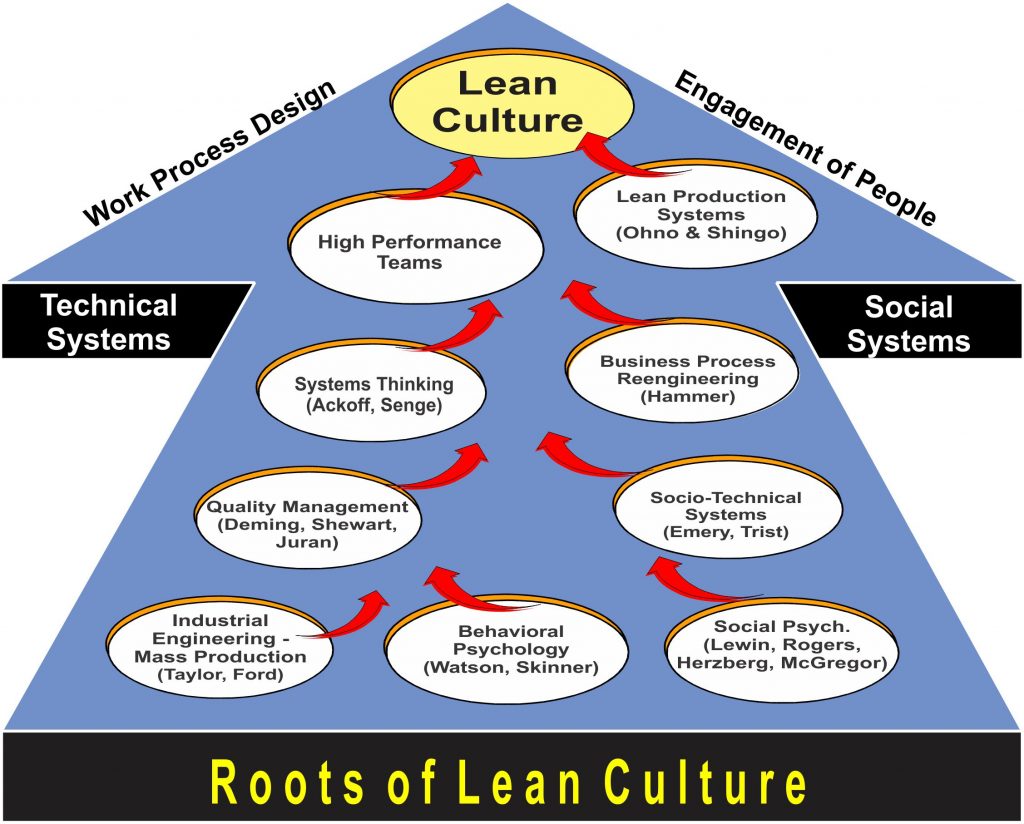
Machinists work with a variety of machines. These machines perform repairs on metal products such a car. They can also create precision metal parts or new alloys. This means that machinists may be exposed to harmful substances. A skilled machinist will be detail-oriented, have strong communication skills, and be able to read mechanical blueprints.
Machinists may work part-time as well as full-time. Many of these machinists begin work right out high school. Some machinists do an apprenticeship before moving on to a fulltime job. Some machinists earn associate degrees in machining. Some machinists might even choose to pursue engineering or computer-aided designing (CAD) degrees.
Machine builders often work in factories, or in specialty shops. While these jobs can be noisy and expose to hazardous materials, they also offer excellent opportunities for problem-solving. Machinists use manual and automatic machines. For those with more experience, it is possible to rise up to managerial and supervisory roles. With the retirement of baby boomers, the need for machinists grows. Job security is also enhanced as machine shops retool to automate.
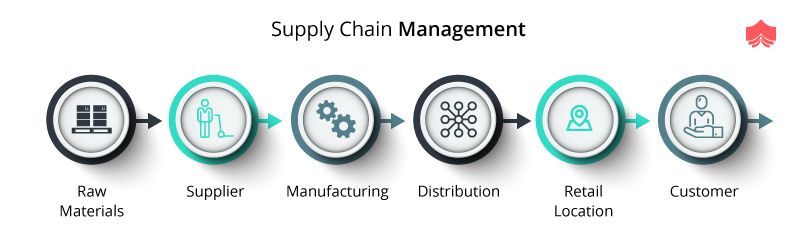
Depending on the employer, machinists can be assigned to specific duties, including setting up machines, repairing them, and making sure that the parts they produce meet quality standards. You can also work with assembly lines. These machines are operated by humans and robots. Other responsibilities include using a computer to program and monitor the machines, and interpreting blueprints.
Machinists can work with many materials such as steel and aluminum, as well brass, copper and other metals. Most machinists work on machines that produce metal parts. However, sometimes they need to work with other materials.
Although machinists typically have a high school diploma in most cases, some employers may require a bachelor's degree. Start your training program for machinists, which can last up to 4 years. To get more experience and learn, you can work alongside a mentor at work. Ask your mentor about any other training opportunities such as apprenticeships, or further education.
Machine operators must collaborate with others, regardless of their company. They can either work as part of a larger team or individually, but they must always follow safety procedures. It includes proper safety equipment such earplugs. Also, machinists are frequently exposed to fumes, chemicals, and other environmental hazards. Fortunately, machinists do not have to be under constant time pressure.
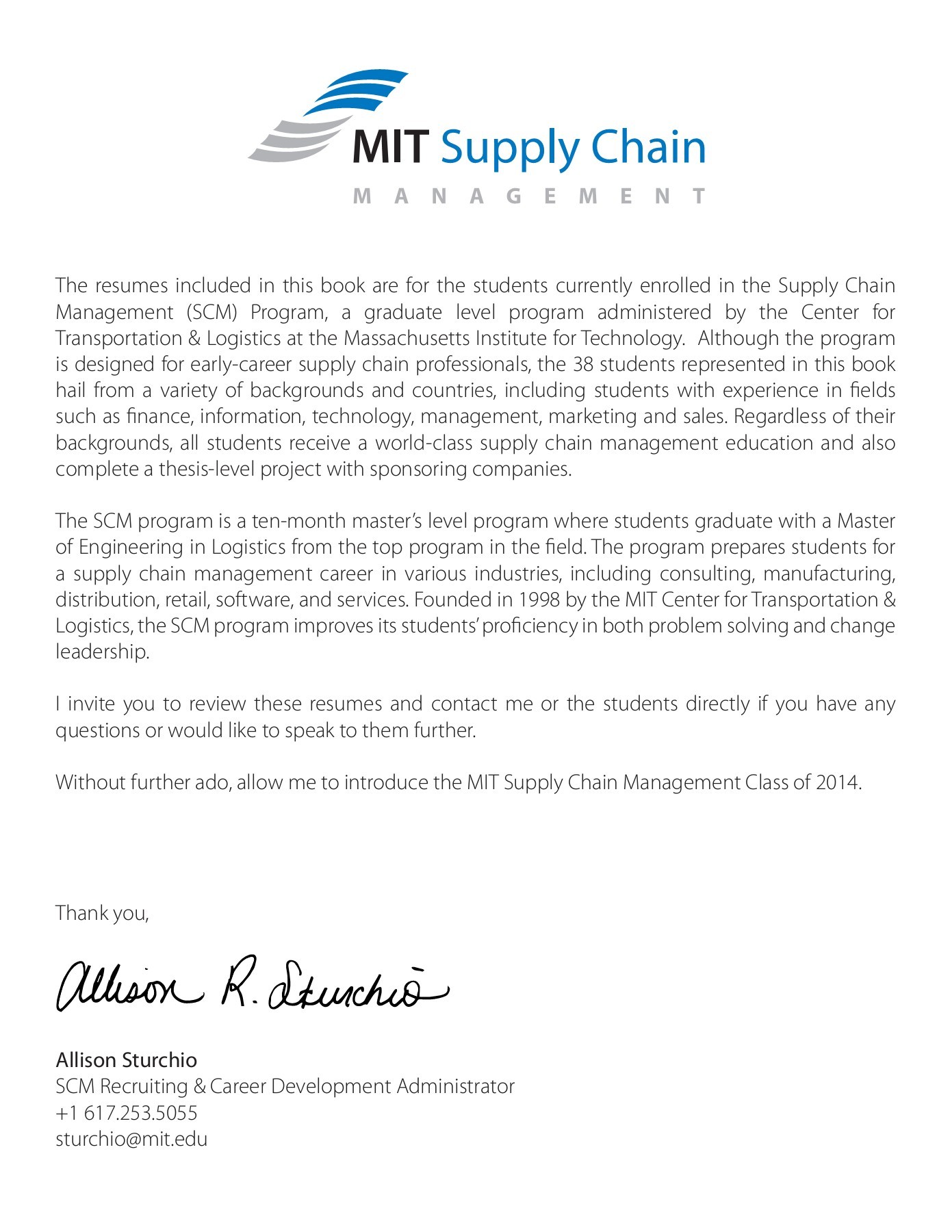
In addition to on-the job training, machinists have the option of enrolling in college courses and joining trade unions. Machinists who are members of a union have better job security and benefits. Union members have access to health insurance and retirement plans. Several colleges offer two-year machining associates programs.
With a degree in machinist work, you can move up the corporate ladder. As car parts demand increases, machinists become more important. Between 2020-2030, there will be a 7% increase in employment. In the coming decades, machinists will remain in high demand due to increased use of artificial Intelligence and retooling of automation.
FAQ
What can I do to learn more about manufacturing?
You can learn the most about manufacturing by getting involved in it. If that is not possible, you could always read books or view educational videos.
How does a Production Planner differ from a Project Manager?
The difference between a product planner and project manager is that a planer is typically the one who organizes and plans the entire project. A production planner, however, is mostly involved in the planning stages.
What does "warehouse" mean?
A warehouse is a place where goods are stored until they are sold. It can be indoors or out. Sometimes, it can be both an indoor and outdoor space.
What are manufacturing & logistics?
Manufacturing is the process of creating goods from raw materials by using machines and processes. Logistics covers all aspects involved in managing supply chains, including procurement and production planning. As a broad term, manufacturing and logistics often refer to both the creation and delivery of products.
What is the difference in Production Planning and Scheduling, you ask?
Production Planning (PP) is the process of determining what needs to be produced at any given point in time. This is done through forecasting demand and identifying production capacities.
Scheduling is the process that assigns dates to tasks so they can get completed within a given timeframe.
Statistics
- You can multiply the result by 100 to get the total percent of monthly overhead. (investopedia.com)
- (2:04) MTO is a production technique wherein products are customized according to customer specifications, and production only starts after an order is received. (oracle.com)
- [54][55] These are the top 50 countries by the total value of manufacturing output in US dollars for its noted year according to World Bank.[56] (en.wikipedia.org)
- According to a Statista study, U.S. businesses spent $1.63 trillion on logistics in 2019, moving goods from origin to end user through various supply chain network segments. (netsuite.com)
- In 2021, an estimated 12.1 million Americans work in the manufacturing sector.6 (investopedia.com)
External Links
How To
How to Use 5S to Increase Productivity in Manufacturing
5S stands as "Sort", Set In Order", Standardize", Separate" and "Store". Toyota Motor Corporation invented the 5S strategy in 1954. It improves the work environment and helps companies to achieve greater efficiency.
This approach aims to standardize production procedures, making them predictable, repeatable, and easily measurable. Cleaning, sorting and packing are all done daily. This knowledge allows workers to be more efficient in their work because they are aware of what to expect.
There are five steps that you need to follow in order to implement 5S. Each step involves a different action which leads to increased efficiency. Sorting things makes it easier to find them later. When items are ordered, they are put together. You then organize your inventory in groups. You can also label your containers to ensure everything is properly labeled.
Employees need to reflect on how they do their jobs. Employees should understand why they do the tasks they do, and then decide if there are better ways to accomplish them. In order to use the 5S system effectively, they must be able to learn new skills.
In addition to improving efficiency, the 5S system also increases morale and teamwork among employees. They are more motivated to achieve higher efficiency levels as they start to see improvement.