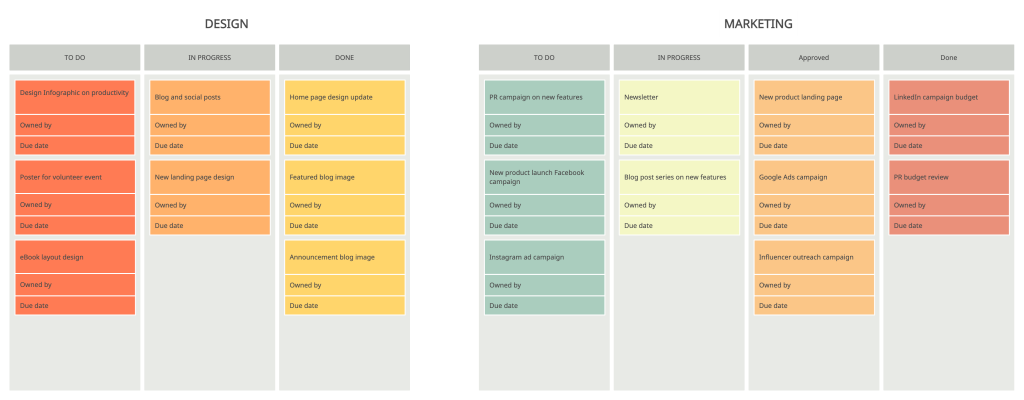
The bill of material (BOM) is an important part in the manufacturing process. The bill of materials (BOM) outlines all the items required to make end products. This includes raw materials, assembly procedures, and so on. It is essential for any company, no matter if they are selling directly to customers or via retail channels. It aids companies to keep track, prevent waste, and reduce production errors. It can also help companies avoid stockouts.
A bill of materials is a very detailed, tabular document that lists the components of an assembly. The document also lists the parts that will be used to construct the assembly. The parts and subassemblies could be purchased from other sources or manufactured in-house. Parts will need to be identified by a unique part number. This allows the assembly team identify the right parts and to gather the necessary materials. It is also important that you note any special requirements on your bill of materials. These special requirements could lead to delays or even errors during the manufacturing process.
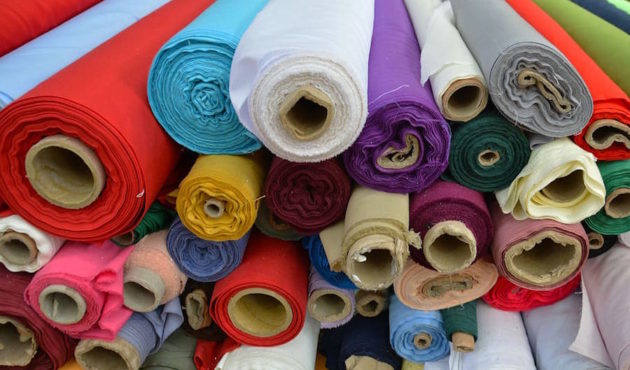
Companies are able to keep track of components and raw materials with bills of materials. They can also be used to increase production. They can prevent stockouts and allow companies to forecast their sales. These documents can also be used to help companies track materials used in production and prevent over-ordering.
A bill of materials is a document that lists the materials, components, and subassemblies needed to produce a product. A bill of materials lists labor and time required to complete each stage. It is important to remember that the bill should include the supplier(s), for each part. You may also need to include any other information that is essential for the production process. It is important to remember that bills of materials can differ from one company to the next.
To ensure that the final product works properly, bills of materials are used during manufacturing. They are also used by companies to plan and order raw materials, reduce waste and minimize production errors. The bill of material helps manufacturers identify the materials necessary to make a product, and then determine the correct amounts. It is important to understand that the bill is a roadmap of the final product. It can be challenging to create a bill-of-materials, especially for products with many parts. There are software tools that allow you to create a bill.
A bill of materials is created to reflect the project's needs and specifications. This document can be used to create a blueprint of the final product, or as a communication tool between supply chain and manufacturing partners. This document is useful for companies in order to avoid over-ordering materials and keep track of all components used in the production process.
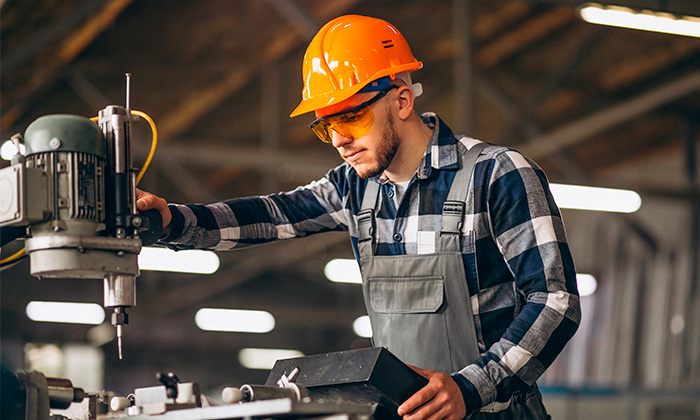
For any company that sells through retail channels, or directly to customers, a bill-of-materials is vital. Bills allow for higher productivity and greater profits. They help companies to avoid waste, reduce production mistakes, and prevent stockouts.
FAQ
What jobs are available in logistics?
There are different kinds of jobs available in logistics. Some examples are:
-
Warehouse workers - They load trucks and pallets.
-
Transportation drivers: They drive trucks and trailers and deliver goods and make pick-ups.
-
Freight handlers: They sort and package freight in warehouses.
-
Inventory managers - These are responsible for overseeing the stock of goods in warehouses.
-
Sales representatives - They sell products to customers.
-
Logistics coordinators – They plan and coordinate logistics operations.
-
Purchasing agents - They purchase goods and services needed for company operations.
-
Customer service representatives - Answer calls and email from customers.
-
Shippers clerks - They process shipping order and issue bills.
-
Order fillers: They fill orders based off what has been ordered and shipped.
-
Quality control inspectors - They check incoming and outgoing products for defects.
-
Others - There is a variety of other jobs in logistics. These include transportation supervisors and cargo specialists.
What does it mean to warehouse?
A warehouse is an area where goods are stored before being sold. It can be an outdoor or indoor area. In some cases, it may be a combination of both.
What skills are required to be a production manager?
A production planner must be organized, flexible, and able multitask to succeed. Communication skills are essential to ensure that you can communicate effectively with clients, colleagues, and customers.
Statistics
- According to a Statista study, U.S. businesses spent $1.63 trillion on logistics in 2019, moving goods from origin to end user through various supply chain network segments. (netsuite.com)
- [54][55] These are the top 50 countries by the total value of manufacturing output in US dollars for its noted year according to World Bank.[56] (en.wikipedia.org)
- You can multiply the result by 100 to get the total percent of monthly overhead. (investopedia.com)
- (2:04) MTO is a production technique wherein products are customized according to customer specifications, and production only starts after an order is received. (oracle.com)
- In the United States, for example, manufacturing makes up 15% of the economic output. (twi-global.com)
External Links
How To
How to use 5S to increase Productivity in Manufacturing
5S stands to stand for "Sort", “Set In Order", “Standardize", and "Store". Toyota Motor Corporation was the first to develop the 5S approach in 1954. It assists companies in improving their work environments and achieving higher efficiency.
The idea behind standardizing production processes is to make them repeatable and measurable. Cleaning, sorting and packing are all done daily. Because workers know what they can expect, this helps them perform their jobs more efficiently.
Implementing 5S requires five steps. These are Sort, Set In Order, Standardize. Separate. And Store. Each step requires a different action, which increases efficiency. For example, when you sort things, you make them easy to find later. When items are ordered, they are put together. After you have divided your inventory into groups you can store them in easy-to-reach containers. Labeling your containers will ensure that everything is correctly labeled.
Employees need to reflect on how they do their jobs. Employees must understand why they do certain tasks and decide if there's another way to accomplish them without relying on the old ways of doing things. To be successful in the 5S system, employees will need to acquire new skills and techniques.
In addition to improving efficiency, the 5S system also increases morale and teamwork among employees. Once they start to notice improvements, they are motivated to keep working towards their goal of increasing efficiency.