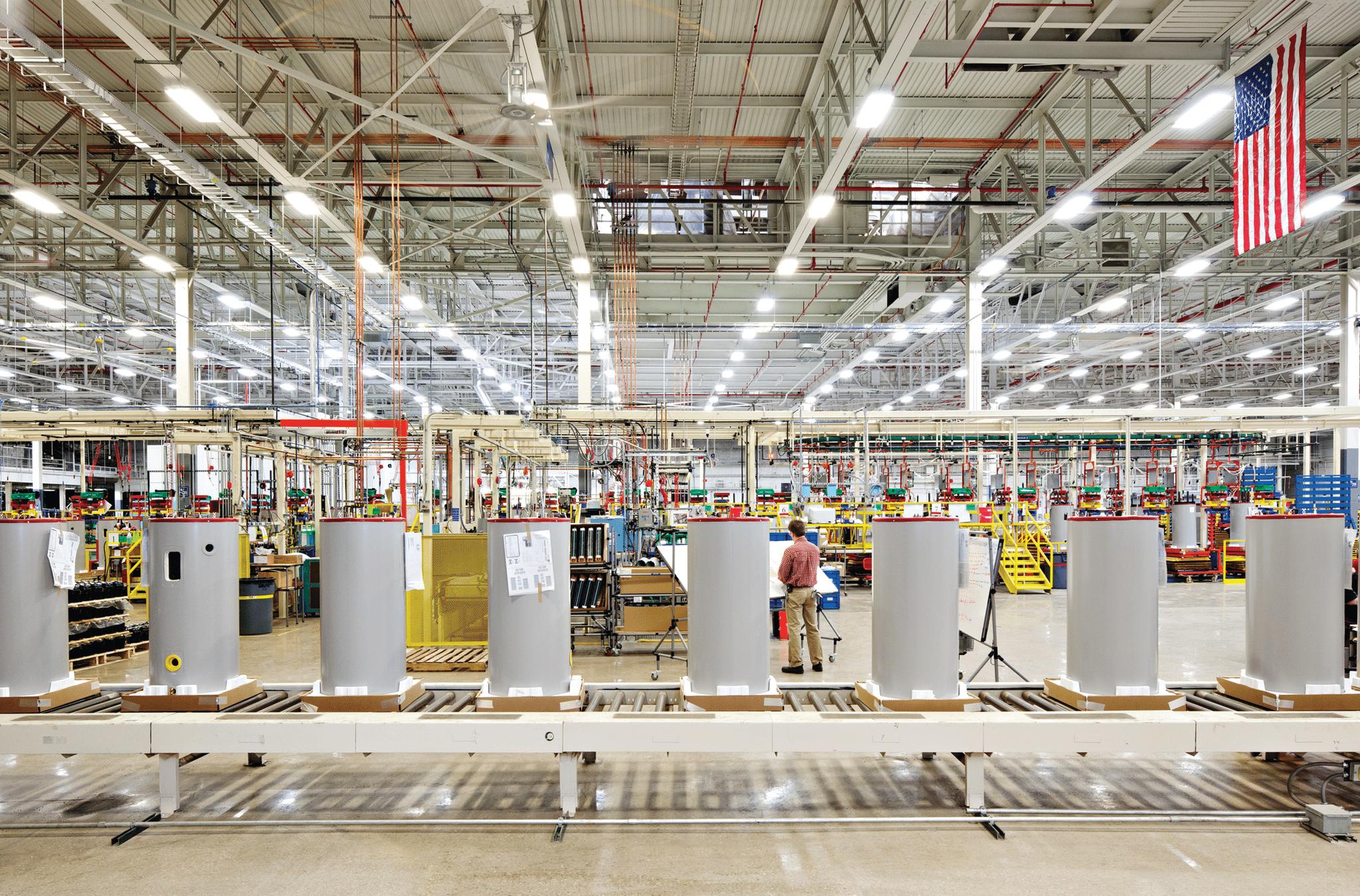
Transport is the industry responsible for moving people and goods across the country. The transportation industry includes trucks, trains and ships as well as buses, airplanes, and other transport equipment. Jobs in the industry include clerical, administrative, and management positions as well as those requiring special training.
Vehicle Operators
The most common job in this industry is truck driver, a position that typically requires less than a high school diploma or GED certificate. Drivers are responsible for operating vehicles that transport goods between a manufacturing facility and retail outlets or distribution centres. They can work to regular or irregular hours and finish their drives according to a time limit.
Airline and Commercial Pilots
Most transportation careers do not require a Bachelor's Degree. Good driving skills, work experience, and a driver's licence are the main requirements. Some workers earn their license after completing on-thejob training, or earning a certificate in a specific trade.
Harbor Pilots and Boating and Waterways Operators as well as Passenger Attendants
Workers in the waterway transportation industry operate and maintain vessels which transport people and cargo across oceans and inland waters. They travel from and to foreign ports, as well as those in the United States, along the Great Lakes and inland waterways. They are responsible for the safety of cargo and passengers by operating switches, controlling engines and inspecting vessels.
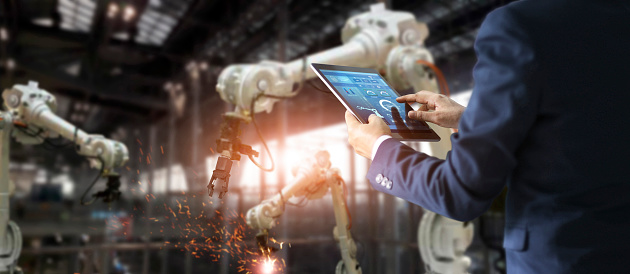
Rail Transportation Workers
Railroad workers control the movement of freight and passenger trains. Some railroad workers drive trains while others control their activities. Others operate the signaling and switching systems at the rail yard. Pump Operators, except Wellhead Pumpers, tend, operate, or control power-driven stationary or mobile pumps or manifold systems for the transfer of gas, oil, liquids, slurries or powdered material from one vessel or container to another.
Transportation and Warehousing Activities Support
The subsector that employs most workers in this sector is warehousing, storage and related services. As shown in Table 1, it is the industry that employs the most clerical and administrative workers, as well as managers.
Warehouse and Distribution Center Managers
Many of these employees work in large distribution and warehousing centers, which are hubs for transport. They are responsible for planning and coordinating the movement of products from production to sale.
Also, they oversee the daily operations of the distribution center or warehouse. They require a great deal of patience, tact, communication and organization.
Transportation Careers, Transport, and Jobs in the Transport Industry
Some jobs within the transportation industry demand a bachelor’s or higher. Other jobs, like that of a air traffic or pilot controller, require specific training. You can only get into these positions after you have completed a training program or on-the-job.
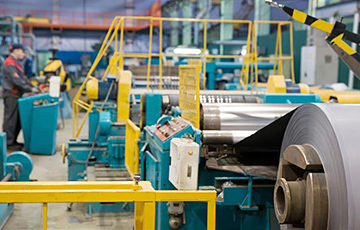
Transport jobs also require a great deal of responsibility and work. It is particularly true for workers in the transportation and warehouse industries who are responsible for the safety and security of people and goods that they transport.
This work is not only about the physical aspects of moving people and goods, but also involves dealing with customers. Communication with customers is key. This includes answering their questions about delivery or shipping times and making sure they receive their orders on schedule.
FAQ
Do we need to know about Manufacturing Processes before learning about Logistics?
No. No. It is important to know about the manufacturing processes in order to understand how logistics works.
What is production management?
Production Planning refers to the development of a plan for every aspect of production. This document will ensure everything is in order and ready to go when you need it. It should also contain information on achieving the best results on set. It should include information about shooting locations, casting lists, crew details, equipment requirements, and shooting schedules.
The first step in filming is to define what you want. You may have already decided where you would like to shoot, or maybe there are specific locations or sets that you want to use. Once you have identified the scenes and locations, you can start to determine which elements are required for each scene. You might decide you need a car, but not sure what make or model. You could look online for cars to see what options are available, and then narrow down your choices by selecting between different makes or models.
After you've found the perfect car, it's time to start thinking about adding extras. Do you have people who need to be seated in the front seat? Maybe you need someone to move around in the back. Maybe you want to change the interior color from black to white? These questions will help you determine the exact look and feel of your car. It is also worth considering the types of shots that you wish to take. You will be filming close-ups and wide angles. Perhaps you want to show the engine or the steering wheel? These details will help identify the exact car you wish to film.
Once you have established all the details, you can create a schedule. A schedule will tell you when you need to start shooting and when you need to finish. You will need to know when you have to be there, what time you have to leave and when your return home. Everyone will know what they need and when. If you need to hire extra staff, you can make sure you book them in advance. It's not worth paying someone to show up if you haven't told him.
When creating your schedule, you will also need to consider the number of days you need to film. Some projects may only take a couple of days, while others could last for weeks. When you are creating your schedule, you should always keep in mind whether you need more than one shot per day or not. Multiple shots at the same location can increase costs and make it more difficult to complete. If you aren't sure whether you need multiple shots, it is best to take fewer photos than you would like.
Budgeting is another important aspect of production planning. A realistic budget will help you work within your means. It is possible to reduce the budget at any time if you experience unexpected problems. It is important to not overestimate how much you will spend. If you underestimate how much something costs, you'll have less money to pay for other items.
Planning production is a tedious process. Once you have a good understanding of how everything works together, planning future projects becomes easy.
Why is logistics important for manufacturing?
Logistics are essential to any business. They are essential to any business's success.
Logistics are also important in reducing costs and improving efficiency.
How is a production manager different from a producer planner?
A production planner is more involved in the planning phase of the project than a project manger.
Statistics
- It's estimated that 10.8% of the U.S. GDP in 2020 was contributed to manufacturing. (investopedia.com)
- According to a Statista study, U.S. businesses spent $1.63 trillion on logistics in 2019, moving goods from origin to end user through various supply chain network segments. (netsuite.com)
- According to the United Nations Industrial Development Organization (UNIDO), China is the top manufacturer worldwide by 2019 output, producing 28.7% of the total global manufacturing output, followed by the United States, Japan, Germany, and India.[52][53] (en.wikipedia.org)
- In 2021, an estimated 12.1 million Americans work in the manufacturing sector.6 (investopedia.com)
- Job #1 is delivering the ordered product according to specifications: color, size, brand, and quantity. (netsuite.com)
External Links
How To
Six Sigma: How to Use it in Manufacturing
Six Sigma can be described as "the use of statistical process control (SPC), techniques to achieve continuous improvement." Motorola's Quality Improvement Department created Six Sigma at their Tokyo plant, Japan in 1986. Six Sigma is a method to improve quality through standardization and elimination of defects. Since there are no perfect products, or services, this approach has been adopted by many companies over the years. Six Sigma's main objective is to reduce variations from the production average. If you take a sample and compare it with the average, you will be able to determine how much of the production process is different from the norm. If there is a significant deviation from the norm, you will know that something needs to change.
Understanding how your business' variability is a key step towards Six Sigma implementation is the first. Once you understand that, it is time to identify the sources of variation. This will allow you to decide if these variations are random and systematic. Random variations are caused by human errors. Systematic variations can be caused by outside factors. If you make widgets and some of them end up on the assembly line, then those are considered random variations. You might notice that your widgets always fall apart at the same place every time you put them together.
Once you've identified the problem areas you need to find solutions. You might need to change the way you work or completely redesign the process. Once you have implemented the changes, it is important to test them again to ensure they work. If they didn't work, then you'll need to go back to the drawing board and come up with another plan.