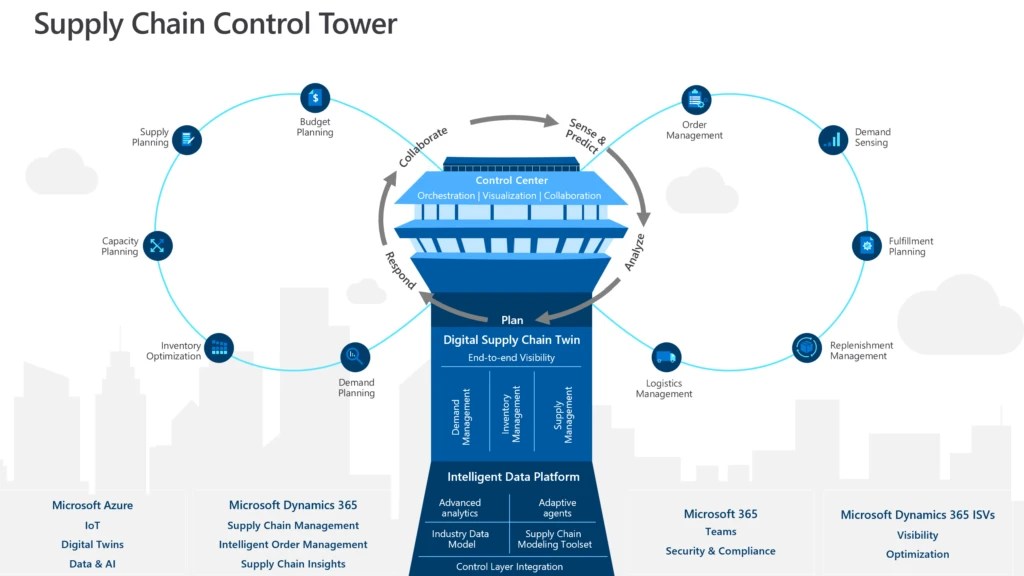
High-paying job opportunities are available for anyone looking to enter the manufacturing industry. There are many kinds of manufacturing jobs, and each job requires different skills. You should explore the different options and choose the manufacturing career that's right for you.
Manufacturing careers require a combination between theoretical and practical skills. Therefore, it is important to set some criteria to decide which skills are most essential to you. Ophthalmic laboratory technician is a good choice if you are interested in repair eyeglasses. For those who are skilled in mechanical or electrical engineering, the best-paying manufacturing jobs could be ones that require technical expertise.
The United States' manufacturing sector is a major contributor to its economy. It generates more economic activity than any other industry. It contributes a sizable share of the nation's economic growth, and holds a significant share of its employment. It is also home to the largest sector in the country, as well as the largest portion of the nation’s economy development.
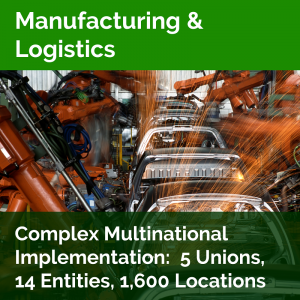
Typically, the best manufacturing jobs require advanced technical skills and experience. You can still get your foot in this industry by applying for entry-level roles. They are also well-paid, with great benefits. The average salary for a job advertised has increased by 1.5% in the past year.
It is easy to sign up for an internet program and get your foot in front of the door. To learn to code, you can either join an online coding bootcamp or enroll in a formal program. These jobs are the highest-paid in manufacturing. Traveling contractors can also make good cash, as many companies are open to hiring experienced manufacturing talent.
You need to have a wide range of skills in order to succeed in manufacturing. For example, you may need to make sure that your products are consistent and that your manufacturing processes adhere to all necessary regulations. You may also need to make the most of all the technologies you have at your disposal.
Many manufacturing jobs can be physically demanding as you will often have to use heavy machinery. You may be required to work in a shop or laboratory, depending on the employer. High-skilled and experienced manufacturing jobs are those that pay the highest.
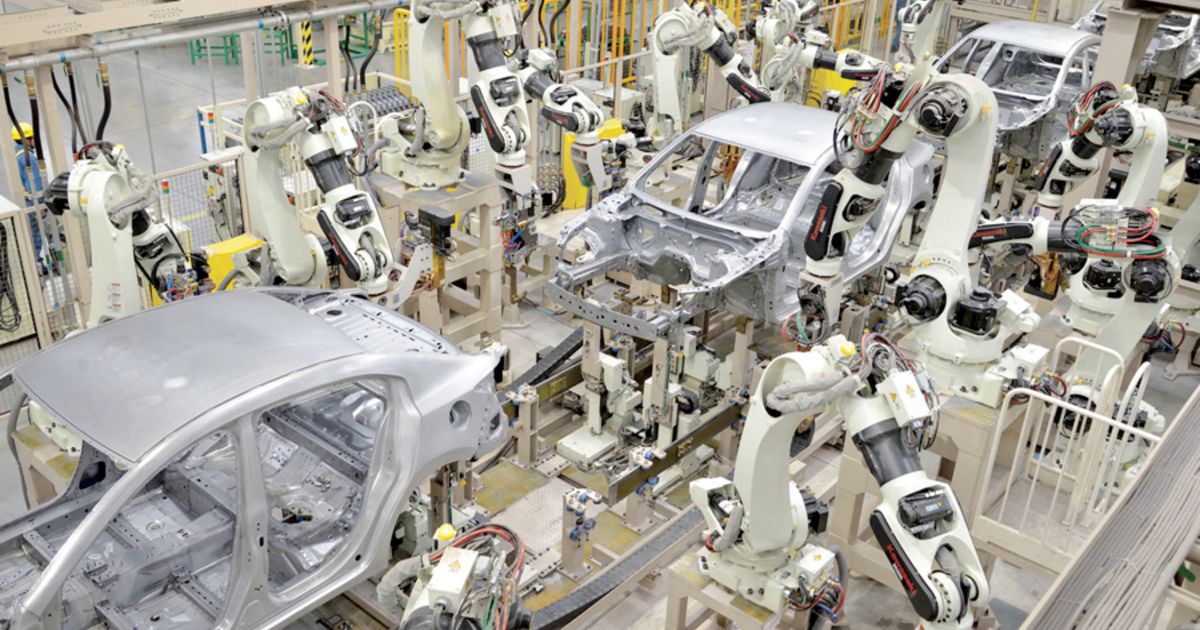
It is important to consider all the companies and industries involved in manufacturing. These include apparel producers, car factories, and electronics production plants. The process of choosing the manufacturing job that suits you best can be hard but rewarding. This is also a great opportunity to learn new skills.
Electromechanical technicians are one of the most lucrative manufacturing jobs. You will be responsible to repair and maintain various manufacturing machines. In order to qualify, you will usually need to have a degree either in engineering or computer sciences. You can still get started in this industry with a high-school diploma.
FAQ
Why automate your warehouse
Modern warehousing has seen automation take center stage. With the rise of ecommerce, there is a greater demand for faster delivery times as well as more efficient processes.
Warehouses should be able adapt quickly to new needs. To do so, they must invest heavily in technology. Automating warehouses is a great way to save money. Here are some benefits of investing in automation
-
Increases throughput/productivity
-
Reduces errors
-
Increases accuracy
-
Boosts safety
-
Eliminates bottlenecks
-
Allows companies to scale more easily
-
It makes workers more efficient
-
The warehouse can be viewed from all angles.
-
Enhances customer experience
-
Improves employee satisfaction
-
Reduces downtime and improves uptime
-
This ensures that quality products are delivered promptly
-
Eliminates human error
-
This helps to ensure compliance with regulations
What is the distinction between Production Planning or Scheduling?
Production Planning (PP) refers to the process of determining how much production is needed at any given moment. Forecasting and identifying production capacity are two key elements to this process.
Scheduling refers the process by which tasks are assigned dates so that they can all be completed within the given timeframe.
What are the responsibilities of a manufacturing manager
A manufacturing manager has to ensure that all manufacturing processes work efficiently and effectively. They must also be alert to any potential problems and take appropriate action.
They must also be able to communicate with sales and marketing departments.
They should also be aware of the latest trends in their industry and be able to use this information to help improve productivity and efficiency.
What is the job of a production plan?
A production planner ensures all aspects of the project are delivered on time, within budget, and within scope. They ensure that the product or service is of high quality and meets client requirements.
What kind of jobs are there in logistics?
There are different kinds of jobs available in logistics. Some examples are:
-
Warehouse workers - They load and unload trucks and pallets.
-
Transportation drivers – They drive trucks or trailers to transport goods and perform pick-ups.
-
Freight handlers: They sort and package freight in warehouses.
-
Inventory managers: They are responsible for the inventory and management of warehouses.
-
Sales reps - They sell products and services to customers.
-
Logistics coordinators: They plan and manage logistics operations.
-
Purchasing agents - They purchase goods and services needed for company operations.
-
Customer service agents - They answer phone calls and respond to emails.
-
Shipping clerks – They process shipping orders, and issue bills.
-
Order fillers - They fill orders based on what is ordered and shipped.
-
Quality control inspectors (QCI) - They inspect all incoming and departing products for potential defects.
-
Others - There are many types of jobs in logistics such as transport supervisors and cargo specialists.
Statistics
- (2:04) MTO is a production technique wherein products are customized according to customer specifications, and production only starts after an order is received. (oracle.com)
- [54][55] These are the top 50 countries by the total value of manufacturing output in US dollars for its noted year according to World Bank.[56] (en.wikipedia.org)
- According to a Statista study, U.S. businesses spent $1.63 trillion on logistics in 2019, moving goods from origin to end user through various supply chain network segments. (netsuite.com)
- You can multiply the result by 100 to get the total percent of monthly overhead. (investopedia.com)
- It's estimated that 10.8% of the U.S. GDP in 2020 was contributed to manufacturing. (investopedia.com)
External Links
How To
Six Sigma: How to Use it in Manufacturing
Six Sigma can be described as "the use of statistical process control (SPC), techniques to achieve continuous improvement." It was developed by Motorola's Quality Improvement Department at their plant in Tokyo, Japan, in 1986. Six Sigma's core idea is to improve the quality of processes by standardizing and eliminating defects. Since there are no perfect products, or services, this approach has been adopted by many companies over the years. Six Sigma's primary goal is to reduce variation from the average value of production. This means that if you take a sample of your product, then measure its performance against the average, you can find out what percentage of the time the process deviates from the norm. If the deviation is excessive, it's likely that something needs to be fixed.
Understanding how your business' variability is a key step towards Six Sigma implementation is the first. Once you understand that, it is time to identify the sources of variation. These variations can also be classified as random or systematic. Random variations occur when people make mistakes; systematic ones are caused by factors outside the process itself. For example, if you're making widgets, and some of them fall off the assembly line, those would be considered random variations. But if you notice that every widget you make falls apart at the exact same place each time, this would indicate that there is a problem.
After identifying the problem areas, you will need to devise solutions. That solution might involve changing the way you do things or redesigning the process altogether. Once you have implemented the changes, it is important to test them again to ensure they work. If they don't work, you will need to go back to the drawing boards and create a new plan.