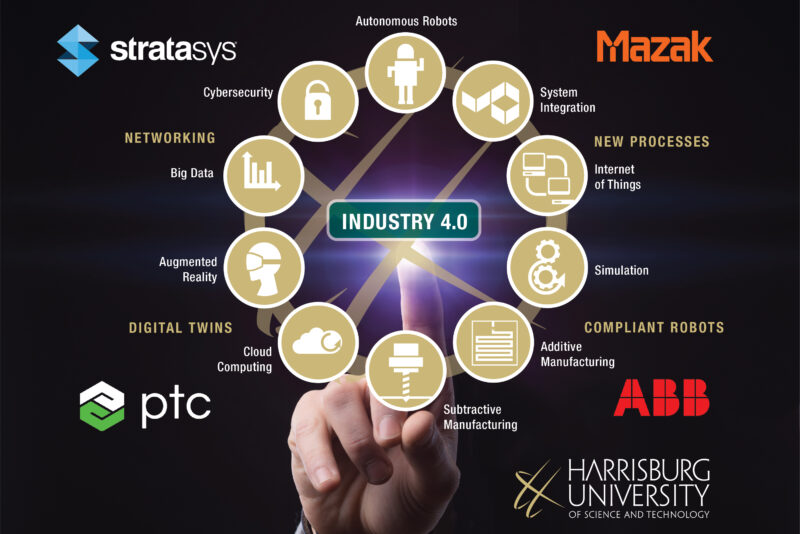
The field of industrial management is engineering in which various engineering processes are combined to create an effective management structure. These engineering processes are integrated into an integrated management system by the industrial manager. Here are some things you should know about the job. Below are some benefits and requirements that you must meet to be an industrial manager. This career is for you if your qualifications are up-to-date and you're looking for a rewarding and challenging job. Continue reading to learn about the career.
Job description
An industrial manager oversees all aspects of the production process. This job will cover many aspects of production, but it will also include how to source raw materials or implement equipment. Computer literacy is essential for industrial production managers, who must be able to use computers to coordinate the work of different departments, suppliers, clients, and other parties. Industrial production managers should also be conversant in the most recent production technologies and management procedures. Many managers take part in professional organizations, attend tradeshows and conferences in the industry, and enroll in courses to earn certification.
Industrial managers coordinate all activities within a company, in addition to supervising production processes. They ensure that production lines are efficient and meet customer requirements in terms of quality and time. In addition, they oversee staffing levels and change production levels as necessary to minimize inventory. They may coordinate communication with suppliers or other departments, and supervise quality control programs. The majority of their role is to manage people. This includes identifying, training and motivating employees.
Education is necessary
To be qualified as an industrial manger, you will need a bachelor's degree either in management or business administration. However, some employers prefer to hire people with experience in these fields. Computer literacy is also a requirement for industrial managers. Computers are increasingly becoming a crucial part of the manufacturing process, helping coordinate production across departments, suppliers, and clients. In order to succeed in this field, individuals interested should have the appropriate education and experience.
Many industrial production manager begin their careers in production and move on to higher-ranking supervisory roles. Professionals must have a business management degree to become industrial managers. However, entry-level workers may still be able obtain this education through their jobs or by taking classes sponsored in part by their companies. However, most managers are expected to have two to five years of relevant experience before becoming a manager.
Potential earnings
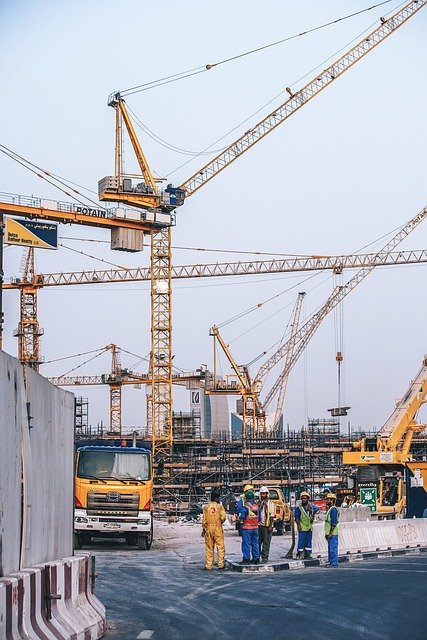
Managers in industrial plants oversee the smooth functioning of the whole process. They are responsible for determining how best to utilize equipment and employees, as well as making strategic decisions. They are responsible for hiring, evaluating, and setting production schedules. They supervise the day-today activities of a workforce and monitor the entire production process to ensure it operates efficiently and at peak efficiency.
The earnings potential of an industrial production manager depends on the employer and the experience of the employee. Although it's hard for anyone to predict what the future earnings will be, the median industrial manager salary was $103,380 as of May 2016. The highest paid industrial production workers earned $172,000. High-skilled industrial production managers may earn more if they have been certified and received additional training. According to U.S. Bureau of Labor Statistics, those who have earned a bachelor’s or higher in industrial production management can earn more.
Work environment
A manager of industrial production divides their time between the production floor or an office. Sometimes, they live in the same building. When working in a manufacturing area, industrial production manager must follow established health and safety protocols and use the proper protective equipment. They may also spend considerable time in meetings with subordinates or analyzing production data. These managers might also create reports. A manager of industrial production often works in a dynamic environment.
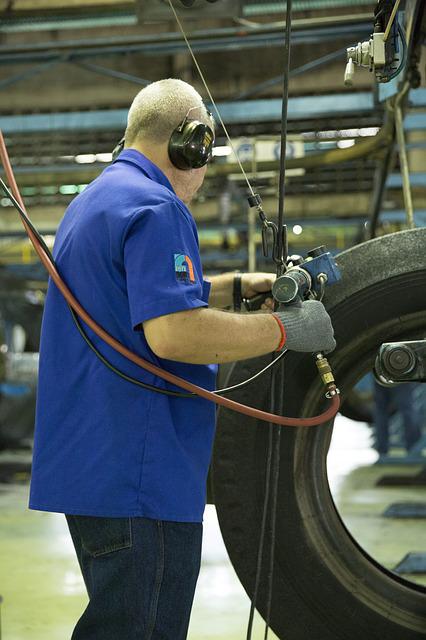
Industrial production managers are an integral part of the business's management structure. They have many responsibilities. They have the responsibility of coordinating activities among workers and increasing productivity. The primary tasks of an industrial producer manager include increasing productivity and maintaining safety. Corporate restructuring has resulted in many levels of managerial and support staff being eliminated. Production managers now have a greater workload. This is a huge challenge for any manager. It can make the job of production managers difficult.
FAQ
How can manufacturing excess production be decreased?
It is essential to find better ways to manage inventory to reduce overproduction. This would reduce the amount of time spent on unnecessary activities such as purchasing, storing, and maintaining excess stock. This could help us free up our time for other productive tasks.
Kanban systems are one way to achieve this. A Kanban board is a visual display used to track work in progress. Kanban systems allow work items to move through different states until they reach their final destination. Each state represents a different priority level.
When work is completed, it can be transferred to the next stage. A task that is still in the initial stages of a process will be considered complete until it moves on to the next stage.
This allows work to move forward and ensures that no work is missed. A Kanban board allows managers to monitor how much work is being completed at any given moment. This information allows managers to adjust their workflow based off real-time data.
Lean manufacturing is another option to control inventory levels. Lean manufacturing emphasizes eliminating waste in all phases of production. Anything that does not contribute to the product's value is considered waste. The following are examples of common waste types:
-
Overproduction
-
Inventory
-
Packaging that is not necessary
-
Material surplus
By implementing these ideas, manufacturers can improve efficiency and cut costs.
How important is automation in manufacturing?
Not only are service providers and manufacturers important, but so is automation. They can provide services more quickly and efficiently thanks to automation. It reduces human errors and improves productivity, which in turn helps them lower their costs.
What is the responsibility for a logistics manager
Logistics managers make sure all goods are delivered on schedule and without damage. This is done through his/her expertise and knowledge about the company's product range. He/she should make sure that enough stock is on hand to meet the demands.
What is it like to manage a logistics company?
A successful logistics business requires a lot more than just knowledge. Effective communication skills are necessary to work with suppliers and clients. You must be able analyze data and draw out conclusions. You must be able to work well under pressure and handle stressful situations. You must be creative and innovative to develop new ideas to improve efficiency. You need to have strong leadership qualities to motivate team members and direct them towards achieving organizational goals.
It is also important to be efficient and well organized in order meet deadlines.
What do you mean by warehouse?
Warehouses and storage facilities are where goods are kept before being sold. It can be either an indoor or outdoor space. In some cases it could be both indoors and outdoors.
Statistics
- In 2021, an estimated 12.1 million Americans work in the manufacturing sector.6 (investopedia.com)
- In the United States, for example, manufacturing makes up 15% of the economic output. (twi-global.com)
- According to the United Nations Industrial Development Organization (UNIDO), China is the top manufacturer worldwide by 2019 output, producing 28.7% of the total global manufacturing output, followed by the United States, Japan, Germany, and India.[52][53] (en.wikipedia.org)
- Job #1 is delivering the ordered product according to specifications: color, size, brand, and quantity. (netsuite.com)
- (2:04) MTO is a production technique wherein products are customized according to customer specifications, and production only starts after an order is received. (oracle.com)
External Links
How To
How to use 5S in Manufacturing to Increase Productivity
5S stands to stand for "Sort", “Set In Order", “Standardize", and "Store". The 5S methodology was developed at Toyota Motor Corporation in 1954. It helps companies achieve higher levels of efficiency by improving their work environment.
This approach aims to standardize production procedures, making them predictable, repeatable, and easily measurable. Cleaning, sorting and packing are all done daily. Through these actions, workers can perform their jobs more efficiently because they know what to expect from them.
Implementing 5S requires five steps. These are Sort, Set In Order, Standardize. Separate. And Store. Each step involves a different action which leads to increased efficiency. Sorting things makes it easier to find them later. Once you have placed items in an ordered fashion, you will put them together. Then, after you separate your inventory into groups, you store those groups in containers that are easy to access. Finally, label all containers correctly.
Employees must be able to critically examine their work practices. Employees need to be able understand their motivations and discover alternative ways to do them. They will need to develop new skills and techniques in order for the 5S system to be implemented.
The 5S Method not only improves efficiency, but it also helps employees to be more productive and happier. They will feel motivated to strive for higher levels of efficiency once they start to see results.