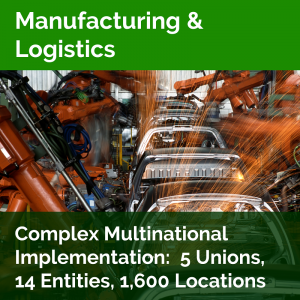
Located in Gibson County, Indiana, Toyota Motor Manufacturing Indiana Inc. is the first Toyota plant to be wholly owned by Toyota in the United States. It produces Toyota's full-size pickup trucks including the Avalon, Corolla and Corolla as well as the Sienna minivan. The Toyota RAV4 Hybrid hybrid is also manufactured here. It is the most successful Toyota hybrid ever.
The plant was originally planned to manufacture the Toyota Highlander, but instead moved to Gibson County, Indiana. The Lexus ES 350 and RAV4 Hybrid compact SUVs have been manufactured at the plant by Toyota since 2011. Toyota spent over $1.33 billion on the plant in 2017.
Toyota Safety Sense 2.5+ also is manufactured here. It has automatic emergency braking. The plant is also preparing all new Camry models for 2018. This new model has a new transmission and more power. It also features a stylish design. It will cost $25,900
Toyota's production of the Toyota Camry is the largest in the United States. It is America's most-sold midsize sedan and has been since 1995. In Kentucky, Toyota has made 10 million Camry cars. The hybrid model was manufactured at the plant, which is the only one in North America.
Toyota Production System refers to a set of techniques and practices that improve quality and efficiency. This system also includes the Toyota Production Engineering and Manufacturing Center. It will house 600 Toyota employees. The center will be the first to produce hydrogen fuel cell modules suitable for heavy-duty commercial trucks. The facility can build up to 100,000 vehicles per year.
Toyota has spent $1.5 billion on the plant in the last five year. Toyota has also employed 700 more workers. By 2020, this investment will provide 470,100 additional jobs in the United States. Toyota has made over $147 Million in Kentucky non-profit partners since 1986.
The Toyota Camry, a reliable and elegant vehicle, is very popular. It comes with the GAK platform and a completely new transmission. It also has a fun driving experience. Consumer Reports listed the Toyota Camry as the number one selling car in America in July.
The Toyota production system includes a number of elements, including continuous improvement, just-in-time parts delivery, and a sophisticated robotic welding system. The Toyota Production Engineering and Manufacturing Center is a good example of how Toyota has made the most of its investment in Kentucky.
Toyota has made significant savings on its production hall construction and air conditioning costs by using a new design. The Visitor Center has interactive video displays, and exhibits on hybrid technologies. Toyota will be producing up to 2,000,000 vehicles in North America over the next 10 year. This is the largest Toyota factory outside Japan.
Toyota's New Global Architecture (or New Global Architecture) is a huge step forward in improving Toyota's production process. This strategy includes a new engine and production organization, as well as a module that unifies vehicle components. The new design retains Toyota's innovative spirit while reflecting Toyota's traditional values.
FAQ
How important is automation in manufacturing?
Not only is automation important for manufacturers, but it's also vital for service providers. It allows them to offer services faster and more efficiently. It helps them to lower costs by reducing human errors, and improving productivity.
Why automate your factory?
Modern warehouses are increasingly dependent on automation. Increased demand for efficient and faster delivery has resulted in a rise in e-commerce.
Warehouses should be able adapt quickly to new needs. In order to do this, they need to invest in technology. Automating warehouses has many benefits. These are just a few reasons to invest in automation.
-
Increases throughput/productivity
-
Reduces errors
-
Improves accuracy
-
Safety Boosts
-
Eliminates bottlenecks
-
Companies can scale more easily
-
Makes workers more efficient
-
This gives you visibility into what happens in the warehouse
-
Enhances customer experience
-
Improves employee satisfaction
-
This reduces downtime while increasing uptime
-
You can be sure that high-quality products will arrive on time
-
Eliminates human error
-
This helps to ensure compliance with regulations
How can we reduce manufacturing overproduction?
In order to reduce excess production, you need to develop better inventory management methods. This would decrease the time that is spent on inefficient activities like purchasing, storing, or maintaining excess stock. By doing this, we could free up resources for other productive tasks.
A Kanban system is one way to achieve this. A Kanban board is a visual display used to track work in progress. A Kanban system allows work items to move through several states before reaching their final destination. Each state has a different priority level.
For instance, when work moves from one stage to another, the current task is complete enough to be moved to the next stage. However, if a task is still at the beginning stages, it will remain so until it reaches the end of the process.
This allows you to keep work moving along while making sure that no work gets neglected. Managers can see how much work has been done and the status of each task at any time with a Kanban Board. This allows them to adjust their workflows based on real-time information.
Lean manufacturing is another option to control inventory levels. Lean manufacturing seeks to eliminate waste from every step of the production cycle. Anything that doesn't add value to the product is considered waste. There are several types of waste that you might encounter:
-
Overproduction
-
Inventory
-
Unnecessary packaging
-
Overstock materials
These ideas can help manufacturers improve efficiency and reduce costs.
Statistics
- Many factories witnessed a 30% increase in output due to the shift to electric motors. (en.wikipedia.org)
- In the United States, for example, manufacturing makes up 15% of the economic output. (twi-global.com)
- According to a Statista study, U.S. businesses spent $1.63 trillion on logistics in 2019, moving goods from origin to end user through various supply chain network segments. (netsuite.com)
- Job #1 is delivering the ordered product according to specifications: color, size, brand, and quantity. (netsuite.com)
- [54][55] These are the top 50 countries by the total value of manufacturing output in US dollars for its noted year according to World Bank.[56] (en.wikipedia.org)
External Links
How To
How to use the Just In-Time Production Method
Just-in-time is a way to cut costs and increase efficiency in business processes. It's the process of obtaining the right amount and timing of resources when you need them. This means that only what you use is charged to your account. Frederick Taylor first coined this term while working in the early 1900s as a foreman. He saw how overtime was paid to workers for work that was delayed. He concluded that if workers were given enough time before they start work, productivity would increase.
JIT teaches you to plan ahead and prepare everything so you don’t waste time. The entire project should be looked at from start to finish. You need to ensure you have enough resources to tackle any issues that might arise. You will have the resources and people to solve any problems you anticipate. This way you won't be spending more on things that aren’t really needed.
There are many types of JIT methods.
-
Demand-driven: This JIT is where you place regular orders for the parts/materials that are needed for your project. This will allow to track how much material has been used up. This will allow to you estimate the time it will take for more to be produced.
-
Inventory-based: You stock materials in advance to make your projects easier. This allows one to predict how much they will sell.
-
Project-driven: This means that you have enough money to pay for your project. If you know the amount you require, you can buy the materials you need.
-
Resource-based JIT: This is the most popular form of JIT. You allocate resources based on the demand. If you have many orders, you will assign more people to manage them. If you don't have many orders, you'll assign fewer people to handle the workload.
-
Cost-based: This is a similar approach to resource-based but you are not only concerned with how many people you have, but also how much each one costs.
-
Price-based: This approach is very similar to the cost-based method except that you don't look at individual workers costs but the total cost of the company.
-
Material-based - This is a variant of cost-based. But instead of looking at the total company cost, you focus on how much raw material you spend per year.
-
Time-based JIT: A variation on resource-based JIT. Instead of focusing only on how much each employee is costing, you should focus on how long it takes to complete your project.
-
Quality-based JIT: This is another variation of resource based JIT. Instead of focusing on the cost of each worker or how long it takes, think about how high quality your product is.
-
Value-based: This is one of the newest forms of JIT. In this scenario, you're not concerned about how products perform or whether customers expect them to meet their expectations. Instead, your goal is to add value to the market.
-
Stock-based. This method is inventory-based and focuses only on the actual production at any given point. It is used when production goals are met while inventory is kept to a minimum.
-
Just-in-time (JIT) planning: This is a combination of JIT and supply chain management. This refers to the scheduling of the delivery of components as soon after they are ordered. It's important as it reduces leadtimes and increases throughput.