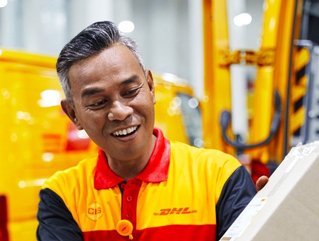
The National Network for Manufacturing Innovation has as its primary objective the development of cutting-edge manufacturing technology. President Obama announced the interagency initiative in his FY 2013 budget proposal. This initiative aims to bring together community colleges, universities, and federal agencies to commercialize novel manufacturing technologies.
The United States plays a key role in its economy, with manufacturing being a major sector. American workers find good work in this sector. In order to remain competitive, manufacturing companies are investing in technological innovations that help them stay productive while reducing labor costs. These innovations include automation, green energy sources, and other technological innovations. Companies are also investing in solutions to reduce machine downtime. These innovative products include autonomous mobile robots that reduce labor costs and increase productivity. Additionally, companies invest in technologies that reduce the waste of resources, such as smart sensor technology.
The "Maker's Economy" will revolutionize how products are made. This economy allows manufacturing users to take an active role in creating and constructing new products with readily available technologies. These innovations are expected by the manufacturing sector, which is expected to benefit from them to increase productivity and operational efficiency as well as enhance decision-making. It is also expected that it will be a significant contributor to the nation’s overall productivity. The United States has a long history of being a world leader for manufacturing.
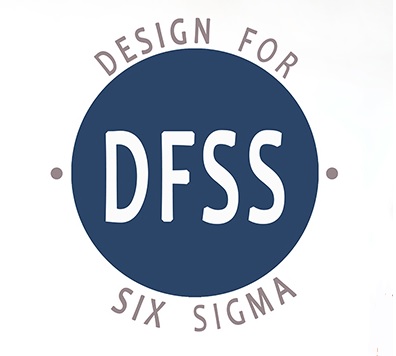
The "Maker's Economy," which relies on many technologies, such as smart factories and artificial Intelligence, is based on a wide range of technologies. These innovations enhance manufacturing productivity by increasing worker efficiency as well as decreasing the time taken to produce a product. The Industrial Internet of Things uses sensors to aid in tasks. It also ensures continuous monitoring of industrial assets. The IIoT also requires secure connectivity and fast data transmission. It is expected that it will improve warehousing efficiency as well as supply chain visibility.
The National Network for Manufacturing Innovation is composed of at least 15 manufacturing institutes. It is expected to accelerate the development and application of manufacturing technologies. This network will also be comprised of public/private partners from government entities, as well private companies.
There are currently 14 manufacturing innovation institutes in the United States, with another three institutes expected to be funded by the Commerce Department in May 2013. Two Institutes are expected to be funded in part by the National Institute of Standards and Technology. This will provide a total of up to $70 million per institute over five to seven years.
Each Institute for Manufacturing Innovation (IMI) will have a different research focus. They will act as hubs of manufacturing innovation for both state and local economies. These Institutes will assist manufacturers in integrating their capabilities. These institutes offer access to cutting edge technology and will also provide training opportunities for workers. These institutes can also be used to help manufacturers tackle cross-cutting problems in advanced manufacturing.
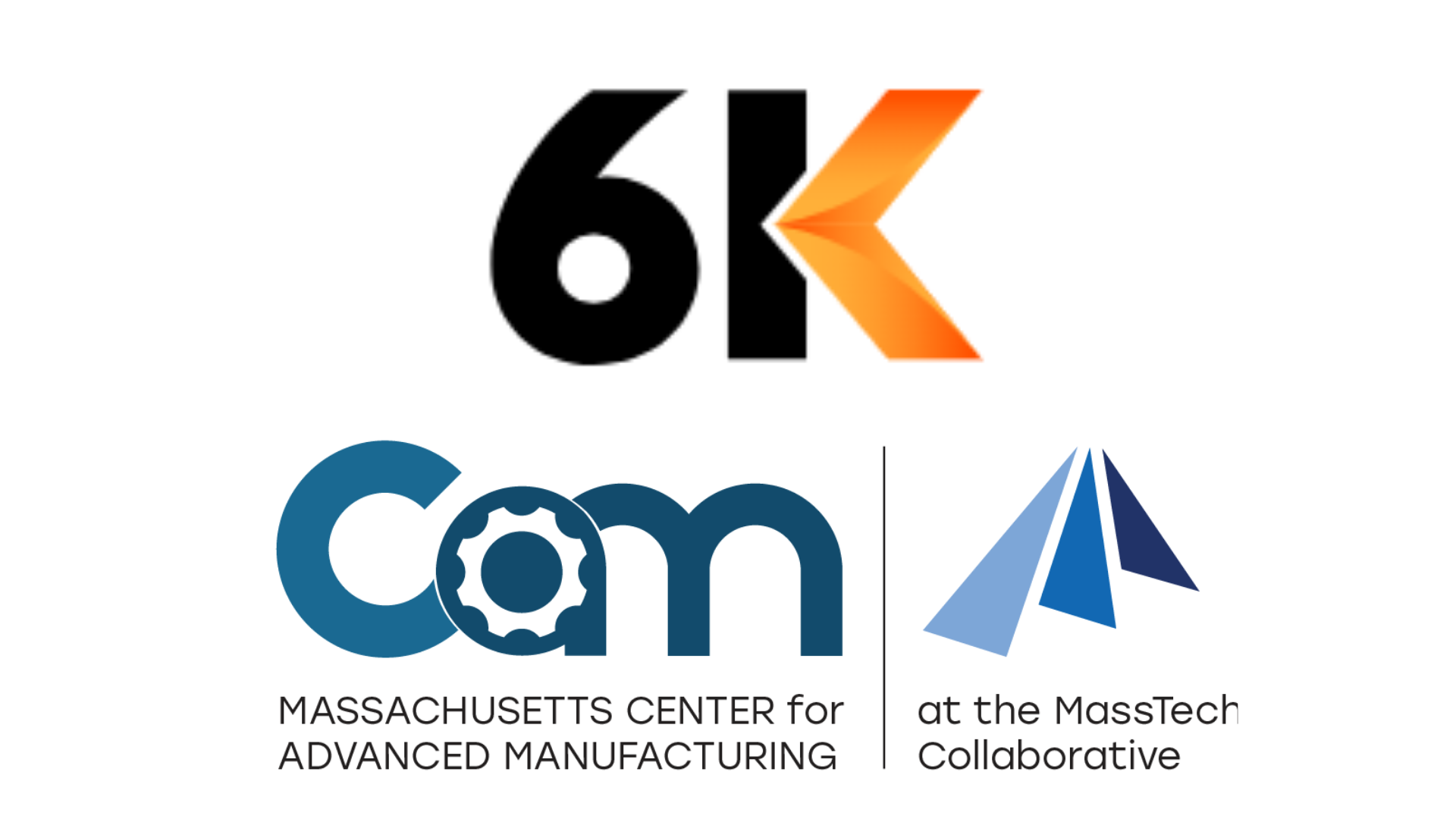
The Network for Manufacturing Innovation is a broad-based program that aims at accelerating the commercialization, application and transfer of innovative manufacturing technologies. It also seeks to strengthen the state's and local economies. The U.S. Department of Energy's National Institute of Standards and Technology will oversee the operation of the institutes.
FAQ
What does it mean to be a manufacturer?
Manufacturing Industries are businesses that produce products for sale. These products are sold to consumers. These companies use various processes such as production, distribution, retailing, management, etc., to fulfill this purpose. They produce goods from raw materials by using machines and other machinery. This covers all types of manufactured goods including clothing, food, building supplies and furniture, as well as electronics, tools, machinery, vehicles and pharmaceuticals.
How can manufacturing excess production be decreased?
Better inventory management is key to reducing excess production. This would reduce time spent on activities such as purchasing, stocking, and maintaining excess stock. This would allow us to use our resources for more productive tasks.
Kanban systems are one way to achieve this. A Kanban board is a visual display used to track work in progress. Kanban systems allow work items to move through different states until they reach their final destination. Each state is assigned a different priority.
When work is completed, it can be transferred to the next stage. A task that is still in the initial stages of a process will be considered complete until it moves on to the next stage.
This allows work to move forward and ensures that no work is missed. With a Kanban board, managers can see exactly how much work is being done at any given moment. This information allows them to adjust their workflow based on real-time data.
Lean manufacturing is another option to control inventory levels. Lean manufacturing emphasizes eliminating waste in all phases of production. Any product that isn't adding value can be considered waste. Here are some examples of common types.
-
Overproduction
-
Inventory
-
Packaging not required
-
Materials in excess
Manufacturers can increase efficiency and decrease costs by implementing these ideas.
What is the job of a manufacturer manager?
A manufacturing manager has to ensure that all manufacturing processes work efficiently and effectively. They should also be aware and responsive to any company problems.
They should also know how to communicate with other departments such as sales and marketing.
They should also be knowledgeable about the latest trends in the industry so they can use this information for productivity and efficiency improvements.
Statistics
- According to a Statista study, U.S. businesses spent $1.63 trillion on logistics in 2019, moving goods from origin to end user through various supply chain network segments. (netsuite.com)
- Many factories witnessed a 30% increase in output due to the shift to electric motors. (en.wikipedia.org)
- It's estimated that 10.8% of the U.S. GDP in 2020 was contributed to manufacturing. (investopedia.com)
- You can multiply the result by 100 to get the total percent of monthly overhead. (investopedia.com)
- (2:04) MTO is a production technique wherein products are customized according to customer specifications, and production only starts after an order is received. (oracle.com)
External Links
How To
How to use Lean Manufacturing in the production of goods
Lean manufacturing (or lean manufacturing) is a style of management that aims to increase efficiency, reduce waste and improve performance through continuous improvement. It was developed in Japan during the 1970s and 1980s by Taiichi Ohno, who received the Toyota Production System (TPS) award from TPS founder Kanji Toyoda. Michael L. Watkins published the original book on lean manufacturing, "The Machine That Changed the World," in 1990.
Lean manufacturing is often defined as a set of principles used to improve the quality, speed, and cost of products and services. It emphasizes reducing defects and eliminating waste throughout the value chain. Lean manufacturing is also known as just in time (JIT), zero defect total productive maintenance(TPM), and five-star (S). Lean manufacturing focuses on eliminating non-value-added activities such as rework, inspection, and waiting.
Lean manufacturing improves product quality and costs. It also helps companies reach their goals quicker and decreases employee turnover. Lean Manufacturing is one of the most efficient ways to manage the entire value chains, including suppliers and customers as well distributors and retailers. Lean manufacturing can be found in many industries. Toyota's philosophy, for example, is what has enabled it to be successful in electronics, automobiles, medical devices, healthcare and chemical engineering as well as paper and food.
Lean manufacturing includes five basic principles:
-
Define Value - Determine the value that your business brings to society. Also, identify what sets you apart from your competitors.
-
Reduce waste - Get rid of any activity that does not add value to the supply chain.
-
Create Flow. Ensure that your work is uninterrupted and flows seamlessly.
-
Standardize and simplify - Make your processes as consistent as possible.
-
Develop Relationships: Establish personal relationships both with internal and external stakeholders.
Although lean manufacturing has always been around, it is gaining popularity in recent years because of a renewed interest for the economy after 2008's global financial crisis. Many businesses have adopted lean production techniques to make them more competitive. Economists think that lean manufacturing is a crucial factor in economic recovery.
Lean manufacturing is now becoming a common practice in the automotive industry, with many benefits. These include better customer satisfaction and lower inventory levels. They also result in lower operating costs.
It can be applied to any aspect of an organisation. Lean manufacturing is most useful in the production sector of an organisation because it ensures that each step in the value-chain is efficient and productive.
There are three main types of lean manufacturing:
-
Just-in Time Manufacturing, (JIT): This kind of lean manufacturing is also commonly known as "pull-systems." JIT is a method in which components are assembled right at the moment of use, rather than being manufactured ahead of time. This method reduces lead times, increases availability, and decreases inventory.
-
Zero Defects Manufacturing - ZDM: ZDM focuses its efforts on making sure that no defective units leave a manufacturing facility. Repairing a part that is damaged during assembly should be done, not scrapping. This applies to finished products, which may need minor repairs before they are shipped.
-
Continuous Improvement (CI), also known as Continuous Improvement, aims at improving the efficiency of operations through continuous identification and improvement to minimize or eliminate waste. Continuous Improvement (CI) involves continuous improvement in processes, people, tools, and infrastructure.