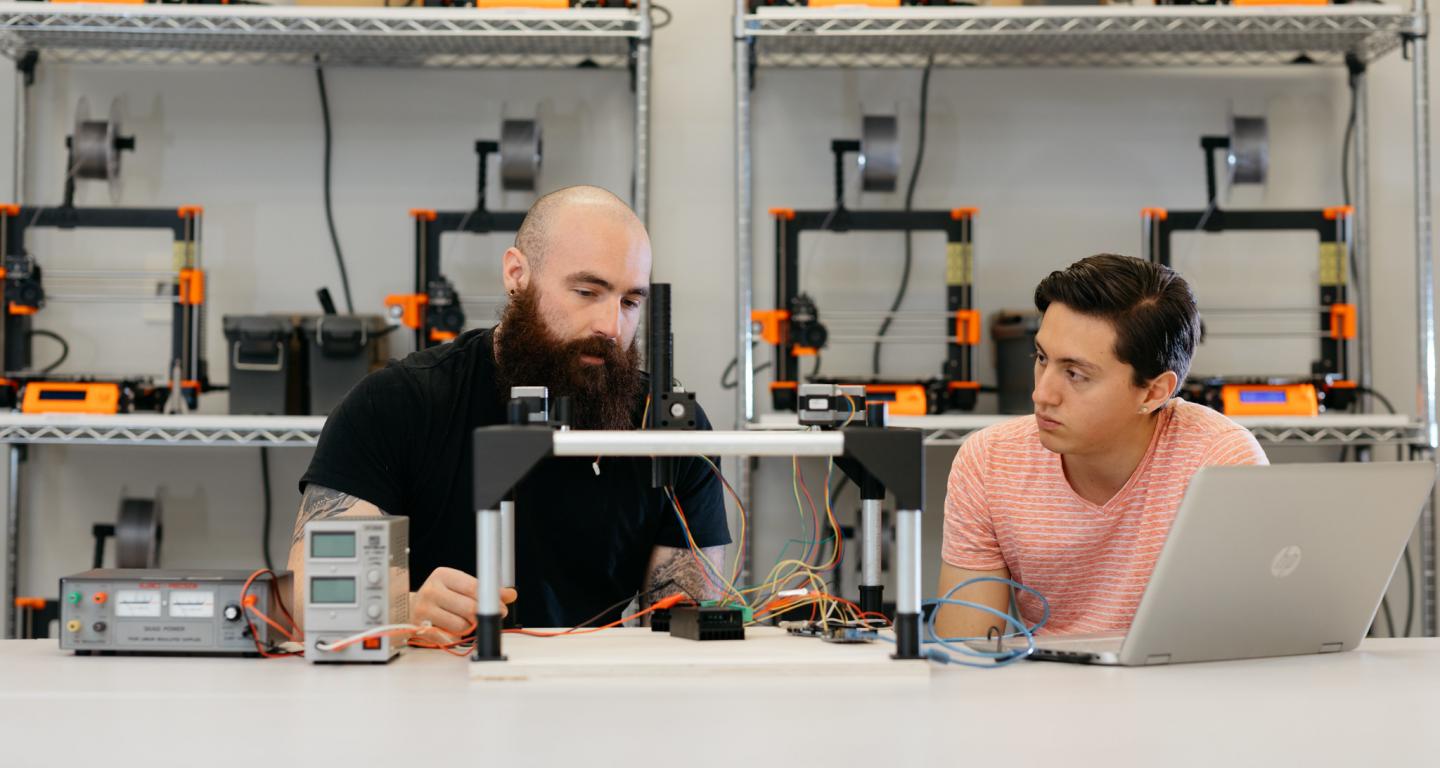
Lean system management reduces waste at the workplace. It is based upon the belief that all activities or processes in an organization should add value for its customers. This can be achieved by eliminating any activities that do not add value and working systematically to create more value.
A lean-management system is designed for improving the overall performance of an enterprise. This helps ensure that all employees understand the goals and purpose of their job.
The first step in lean system management is to identify what value is. This is done by identifying customer needs and then designing a system that meets those needs. To achieve this, it is important to ensure that the entire production process and customer service are efficient and consistent.
Using lean manufacturing principles to make products is an effective way to reduce costs and increase efficiency, but you need to make sure your staff is on board with the changes. The results of the program could be disastrous if the staff is not committed.
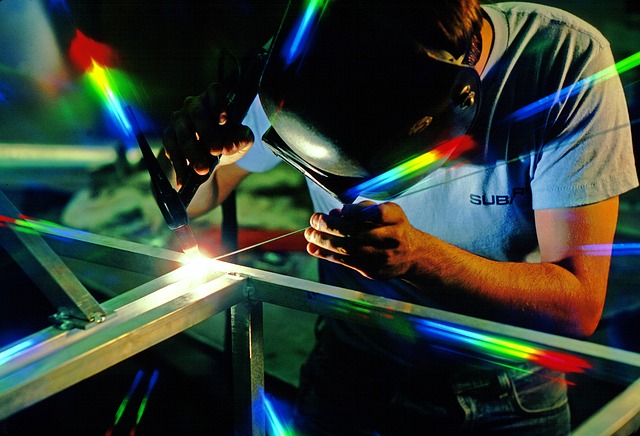
It is not enough to get the employees on board. Your organization must also have a strong supply chain. This is because the majority of lean initiatives require a lot of retooling of the supply chain to make it work well.
One of the most important things that you can do to help with this is to make sure your staff is properly trained on lean principles. You can do this by making sure that your employees are aware of what waste is and the importance of removing it from production.
Teamwork is another aspect to be considered when implementing lean concepts. This is not easy to do, but it's an important element of the Lean System and will allow you to eliminate waste from your production.
This will allow your team to produce better quality products and services and increase your company's bottom line in the long run. This can be encouraged by having them meet regularly to discuss wastes and how to eliminate them.
Lean managers will help you reach this goal by ensuring workers are trained properly and have the knowledge to implement these techniques. They can keep your production processes flowing smoothly and efficiently by keeping all team members informed of potential problems.
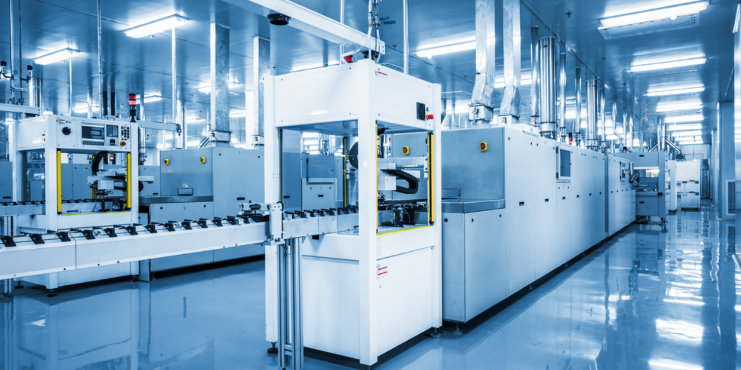
The final stage in lean management is to evaluate and improve the implementation of each procedure. You can do this by tracking each project's progress and making sure that all necessary changes are made.
According to your organization’s size, you might need to hire a manager to oversee lean operations. Searching for lean management positions or job boards can help you find candidates.
FAQ
Why automate your warehouse
Automation has become increasingly important in modern warehousing. E-commerce has brought increased demand for more efficient and quicker delivery times.
Warehouses should be able adapt quickly to new needs. To do so, they must invest heavily in technology. The benefits of automating warehouses are numerous. These are some of the benefits that automation can bring to warehouses:
-
Increases throughput/productivity
-
Reduces errors
-
Increases accuracy
-
Safety enhancements
-
Eliminates bottlenecks
-
This allows companies to scale easily
-
Increases efficiency of workers
-
Gives you visibility into all that is happening in your warehouse
-
Enhances customer experience
-
Improves employee satisfaction
-
It reduces downtime, and increases uptime
-
You can be sure that high-quality products will arrive on time
-
Eliminates human error
-
This helps to ensure compliance with regulations
How does a production planner differ from a project manager?
The primary difference between a producer planner and a manager of a project is that the manager usually plans and organizes the whole project, while a production planner is only involved in the planning stage.
How can we improve manufacturing efficiency?
First, determine which factors have the greatest impact on production time. We then need to figure out how to improve these variables. If you don’t know how to start, look at which factors have the greatest impact upon production time. Once you identify them, look for solutions.
Statistics
- According to a Statista study, U.S. businesses spent $1.63 trillion on logistics in 2019, moving goods from origin to end user through various supply chain network segments. (netsuite.com)
- (2:04) MTO is a production technique wherein products are customized according to customer specifications, and production only starts after an order is received. (oracle.com)
- According to the United Nations Industrial Development Organization (UNIDO), China is the top manufacturer worldwide by 2019 output, producing 28.7% of the total global manufacturing output, followed by the United States, Japan, Germany, and India.[52][53] (en.wikipedia.org)
- In 2021, an estimated 12.1 million Americans work in the manufacturing sector.6 (investopedia.com)
- Job #1 is delivering the ordered product according to specifications: color, size, brand, and quantity. (netsuite.com)
External Links
How To
How to use the Just-In Time Method in Production
Just-intime (JIT), a method used to lower costs and improve efficiency in business processes, is called just-in-time. This is where you have the right resources at the right time. This means that only what you use is charged to your account. Frederick Taylor, a 1900s foreman, first coined the term. Taylor observed that overtime was paid to workers if they were late in working. He decided that workers would be more productive if they had enough time to complete their work before they started to work.
JIT is about planning ahead. You should have all the necessary resources ready to go so that you don’t waste money. Also, you should look at the whole project from start-to-finish and make sure you have the resources necessary to address any issues. If you anticipate that there might be problems, you'll have enough people and equipment to fix them. You won't have to pay more for unnecessary items.
There are many JIT methods.
-
Demand-driven: This type of JIT allows you to order the parts/materials required for your project on a regular basis. This will allow you to track how much material you have left over after using it. This will allow to you estimate the time it will take for more to be produced.
-
Inventory-based: This type allows you to stock the materials needed for your projects ahead of time. This allows you to predict how much you can expect to sell.
-
Project-driven: This method allows you to set aside enough funds for your project. You will be able to purchase the right amount of materials if you know what you need.
-
Resource-based JIT : This is probably the most popular type of JIT. Here you can allocate certain resources based purely on demand. You will, for example, assign more staff to deal with large orders. If you don't have many orders, you'll assign fewer people to handle the workload.
-
Cost-based: This is similar to resource-based, except that here you're not just concerned about how many people you have but how much each person costs.
-
Price-based pricing: This is similar in concept to cost-based but instead you look at how much each worker costs, it looks at the overall company's price.
-
Material-based - This is a variant of cost-based. But instead of looking at the total company cost, you focus on how much raw material you spend per year.
-
Time-based: This is another variation of resource-based JIT. Instead of focusing only on how much each employee is costing, you should focus on how long it takes to complete your project.
-
Quality-based JIT - This is another form of resource-based JIT. Instead of looking at the labor costs and time it takes to make a product, think about its quality.
-
Value-based JIT: This is the latest form of JIT. In this scenario, you're not concerned about how products perform or whether customers expect them to meet their expectations. Instead, your goal is to add value to the market.
-
Stock-based is an inventory-based system that measures the number of items produced at any given moment. It's useful when you want maximum production and minimal inventory.
-
Just-in-time planning (JIT): This is a combination JIT and supply-chain management. It refers to the process of scheduling the delivery of components as soon as they are ordered. It's important because it reduces lead times and increases throughput.