify - Make your processes as consistent as possible.
-
Build relationships - Develop and maintain personal relationships with both your internal and external stakeholders.
Although lean manufacturing has always been around, it is gaining popularity in recent years because of a renewed interest for the economy after 2008's global financial crisis. Many businesses have adopted lean manufacturing techniques to help them become more competitive. According to some economists, lean manufacturing could be a significant factor in the economic recovery.
Lean manufacturing, which has many benefits, is now a standard practice in the automotive industry. These benefits include increased customer satisfaction, reduced inventory levels and lower operating costs.
The principles of lean manufacturing can be applied in almost any area of an organization. However, it is particularly useful when applied to the production side of an organization because it ensures that all steps in the value chain are efficient and effective.
There are three main types of lean manufacturing:
-
Just-in-Time Manufacturing (JIT): This type of lean manufacturing is commonly referred to as "pull systems." JIT stands for a system where components are assembled on the spot rather than being made in advance. This method reduces lead times, increases availability, and decreases inventory.
-
Zero Defects Manufacturing - ZDM: ZDM focuses its efforts on making sure that no defective units leave a manufacturing facility. It is better to repair a part than have it removed from the production line if it needs to be fixed. This also applies to finished products that need minor repairs before being shipped.
-
Continuous Improvement (CI): CI aims to improve the efficiency of operations by continuously identifying problems and making changes in order to eliminate or minimize waste. Continuous improvement involves continuous improvement of processes and people as well as tools.