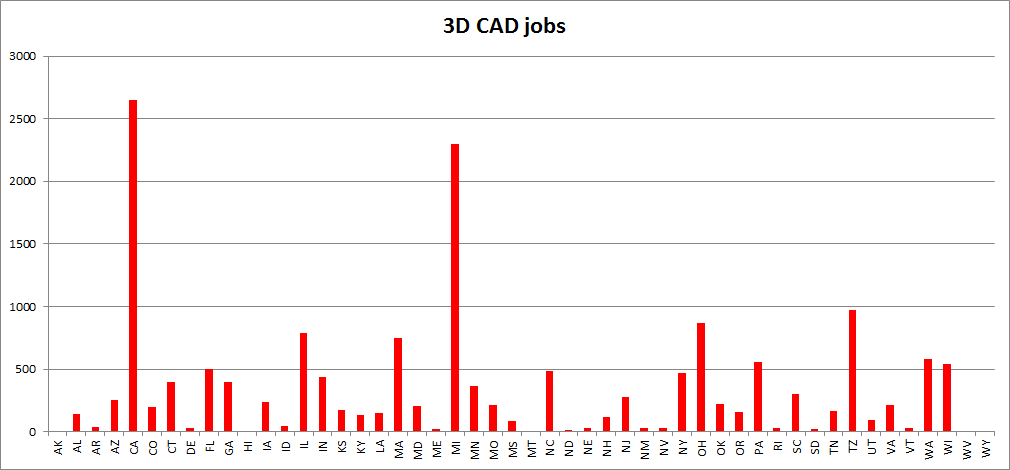
As an industrial design, you are responsible for designing innovative products that can be used in the home, office or industry. You'll find information about your job duties, education and training requirements, as well as the possible salary. In addition, you'll discover how to get started in this field, and explore the various career paths available. Learn about the job's benefits and potential advancement. Once you've completed your education, you'll be well on your way to a lucrative career in the design field.
Your job duties
The Industrial Designer is responsible for conceptualizing new products and services by integrating business, art, and engineering skills. They are responsible for balancing aesthetics and functionality, and ensuring alignment with brand strategies. Experience in the field and a strong portfolio are essential for being an Industrial Designer. Industrial Designers should have strong computer-aided designing software skills and creativity in incorporating new technology into products.
Industrial Designers create design regulations and concepts as a part their job. They need to be able communicate design concepts effectively to cross-functional teams and have strong analytical and problem-solving abilities. They should be able interact with engineers, create 3D models, and work with model shops. In addition to utilizing computer-aided design software, Industrial Designers must be proficient in Microsoft Office, Solidworks, and Keyshot.
Education required
For those looking to work in this industry, a background in industrial design is a great asset. Students in such programs have the chance to build an electronic portfolio to show their design skills. Likewise, some industrial designers also have a Master of Business Administration degree, which helps them enhance their business acumen and better understand the limitations of products. Industrial designers use their analytical skills in order to understand consumer needs. They also use reasoning to design innovative products.
The kind of work you are interested in is a factor in the education that an industrial designer needs. A bachelor's degree is required for industrial designers. Some schools offer degrees for industrial design. But others do not. Candidats should not only take business and design courses. They also need to take courses that include mathematics, computer science engineering, art, and computer sciences. Prospective employers will also appreciate a portfolio. You have many opportunities for career growth and advancement, as there are with all jobs in design.
You have many career options

If you are interested to be an industrial designer, there are several entry-level job opportunities at design firms and manufacturing companies. You can then apply for positions as chief designer or head of design department. Whatever position you decide to pursue, any opportunity to practice your design skills will be helpful. Listed below are a few of the most common entry-level positions available to industrial designers.
An industrial designer typically holds a bachelor’s degree or other related qualification. Employers often look for candidates with background in graphic design or sketching to boost their application for jobs. Employers may favor candidates with 3D modeling and CADD skills in some cases. An industrial designer, for example, is required to be proficient at drafting, rendering, and presenting the work to decision-makers, regardless of whether they are an engineer or an architect.
Salary
The annual salary of an industrial designer varies depending on the educational background and experience. A person with a Masters' or Doctorate degree generally earns more than 75,019 annually. A Bachelor's or Master's degree will earn you less. Many industrial designers move up to managerial roles. Here are some tips to increase your salary. To begin, make sure to read the job description carefully and know your exact salary expectations.
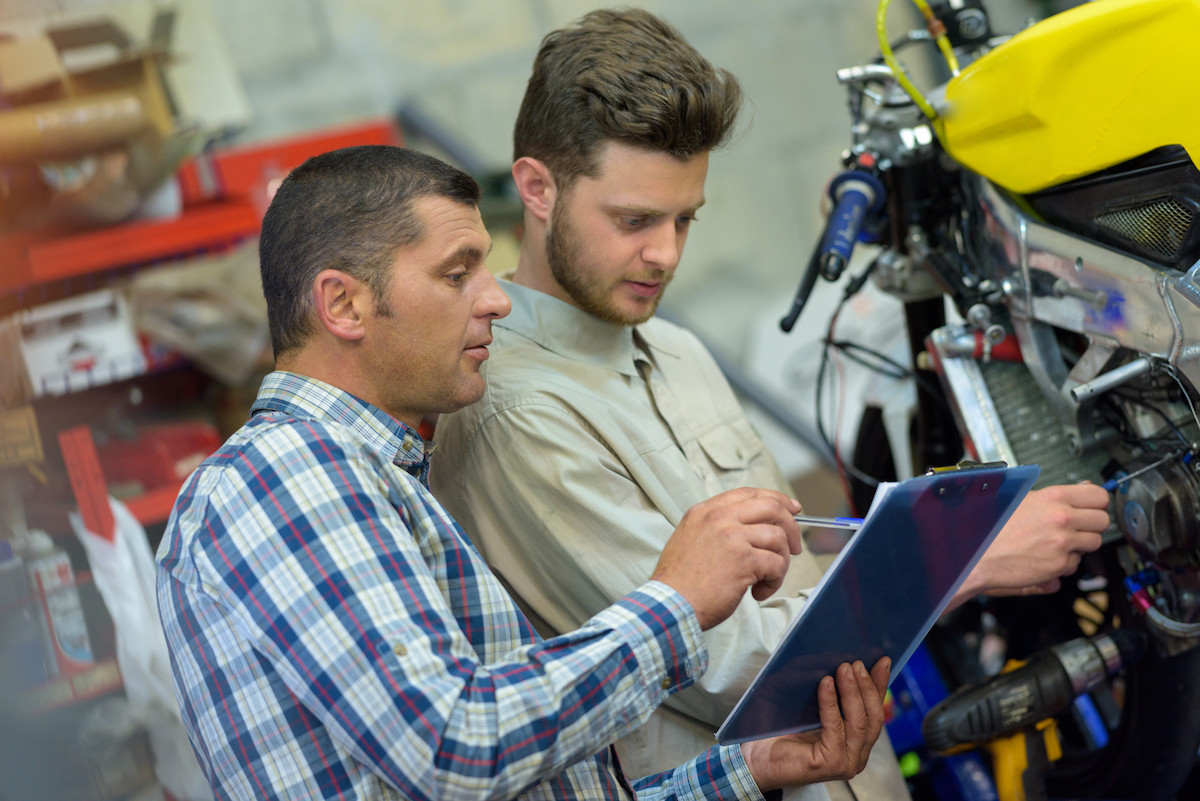
Industrial Designers earn an average annual salary of $62,315, though the actual amount can be much higher. The U.S. Bureau of Labor Statistics states that top earners are those who make more than $106,000 a year in this field. This figure is only a starting point. Your industry experience, where you work, and your location all will impact the salary you receive. Once you have established the skills and whereabouts of your work, it's time to consider the compensation you receive in your area.
FAQ
What is the importance of logistics in manufacturing?
Logistics are an essential component of any business. They are essential to any business's success.
Logistics play a key role in reducing expenses and increasing efficiency.
What is the difference between a production planner and a project manager?
The main difference between a production planner and a project manager is that a project manager is usually the person who plans and organizes the entire project, whereas a production planner is mainly involved in the planning stage of the project.
What are the goods of logistics?
Logistics is the process of moving goods from one point to another.
They include all aspects of transport, including packaging, loading, transporting, unloading, storing, warehousing, inventory management, customer service, distribution, returns, and recycling.
Logisticians ensure the product reaches its destination in the most efficient manner. They assist companies with their supply chain efficiency through information on demand forecasts. Stock levels, production times, and availability.
They can also track shipments in transit and monitor quality standards.
What are the 4 types manufacturing?
Manufacturing refers to the transformation of raw materials into useful products by using machines and processes. Manufacturing involves many activities, including designing, building, testing and packaging, shipping, selling, service, and so on.
Why automate your factory?
Automation has become increasingly important in modern warehousing. With the rise of ecommerce, there is a greater demand for faster delivery times as well as more efficient processes.
Warehouses have to be flexible to meet changing requirements. To do so, they must invest heavily in technology. Automating warehouses has many benefits. These are some of the benefits that automation can bring to warehouses:
-
Increases throughput/productivity
-
Reduces errors
-
Increases accuracy
-
Safety is boosted
-
Eliminates bottlenecks
-
Allows companies scale more easily
-
Makes workers more efficient
-
Gives you visibility into all that is happening in your warehouse
-
Enhances customer experience
-
Improves employee satisfaction
-
It reduces downtime, and increases uptime
-
Quality products delivered on time
-
Eliminates human error
-
It ensures compliance with regulations
Statistics
- Job #1 is delivering the ordered product according to specifications: color, size, brand, and quantity. (netsuite.com)
- According to the United Nations Industrial Development Organization (UNIDO), China is the top manufacturer worldwide by 2019 output, producing 28.7% of the total global manufacturing output, followed by the United States, Japan, Germany, and India.[52][53] (en.wikipedia.org)
- It's estimated that 10.8% of the U.S. GDP in 2020 was contributed to manufacturing. (investopedia.com)
- You can multiply the result by 100 to get the total percent of monthly overhead. (investopedia.com)
- [54][55] These are the top 50 countries by the total value of manufacturing output in US dollars for its noted year according to World Bank.[56] (en.wikipedia.org)
External Links
How To
Six Sigma in Manufacturing:
Six Sigma is defined by "the application SPC (statistical process control) techniques to achieve continuous improvements." Motorola's Quality Improvement Department developed it at their Tokyo plant in Japan in 1986. The basic idea behind Six Sigma is to improve quality by improving processes through standardization and eliminating defects. This method has been adopted by many companies in recent years as they believe there are no perfect products or services. Six Sigma seeks to reduce variation between the mean production value. This means that if you take a sample of your product, then measure its performance against the average, you can find out what percentage of the time the process deviates from the norm. If the deviation is excessive, it's likely that something needs to be fixed.
Understanding how your business' variability is a key step towards Six Sigma implementation is the first. Once you understand that, it is time to identify the sources of variation. These variations can also be classified as random or systematic. Random variations occur when people do mistakes. Symmetrical variations are caused due to factors beyond the process. If you make widgets and some of them end up on the assembly line, then those are considered random variations. If however, you notice that each time you assemble a widget it falls apart in exactly the same spot, that is a problem.
Once you identify the problem areas, it is time to create solutions. That solution might involve changing the way you do things or redesigning the process altogether. To verify that the changes have worked, you need to test them again. If they don’t work, you’ll need to go back and rework the plan.